Setting the Stage: Advances and Imperatives in Silicone Resin Coatings
Silicone resins have emerged as indispensable components in industrial coatings, offering unique thermal stability, weather resistance, and adhesion properties that traditional polymer systems cannot match. The growing demand for durable surface protection in sectors such as automotive, construction, and petrochemicals has propelled silicone resins into the spotlight. Technological advancements in resin chemistry, coupled with evolving application methods, are unlocking new performance thresholds, while environmental regulations continue to drive formulations toward lower volatile organic compounds and enhanced sustainability.
Against this backdrop, stakeholders across the value chain-from resin manufacturers to end-use consumers-are reassessing their strategies to capitalize on the expanding opportunities. Research and development efforts are increasingly focused on tailoring resin backbones, functional groups, and curing mechanisms to meet the exacting demands of high-temperature and corrosive environments. Simultaneously, supply chain dynamics, raw material availability, and regulatory frameworks are influencing market entry and growth potential. This introduction sets the stage for a deeper exploration of the forces shaping the silicone resin landscape and the strategic considerations essential for industry success.
Evolving Dynamics Reshaping Silicone Resins in Industrial Coatings
In recent years, a confluence of technological breakthroughs and shifting market priorities has redefined the silicone resin industry. The integration of fumed silica into resin matrices has unlocked unprecedented mechanical reinforcement, enabling coatings to withstand harsher operating conditions. Concurrently, methyl-silicone formulations have been refined to balance viscosity and reactivity, catering to a spectrum of processing requirements from high-viscosity castings to low-viscosity spray applications. Phenyl-modified resins, especially those with elevated phenyl content, are gaining traction for their superior thermal stability and ultraviolet resistance, expanding their use in exterior architectural coatings and protective marine finishes.
Beyond chemistry, application innovations are redefining performance benchmarks. The migration toward high-temperature coatings for industrial ovens and petrochemical equipment underscores the need for formulations that can endure rapid thermal cycling while maintaining adhesion. Wood finish applications continue to leverage silicone alkyd blends, marrying the resilience of silicone with the aesthetic warmth of traditional alkyds. These transformative shifts reflect a broader trend: the pursuit of multifunctional coatings that address durability, safety, and sustainability in equal measure. As industry leaders adapt to evolving performance requirements and regulatory mandates, the capacity to innovate at the molecular level and optimize processing workflows will determine competitive advantage.
How 2025 Tariffs Are Reconfiguring the US Silicone Resin Ecosystem
The introduction of new United States tariffs in 2025 has reverberated across the silicone resin supply chain, challenging established trade patterns and cost structures. Increased duties on imported raw silicone-based intermediates have prompted domestic producers to reevaluate sourcing strategies. Some manufacturers have accelerated local production expansion, investing in capacity upgrades to reduce dependence on tariff-exposed imports. Others have sought tariff relief through trade agreements and duty drawback programs, navigating complex customs regulations to maintain margin integrity.
End-users are likewise responding to the cost pressures. Coating formulators are exploring alternative chemistries and locally available siloxane precursors to soften the impact of import levies. Petrochemical equipment coating providers, in particular, are experimenting with in-house blending and resin recovery techniques to stabilize production costs. While short-term disruptions in supply chains have created volatility in pricing, these adjustments are fostering greater resilience. Over time, the market is likely to see a realignment as regional value chains become more self-contained, and innovation in raw-material alternatives gains momentum. Ultimately, the cumulative effect of the 2025 tariff changes will shape both procurement strategies and the competitive landscape in the U.S. silicone resin market.
