Introduction to Silicon Parts for Furnaces & LPCVD
The silicon parts that underpin furnace and Low Pressure Chemical Vapor Deposition (LPCVD) applications serve as the backbone of advanced manufacturing in industries ranging from semiconductors to renewable energy. As process temperatures climb and performance requirements tighten, the demand for high-purity, durable silicon-based components has never been greater. Fueled by the relentless push toward smaller device geometries, higher throughput, and tighter process controls, suppliers are tasked with delivering components that can withstand extreme environments while ensuring consistent thermal and chemical stability.
This executive summary distills the latest dynamics shaping the furnace and LPCVD silicon parts landscape. It highlights the critical shifts in materials engineering, the interplay of global trade policies, key segmentation and regional patterns, and the competitive strategies of leading suppliers. By guiding decision-makers through actionable insights, this overview equips technical leaders, procurement heads, and strategy teams with the perspective needed to navigate complexity, mitigate risk, and capitalize on emerging opportunities.
Transformative Shifts Reshaping the Furnace Silicon Parts Ecosystem
Over the past several years, the furnace and LPCVD silicon parts sector has experienced transformative shifts driven by technological breakthroughs and evolving market demands. First, the development of engineered silicon carbide and silicon nitride formulations has enabled parts to endure higher temperatures and harsher chemical atmospheres, extending component lifetimes and reducing maintenance cycles. Simultaneously, advanced surface treatments-ranging from plasma-enhanced coatings to nanoparticle infusions-have improved wear resistance and thermal uniformity, meeting the exacting standards of semiconductor fabrication.
Moreover, digitalization initiatives have introduced predictive maintenance and process simulation tools that harness real-time sensor data and machine learning algorithms. These solutions optimize furnace ramp rates and deposition uniformity, minimizing variability and waste. In parallel, growing emphasis on sustainability is reshaping material selection and production methods: manufacturers are reducing energy consumption, recycling silicon waste streams, and sourcing raw materials from certified low-carbon suppliers. Collectively, these innovations are redefining performance benchmarks and creating differentiation for both equipment OEMs and component suppliers.
Cumulative Impact of United States Tariffs 2025
As of 2025, the implementation of new United States tariffs on imported silicon parts and precursor materials has introduced significant supply chain recalibrations. Tariffs levied on critical imports from key manufacturing hubs have driven material costs upward, prompting end-users to explore domestic sourcing and regional alliances. This refocusing on localized supply chains has, in turn, accelerated investments in North American and European fabrication facilities, mitigating exposure to trade policy volatility.
At the same time, companies dependent on non-tariffed alternatives are experimenting with substitute materials and reoptimized process recipes to preserve yield targets. While short-term price pressures have elevated component expenditures, the enforced shift toward supplier diversification has enhanced resilience across the ecosystem. Looking ahead, continued dialogue between industry stakeholders and policy makers will be essential to balance fair trade objectives with the imperative of maintaining seamless flows of high-purity materials critical for advanced manufacturing.
Key Segmentation Insights for Material-Based Differentiation
Segmentation based on material type reveals that silicon parts are categorized into three primary groups: silicon, silicon carbide and silicon nitride. Within the silicon grouping, monocrystalline and polycrystalline variants address distinct performance requirements-monocrystalline parts deliver superior uniformity and are predominantly used in wafer processing and precision heating applications, while polycrystalline elements offer cost-effective solutions for general-purpose furnaces. Meanwhile, silicon carbide components stand out for their exceptional thermal shock resistance and mechanical strength at extreme temperatures, making them indispensable in high-temperature reactor chambers. Silicon nitride, valued for its outstanding fracture toughness and chemical inertness, finds application in environments where corrosion resistance and impact durability are paramount.
Understanding these material-driven segments enables suppliers and end-users to align product portfolios with process specifications and cost targets. It also highlights areas ripe for innovation, such as hybrid composites that merge monocrystalline silicon’s uniformity with silicon carbide’s robustness, unlocking next-generation performance envelopes.
This comprehensive research report categorizes the Silicon Parts for Furnaces & LPCVD market into clearly defined segments, providing a detailed analysis of emerging trends and precise revenue forecasts to support strategic decision-making.
- Material Type
Key Regional Insights Influencing Demand Patterns
Regional dynamics further influence strategic priorities within the furnace and LPCVD silicon parts market. In the Americas, strong semiconductor expansion in the United States and manufacturing resurgence in Mexico have spurred demand for both high-precision monocrystalline components and rugged polycrystalline parts. Europe, the Middle East and Africa present a diverse landscape: European fabs are driving uptake of advanced silicon carbide parts for power device production, while emerging Middle Eastern and North African chip-making initiatives are increasing demand for standard furnace components and localized service capabilities. Across Asia-Pacific, capacity growth in China, Taiwan and Japan dominates the market narrative, with massive investments in semiconductor and specialty electronics fabs fueling robust requirements for all material types, particularly silicon nitride and silicon carbide for next-generation power and MEMS devices.
These regional patterns underscore the importance of aligning manufacturing footprints, inventory strategies and technical support networks with localized demand drivers and trade regulations. They also reinforce the value of region-specific R&D partnerships to co-develop tailored components that meet unique operational conditions.
This comprehensive research report examines key regions that drive the evolution of the Silicon Parts for Furnaces & LPCVD market, offering deep insights into regional trends, growth factors, and industry developments that are influencing market performance.
