Introduction to Sintered Silicon Carbide and Its Industrial Significance
Sintered silicon carbide has emerged as a cornerstone of high-performance ceramic engineering, combining exceptional hardness, thermal shock resistance, and chemical inertness. This introduction outlines the fundamental principles of the sintering process for silicon carbide, highlighting how controlled temperature, pressure, and atmosphere converge to create a material capable of withstanding extreme environments. By leveraging advanced sintering techniques, manufacturers can tailor microstructures to meet demanding specifications across sectors ranging from aerospace to energy.
Leveraging the intrinsic properties of silicon carbide, sintering transforms powdered raw materials into dense, near-net-shape components with superior mechanical strength. Critical stages include particle packing, binder removal, and densification under high-temperature conditions-each step demanding precise process control. As the market evolves, innovations in process parameters and material formulations continue to push performance boundaries, enabling components that outperform traditional ceramics.
This overview sets the scene for a deeper exploration of industry shifts, policy impacts, segmentation dynamics, regional trends, competitive landscapes, and strategic recommendations. Readers will gain insights into how emerging sintering processes and market forces are reshaping silicon carbide production, and how industry leaders can capitalize on opportunities presented by this ever-advancing technology.
Key Technological and Sustainability Shifts Reshaping the Industry
The landscape of silicon carbide sintering is experiencing transformative shifts driven by technological breakthroughs and sustainability imperatives. Recent advancements in spark plasma sintering and hybrid manufacturing are enabling densification at lower temperatures and reduced cycle times, while pressureless sintering variants-such as nanostructured pressureless approaches-are unlocking new pathways to finer grain sizes and enhanced mechanical properties.
Moreover, digital process monitoring and automation are improving repeatability and yield, as process automation platforms integrate real-time data analytics to fine-tune temperature profiles and pressure parameters. Sustainability developments are equally impactful: energy efficiency initiatives and renewable energy integration within sintering furnaces are reducing carbon footprints and operational costs.
Furthermore, the demand for breakthrough materials has spurred innovation insights in both abrasive and electronic grades, leading to future advanced abrasives that deliver superior cutting performance and next-generation electronic grade silicon carbide for power electronics. As hybrid manufacturing and future integrated processes gain traction, the sintered silicon carbide market is positioned for significant evolution, underscoring the need for stakeholders to stay ahead of these dynamic shifts.
Assessing the 2025 US Tariff Impact on Supply Chains and Costs
The imposition of new United States tariffs in 2025 has had a cumulative impact on the silicon carbide supply chain and cost structures. Higher duties on imported feedstock and sintered components have increased energy and material cost pressures, prompting manufacturers to re-evaluate sourcing strategies. Companies facing elevated labor and production costs have accelerated efforts to adopt energy-efficient sintering optimization techniques and explore renewable energy integration within their facilities.
In response, several producers have diversified their supply chains, forging partnerships with domestic raw material processors to mitigate the risk of tariff-induced volatility. This strategic pivot has also spurred investment in advanced manufacturing techniques, such as hybrid manufacturing, to reduce dependency on external suppliers. While short-term margin compression has been observed, the drive toward process automation and future cost innovations is expected to offset these pressures over time.
However, the tariff environment has reinforced the importance of demand analysis and sustainability developments, as end users in aerospace, automotive, and energy sectors scrutinize total cost of ownership. By anticipating regulatory changes and aligning production strategies with cost management imperatives, industry players can maintain competitiveness despite the evolving trade landscape.
In-Depth Segmentation Insights Across Material, Process, and Cost Dimensions
Segmentation analysis reveals nuanced opportunities and challenges across multiple dimensions. Based on material grade, abrasive grade offerings are diversifying into future advanced abrasives and high performance abrasives, while electronic grade formulations are optimized for power devices and industrial grade materials support harsh environment applications.
Examining sintering processes, hot pressing remains essential for high-density components, whereas pressureless sintering is branching into emerging variants and nanostructured pressureless techniques. Spark plasma sintering continues to gain traction for rapid densification and fine grain control.
In applications, electrical components benefit from precise dimensional control, heat exchangers exploit silicon carbide’s thermal conductivity, and structural components are evolving toward future structural innovations and load bearing structures that enhance mechanical resilience.
End users in aerospace demand lightweight, high-temperature parts, automotive segments focus on future mobility solutions and performance vehicles, energy infrastructures seek corrosion-resistant modules, and industrial equipment manufacturers prioritize durability.
Production technology segmentation highlights advanced manufacturing techniques progressing to future integrated processes and hybrid manufacturing, raw material processing improvements, and sintering optimization efforts centered on energy efficiency and process automation.
