Understanding the Evolving Demand for Double-Sided Grinding Solutions
As semiconductor fabrication demands continue to advance at an unprecedented pace, the need for precise and efficient double-sided grinding machines has taken center stage. The subtleties of thickness uniformity, surface quality, and throughput have become critical differentiators in wafer production, influencing yield, performance, and cost optimization. Against this backdrop, this executive summary delves into the forces reshaping the market, offering a comprehensive lens through which industry leaders can navigate evolving complexities.
Starting with the fundamental principles of double-sided grinding, it emphasizes how incremental improvements translate into substantial gains across the fabrication lifecycle. The current industry environment is characterized by a convergence of heightened miniaturization requirements, stringent defect control, and the relentless pursuit of lower cost per wafer. These imperatives have elevated machine precision and automation sophistication to the forefront of strategic discussions.
This introduction sets the stage for a deep dive into transformative shifts that redefine competitive advantage, the emerging impact of policy measures such as the United States tariffs scheduled for 2025, and an in-depth examination of market segmentation to uncover latent opportunities. Ultimately, it outlines the framework through which stakeholders can align their technology roadmaps, capital investments, and operational strategies to maintain leadership in this high-stakes arena.
Revolutionizing Wafer Grinding with Emerging Technologies
Over the past few years, the landscape of double-sided grinding machines has undergone a profound metamorphosis driven by technological breakthroughs and shifting production paradigms. Advanced sensor integration paired with real-time data analytics has enabled adaptive process control, shifting the industry away from static recipes to dynamic feedback loops that continuously optimize grinding performance. This transformation has resulted in a leap in consistency and throughput, empowering manufacturers to meet lean production goals without sacrificing quality.
Moreover, the integration of machine learning algorithms has ushered in predictive maintenance capabilities that reduce unscheduled downtime and extend equipment lifespans. Gone are the days when preventive maintenance was conducted on a rigid schedule; today’s systems anticipate component wear and potential drift before they impact yields, fostering an environment of proactive reliability.
Concurrently, the push toward Industry 4.0 ecosystems has intensified, with fully automatic configurations serving as central nodes within interconnected fabs. This seamless orchestration of upstream and downstream processes elevates productivity, enabling just-in-time material flows and minimizing work-in-progress inventory. The confluence of automation, data intelligence, and connectivity is redefining what a competitive grinding platform looks like, setting new benchmarks for speed, precision, and operational resilience.
Navigating the 2025 U.S. Tariff Regime on Silicon Wafer Machinery
The imposition of revised United States tariffs on imported semiconductor manufacturing equipment, slated to take effect in 2025, is poised to reshape global supply chains and cost structures. Manufacturers reliant on machinery sourced from key exporting nations face the challenge of recalibrating procurement strategies and mitigating the financial burden of higher import duties. This policy shift threatens to erode profit margins unless organizations adopt agile sourcing models or negotiate alternative supplier agreements.
In response, several industry leaders have begun exploring regional manufacturing expansions to circumvent tariff impacts, establishing local assembly and service hubs that reduce cross-border dependencies. By localizing final assembly and component integration, they aim to insulate operations from import duties while preserving access to advanced grinding technologies. This trend also fosters stronger collaboration with domestic equipment vendors, accelerating knowledge transfer and co-innovation.
Importantly, the tariffs catalyze a broader reassessment of total cost of ownership for grinding platforms. Companies are increasingly evaluating not only upfront capital expenditures but also long-term operational efficiencies, service frameworks, and upgrade pathways that deliver sustainable value under the new tariff regime. The net effect is an industry poised for strategic realignment, where agility and diversification become as crucial as technical performance.
Unveiling Market Dynamics through Comprehensive Segmentation
An in-depth examination of wafer diameter reveals that demand patterns vary significantly across the 150Mm, 200Mm, and 300Mm segments, with each size catering to distinct fabrication densities and device applications. The smallest diameters remain vital for legacy applications and specialized sensors, whereas larger diameters command share in high-volume consumer electronics, 5G communications, and advanced logic devices. Automation level further delineates market preferences, with fully automatic lines dominating cutting-edge fabs seeking zero-touch operations, while semi-automatic and manual configurations persist in cost-sensitive and low-volume environments.
The end-user landscape spans automotive sectors, encompassing both electric vehicles with stringent battery cell tolerance demands and traditional vehicles that prioritize cost efficiency in sensor integration. In consumer electronics, computing devices drive the need for unparalleled surface flatness, mobile devices impose aggressive cycle-time targets, and wearables demand ultra-thin, robust substrates. Solar manufacturing bifurcates into crystalline modules requiring high throughput and thin-film panels where material uniformity is paramount. Telecommunications equipment manufacturers insist on wafers that support emerging millimeter-wave and photonic applications.
