Introduction to Silicon Nitride Plasma Etching Dynamics
Silicon nitride plasma etching has emerged as a cornerstone process in advanced semiconductor and microfabrication industries, enabling precise patterning, high etch rates, and exceptional selectivity. As device geometries shrink and functional integration intensifies, manufacturers and research facilities must navigate an increasingly complex landscape of process technologies, material innovations, and regulatory changes. This executive summary explores the critical drivers shaping the silicon nitride etching arena, from groundbreaking equipment architectures to evolving global trade policies. It highlights how laser-like focus on anisotropy, uniformity, and throughput underpins competitive advantage, while stringent environmental and safety standards demand ever-more sophisticated process control.
Against this backdrop, stakeholders must evaluate emerging etch chemistries, chamber designs, and end-point detection strategies to sustain yield and performance. Seamless alignment between R&D and production teams is vital for accelerating cycle times and reducing defectivity. Moreover, cross-industry collaboration-from aerospace to photonics-fuels knowledge transfer and unlocks novel applications. This summary sets the stage for an in-depth assessment of transformative shifts, tariff impacts, granular segmentation insights, regional dynamics, and leading market players. It culminates with targeted recommendations designed to inform strategic decision-making and operational excellence in a market defined by rapid innovation and razor-thin margins.
Transformative Shifts Reshaping the Etching Ecosystem
Over the last decade, the silicon nitride etching landscape has undergone radical transformation driven by converging technological trends and rising performance expectations. Miniaturization imperatives have pushed etch profiles to unprecedented aspect ratios, necessitating innovations in deep reactive ion etching and inductively coupled plasma systems. Concurrently, demand for advanced photonic devices and MEMS sensors has spurred development of specialized chemistries and chamber architectures optimized for high etch selectivity and minimal damage to delicate structures.
Moreover, the shift toward single-wafer processing has delivered enhanced process repeatability and rapid recipe changeover, boosting throughput in high-volume manufacturing. At the same time, hybrid etching techniques combining anisotropic and isotropic steps have unlocked new design freedoms for integrated circuit interconnects and optical waveguides. Sustainability concerns are also molding equipment design, with manufacturers integrating advanced scrub systems, low-global-warming-potential gases, and closed-loop gas recycling to curtail ecological footprints.
Consequently, collaboration between equipment vendors, material suppliers, and end users has intensified, accelerating the adoption of automated load stations, in-situ metrology, and AI-driven endpoint control. These transformative shifts are laying the groundwork for the next era of silicon nitride plasma etching, where agility, precision, and sustainability converge to meet the relentless demands of tomorrow’s devices.
Cumulative Impact of United States Tariffs in 2025 on Etching Operations
In 2025, the imposition of cumulative tariffs by the United States has significantly altered supply-chain economics and procurement strategies for silicon nitride plasma etching equipment and consumables. Tariffs on imported wafer carriers, vacuum pumps, RF power supplies, and specialty gases have driven reevaluation of sourcing strategies, prompting many manufacturers to diversify vendor portfolios and localize critical components. As a result, capital expenditure planning now prioritizes equipment models with modular designs and interchangeable parts to buffer against future trade disruptions.
At the same time, end-users are accelerating qualification of domestic suppliers for chamber liners, electrodes, and dielectric coatings to mitigate the impact of cross-border duties. Contract negotiations increasingly include tariff adjustment clauses, while inventory management teams adopt just-in-time and safety stock policies to balance working capital against shortage risks. Furthermore, research and development groups are investigating alternative chemistries and process recipes that leverage readily available gases and etch byproducts, reducing reliance on tariff-impacted imports.
This cumulative tariff environment has also intensified consolidation trends, as larger conglomerates pursue vertical integration to secure upstream inputs and intellectual property. Consequently, agility in supply-chain management and strategic supplier alliances have become pivotal for maintaining competitiveness and ensuring uninterrupted production in a tariff-volatile global economy.
Key Segmentation Insights Across Application, Technology, Industry and More
Detailed segmentation analysis reveals nuanced growth vectors across multiple dimensions of the silicon nitride plasma etching market. Based on application, integrated circuit manufacturing continues to dominate owing to relentless node scaling, while MEMS fabrication and photonic device production gain traction as sensor and optical markets expand. Opto-electronic device manufacturers, seeking superior film uniformity and etch rate control, are driving demand for high-precision RIE and deep etch solutions.
From a technology standpoint, capacitively coupled plasma etching remains a cost-effective option for shallow etch applications, whereas deep reactive ion etching captures share in scenarios requiring high aspect ratios. Inductively coupled plasma etching, prized for low damage and high throughput, is gaining preference in advanced nodes, and innovators are refining RF power delivery to enhance anisotropy. Reactive ion etching, with its versatility across delicate mask materials, sustains steady adoption in prototyping and low-volume manufacturing environments.
