The Sintering Market size was estimated at USD 1.74 billion in 2024 and expected to reach USD 1.83 billion in 2025, at a CAGR 5.48% to reach USD 2.39 billion by 2030.

Unveiling the Dynamics of the Sintering Landscape
Sintering stands as a cornerstone of advanced materials manufacturing, enabling the creation of components with complex geometries, precise tolerances, and tailored material properties. From traditional powder metallurgy applications to cutting-edge additive manufacturing processes, sintering technology influences sectors ranging from aerospace to healthcare. This report delves into the market forces, technological innovations, and strategic imperatives that are reshaping the global sintering landscape.
As demand for lightweight, high-performance materials intensifies, manufacturers are pushing the boundaries of sintering capabilities. The drive toward sustainability, efficiency, and digitalization further fuels the adoption of novel sintering techniques. This executive summary provides a concise yet comprehensive overview of the critical trends, segmentation insights, regional dynamics, and competitive developments that will define the industry’s trajectory in the coming years.
Evolutionary Forces Redefining Sintering Technologies
Over the past decade, sintering has undergone transformative shifts propelled by advancements in process control, materials science, and digital integration. Hybrid sintering approaches, which combine additive manufacturing with post-sintering densification, have emerged to reconcile precision and throughput. Meanwhile, innovations in microwave and spark plasma sintering are reducing cycle times and enabling the consolidation of materials previously considered challenging.
Concurrently, the integration of real-time monitoring systems and closed-loop control has ushered in Industry 4.0–era capabilities. Smart furnaces equipped with sensor networks now facilitate predictive maintenance, optimize energy consumption, and enhance consistency across batches. These technological leaps are accompanied by a growing emphasis on circular economy principles, driving investment in recycling and reuse of powder feedstocks. Taken together, these forces are redefining what sintering can achieve and unlocking new applications across key industries.
Assessing the Ripple Effects of 2025 US Tariff Measures
The introduction of united states tariff adjustments in early 2025 has had a profound effect on global sintering value chains. Import duties on select metal and ceramic powders prompted a strategic shift, as domestic producers scaled up capacity to offset rising input costs. Exporters in Asia-Pacific reconfigured supply routes, seeking duty-free corridors and leveraging free-trade agreements to maintain competitive pricing.
These tariff measures also stimulated accelerated investment in local powder manufacturing and advanced process equipment. Companies responded by diversifying raw material sourcing and establishing joint ventures in tariff-resilient markets. At the same time, downstream equipment providers intensified collaborations with regional partners to mitigate logistics complexities. The net result is a more resilient and decentralized sintering ecosystem that balances cost pressures with supply chain agility.
Deep Dive into Market Segmentation Dimensions
Segmentation analysis reveals nuanced opportunities across material classes, process types, end-use industries, and equipment categories. In the materials domain, ceramic powders continue to expand with innovations in oxide and non-oxide formulations, while composite blends are engineered for tailored thermal and mechanical performance. Metal powders, spanning ferrous and non-ferrous varieties, are seeing heightened demand for high-strength, corrosion-resistant applications. Polymer powder developments focus on high-temperature polymers that complement metal and ceramic substrates.
On the process dimension, hot isostatic pressing retains its position for critical aerospace and medical components, whereas pressureless sintering and microwave sintering are gaining traction for high-volume, cost-sensitive applications. Spark plasma sintering emerges as a versatile solution for rapid prototyping and research-driven development. End-use industries such as aerospace, automotive, and healthcare continue to drive R&D investments, while construction, electronics, and energy sectors accelerate adoption of sintered parts. Equipment choices balance batch furnaces for flexibility against continuous furnaces for steady-state throughput, enabling manufacturers to align capital expenditure with production requirements.
This comprehensive research report categorizes the Sintering market into clearly defined segments, providing a detailed analysis of emerging trends and precise revenue forecasts to support strategic decision-making.
- Material
- Process Type
- End Use Industry
- Equipment Type
Regional Dynamics Shaping Sintering Adoption Patterns
Regional dynamics underscore diverse growth trajectories and strategic priorities. In the Americas, demand is propelled by a robust aerospace sector and automotive electrification initiatives, prompting investments in hybrid sintering systems and localized powder production. Europe, Middle East & Africa benefit from stringent environmental regulations and sustainability mandates, accelerating adoption of energy-efficient microwave and hybrid sintering technologies. Meanwhile, Asia-Pacific leads in volume, with manufacturing hotspots in China, Japan, and South Korea scaling up capacity for metal and ceramic powders while fostering advanced additive-assisted sintering.
Each region presents distinct regulatory frameworks, supply chain structures, and end-user demands. Companies navigating these landscapes must tailor their value propositions, calibrate pricing strategies, and forge strategic alliances. The convergence of regulatory compliance, cost optimization, and technological differentiation will define competitive success across these geographies.
This comprehensive research report examines key regions that drive the evolution of the Sintering market, offering deep insights into regional trends, growth factors, and industry developments that are influencing market performance.