Machine configuration options include multi head systems engineered for parallel processing, single head arrangements in both horizontal and vertical orientations to meet space or process constraints, and twin head platforms available with adjustable or fixed spindles to balance flexibility and precision. Process type segmentation distinguishes traditional grinding only approaches from integrated grinding-polishing workflows, the latter offering chemical mechanical polishing or purely mechanical polishing modules. These configurations allow fabricators to tailor their equipment investment to specific yield, planarization, and surface roughness targets, ensuring each production line aligns with application requirements.
This comprehensive research report categorizes the Silicon Wafer Double-sides Grinding Machines market into clearly defined segments, providing a detailed analysis of emerging trends and precise revenue forecasts to support strategic decision-making.
- Wafer Diameter
- Automation Level
- End-User Industry
- Machine Configuration
- Process Type
Regional Trends Shaping the Future of Grinding Equipment
The Americas region encompasses North and South American operations where advanced automotive semiconductor applications and mobile device production create strong demand for high-precision double-sided grinding tools. Local capacity expansions and a growing emphasis on reshoring key fab equipment contribute to healthy growth trajectories in this hemisphere.
Across Europe, the Middle East & Africa, semiconductor manufacturers navigate a complex regulatory environment and diverse end-user needs, from automotive electronics clusters in Germany to renewable energy initiatives in the UAE. Here, the interplay between tightening environmental standards and bespoke manufacturing requirements shapes the adoption of grinding platforms designed for minimal waste and optimized resource usage.
Asia-Pacific emerges as the focal point of global wafer production, driven by sprawling consumer electronics hubs, robust solar panel installations, and a national mandate in several markets to bolster domestic semiconductor prowess. In this theater, competition among equipment suppliers is intense, prompting rapid innovation cycles and aggressive investment in localized customer support infrastructures. Such dynamics ensure that Asia-Pacific remains the epicenter of both demand growth and technological advancement in double-sided grinding machines.
This comprehensive research report examines key regions that drive the evolution of the Silicon Wafer Double-sides Grinding Machines market, offering deep insights into regional trends, growth factors, and industry developments that are influencing market performance.
- Americas
- Europe, Middle East & Africa
- Asia-Pacific
Identifying Key Players Driving Grinding Machine Innovation
A handful of leading manufacturers exert significant influence over product roadmaps and industry benchmarks. These firms consistently invest in research to refine spindle stability, optimize wafer handling modules, and integrate advanced metrology instruments. Their deep service networks and global footprint enable rapid installation, calibration, and field upgrades, reinforcing customer loyalty and driving incremental revenue through aftermarket services.
In addition to established players, emerging enterprises are carving niches by delivering specialized solutions such as compact systems tailored for research institutions or high-speed platforms optimized for large-scale solar cell production. These challengers leverage agile development processes to bring next-generation features-like artificial intelligence-driven adaptive grinding algorithms-to market at a faster pace.
Collaborations between equipment vendors and semiconductor fabs further accelerate innovation, as joint development programs facilitate co-optimized solutions that address the exacting requirements of advanced processes. Through these strategic partnerships, the ecosystem continues to evolve toward more modular, upgradeable architectures that extend machine lifecycles and lower total cost of ownership.
This comprehensive research report delivers an in-depth overview of the principal market players in the Silicon Wafer Double-sides Grinding Machines market, evaluating their market share, strategic initiatives, and competitive positioning to illuminate the factors shaping the competitive landscape.
- DISCO Corporation
- Tokyo Seimitsu Co., Ltd.
- Lapmaster Wolters, Inc.
- Okamoto Machine Tool Works, Ltd.
- Strasbaugh, Inc.
- Nanjing Sanjia Precision Machinery Co., Ltd.
- Vertex Systems Co., Ltd.
- Taian Tools Co., Ltd.
- Seibu Giken DST Co., Ltd.
- Hangzhou Xiantuo Precision Technology Co., Ltd.
Strategic Actions to Capitalize on Grinding Market Opportunities
To harness the full potential of this evolving market, industry leaders should adopt a dual focus on technology differentiation and supply chain resilience. Establishing strategic partnerships with multiple machine suppliers can mitigate the risks posed by tariff fluctuations and ensure access to a diverse pool of capabilities. Concurrently, investing in flexible automation frameworks will enable rapid reconfiguration of production lines in response to shifting product mixes or wafer size transitions.
Operational excellence should be underscored by the integration of predictive analytics within quality control protocols, allowing defects to be detected and corrected in real time. By embedding advanced sensor suites and data-driven decision engines, manufacturers can reduce scrap rates and maximize throughput consistency. Furthermore, piloting integrated grinding-polishing solutions can yield significant time savings and surface quality improvements, particularly in high-precision markets such as automotive sensors and photonic wafers.