- Americas
- Asia-Pacific
- Europe, Middle East & Africa
Key Company Insights Driving Competitive Differentiation
A competitive analysis of leading suppliers highlights a mix of diversified specialty chemical providers, ceramics innovators and high-purity material specialists. Companies such as American Elements and CoorsTek, Inc. leverage integrated supply chains and broad portfolios spanning silicon carbides and nitrides, while Carbolite Gero and Saint-Gobain Ceramics focus on advanced furnace design and customized component assemblies. Firms like Donaldson Company, Inc. and Morgan Advanced Materials plc bring deep expertise in filtration and ceramic technologies, respectively, enabling cross-pollination of capabilities into silicon part manufacturing.
Meanwhile, regional champions such as Kyocera International, Inc., SKC Solmics Co., Ltd., and Tokai Carbon Co., Ltd. capitalize on local manufacturing scale and established relationships with major semiconductor fabs. Emerging players like EpiGaN nv and Insaco, Inc. differentiate themselves through niche process enhancements and specialized coating services. Collectively, these companies are driving the market forward through targeted R&D investments, strategic partnerships with equipment OEMs, and selective mergers and acquisitions designed to expand technical capabilities or geographic reach.
This comprehensive research report delivers an in-depth overview of the principal market players in the Silicon Parts for Furnaces & LPCVD market, evaluating their market share, strategic initiatives, and competitive positioning to illuminate the factors shaping the competitive landscape.
- American Elements
- Carbolite Gero
- CoorsTek, Inc.
- Donaldson Company, Inc.
- EpiGaN nv
- Insaco, Inc.
- Kyocera International, Inc.
- Morgan Advanced Materials plc
- Saint-Gobain Ceramics
- SGL Carbon SE
- SKC Solmics Co., Ltd.
- Tokai Carbon Co., Ltd.
- Watlow Electric Manufacturing Company
Actionable Recommendations for Industry Leaders
To thrive amid shifting policies, intensifying competition and accelerating technological change, industry leaders should pursue a multi-pronged strategy. First, diversifying supply chains by qualifying additional regional suppliers will mitigate tariff impacts and logistical bottlenecks; establishing dual-sourcing agreements in the Americas and Asia-Pacific can ensure continuity under evolving trade regulations. Second, investing in digital process control and predictive maintenance platforms will enhance yield consistency and reduce unplanned downtime, translating into lower total cost of ownership for end-users. Third, prioritizing research into hybrid material systems-such as composite silicon carbide–silicon nitride parts-can create breakthrough performance advantages and open new application segments.
Moreover, forging collaborative partnerships with key semiconductor equipment manufacturers and research institutions will accelerate co-development cycles and align product roadmaps with emerging node requirements. Engaging proactively in policy discussions and industry consortia will help shape balanced trade frameworks while preserving access to critical raw materials. Finally, embedding sustainability metrics in product development-from carbon-neutral manufacturing to circular material reuse-will meet growing environmental demands and foster stronger relationships with socially conscious customers.
Explore AI-driven insights for the Silicon Parts for Furnaces & LPCVD market with ResearchAI on our online platform, providing deeper, data-backed market analysis.
Ask ResearchAI anything
World's First Innovative Al for Market Research
Conclusion: Positioning for Sustainable Growth
The intersection of material innovation, trade policy and regional demand growth presents both challenges and opportunities for suppliers of furnace and LPCVD silicon parts. Companies that successfully navigate this landscape will be those that combine resilient supply chains with advanced digital and materials capabilities, maintain close alignment with regional fab roadmaps, and invest in sustainable practices that resonate with customers and regulators alike. By integrating these priorities into corporate strategy, suppliers can not only safeguard their operations against external shocks but also capture value from the shift toward high-performance, energy-efficient manufacturing processes.
This section provides a structured overview of the report, outlining key chapters and topics covered for easy reference in our Silicon Parts for Furnaces & LPCVD market comprehensive research report.
- Preface
- Research Methodology
- Executive Summary
- Market Overview
- Market Dynamics
- Market Insights
- Cumulative Impact of United States Tariffs 2025
- Silicon Parts for Furnaces & LPCVD Market, by Material Type
- Americas Silicon Parts for Furnaces & LPCVD Market
- Asia-Pacific Silicon Parts for Furnaces & LPCVD Market
- Europe, Middle East & Africa Silicon Parts for Furnaces & LPCVD Market
- Competitive Landscape
- ResearchAI
- ResearchStatistics
- ResearchContacts
- ResearchArticles
- Appendix
- List of Figures [Total: 18]
- List of Tables [Total: 100 ]
Call to Action: Contact Ketan Rohom for the Full Report
To access the comprehensive analysis, in-depth profiles and strategic guidance detailed in this executive summary, connect directly with Ketan Rohom, Associate Director, Sales & Marketing. Ketan can provide tailored information on report contents, pricing options and licensing terms, ensuring you secure the insights needed to make informed strategic decisions. Reach out today to accelerate your pathway to competitive advantage with the full furnace and LPCVD silicon parts market research report.
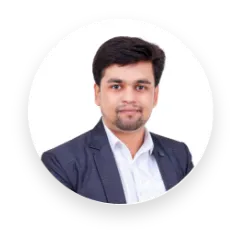
- When do I get the report?
- In what format does this report get delivered to me?
- How long has 360iResearch been around?
- What if I have a question about your reports?
- Can I share this report with my team?
- Can I use your research in my presentation?