The Smart Factory Market size was estimated at USD 147.13 billion in 2024 and expected to reach USD 159.52 billion in 2025, at a CAGR 8.67% to reach USD 242.42 billion by 2030.

Pioneering the Future of Manufacturing with Smart Factory Solutions
The manufacturing sector is undergoing a profound metamorphosis driven by digital innovation, evolving customer demands, and intensifying competitive pressures. This executive summary introduces the concept of the smart factory, a synthesis of advanced automation, real-time data analytics, and interconnected systems designed to optimize production processes, improve quality, and reduce downtime. As manufacturers seek to harness the benefits of Industry 4.0, they face complex decisions involving technology selection, integration approaches, and workforce adaptation. This report lays the groundwork by contextualizing the current market landscape, identifying the critical drivers and barriers, and framing the strategic implications for decision-makers. Through evidence-based analysis and expert commentary, the introduction establishes the imperative for adopting smart factory solutions as a means to achieve operational excellence, sustainability objectives, and enhanced competitiveness in an increasingly digital economy.
Unveiling the Transformative Shifts Reshaping Manufacturing
Manufacturing is being reshaped by a confluence of technological and operational shifts. The proliferation of artificial intelligence and machine learning has enabled predictive maintenance and quality control at an unprecedented scale, while digital twins provide virtual replicas of physical assets for simulation and optimization. Concurrently, robotics and autonomous systems are redefining the production floor, enhancing flexibility and throughput. Connectivity paradigms have evolved from isolated systems to pervasive IoT architectures, supporting real-time data exchange and edge computing capabilities. Cybersecurity has emerged as a strategic imperative, prompting investment in resilient network frameworks and secure device authentication. Sustainability considerations, including energy management and waste reduction, now influence every stage of the value chain. These transformative shifts are converging to create a new manufacturing paradigm where agility, transparency, and efficiency are paramount, setting the stage for the smart factory era.
Assessing the Cumulative Impact of United States Tariffs in 2025
The introduction of new tariffs by the United States in 2025 has introduced notable complexities into global supply chains and cost structures. Manufacturers reliant on imported robotics, sensors, and precision equipment have experienced elevated procurement expenses, prompting some to reevaluate sourcing strategies and explore nearshoring options. Tariff-related cost inflation has also accelerated interest in localizing component production and deepening collaboration with domestic suppliers. Meanwhile, service providers offering integration and maintenance solutions have adapted pricing models and contractual frameworks to reflect the evolving trade environment. Software vendors are contending with fluctuations in licensing fees tied to hardware costs, further influencing buyer purchasing cycles. In aggregate, these tariff measures have reinforced the strategic importance of supply chain resilience, risk diversification, and end-to-end visibility. Forward-looking organizations are leveraging advanced analytics to model tariff impacts, allocate buffer inventories, and refine procurement workflows to safeguard continuity and cost predictability.
Revealing Key Insights Across Core Market Segments
Analyzing market segmentation reveals distinct patterns of value creation and adoption. Within the component domain, equipment such as CNC machines, industrial PCs and controllers, industrial robots, and sensors represent the backbone of automation investments, while software offerings spanning analytics platforms, ERP, MES, and PLM orchestrate data-driven decision-making. Integration and deployment services facilitate rapid system commissioning, and ongoing maintenance and support ensure uptime. Technology-based segmentation underscores the dominance of big data analytics in harnessing operational insights, alongside the rising influence of cloud computing, digital twins, and immersive reality solutions. Connectivity preferences illustrate a balance between wired protocols like Ethernet and Fieldbus and wireless alternatives including Bluetooth, Wi-Fi, WirelessHART, and Zigbee. Enterprise size analysis shows that large organizations are pioneering large-scale smart factory rollouts, whereas SMEs prioritize turnkey solutions and managed services. Deployment choices hinge on organizational agility, with cloud-based platforms offering scalability and on-premises systems delivering tighter control. Application areas such as asset tracking, energy management, process automation, production planning, and quality inspection each unlock efficiency gains. End-use industries ranging from aerospace and automotive to healthcare and semiconductors are tailoring smart factory strategies to address sector-specific productivity and regulatory requirements.