Unpacking Market Segmentation for Precision in Silicone Resin Applications
A nuanced segmentation framework illuminates the diverse value pools within the silicone resin market. When evaluated by resin type, the landscape encompasses specialized classes such as fumed silica modified resin, highly crosslinked methyl silicone resin available in both high and low viscosities, phenyl silicone resin offered in formulations with varying phenyl content, and versatile silicone alkyd resin blends. Application-based segmentation reveals three core categories: anti-foaming agents for process optimization, high-temperature coatings tailored for both industrial ovens and petrochemical equipment, and decorative as well as protective wood finishes. Examining end-use industries highlights the automotive sector’s dual demand from original equipment manufacturers and aftermarket refinishing, the construction industry’s push for durable façade and interior coatings, the electrical and electronics segment’s need for arc-resistant conformal coatings and potting systems, and marine applications requiring robust corrosion protection. Considering form factor, emulsions deliver ease of handling, liquid resins are offered in both solvent-based and water-based systems for flexible formulation design, powders facilitate application efficiency, and solid resins-available as flakes or granules-enable clean, operator-friendly dosing. This holistic segmentation provides stakeholders with precise insights to tailor product development, optimize supply chains, and prioritize market entry strategies.
This comprehensive research report categorizes the Silicone Resins for Industrial Coatings market into clearly defined segments, providing a detailed analysis of emerging trends and precise revenue forecasts to support strategic decision-making.
- Resin Type
- Application
- End Use Industry
- Form
Regional Pathways Driving Growth in Silicone Resin Markets
Regional variations in industrial growth dynamics, regulatory environments, and raw material availability underpin distinct market trajectories across the globe. In the Americas, demand is buoyed by the automotive aftermarket’s appetite for high-performance refinish coatings and an expanding infrastructure sector investing in long-life architectural surfaces. European, Middle Eastern, and African markets present a complex mosaic of mature Western European economies, emerging Middle Eastern industrial hubs, and African construction markets, each driving tailored demands for low-emission, high-temperature, and UV-resistant coatings. Meanwhile, Asia-Pacific stands out as the fastest-growing region, propelled by robust manufacturing capacity expansion in China and India, significant capital expenditure in petrochemical facilities, and an ever-increasing focus on sustainable building materials in developed economies like Japan and South Korea. Understanding these regional nuances is critical for aligning production footprints, navigating local compliance, and forging partnerships that accelerate commercial success.
This comprehensive research report examines key regions that drive the evolution of the Silicone Resins for Industrial Coatings market, offering deep insights into regional trends, growth factors, and industry developments that are influencing market performance.
- Americas
- Europe, Middle East & Africa
- Asia-Pacific
Competitive Landscape and Strategic Moves in Silicone Resin Manufacturing
The competitive landscape is characterized by legacy chemical producers, specialty resin innovators, and integrated industrial conglomerates vying for market share. Leading global manufacturers have leveraged scale to secure preferential access to siloxane feedstocks, enabling them to invest heavily in R&D for next-generation elastomeric and thermoset formulations. A number of specialty firms have differentiated by focusing on niche chemistries-such as high-phenyl resins for aerospace-grade coatings and ultra-low viscosity methyl silicones for electronics potting-capturing premium segments. Strategic partnerships and joint ventures are reshaping capabilities, with alliances between resin producers and coating formulators expediting the path from lab to market. Meanwhile, regional players are consolidating their positions by expanding local manufacturing and tailoring service models to meet proximity and responsiveness requirements. This multiplicity of competitive approaches underscores the importance of agility and deep technical expertise in securing sustainable growth.
This comprehensive research report delivers an in-depth overview of the principal market players in the Silicone Resins for Industrial Coatings market, evaluating their market share, strategic initiatives, and competitive positioning to illuminate the factors shaping the competitive landscape.
- Shin-Etsu Chemical Co., Ltd.
- Wacker Chemie AG
- Dow Inc.
- Evonik Industries AG
- Momentive Performance Materials Inc.
- Elkem Silicones
- KCC Corporation
- J.M. Huber Corporation
- DIC Corporation
- Gelest, Inc.
Strategic Imperatives for Leading in the Silicone Resin Industry
Industry leaders must adopt a multi-pronged strategy to navigate the evolving silicone resin environment. Firstly, accelerating innovation pipelines through collaborative R&D can unlock breakthrough performance properties while sharing development risk. Co-development partnerships with equipment manufacturers and end-users will ensure formulations address real-world application challenges and regulatory shifts. Secondly, supply chain resilience must be fortified by diversifying siloxane sourcing, integrating backward where feasible, and establishing contingency stocks to mitigate tariff and logistical disruptions. Thirdly, market positioning should be sharpened by leveraging advanced digital tools-from predictive analytics for demand forecasting to customer portals that enhance order transparency-driving operational excellence and strengthening client relationships. Finally, sustainability imperatives call for heightened investment in low-VOC, bio-based, and recyclable resin platforms, signaling a commitment to environmental stewardship and appealing to ESG-conscious buyers. By executing on these imperatives, organizations can secure competitive differentiation and long-term profitability.