Considering end-user industry, the semiconductor sector accounts for the bulk of volume, but aerospace and defense customers increasingly utilize etching for microthrusters and sensor arrays. Automotive suppliers are leveraging etch capabilities to produce LiDAR and radar components, and consumer electronics brands push for faster cycle times and smaller feature sizes. Healthcare and life sciences labs use etching in microfluidic device fabrication, while telecommunications players incorporate photonic devices for high-speed data transmission.
Material-type segmentation highlights the importance of hard masks for rigorous profile control, while soft masks-encompassing photoresist and polymeric film variants-offer economical options for less demanding etch steps. Substrate materials, including quartz, sapphire, and silicon carbide, cater to specialized applications requiring unique thermal and optical properties. Etch depth requirements range from surface etching for cleaning and pattern definition to deep etching for MEMS channels and photonic trenches.
Production capacity profiles differentiate high volume production lines, where uptime and throughput reign supreme, from low volume manufacturing cells focused on flexibility. Prototype development platforms, equipped with rapid recipe change capabilities, support agile innovation cycles. Process-type analysis bifurcates the market into batch etching systems, valued for cost efficiency, and single wafer processing tools, favored for precision and repeatability. Equipment type further segments the landscape into automatic load, manual load, and semi-automatic load configurations, each balancing labor costs and throughput requirements. Functionality-based insights underscore the criticality of anisotropy control, etch rate consistency, selectivity to underlying films, and film uniformity across the substrate.
This comprehensive research report categorizes the Silicon Nitride Plasma Etching Machine market into clearly defined segments, providing a detailed analysis of emerging trends and precise revenue forecasts to support strategic decision-making.
- Application
- Technology
- End User Industry
- Material Type
- Etching Depth
- Production Capacity
- Process Type
- Equipment Type
- Functionality
Key Regional Insights Across Major Global Markets
Geographically, the Americas region maintains strong leadership in silicon nitride plasma etching consumption, driven by robust semiconductor fabs in the United States and Canada, as well as a thriving aerospace and defense sector. Domestic R&D initiatives and local fabrication capabilities underpin ongoing investments in next-generation etch equipment and process development. In Europe, Middle East & Africa, booming automotive electronics demand and photonics clusters in Germany, France, and the UK are catalyzing growth, while strategic support from government consortia advances sustainable etch technology research. Meanwhile, Asia-Pacific remains the fastest-growing region, propelled by large-scale foundry expansions in Taiwan, South Korea, and China. Regional supply chains here benefit from integrated equipment manufacturing ecosystems, localized material production, and a talent pool skilled in advanced plasma processes. Each region’s unique macroeconomic conditions and policy frameworks shape adoption rates and investment priorities, underscoring the need for region-specific strategies.
This comprehensive research report examines key regions that drive the evolution of the Silicon Nitride Plasma Etching Machine market, offering deep insights into regional trends, growth factors, and industry developments that are influencing market performance.
- Americas
- Asia-Pacific
- Europe, Middle East & Africa
Key Company Insights Driving Innovation and Competitive Dynamics
Leading players continue to push the envelope in etch system performance and service offerings. Applied Materials, Inc. and Lam Research Corporation stand out for their comprehensive suite of plasma etching platforms, extensive field service networks, and ongoing investment in low-GWP chemistry development. ASML Holding N.V. complements its lithography leadership by advancing etch system integration for high-NA and EUV nodes. Tokyo Electron Limited differentiates through its compact single-wafer tools optimized for rapid recipe development and reduced cycle times, while Hitachi High-Tech Corporation focuses on niche MEMS and photonic device applications with highly customizable etch modules.
Emerging contenders like Beijing NAURA Microelectronics Equipment Co., Ltd. and Mattson Technology, Inc. are securing market share by offering cost-competitive solutions tailored to regionally based foundries and research institutions. LPE S.p.A. and Oxford Instruments Plc emphasize specialized deep etch and precision RIE systems, targeting high-value photonics and quantum computing markets. Companies such as Nano-Master, Inc. and Plasma-Therm, LLC differentiate through agile response to custom etch requirements and rapid prototyping services. SPTS Technologies, Ltd. (a KLA Company) leverages advanced process control and data analytics to optimize etch uniformity, while SAMCO Inc. and Trion Technology, Inc. offer niche platforms for emerging substrate materials. ULVAC, Inc. rounds out the competitive landscape with its focus on energy-efficient chamber designs and global service infrastructure.
This comprehensive research report delivers an in-depth overview of the principal market players in the Silicon Nitride Plasma Etching Machine market, evaluating their market share, strategic initiatives, and competitive positioning to illuminate the factors shaping the competitive landscape.
- Applied Materials, Inc.
- ASML Holding N.V.
- Beijing NAURA Microelectronics Equipment Co., Ltd.