Market trends emphasize demand analysis, while innovation insights spotlight breakthrough materials and emerging processes, and sustainability developments guide eco-conscious strategies.
Cost analysis underlines energy cost pressures-addressed through future cost innovations and renewable energy integration-alongside labor, material, and production cost considerations.
This comprehensive research report categorizes the Sintering Silicon Carbide market into clearly defined segments, providing a detailed analysis of emerging trends and precise revenue forecasts to support strategic decision-making.
- Material Grade
- Sintering Process
- Applications
- End User
- Production Technology
- Market Trends
- Cost Analysis
Regional Dynamics and Their Influence on Market Development
Regional dynamics play a pivotal role in shaping market trajectories. In the Americas, strong investments in automotive and energy infrastructure are fueling demand for high-performance abrasive and industrial grade silicon carbide, while leading manufacturers expand capacity to support North American markets.
Over in Europe, Middle East & Africa, stringent environmental regulations and ambitious sustainability targets are accelerating adoption of energy-efficient sintering optimization and renewable energy integration. Key applications in aerospace and structural components benefit from regional expertise in process automation and advanced manufacturing techniques.
Meanwhile, Asia-Pacific remains the largest consumer and producer hub, driven by rapid industrialization, extensive electronics manufacturing, and growing energy sector investments. Emerging variants of pressureless sintering and hybrid manufacturing are proliferating across China, Japan, and South Korea, where technological innovation and government incentives support breakthrough materials and future integrated processes.
These regional insights underline the importance of tailoring strategies to local regulatory frameworks, infrastructure capabilities, and end user demands to maximize market penetration and operational efficiency.
This comprehensive research report examines key regions that drive the evolution of the Sintering Silicon Carbide market, offering deep insights into regional trends, growth factors, and industry developments that are influencing market performance.
- Americas
- Asia-Pacific
- Europe, Middle East & Africa
Competitive Landscape: Leading Innovators and Specialized Players
A competitive landscape featuring both global conglomerates and specialized players is driving continuous innovation. Major corporations such as 3M Advanced Ceramics Division, Saint-Gobain Ceramics & Plastics and Morgan Advanced Materials PLC have established comprehensive portfolios covering abrasive, electronic, and industrial grades. At the same time, companies like CoorsTek Ceramics Inc. and Mitsubishi Materials Corporation are investing heavily in process automation and sintering optimization to enhance throughput and energy efficiency.
Meanwhile, nimble specialists including American Sintering Technologies LLC, Frontier Materials Sintering Ltd. and Stellar Sintering Innovations are pioneering breakthrough materials and emerging processes via Spark Plasma Sintering and nanostructured pressureless approaches. Dow Corning Silicon Technologies LLC, Tokuyama Silicon Materials and Wacker Chemie Silicon Division continue to bolster raw material processing capabilities, ensuring consistent supply and material purity.
Complementing these efforts, precision engineering outfits such as CeramTec International GmbH, Precision Ceramics Inc. and Schunk Ceramics Corporation deliver tailored solutions for load bearing structures and performance vehicles, while Scientific partners like PolySinter Tech Solutions, PSI Sintering Technologies and Showa Denko Advanced Ceramics drive research in future integrated processes.
Collectively, this diverse array of players-from Global Ceramics Inc. and HighTemp Ceramics Group to Innovate Silicon Ceramics and TechSinter Materials Corp.-is shaping a market defined by technological advancement, strategic partnerships and relentless cost innovation.
This comprehensive research report delivers an in-depth overview of the principal market players in the Sintering Silicon Carbide market, evaluating their market share, strategic initiatives, and competitive positioning to illuminate the factors shaping the competitive landscape.
- 3M Advanced Ceramics Division
- American Sintering Technologies LLC
- CeramTec International GmbH
- CeramTech Advanced Materials Inc.
- CoorsTek Ceramics Inc.
- Dow Corning Silicon Technologies LLC
- Element Six (De Beers Group)
- Frontier Materials Sintering Ltd.
- Fusion Sintered Ceramics LLC
- Global Ceramics Inc.
- HighTemp Ceramics Group
- Innovate Silicon Ceramics
- Keramik Industries Ltd.
- Mitsubishi Materials Corporation
- Morgan Advanced Materials PLC
- Nippon Steel Ceramics
- Nova Ceramics and Composites Inc.
- PolySinter Tech Solutions
- Precision Ceramics Inc.