Finally, stakeholders should monitor geopolitical developments closely, preemptively adjusting sourcing strategies and exploring local content partnerships. By diversifying manufacturing footprints and fostering collaborative relationships with regional equipment providers, organizations will position themselves to absorb policy shocks and capitalize on emerging market inflections.
Robust Framework Underpinning the Research Insights
The research underpinning these insights employs a multi-tiered approach, beginning with extensive primary interviews conducted with equipment engineers, process development managers, and procurement directors across leading semiconductor manufacturing facilities. These firsthand perspectives ensured a granular understanding of operational pain points and technology aspirations.
Secondary research complemented this foundation, drawing upon patent filings, technical white papers, industry conference proceedings, and regulatory filings to map technology trajectories and policy impacts. Market segmentation classifications were validated through cross-referencing machinery shipment data and end-user purchasing behavior, ensuring that diameter, automation, end-user industry, machine configuration, and process type categories accurately reflected real-world adoption patterns.
Quantitative analysis incorporated historical equipment installation statistics and maintenance expenditure records to contextualize growth drivers without relying on projected market sizing. Concurrently, qualitative assessments examined case studies of leading fabs, highlighting best practices in machine deployment, automation integration, and supply chain management. This rigorous methodology yields a holistic portrait of the current state of double-sided grinding machines and the forces poised to shape its trajectory.
Explore AI-driven insights for the Silicon Wafer Double-sides Grinding Machines market with ResearchAI on our online platform, providing deeper, data-backed market analysis.
Ask ResearchAI anything
World's First Innovative Al for Market Research
Harnessing Insights to Drive the Next Generation of Grinding Machines
In an era defined by the relentless drive toward greater yield, faster cycle times, and tighter tolerances, the insights presented herein illuminate the pathways to operational excellence in double-sided grinding. By understanding the technological shifts reshaping machine capabilities and the policy environment influencing capital decisions, stakeholders can align their strategies with both near-term imperatives and long-term industry evolution.
Segmentation analysis clarifies where growth pockets exist, whether in specific wafer sizes, automation tiers, or application segments such as electric vehicle sensors or renewable energy photovoltaics. Regional insights highlight how localized dynamics-from reshoring trends in the Americas to the innovation crucible of Asia-Pacific-will dictate investment priorities. Meanwhile, key company profiles underscore the importance of partnering with vendors that not only deliver high-precision platforms but also commit to continuous service excellence and collaborative development.
Armed with these findings, decision-makers can formulate action plans that balance disruption readiness with sustainable performance gains. The future of double-sided grinding machines belongs to those who integrate advanced analytics, agile automation, and resilient supply chain architectures into their core operations, thereby transforming raw wafers into the devices that define tomorrow’s digital age.
This section provides a structured overview of the report, outlining key chapters and topics covered for easy reference in our Silicon Wafer Double-sides Grinding Machines market comprehensive research report.
- Preface
- Research Methodology
- Executive Summary
- Market Overview
- Market Dynamics
- Market Insights
- Cumulative Impact of United States Tariffs 2025
- Silicon Wafer Double-sides Grinding Machines Market, by Wafer Diameter
- Silicon Wafer Double-sides Grinding Machines Market, by Automation Level
- Silicon Wafer Double-sides Grinding Machines Market, by End-User Industry
- Silicon Wafer Double-sides Grinding Machines Market, by Machine Configuration
- Silicon Wafer Double-sides Grinding Machines Market, by Process Type
- Americas Silicon Wafer Double-sides Grinding Machines Market
- Europe, Middle East & Africa Silicon Wafer Double-sides Grinding Machines Market
- Asia-Pacific Silicon Wafer Double-sides Grinding Machines Market
- Competitive Landscape
- ResearchAI
- ResearchStatistics
- ResearchContacts
- ResearchArticles
- Appendix
- List of Figures [Total: 26]
- List of Tables [Total: 501 ]
Secure the Full Report and Connect with Ketan Rohom
To explore these critical findings in greater detail and to secure your competitive advantage, reach out to Ketan Rohom, Associate Director, Sales & Marketing. His expertise will guide you through the comprehensive report, enabling you to make informed decisions and accelerate growth in the silicon wafer double-sided grinding machine market. Connect today to transform insight into action and stay ahead in this dynamic landscape.
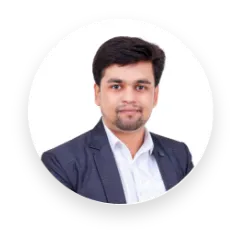
- When do I get the report?
- In what format does this report get delivered to me?
- How long has 360iResearch been around?
- What if I have a question about your reports?
- Can I share this report with my team?
- Can I use your research in my presentation?