Introduction to Silicon Carbide Wear Plates and Market Dynamics
Silicon carbide wear plates have emerged as a high-performance solution for industries facing extreme abrasion, corrosion, and high-temperature challenges. As demand grows for durable, lightweight materials that can extend equipment life and reduce maintenance costs, silicon carbide stands out for its exceptional hardness, thermal stability, and chemical inertness. Its application spans sectors as diverse as mining, construction, energy, and defense, where equipment downtime and wear-related failures can translate into significant operational risks and losses.
In recent years, innovations in composite structures and advanced manufacturing processes have expanded the potential uses of silicon carbide wear plates. Hybrid fiber reinforcements, reaction-bonded composites, and additive manufacturing techniques now enable tailored solutions to precise performance requirements. Meanwhile, evolving global trade policies and shifting supply chains influence the competitive dynamics and cost structures for producers and end users alike.
This executive summary offers a clear, concise overview of the latest market transformations, tariff impacts, segmentation dynamics, regional variations, and leading players shaping the future of silicon carbide wear plates. It equips decision-makers with the insights needed to navigate an increasingly complex landscape, optimize material selections, and devise strategic investments for sustainable growth.
Transformative Shifts Reshaping the Silicon Carbide Wear Plate Landscape
The silicon carbide wear plate market is undergoing transformative shifts driven by material science breakthroughs and evolving industrial demands. First, the advent of composite architectures, which integrate long and short fibers within silicon carbide matrices, has improved impact resistance and tailored wear properties. This shift from monolithic plates toward hybrid structures supports equipment designs that withstand higher loads and reduce abrasive wear over extended service cycles.
Simultaneously, advanced manufacturing processes, including 3D printing and hot isostatic pressing, are enabling complex geometries and finer microstructures that enhance performance consistency. Manufacturers now optimize pore distribution and bonding interfaces, resulting in plates that resist chipping, cracking, and thermal shock. These capabilities challenge traditional production methods, prompting legacy producers to upgrade facilities or partner with specialized technology providers.
In parallel, sustainability considerations are driving demand for eco-efficient manufacturing. Cold isostatic pressing at prototype scales and additive techniques for low-volume production reduce material waste and energy consumption. As end users prioritize life-cycle impacts, wear plates that balance durability with environmental performance offer a competitive edge.
These innovations converge with rising maintenance costs and stricter equipment uptime requirements across mining, construction, and power generation, catalyzing the adoption of high-performance silicon carbide solutions. By embracing these transformative trends, industry stakeholders can position themselves to capture value in a market redefining wear protection standards.
Analyzing the Cumulative Impact of 2025 U.S. Tariffs on Silicon Carbide Wear Plates
In 2025, the imposition of new tariffs by the United States has significantly affected the cost structure and competitive balance of silicon carbide wear plate imports and exports. Suppliers relying on cross-border trade of raw silicon carbide powders and finished plates have faced higher duties, leading to increased landed costs for equipment manufacturers and end users. These additional expenses have prompted sourcing strategies to pivot toward domestic production, where tariff impacts are minimal and lead times shorter.
Consequently, North American producers have ramped up capacity expansions and invested in local supply chains to meet rising demand. This strategic shift fosters greater vertical integration, with companies securing raw material inputs and refining in-house processing capabilities. While these measures partially mitigate tariff-induced cost increases, some price pass-through to end users remains inevitable, especially in capital-intensive sectors such as mining and construction.
Beyond cost implications, the tariff landscape has spurred innovation in material formulations and processing techniques designed to maximize performance at optimized price points. Suppliers are exploring lower-cost precursor chemicals and streamlined bonding processes to offset duty burdens. Additionally, industry alliances between domestic ceramic manufacturers and equipment OEMs are strengthening, as collaborative R&D efforts focus on high-value, low-cost wear solutions.
Overall, the 2025 tariff measures have accelerated a realignment of global trade flows and supply chains for silicon carbide wear plates, reinforcing domestic production hubs and fueling technological advancements aimed at balancing cost and performance.
Comprehensive Segmentation Insights for Silicon Carbide Wear Plate Applications
The silicon carbide wear plate market is characterized by five key segmentation dimensions that influence product design, application performance, and supply chain dynamics. From a type perspective, the market divides into composite and monolithic wear plates. Composite variants leverage hybrid structures, long fibers, and short fibers to deliver enhanced toughness and impact resistance, making them ideal for highly abrasive environments. Monolithic plates, produced via hot pressing, reaction bonding, or solid pressing, offer simplicity and cost-effectiveness for standard wear applications, but often trade off toughness for hardness.
