Introduction to Intelligent Ultrasonic Metal Welding: Advanced Techniques Shaping the Future of Precision and Efficiency in Manufacturing
The dawn of intelligent manufacturing has ushered in a new era for metal joining technologies, with smart ultrasonic welding machines leading the charge. By harnessing high-frequency vibrations to generate heat at metal interfaces, these systems deliver strong, precise bonds without the need for additional materials or high-temperature processes. This transformative approach aligns with the growing emphasis on lightweight assembly, miniaturization, and sustainability within sectors such as electronics, automotive, and consumer goods.
As industries grapple with ever-tighter tolerances and accelerated production cycles, ultrasonic welding machines equipped with advanced sensors and adaptive control algorithms are becoming indispensable. Real-time monitoring of weld quality and the ability to fine-tune process parameters on the fly ensure consistent outcomes and minimize downtime. Moreover, the integration of machine learning modules enables predictive maintenance, whereby potential failures are identified before they occur. Consequently, manufacturers experience reduced operational disruptions and lower total cost of ownership.
Furthermore, regulatory pressures and the shift toward electric vehicles have intensified the demand for reliable battery tab welding solutions. In response, ultrasonic welding platforms now offer specialized tooling and automated handling systems tailored to battery assembly. This progress not only supports the mass adoption of clean mobility but also facilitates compliance with stringent quality standards. In sum, intelligent ultrasonic metal welding machines are redefining precision joining, empowering manufacturers to meet evolving performance benchmarks and sustainable production objectives.
Emerging Technological and Industry Trends Catalyzing a Paradigm Shift in Ultrasonic Metal Welding Applications
In recent years, the ultrasonic welding landscape has undergone radical transformation, driven by advances in digital connectivity and materials science. High-performance piezoelectric transducers, once limited by cost and complexity, are now more accessible thanks to modular designs and scalable production. This evolution has enabled manufacturers to tailor welding systems to specific applications, whether joining dissimilar metals in medical devices or fusing fine aluminum foils in consumer electronics.
Moreover, the proliferation of Industry 4.0 frameworks has ushered in unprecedented levels of process transparency. Connected welding stations feed critical data streams into centralized analytics platforms, allowing engineers to identify inefficiencies and optimize throughput rates. Consequently, the trend toward smart factories has empowered stakeholders to pursue continuous improvement initiatives, unlocking new realms of productivity and product quality.
Another pivotal shift is the convergence of ultrasonic welding with advanced robotics. Collaborative robots equipped with ultrasonic end-of-arm tooling bridge the gap between human dexterity and automated precision. By integrating force-feedback sensors and vision-guided positioning, these systems can adapt in real time to subtle variations in part geometry, significantly reducing cycle times while maintaining rigorous acceptance criteria.
Transitioning from isolated use cases to fully integrated manufacturing cells, the ultrasonic welding industry is charting a course toward seamless interoperability. As equipment suppliers, controls engineers, and end users converge around open-architecture ecosystems, the stage is set for accelerated innovation and new business models centered on subscription-based maintenance and outcome-driven services.
Assessing the Compounded Effects of 2025 United States Tariff Measures on the Smart Ultrasonic Metal Welding Industry
The implementation of new United States tariffs in early 2025 has generated a ripple effect across the smart ultrasonic metal welding sector, compelling manufacturers and system integrators to re-evaluate supply chain strategies. With levies imposed on key components such as high-grade piezoelectric crystals and precision instrumentation sourced from international suppliers, production costs have risen modestly. As a result, price sensitivity among original equipment manufacturers has increased, leading to a renewed emphasis on regional sourcing and vendor diversification.
Consequently, some end users have accelerated investments in domestic manufacturing capabilities to mitigate exposure to cross-border trade risks. This strategic pivot has spurred growth in North American assembly hubs that specialize in precision sensor production and ultrasonic generator assembly. Simultaneously, original suppliers have sought to establish localized partnerships, licensing technology to regional assemblers in order to preserve market share and streamline logistics.
However, the tariffs have also incentivized innovation within the supply base. Component manufacturers are exploring alternative materials for welding horns and anvil assemblies that can deliver comparable performance at a lower import tariff bracket. Additionally, research into composite and polymer-infused toolings is gaining traction as an avenue to sidestep certain duty classifications. These adaptive measures underscore the sector’s resilience in the face of trade policy shifts.