This comprehensive research report categorizes the Smart Factory market into clearly defined segments, providing a detailed analysis of emerging trends and precise revenue forecasts to support strategic decision-making.
- Components
- Technology
- Connectivity
- Enterprise Size
- Deployment
- Application Area
- End Use
Decoding Regional Dynamics Driving Market Expansion
Regional dynamics play a pivotal role in shaping market momentum. In the Americas, investments in advanced manufacturing hubs and strong government support for automation initiatives are accelerating adoption of smart factory solutions. The region’s emphasis on reshoring critical production and enhancing supply chain resilience has bolstered demand for integrated hardware and software offerings. Europe, the Middle East and Africa are benefiting from ambitious sustainability mandates and digital innovation grants, spurring enterprises to modernize legacy assets and invest in eco-efficient operations. Collaborative ecosystems involving technology providers, research institutions, and OEMs are driving proof-of-concept deployments across manufacturing clusters. In Asia-Pacific, robust industrial modernization programs in countries such as China, Japan, and India are catalyzing large-scale implementations of robotics, AI-driven analytics, and cloud-enabled platforms. Rapid digital infrastructure expansion and favorable government incentives continue to underpin the region’s trajectory as a leading smart factory market.
This comprehensive research report examines key regions that drive the evolution of the Smart Factory market, offering deep insights into regional trends, growth factors, and industry developments that are influencing market performance.
- Americas
- Europe, Middle East & Africa
- Asia-Pacific
Profiling Leading Innovators and Market Movers
Leading technology providers and system integrators are defining the competitive landscape through strategic innovation and partnerships. Market frontrunners have diversified their portfolios by acquiring analytics startups and establishing dedicated centers of excellence for digital twin development. Others have formed alliances with cloud hyperscalers to deliver scalable IoT platforms and extend global footprint. Key players are also enhancing service offerings by embedding cybersecurity modules and predictive maintenance algorithms into core solutions. In parallel, specialized vendors are capitalizing on niche applications such as quality inspection and energy optimization, differentiating via deep domain expertise and industry-specific compliance standards. Cross-sector collaborations between industrial OEMs and enterprise software vendors are facilitating end-to-end automation frameworks. These competitive dynamics underscore the importance of continuous R&D investment, ecosystem integration, and customer-centric service models as the driving forces behind market leadership.
This comprehensive research report delivers an in-depth overview of the principal market players in the Smart Factory market, evaluating their market share, strategic initiatives, and competitive positioning to illuminate the factors shaping the competitive landscape.
- 3D Systems Corporation
- ABB Ltd.
- Andea sp. z o.o.
- Cisco Systems, Inc.
- Cognex Corporation
- Emerson Electric Co.
- Epicor Software Corporation
- Fanuc Corporation
- Fruitcore Robotics GmbH
- Fujitsu Limited
- General Electric Company
- Hitachi, Ltd.
- Honeywell International Inc.
- HP Development Company, L.P.
- International Business Machines Corporation
- KUKA AG by Midea Group
- Microsoft Corporation
- Mitsubishi Electric Corporation
- NVIDIA Corporation
- Oracle Corporation
- Robert Bosch GmbH
- Rockwell Automation, Inc.
- SAP SE
- Schneider Electric SE
- Siemens AG
- Stratasys Ltd.
- TE Connectivity Ltd.
- Telefonaktiebolaget LM Ericsson
- Texas Instruments Incorporated
- Ubisense Ltd.
- Yokogawa Electric Corporation
Actionable Strategies for Industry Leaders to Seize Opportunities
To capitalize on the smart factory wave, industry leaders should embark on a phased transformation roadmap. Initiating pilot projects in targeted production lines enables rapid validation of technology efficacy and return on investment. Concurrently, organizations must invest in workforce upskilling programs to cultivate data literacy and digital competencies across operations teams. Establishing an open architecture framework facilitates modular expansion and mitigates vendor lock-in risks. Strategic partnerships with cloud providers and analytics specialists can accelerate deployment timelines and unlock specialized capabilities. Emphasizing cybersecurity by design and adopting industrial reference architectures enhances system resilience. Sustainability targets should be integrated into performance metrics, leveraging real-time energy monitoring and waste reduction analytics. Finally, continuous benchmarking against industry standards and participation in collaborative innovation networks will ensure ongoing competitiveness and agility in response to evolving market demands.