Application segmentation drives specialized wear solutions across construction, grinding, and mining sectors. In construction, loaders, excavators, pavement wear plates, and pulverized fly ash conveyance liners demand plates that resist high-impact loads and varying abrasion modes. Grinding applications require autogenous and semi-autogenous mill liners, ball mill liners, and rod mill liners that withstand continuous cyclic impacts and sliding wear. Mining operations depend on conveyor liners, crusher wear plates, and drilling equipment plates that must endure both high-pressure abrasion and corrosive conditions in ore processing.
End use industries further refine wear plate requirements across aerospace, automotive, defense, and energy and power sectors. Jet engines and spacecraft components demand materials capable of withstanding extreme thermal cycling and erosion, while automotive brakes, clutches, and engine components require wear plate variants with precise dimensional tolerances and thermal conductivity properties. Defense applications in armor plate systems and military aircraft prioritize ballistic resistance and structural integrity. In the oil and gas sector, pipelines and turbine liners benefit from non-oxide-based silicon carbide formulations that provide excellent corrosion and erosion resistance.
Material composition serves as a critical segmentation axis, with carbide composites, non-oxide-based, and oxide-based categories each offering unique performance profiles. WC-Co and WC-Ni composites excel in combined hardness and toughness, while boron carbide and silicon carbide deliver superior abrasive resistance. Oxide-based variants, such as alumina and zirconia, offer cost-effective alternatives with good wear performance in moderate environments.
Manufacturing process segmentation spans additive manufacturing, cold isostatic pressing, and hot isostatic pressing. Additive manufacturing techniques such as 3D printing and direct write deposition enable rapid prototyping and complex geometries for bespoke wear plates. Cold isostatic pressing supports low-volume production and prototype runs with minimal tooling costs. Hot isostatic pressing facilitates both batch and mass manufacturing, ensuring uniform density and minimal porosity in high-volume production. Understanding these interdependent segmentation layers empowers stakeholders to align material choices and process methods with specific operational demands, optimizing wear life and total cost of ownership.
This comprehensive research report categorizes the Silicon Carbide Wear Plate market into clearly defined segments, providing a detailed analysis of emerging trends and precise revenue forecasts to support strategic decision-making.
- Type
- Application
- End Use Industry
- Material Composition
- Manufacturing Process
Regional Market Variations and Growth Drivers for Wear Plate Applications
Regional dynamics exhibit distinct growth trajectories and competitive environments across the Americas, Europe, Middle East & Africa, and Asia-Pacific. In the Americas, increasing investments in mining expansion projects and infrastructure upgrades drive the demand for wear-resistant solutions. Domestic producers benefit from reshoring trends and tariff-driven localization efforts, solidifying the region as a key manufacturing hub, particularly for monolithic and composite plates serving heavy industries.
In Europe, Middle East & Africa, stringent environmental regulations and sustainability targets favor manufacturing processes with lower carbon footprints, such as cold isostatic pressing. This region also leads in high-value applications in aerospace and defense, where reliability under extreme conditions elevates the demand for non-oxide-based silicon carbide. European material science clusters continue to pioneer advanced formulations, while Middle Eastern mining operations and African construction projects create growing markets for durable wear components.
Asia-Pacific remains the largest consumer region, driven by rapid industrialization in China and India, robust automotive production in Japan and South Korea, and energy infrastructure development across Southeast Asia. Suppliers in this region leverage scale economies and cost-efficient manufacturing to capture substantial export volumes. At the same time, rising labor and energy costs are prompting investment in automation and additive manufacturing to maintain competitive pricing and meet diverse application requirements.
This comprehensive research report examines key regions that drive the evolution of the Silicon Carbide Wear Plate market, offering deep insights into regional trends, growth factors, and industry developments that are influencing market performance.
- Americas
- Asia-Pacific
- Europe, Middle East & Africa
Key Competitive Profiles and Technological Leadership in Wear Plate Market
Leading companies are shaping the competitive landscape through continuous innovation, capacity expansions, and strategic partnerships. 3M Ceramics leverages advanced ceramics expertise to deliver tailored composite wear plates for critical industries, while Blasch Precision Ceramics focuses on precision-engineered monolithic solutions for high-throughput mining applications. CeramTec GmbH and CoorsTek Inc. both maintain extensive R&D portfolios, exploring novel bonding agents and fiber reinforcements to boost abrasion resistance and toughness.
Honsin Ceramics and Kennametal Inc. have accelerated additive manufacturing capabilities, enabling rapid customization and complex plate geometries that meet stringent aerospace and defense specifications. Morgan Advanced Materials plc combines deep material science knowledge with global production networks to serve automotive and energy markets, whereas Ortech Inc. specializes in reaction-bonded silicon carbide plates for chemical and petrochemical processing equipment.
Saint-Gobain Ceramic Materials focuses on combining oxide and non-oxide compositions to strike optimal balances between cost and performance, and TimkenSteel Corporation’s investments in hot isostatic pressing facilities underscore the importance of uniform microstructures in high-volume wear applications. Collectively, these players drive market innovation through targeted product portfolios, geographic diversification, and collaborative partnerships with equipment OEMs.