Taken together, the cumulative impact of these tariffs extends beyond immediate cost implications. It has catalyzed a broader reevaluation of procurement practices, engendered strategic domestic partnerships, and seeded material-level innovation-all of which are reshaping the competitive dynamics of the global ultrasonic welding ecosystem.
Deconstructing Market Segmentation Dynamics to Uncover Distinct Applications and End-User Industry Requirements in Ultrasonic Welding
Analyzing market segmentation reveals critical insights into where demand for ultrasonic welding technology is most pronounced and where future investments will yield the highest returns. The battery tab welding application towers above other use cases, driven by the accelerating rollout of electric vehicles and portable electronics. Within this domain, assembly lines for consumer electronics batteries capitalize on high-volume, low-footprint welding stations, while EV battery modules demand specialized cells marrying high current-carrying tabs with robust mechanical integrity. Industrial battery manufacturing, meanwhile, leverages heavy-duty ultrasonic welders configured to accommodate larger cell formats and more stringent safety standards.
Shifting to end-user industries, the aerospace sector applies ultrasonic welding to join lightweight aluminum and copper alloys for avionics components, prioritizing weld repeatability under extreme operating conditions. The automotive industry’s pivot to lightweight construction and electrification continues to spur investments, particularly in battery pack assembly and high-voltage busbar fabrication. Consumer goods manufacturers adopt ultrasonic welding for hermetic sealing of precision sensors, while the electronics domain exploits the process for foil welding in capacitors and flexible printed circuits. In the medical field, the need for contamination-free, chemical-free joining methods makes ultrasonic welding indispensable for device housings and microfluidic components.
Automation level further distinguishes market needs: fully automatic systems dominate high-volume production, offering rapid cycle times and integrated quality inspection modules, whereas manual and semi-automatic configurations serve niche applications and prototyping facilities seeking cost-effective flexibility. Power rating preferences align with application scale-high-power welders for heavy-gauge metals, medium-power for standard sheet and foil, and low-power variants for delicate substrates. Additionally, machine type segmentation highlights bench-top solutions as the go-to choice for R&D labs and small workshops, while handheld units find favor in field service and maintenance operations. Finally, machine configuration trends reveal multi-stack arrangements optimized for simultaneous multi-point welding, contrasted with single-stack designs valued for their simplicity and ease of setup.
This comprehensive research report categorizes the Smart Ultrasonic Metal Welding Machine market into clearly defined segments, providing a detailed analysis of emerging trends and precise revenue forecasts to support strategic decision-making.
- Application
- End User Industry
- Automation Level
- Power Rating
- Machine Type
- Machine Configuration
Analyzing Regional Market Variations Across Americas, EMEA, and Asia-Pacific to Identify Core Growth Drivers in Ultrasonic Welding
Regional market variations shed light on distinct growth trajectories and highlight the nuanced interplay between industrial maturity and emerging investment priorities. In the Americas, North American manufacturers are doubling down on automation upgrades to support reshoring initiatives and meet stringent quality commitments in automotive and aerospace supply chains. Government incentives aimed at bolstering domestic advanced manufacturing infrastructure have further accelerated the deployment of ultrasonic welding stations, particularly in key automotive corridors across the United States and Mexico. At the same time, demand in South America is gathering momentum in consumer electronics assembly, with select hubs exploring trilateral logistics frameworks to streamline component movement.
Conversely, Europe, the Middle East, and Africa collectively exhibit a dual focus on precision applications and energy transition projects. Western European OEMs are early adopters of ultrasonic welding for hydrogen fuel cell stack assembly and next-generation battery modules, supported by collaborative R&D consortia. In the Middle East, burgeoning aerospace projects and diversified industrialization agendas have spurred interest in localized welding capabilities. North African electronics parks, benefiting from free trade agreements, are emerging as export bases for compact consumer devices.
Asia-Pacific remains the epicenter of ultrasonic welding adoption, boasting both mature manufacturing powerhouses in Japan and South Korea and rapidly expanding markets in China, India, and Southeast Asia. Here, the convergence of high-volume automotive battery production, consumer electronics fabrication, and medical device manufacturing has created unparalleled scale. Rather than simply serving as an offshoring destination, regional players are driving process innovations, from AI-enhanced quality analytics to novel horn materials tailored for local alloy compositions. This dynamic ecosystem underscores why Asia-Pacific continues to set the pace for global ultrasonic welding technology evolution.
This comprehensive research report examines key regions that drive the evolution of the Smart Ultrasonic Metal Welding Machine market, offering deep insights into regional trends, growth factors, and industry developments that are influencing market performance.