Rigorous Approach Underpinning the Silicone Resin Market Analysis
This analysis draws upon a robust methodology combining primary interviews with resin formulators, coating application specialists, and procurement executives, alongside secondary data from regulatory filings, patent databases, and industry publications. Proprietary supply-chain mapping tools were employed to chart raw material flows and identify tariff-sensitive nodes. The segmentation framework was validated through cross-referenced corporate disclosures and trade association reports, ensuring each resin type, application, end-use industry, and form factor is accurately represented. Pricing and margin benchmarks were established using a mix of public tender results and confidential financial models, while regional demand projections were informed by industrial output statistics and capital expenditure trends. Rigorous triangulation techniques have been applied to mitigate bias and ensure confidence in the insights presented, providing a reliable foundation for strategic decision-making.
Explore AI-driven insights for the Silicone Resins for Industrial Coatings market with ResearchAI on our online platform, providing deeper, data-backed market analysis.
Ask ResearchAI anything
World's First Innovative Al for Market Research
Synthesis of Trends and Strategic Outlook for Silicone Coatings
Silicone resins stand at the crossroads of innovation and industrial demand, delivering performance characteristics that are critical to modern coatings applications. The convergence of high-temperature resilience, enhanced mechanical properties, and evolving regulatory landscapes is redefining competitive dynamics. Segmentation analysis reveals targeted opportunities in specialized resin types, application niches, end-use industries, and form factors, while regional insights highlight differentiated growth paths across the Americas, Europe, Middle East and Africa, and Asia-Pacific. With new trade measures influencing cost structures and supply chains, strategic agility and collaborative innovation will determine market leaders. By embracing the recommendations outlined herein, stakeholders can harness the transformative potential of silicone resins to drive sustainable growth and maintain technological leadership in a rapidly evolving marketplace.
This section provides a structured overview of the report, outlining key chapters and topics covered for easy reference in our Silicone Resins for Industrial Coatings market comprehensive research report.
- Preface
- Research Methodology
- Executive Summary
- Market Overview
- Market Dynamics
- Market Insights
- Cumulative Impact of United States Tariffs 2025
- Silicone Resins for Industrial Coatings Market, by Resin Type
- Silicone Resins for Industrial Coatings Market, by Application
- Silicone Resins for Industrial Coatings Market, by End Use Industry
- Silicone Resins for Industrial Coatings Market, by Form
- Americas Silicone Resins for Industrial Coatings Market
- Europe, Middle East & Africa Silicone Resins for Industrial Coatings Market
- Asia-Pacific Silicone Resins for Industrial Coatings Market
- Competitive Landscape
- ResearchAI
- ResearchStatistics
- ResearchContacts
- ResearchArticles
- Appendix
- List of Figures [Total: 24]
- List of Tables [Total: 458 ]
Engage with Our Expert to Access the Comprehensive Silicone Resin Report
To explore these insights in depth and secure your copy of the full silicone resin market research report, reach out to Ketan Rohom, Associate Director of Sales & Marketing. His expertise will guide you through the report’s value, subscription options, and tailored licensing solutions. Engage now to leverage timely data and strategic analysis that will empower your organization’s growth in the dynamic world of industrial silicone coatings.
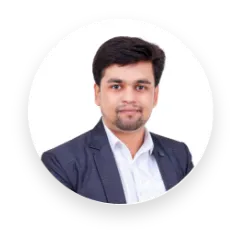
- When do I get the report?
- In what format does this report get delivered to me?
- How long has 360iResearch been around?
- What if I have a question about your reports?
- Can I share this report with my team?
- Can I use your research in my presentation?