This comprehensive research report delivers an in-depth overview of the principal market players in the Silicon Carbide Wear Plate market, evaluating their market share, strategic initiatives, and competitive positioning to illuminate the factors shaping the competitive landscape.
- 3M Ceramics
- Blasch Precision Ceramics
- CeramTec GmbH
- CoorsTek Inc.
- Honsin Ceramics
- Kennametal Inc.
- Morgan Advanced Materials plc
- Ortech Inc.
- Saint-Gobain Ceramic Materials
- TimkenSteel Corporation
Actionable Recommendations for Strategic Growth and Innovation
Industry leaders must adopt a multifaceted strategy to maintain competitive advantage and capitalize on emerging opportunities. First, prioritizing R&D collaborations with universities and material research institutes can accelerate the development of next-generation composites and processing methods, such as nano-scale fiber reinforcements or hybrid additive production workflows. Second, securing vertically integrated supply chains-from raw silicon carbide precursors to finished plates-helps mitigate tariffs and logistical disruptions, ensuring consistent product quality and delivery timelines.
Third, diversifying product portfolios across segmentation dimensions-type, application, end use, material composition, and process-enables tailored solutions that address specific customer pain points, from high-impact mining wear to precision aerospace applications. Fourth, investing in digital manufacturing platforms and predictive maintenance technologies can optimize production yields and extend product life, leveraging data analytics to refine material formulations and design features.
Fifth, establishing regional manufacturing or assembly sites in key markets such as North America and Europe aligns with localization trends and regulatory preferences, while maintaining cost-effective bulk production in Asia-Pacific. Finally, forging strategic alliances with equipment OEMs and service providers fosters integrated solutions that combine wear plates with installation, monitoring, and life-cycle support services, creating comprehensive value propositions that differentiate offerings in a crowded market.
Explore AI-driven insights for the Silicon Carbide Wear Plate market with ResearchAI on our online platform, providing deeper, data-backed market analysis.
Ask ResearchAI anything
World's First Innovative Al for Market Research
Executive Summary and Synthesis of Market Insights
The silicon carbide wear plate market stands at the intersection of material science innovation, evolving industrial demands, and shifting global trade dynamics. By understanding the transformative shifts in composite architectures and manufacturing techniques, companies can develop wear solutions that deliver unmatched durability and performance. Awareness of tariff impacts underscores the importance of supply chain resilience and localized production strategies. Detailed segmentation insights reveal the diverse requirements across applications and industries, guiding tailored product development.
Regional analysis highlights the need for flexible manufacturing networks that balance cost efficiencies in Asia-Pacific with high-value production closer to end markets in the Americas and EMEA. Reviewing competitive profiles demonstrates that leading players differentiate through continuous innovation, strategic partnerships, and integrated service offerings. Armed with these insights, industry stakeholders can refine their strategic roadmaps, investing in capabilities that drive product innovation, operational excellence, and customer-centric solutions.
This section provides a structured overview of the report, outlining key chapters and topics covered for easy reference in our Silicon Carbide Wear Plate market comprehensive research report.
- Preface
- Research Methodology
- Executive Summary
- Market Overview
- Market Dynamics
- Market Insights
- Cumulative Impact of United States Tariffs 2025
- Silicon Carbide Wear Plate Market, by Type
- Silicon Carbide Wear Plate Market, by Application
- Silicon Carbide Wear Plate Market, by End Use Industry
- Silicon Carbide Wear Plate Market, by Material Composition
- Silicon Carbide Wear Plate Market, by Manufacturing Process
- Americas Silicon Carbide Wear Plate Market
- Asia-Pacific Silicon Carbide Wear Plate Market
- Europe, Middle East & Africa Silicon Carbide Wear Plate Market
- Competitive Landscape
- ResearchAI
- ResearchStatistics
- ResearchContacts
- ResearchArticles
- Appendix
- List of Figures [Total: 26]
- List of Tables [Total: 901 ]
Call to Action: Engage with Ketan Rohom for Comprehensive Market Analysis
To unlock deeper insights and actionable intelligence on the silicon carbide wear plate market, contact Ketan Rohom, Associate Director, Sales & Marketing. Secure comprehensive data, in-depth analysis, and tailored recommendations to guide your strategic decisions and maximize competitive advantage.
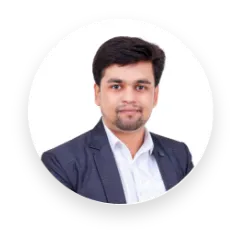
- When do I get the report?
- In what format does this report get delivered to me?
- How long has 360iResearch been around?
- What if I have a question about your reports?
- Can I share this report with my team?
- Can I use your research in my presentation?