- PSI Sintering Technologies
- Saint-Gobain Ceramics & Plastics
- Sandvik Materials Technology AB
- Schunk Ceramics Corporation
- Showa Denko Advanced Ceramics
- Stellar Sintering Innovations
- Sumitomo Electric Ceramics
- TechSinter Materials Corp.
- Tokuyama Silicon Materials
- Vesuvius Sintering Solutions
- Wacker Chemie Silicon Division
Actionable Strategies for Strengthening Market Position and Profitability
Industry leaders must adopt a proactive approach to sustain growth and resilience. First, diversifying supply chains by partnering with domestic raw material processors and exploring alternative sources mitigates tariff risk and material cost volatility. Second, investing in process automation and energy efficiency through sintering optimization will reduce operating expenses and enhance throughput reliability.
Third, expanding capabilities in nanostructured pressureless sintering and hybrid manufacturing unlocks new material performance levels, supporting future advanced abrasives and structural innovations. Fourth, integrating digital monitoring systems and real-time data analytics optimizes temperature control and pressure parameters, ensuring consistent quality across batches.
Fifth, forging strategic collaborations with research institutions accelerates innovation in breakthrough materials and emerging processes, while sustainability developments-such as renewable energy integration and future cost innovations-align production practices with environmental stewardship.
Lastly, tailoring product offerings to end user priorities in aerospace, automotive, energy, and industrial equipment sectors will cultivate long-term partnerships, enhance value propositions, and drive competitive differentiation.
Explore AI-driven insights for the Sintering Silicon Carbide market with ResearchAI on our online platform, providing deeper, data-backed market analysis.
Ask ResearchAI anything
World's First Innovative Al for Market Research
Conclusion: Harnessing Innovation and Strategy for Sustainable Growth
In sum, the sintered silicon carbide market stands at a pivotal junction defined by technological innovation, regulatory shifts, and evolving end user demands. Advancements in spark plasma sintering, nanostructured pressureless processes and hybrid manufacturing are redefining material capabilities, while sustainability and energy efficiency initiatives support cost management and environmental goals.
Navigating the impact of United States tariffs requires strategic supply chain diversification and a focus on process automation to safeguard margins. Detailed segmentation insights reveal targeted opportunities across material grades, sintering processes, applications, end users, production technologies, market trends, and cost factors.
Regional analysis underscores divergent growth drivers in the Americas, Europe, Middle East & Africa, and Asia-Pacific, mandating localized strategies that resonate with regulatory landscapes and infrastructure realities. Meanwhile, a competitive landscape of established conglomerates and agile innovators highlights the importance of partnerships, R&D investments, and continuous process improvement.
By embracing these insights and recommendations, stakeholders can harness the full potential of sintered silicon carbide technology, deliver high-value solutions, and secure a sustainable competitive edge.
This section provides a structured overview of the report, outlining key chapters and topics covered for easy reference in our Sintering Silicon Carbide market comprehensive research report.
- Preface
- Research Methodology
- Executive Summary
- Market Overview
- Market Dynamics
- Market Insights
- Cumulative Impact of United States Tariffs 2025
- Sintering Silicon Carbide Market, by Material Grade
- Sintering Silicon Carbide Market, by Sintering Process
- Sintering Silicon Carbide Market, by Applications
- Sintering Silicon Carbide Market, by End User
- Sintering Silicon Carbide Market, by Production Technology
- Sintering Silicon Carbide Market, by Market Trends
- Sintering Silicon Carbide Market, by Cost Analysis
- Americas Sintering Silicon Carbide Market
- Asia-Pacific Sintering Silicon Carbide Market
- Europe, Middle East & Africa Sintering Silicon Carbide Market
- Competitive Landscape
- ResearchAI
- ResearchStatistics
- ResearchContacts
- ResearchArticles
- Appendix
- List of Figures [Total: 30]
- List of Tables [Total: 680 ]
Contact Ketan Rohom to Obtain the Full Market Research Report
To access a comprehensive analysis of sintered silicon carbide and gain actionable intelligence tailored to your business objectives, reach out directly to Ketan Rohom, Associate Director, Sales & Marketing. He can provide detailed guidance on how this market research report addresses your strategic needs and drives informed decision-making. Connect with Ketan Rohom today to elevate your understanding of this dynamic industry and unlock new growth opportunities.
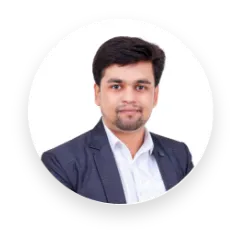
- When do I get the report?
- In what format does this report get delivered to me?
- How long has 360iResearch been around?
- What if I have a question about your reports?
- Can I share this report with my team?
- Can I use your research in my presentation?