- Americas
- Europe, Middle East & Africa
- Asia-Pacific
Profiling Leaders Driving Sintering Innovation
Industry leaders are distinguished by their integrated offerings and collaborative innovation models. Established powder metallurgy firms have expanded into advanced process equipment, delivering turnkey solutions that span powder production to sintering furnaces. Concurrently, additive manufacturing pioneers are entering the sintering space, leveraging their expertise in digital part design and process simulation. Strategic alliances between materials suppliers and equipment manufacturers are accelerating time-to-market for novel sintering workflows.
Companies investing in digital services-ranging from remote furnace monitoring to AI-driven process optimization-are gaining an edge. Partnerships with research institutions and cross-industry consortia are fueling breakthrough developments in high-entropy alloys, functionally graded materials, and multi-material sintering platforms. As competition intensifies, the ability to deliver consistent quality, rapid scaling, and sustainable operations will be the hallmark of market champions.
This comprehensive research report delivers an in-depth overview of the principal market players in the Sintering market, evaluating their market share, strategic initiatives, and competitive positioning to illuminate the factors shaping the competitive landscape.
- Ipsen International Holding GmbH
- SECO/WARWICK S.A.
- Tenova S.p.A.
- ALD Vacuum Technologies GmbH
- Nabertherm GmbH
- Carbolite Gero Limited
- ECM Technologies, Inc.
- Thermcraft, Inc.
- The Lenton Industrial Furnace Company Limited
- Meteoric Technical Services Limited
Strategic Imperatives for Industry Leadership
To capture emerging opportunities, industry leaders should prioritize investments in smart sintering technologies that integrate sensor networks, data analytics, and closed-loop control. Cultivating partnerships across the supply chain-from powder producers to end-use manufacturers-will enable co-development of specialized materials and processes. Expanding regional manufacturing footprints in tariff-sensitive markets can mitigate cost pressures while enhancing customer proximity.
Furthermore, embedding sustainability at the core of operations-through recycled feedstocks, energy-efficient furnace designs, and lifecycle assessment tools-will address regulatory and customer demands. Organizations should also foster a culture of continuous learning by collaborating with academic and research institutions, accelerating the commercialization of next-generation sintering modalities. Finally, developing modular, scalable equipment platforms will allow rapid adaptation to shifting production volumes and material requirements.
Rigorous Methodological Framework Underpinning Analysis
This analysis draws on a triangulated research framework combining primary interviews with sintering technologists, equipment OEM executives, and end-user procurement leaders. Secondary sources include industry journals, technical white papers, patent filings, and regulatory filings. Data validation employed cross-referencing of proprietary shipment records, tariffs schedules, and investment announcements.
Quantitative insights were supplemented by qualitative assessments of innovation pipelines, partnership ecosystems, and sustainability initiatives. Regional market dynamics were mapped through trade flow analyses and policy reviews. The rigorous methodology ensures that findings reflect current market realities and technical advancements while providing a robust foundation for strategic decision-making.
Explore AI-driven insights for the Sintering market with ResearchAI on our online platform, providing deeper, data-backed market analysis.
Ask ResearchAI anything
World's First Innovative Al for Market Research
Synthesizing Insights to Inform Forward Planning
The sintering market stands at an inflection point, shaped by technological breakthroughs, evolving trade policies, and shifting end-use demands. Segmentation insights highlight the interplay between material innovation, process evolution, and industry-specific requirements. Regional analyses underscore the importance of tailored strategies to navigate diverse regulatory and economic environments.
As the competitive landscape intensifies, companies that harness data-driven methodologies, forge strategic collaborations, and champion sustainability will lead the next wave of growth. This executive summary provides the foundational insights necessary to chart a clear path forward in a dynamic market environment.
This section provides a structured overview of the report, outlining key chapters and topics covered for easy reference in our Sintering market comprehensive research report.
- Preface
- Research Methodology
- Executive Summary
- Market Overview
- Market Dynamics
- Market Insights
- Cumulative Impact of United States Tariffs 2025
- Sintering Market, by Material
- Sintering Market, by Process Type
- Sintering Market, by End Use Industry
- Sintering Market, by Equipment Type
- Americas Sintering Market
- Europe, Middle East & Africa Sintering Market
- Asia-Pacific Sintering Market
- Competitive Landscape
- ResearchAI
- ResearchStatistics
- ResearchContacts
- ResearchArticles
- Appendix
- List of Figures [Total: 24]
- List of Tables [Total: 284 ]
Engage with Our Expert to Access Complete Market Intelligence
Ready to elevate your strategic positioning with unparalleled insights into the sintering market? Reach out to Ketan Rohom, Associate Director of Sales & Marketing, to explore how this in-depth report can empower your decision-making and drive sustained growth. Engage now to secure a comprehensive analysis that illuminates market dynamics, competitive benchmarks, and actionable strategies tailored to your aspirations.
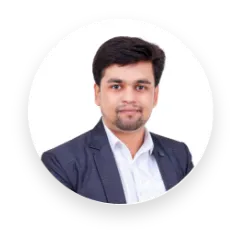
- How big is the Sintering Market?
- What is the Sintering Market growth?
- When do I get the report?
- In what format does this report get delivered to me?
- How long has 360iResearch been around?
- What if I have a question about your reports?
- Can I share this report with my team?
- Can I use your research in my presentation?