- Hitachi High-Tech Corporation
- Lam Research Corporation
- LPE S.p.A.
- Mattson Technology, Inc.
- Nano-Master, Inc.
- Oxford Instruments Plc
- Plasma-Therm, LLC
- SAMCO Inc.
- SPTS Technologies, Ltd. (A KLA Company)
- Tokyo Electron Limited
- Trion Technology, Inc.
- ULVAC, Inc.
Actionable Recommendations for Industry Stakeholders
Industry leaders must embrace strategic agility and technology partnerships to navigate complexity and capitalize on growth opportunities. First, prioritizing integration of advanced endpoint control and machine-learning analytics into existing etch systems will optimize process stability, reduce defectivity, and lower cost of ownership. Second, forging alliances with gas suppliers to develop custom low-GWP chemistries can secure preferential supply terms and differentiate product offerings on sustainability metrics.
In addition, companies should accelerate development of modular hardware architectures that support rapid integration of new chamber materials, mask types, and power delivery schemes, enabling swift responses to evolving device requirements. Strengthening collaboration with end-users through co-innovation centers and joint design-for-manufacturability programs will bridge the gap between research and production, ensuring that next-generation etch solutions meet real-world performance targets.
To mitigate supply-chain risks, establishing diversified procurement channels for critical subsystems and components is essential, as is maintaining a balanced mix of in-house manufacturing and strategic outsourcing. Leaders should also invest in workforce upskilling initiatives, equipping process engineers and service technicians with competencies in advanced plasma diagnostics and remote monitoring. By implementing these recommendations, stakeholders can enhance resilience, accelerate innovation cycles, and secure a competitive edge in the silicon nitride plasma etching domain.
Explore AI-driven insights for the Silicon Nitride Plasma Etching Machine market with ResearchAI on our online platform, providing deeper, data-backed market analysis.
Ask ResearchAI anything
World's First Innovative Al for Market Research
Conclusion on Future Trajectories and Strategic Imperatives
Silicon nitride plasma etching stands at the nexus of accelerating device complexity, sustainability mandates, and shifting trade policies. The interplay of high aspect-ratio etch demands, advanced mask materials, and region-specific dynamics requires a multifaceted strategic approach. Companies that excel will be those that harmonize equipment innovation, supply-chain flexibility, and deep customer engagement.
Looking ahead, the integration of digital twins and predictive maintenance into etch platforms will become increasingly indispensable for maximizing uptime and yield. Concurrently, the pursuit of greener chemistries and closed-loop gas systems will not only address regulatory pressures but also unlock cost savings and bolster corporate responsibility credentials. Finally, targeted investments in emerging end-user segments-from quantum photonics to microfluidics-will pave the way for new revenue streams and long-term market leadership.
This section provides a structured overview of the report, outlining key chapters and topics covered for easy reference in our Silicon Nitride Plasma Etching Machine market comprehensive research report.
- Preface
- Research Methodology
- Executive Summary
- Market Overview
- Market Dynamics
- Market Insights
- Cumulative Impact of United States Tariffs 2025
- Silicon Nitride Plasma Etching Machine Market, by Application
- Silicon Nitride Plasma Etching Machine Market, by Technology
- Silicon Nitride Plasma Etching Machine Market, by End User Industry
- Silicon Nitride Plasma Etching Machine Market, by Material Type
- Silicon Nitride Plasma Etching Machine Market, by Etching Depth
- Silicon Nitride Plasma Etching Machine Market, by Production Capacity
- Silicon Nitride Plasma Etching Machine Market, by Process Type
- Silicon Nitride Plasma Etching Machine Market, by Equipment Type
- Silicon Nitride Plasma Etching Machine Market, by Functionality
- Americas Silicon Nitride Plasma Etching Machine Market
- Asia-Pacific Silicon Nitride Plasma Etching Machine Market
- Europe, Middle East & Africa Silicon Nitride Plasma Etching Machine Market
- Competitive Landscape
- ResearchAI
- ResearchStatistics
- ResearchContacts
- ResearchArticles
- Appendix
- List of Figures [Total: 34]
- List of Tables [Total: 510 ]
Engage with Ketan Rohom to Access the Full Research Report
To delve deeper into this comprehensive analysis and harness actionable insights tailored to your organization’s strategic objectives, contact Ketan Rohom, Associate Director, Sales & Marketing. Secure your copy of the full research report today and position your business at the forefront of silicon nitride plasma etching innovation.
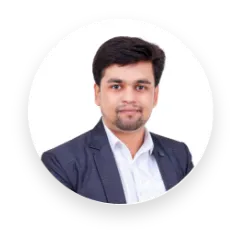
- When do I get the report?
- In what format does this report get delivered to me?
- How long has 360iResearch been around?
- What if I have a question about your reports?
- Can I share this report with my team?
- Can I use your research in my presentation?