- Americas
- Europe, Middle East & Africa
- Asia-Pacific
Profiling Industry Leaders and Innovators Driving Technological Advancement and Competitive Differentiation in Ultrasonic Welding
Within a competitive landscape characterized by technological specialization and strategic partnerships, several key companies have emerged as defining forces. Leading equipment manufacturers have established themselves by advancing generator technologies that offer unprecedented energy efficiency and waveform control, enabling weld profiles previously thought unattainable. Simultaneously, sensor and transducer specialists are collaborating with system integrators to embed real-time acoustic emission monitoring, paving the way for closed-loop control architectures.
These innovators have also pursued strategic alliances with automation providers, resulting in turnkey cells that seamlessly marry welding technology with robotic handling and machine vision. Such end-to-end solutions appeal to high-volume sectors by reducing integration complexity and accelerating time to market. To further differentiate, many firms are leveraging digital twin simulations to validate process parameters in virtual environments before deploying on the factory floor, a practice that minimizes prototyping cycles and maximizes first-pass yield.
Concurrent to technology development, influential component suppliers are expanding their geographic footprint through joint ventures and licensing agreements in high-growth regions. This approach not only mitigates tariff-related pressures but also fosters localized expertise and service capabilities. Collectively, these concerted efforts underscore the importance of ecosystem orchestration, where cross-functional collaboration drives the rapid adoption of next-generation ultrasonic welding solutions.
This comprehensive research report delivers an in-depth overview of the principal market players in the Smart Ultrasonic Metal Welding Machine market, evaluating their market share, strategic initiatives, and competitive positioning to illuminate the factors shaping the competitive landscape.
- Herrmann Ultraschalltechnik GmbH & Co. KG
- Telsonic AG
- Weber Ultrasonics GmbH
- Amada Miyachi America, Inc.
- Dukane Corporation
- Branson Ultrasonics Corporation
- Sonotronic Nagel GmbH
- Rinco Ultrasonics AG
- SCHUNK Sonosystems GmbH
- Sonics & Materials, Inc.
Strategic Actionable Recommendations for Industry Leaders to Capitalize on Smart Ultrasonic Welding Innovations and Market Opportunities
To navigate the complexities of an evolving ultrasonic welding ecosystem, industry leaders should prioritize several strategic initiatives. First, cultivating partnerships with domestic component developers can mitigate exposure to international tariffs and shorten supply chains. By collaborating on research and development, original equipment manufacturers can co-create tailored materials and tooling designs that balance performance with cost efficiency.
Additionally, investing in modular automation platforms will enable more agile production environments. Leaders should seek to integrate ultrasonic welding modules into flexible manufacturing cells that support rapid changeovers between applications. Incorporating standardized communication protocols and open interfaces ensures interoperability and reduces customization overhead.
Furthermore, organizations must embrace data-centric process optimization. Deploying advanced analytics to interpret welding signatures and machine health metrics will facilitate predictive maintenance and continuous quality improvement. Establishing clear key performance indicators aligned with yield targets and uptime objectives encourages cross-functional accountability.
Lastly, cultivating a skilled workforce remains paramount. Workforce development programs that blend hands-on training with digital simulation tools will equip technicians and engineers to operate sophisticated smart welding systems effectively. By prioritizing talent cultivation alongside technological investment, companies can maximize the returns on their ultrasonic welding modernization initiatives.
Rigorous Multi-Pronged Research Methodology Employed to Ensure Comprehensive and Objective Analysis of Ultrasonic Welding Market Trends
The market analysis presented in this report is founded on a rigorous, multi-faceted research methodology designed to ensure the accuracy and relevance of insights. Primary data collection involved in-depth interviews with leading equipment manufacturers, component suppliers, and end users across key industries, providing firsthand perspectives on technology adoption, application challenges, and strategic imperatives.
Secondary research encompassed the review of peer-reviewed journals, industry white papers, and technical standards pertaining to ultrasonic welding processes, materials science advancements, and automation integration. Additionally, trade association publications and patent databases were examined to uncover emerging innovations and competitive dynamics. This comprehensive literature review grounded the analysis in both academic and commercial contexts.
Quantitative analysis of market segmentation and regional deployment trends leveraged proprietary datasets alongside validated public information sources. Emphasis was placed on cross-referencing multiple sources to triangulate findings and minimize bias. Where appropriate, case studies of representative deployment scenarios were incorporated to illustrate real-world performance outcomes and best practices.