Methodological Rigor Underpinning Our Market Analysis
Our analysis is grounded in a rigorous methodology that blends quantitative and qualitative research to ensure accuracy and relevance. Secondary data was sourced from industry publications, regulatory filings, and proprietary databases. Primary research involved in-depth interviews with senior executives, technology architects, and end-user representatives to validate market dynamics and adoption drivers. Data triangulation techniques were applied to reconcile discrepancies and enhance confidence in trend identification. Market segmentation was refined through statistical analysis and feedback loops with domain experts. Forecasting models incorporate scenario planning to account for variables such as tariff fluctuations and regional policy shifts. Finally, peer review by independent analysts ensured objectivity and adherence to best practices in market research.
Explore AI-driven insights for the Smart Factory market with ResearchAI on our online platform, providing deeper, data-backed market analysis.
Ask ResearchAI anything
World's First Innovative Al for Market Research
Concluding Perspectives on the Smart Factory Revolution
The smart factory landscape is at a pivotal juncture, with technological breakthroughs and shifting regulatory landscapes converging to redefine manufacturing excellence. Organizations that proactively embrace automation, data-centric process improvements, and resilient supply chain strategies will secure a competitive edge. From the emergence of immersive digital twins to the strategic implications of trade policy, the insights presented herein equip decision-makers with a multi-dimensional understanding of the market. As the pace of innovation accelerates, continuous evaluation of technology roadmaps, skillset investments, and strategic partnerships will be essential. This conclusion reaffirms the urgency of an agile, informed approach to smart factory adoption and underscores the transformative potential that lies at the intersection of industry expertise and cutting-edge digital capabilities.
This section provides a structured overview of the report, outlining key chapters and topics covered for easy reference in our Smart Factory market comprehensive research report.
- Preface
- Research Methodology
- Executive Summary
- Market Overview
- Market Dynamics
- Market Insights
- Cumulative Impact of United States Tariffs 2025
- Smart Factory Market, by Components
- Smart Factory Market, by Technology
- Smart Factory Market, by Connectivity
- Smart Factory Market, by Enterprise Size
- Smart Factory Market, by Deployment
- Smart Factory Market, by Application Area
- Smart Factory Market, by End Use
- Americas Smart Factory Market
- Europe, Middle East & Africa Smart Factory Market
- Asia-Pacific Smart Factory Market
- Competitive Landscape
- ResearchAI
- ResearchStatistics
- ResearchContacts
- ResearchArticles
- Appendix
- List of Figures [Total: 30]
- List of Tables [Total: 560 ]
Elevate Your Market Strategy with Expert Insights
Elevate your strategic outlook by securing the complete Smart Factory Market research report. Engage directly with Ketan Rohom, Associate Director, Sales & Marketing, to explore tailored insights that align with your organization’s digital transformation goals. This comprehensive dossier equips you with depth on emerging technologies, regional trajectories, and competitive landscapes, empowering you to make informed investment and partnership decisions. Reach out to arrange a personalized briefing and gain exclusive access to data-driven analyses, expert forecasts, and actionable recommendations designed to propel your smart factory initiatives to the forefront of industry innovation.
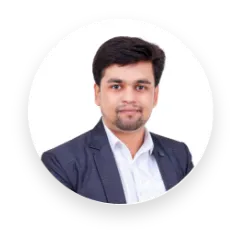
- How big is the Smart Factory Market?
- What is the Smart Factory Market growth?
- When do I get the report?
- In what format does this report get delivered to me?
- How long has 360iResearch been around?
- What if I have a question about your reports?
- Can I share this report with my team?
- Can I use your research in my presentation?