Throughout the research process, rigorous data validation protocols were applied, including consistency checks, peer reviews by subject matter experts, and sensitivity analyses to assess the robustness of insights under varying market conditions. This methodological rigor underpins the report’s actionable intelligence and ensures that stakeholders can rely on the findings for strategic decision-making.
Explore AI-driven insights for the Smart Ultrasonic Metal Welding Machine market with ResearchAI on our online platform, providing deeper, data-backed market analysis.
Ask ResearchAI anything
World's First Innovative Al for Market Research
Concluding Insights Highlighting Key Findings and Strategic Imperatives for Stakeholders in the Ultrasonic Welding Sector
In summary, the smart ultrasonic metal welding market is experiencing robust evolution as a result of technological breakthroughs, shifting trade policies, and diversified application demands. Advanced ultrasonic systems are redefining precision joining across critical sectors, driving manufacturers to adopt fully integrated, data-driven solutions. Tariff-induced supply chain adjustments are catalyzing regional manufacturing enhancements and material innovation, reinforcing the industry’s adaptability.
Segmentation insights highlight the pronounced growth in battery tab welding applications, underscoring the importance of tailored system configurations across varying automation levels and power ratings. Regional analysis reveals that while Asia-Pacific continues to lead in both scale and innovation, the Americas and EMEA regions are rapidly enhancing their domestic capabilities to capitalize on reshoring and energy transition imperatives.
Key industry participants have distinguished themselves through targeted R&D, strategic partnerships, and digital twin implementations, collectively raising the bar for performance and integration ease. By pursuing the recommended strategic initiatives around supply chain localization, modular automation, data-centric optimization, and workforce development, stakeholders can secure competitive advantages and future-proof their operations.
Overall, the convergence of intelligent welding technology with broader manufacturing digitization trends promises sustained growth and new value creation opportunities for all participants in the ultrasonic welding ecosystem.
This section provides a structured overview of the report, outlining key chapters and topics covered for easy reference in our Smart Ultrasonic Metal Welding Machine market comprehensive research report.
- Preface
- Research Methodology
- Executive Summary
- Market Overview
- Market Dynamics
- Market Insights
- Cumulative Impact of United States Tariffs 2025
- Smart Ultrasonic Metal Welding Machine Market, by Application
- Smart Ultrasonic Metal Welding Machine Market, by End User Industry
- Smart Ultrasonic Metal Welding Machine Market, by Automation Level
- Smart Ultrasonic Metal Welding Machine Market, by Power Rating
- Smart Ultrasonic Metal Welding Machine Market, by Machine Type
- Smart Ultrasonic Metal Welding Machine Market, by Machine Configuration
- Americas Smart Ultrasonic Metal Welding Machine Market
- Europe, Middle East & Africa Smart Ultrasonic Metal Welding Machine Market
- Asia-Pacific Smart Ultrasonic Metal Welding Machine Market
- Competitive Landscape
- ResearchAI
- ResearchStatistics
- ResearchContacts
- ResearchArticles
- Appendix
- List of Figures [Total: 30]
- List of Tables [Total: 650 ]
Engage Directly with the Associate Director of Sales & Marketing for Personalized Market Research Insights and Report Acquisition
For tailored insights and an in-depth exploration of the smart ultrasonic metal welding machine market, reach out directly to our Associate Director of Sales & Marketing, Ketan Rohom. He will guide you through the extensive research findings, clarify any questions about market dynamics, and provide customized recommendations that align with your strategic objectives. By securing the full market research report, you gain exclusive access to proprietary analyses, detailed company profiles, and actionable intelligence designed to bolster your competitive positioning.
Engaging with Ketan ensures that you receive personalized support in interpreting the data and translating insights into practical strategies. Whether you are evaluating new technology investments or refining your market entry approach, this report equips you with the knowledge needed to make informed decisions. Don’t miss the opportunity to leverage expert perspectives and comprehensive market coverage. Contact Ketan Rohom today to secure your copy of the report and unlock the full potential of smart ultrasonic metal welding solutions.
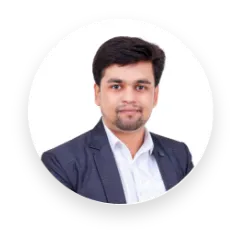
- When do I get the report?
- In what format does this report get delivered to me?
- How long has 360iResearch been around?
- What if I have a question about your reports?
- Can I share this report with my team?
- Can I use your research in my presentation?