The Solder Materials Market size was estimated at USD 4.57 billion in 2024 and expected to reach USD 4.79 billion in 2025, at a CAGR 4.75% to reach USD 6.05 billion by 2030.

Navigating a Dynamic Solder Materials Market
The solder materials market stands at a pivotal juncture, shaped by rapid technological advancements and evolving end-use demands. As manufacturers pursue higher precision and reliability, materials science has propelled the development of novel alloy compositions and flux systems. This executive summary distills the critical factors driving market momentum and frames the strategic considerations that industry leaders cannot afford to overlook. Through a careful synthesis of current trends and structural forces, readers will gain clarity on the forces reshaping supply chains, influencing product innovation, and redefining competitive dynamics.
In an era of heightened performance requirements, the solder materials sector is responding with solutions that emphasize miniaturization, thermal stability, and environmental compliance. The convergence of industrial sectors such as automotive electronics, medical devices, and aerospace applications underscores the importance of cross-sectoral insights. By examining both the macroeconomic backdrop and the granular technical breakthroughs, this analysis equips decision-makers with a robust understanding of where the market is heading and how organizations can position themselves for sustainable success.
Precision and Sustainability Redefine Industry Standards
Over the past decade, the solder materials landscape has experienced profound transformation driven by the intensifying push toward miniaturization and advanced electronics integration. Shrinking component sizes and tighter packaging constraints have elevated reflow soldering and laser techniques, enabling submillimeter interconnects that were previously unattainable. This shift has placed a premium on alloy systems and flux chemistries that can withstand higher thermal cycles while maintaining joint integrity. Concurrently, selective soldering solutions have evolved from manual setups to fully programmable platforms, delivering repeatable results and reduced defects at scale.
Sustainability has emerged as another cornerstone of this evolution, with no-clean and water-soluble flux types gaining traction as manufacturers adhere to stricter environmental regulations. Alloy innovation has paralleled these trends, as tin-silver-copper compositions like SAC305 have become industry mainstays for combining mechanical strength with lead-free compliance. As different processes-dip, wave, and selective soldering-integrate advanced automation, the market is witnessing a convergence of precision engineering, real-time quality monitoring, and digital traceability. This transformative synergy is setting new benchmarks for productivity and reliability across end-use sectors.
Tariff Shifts Reshape Global Supply Chains
The United States’ tariff adjustments scheduled for 2025 are poised to reshape global trade flows and cost structures within the solder materials market. By raising import duties on certain alloys and flux systems, domestic manufacturers might secure a short-term pricing advantage. However, these measures could inadvertently drive up the cost of components that rely on specialized raw materials from tariff-affected regions. Electronics, automotive, and aerospace supply chains may face higher procurement costs, prompting end users to seek alternative sourcing strategies or negotiate long-term contracts to hedge against volatility.
Moreover, elevated tariffs can accelerate regionalization as companies shift production closer to key markets to avoid import levies. This realignment offers opportunities for North American foundries and downstream assemblers to capture market share, yet it also demands investment in capacity expansion and process optimization. In response, industry stakeholders are reassessing their logistics networks, prioritizing supplier diversification and inventory management solutions. The net effect will be a more fragmented but resilient supply chain architecture, where agility and strategic partnerships determine competitive positioning.
Unpacking Multi-Dimensional Market Segments
Process differentiation lies at the heart of market segmentation, encompassing dip soldering, laser soldering, reflow soldering, selective soldering, and wave soldering. Within selective soldering, both automatic and programmable platforms are forging ahead, enabling manufacturers to adapt quickly to complex board layouts. Meanwhile, wave soldering continues to segment into dual wave and single wave systems, each catering to specific throughput and defect-rate requirements. These process choices influence material selection, throughput optimization, and capital expenditure profiles across manufacturing lines.
Alloy selection offers another layer of granularity, with tin-bismuth, tin-copper, tin-lead, tin-silver, and tin-silver-copper variants each fulfilling distinct performance criteria. Tin-silver-copper alloys like SAC305, SAC387, and SAC405 stand out for their balanced properties in high-reliability applications. The end-use spectrum further refines market dynamics, stretching from aerospace and defense-encompassing avionics, defense electronics, and satellite systems-to automotive segments that include ADAS, engine control units, infotainment systems, and sensors. The electronics arena, with LED lighting, PCB assembly, power electronics, and semiconductors, demands materials that deliver low voiding and consistent wetting.
Flux chemistry and product form add depth to segmentation, with no-clean, rosin-activated, rosin-mildly activated, water-soluble inorganic acid, and water-soluble organic acid formulations aligning to varied process and environmental mandates. Bars, paste, powder, preforms, and wire shapes accommodate distinct application methodologies. Paste classifications from Type 3 to Type 6 and wire gauges from 0.5 mm through 1.5 mm ensure that every assembly challenge, from fine-pitch components to high-volume wave lines, is addressed by a tailored materials portfolio.
This comprehensive research report categorizes the Solder Materials market into clearly defined segments, providing a detailed analysis of emerging trends and precise revenue forecasts to support strategic decision-making.
- Process
- Alloy Type
- End Use
- Flux Type
- Form
Regional Dynamics Fueling Market Growth
The Americas region continues to be characterized by robust demand for advanced solder solutions across aerospace, defense, and medical device manufacturing. North American assemblers are increasingly adopting lead-free alloys and automated selective soldering systems to meet stringent regulatory requirements and reduce defect rates. Latin American markets are gradually aligning with global standards, offering growth potential driven by automotive electronics and industrial machinery modernization.
Across Europe, the Middle East, and Africa, the market is driven by regulatory frameworks that favor environmentally friendly materials. RoHS-compliant alloys and no-clean flux systems dominate, while dual wave and programmable selective soldering platforms are gaining ground in high-precision sectors. Regional supply resilience is bolstered by a network of local distributors and specialist integrators, enabling rapid response to shifting demand patterns.
In Asia-Pacific, the largest electronics production hub, solder materials suppliers face intense competition and cost pressures. Manufacturers prioritize high-throughput reflow lines and powder-based formulations to support mobile devices and consumer electronics. Meanwhile, emerging markets like India and Southeast Asia are investing heavily in automotive electronics and industrial automation, creating new demand for tin-silver-copper alloys and high-reliability processes.
This comprehensive research report examines key regions that drive the evolution of the Solder Materials market, offering deep insights into regional trends, growth factors, and industry developments that are influencing market performance.
- Americas
- Europe, Middle East & Africa
- Asia-Pacific
Competitive Forces Driving Innovation
Leading global manufacturers continue to leverage scale and R&D capabilities to maintain a competitive edge in solder materials. These firms invest heavily in alloy innovation, digital process control, and sustainable flux technologies to differentiate their offerings. At the same time, mid-tier and specialized players are carving out niches by focusing on rapid customization, localized support, and agile supply models that address the unique needs of contract electronics manufacturers.
Innovative startups are also reshaping the competitive landscape by introducing next-generation materials such as nanoparticle-enhanced pastes and bio-derived flux alternatives. These entrants often collaborate with research institutions to accelerate product validation and market entry. Concurrently, strategic partnerships between materials developers and equipment OEMs are fostering integrated solutions, where solder alloys, flux chemistries, and deposition platforms are co-engineered for optimal performance. As consolidation continues in the supply chain, companies that align R&D with customer-centric service will capture the lion’s share of long-term growth.
This comprehensive research report delivers an in-depth overview of the principal market players in the Solder Materials market, evaluating their market share, strategic initiatives, and competitive positioning to illuminate the factors shaping the competitive landscape.
- Indium Corporation
- Nihon Superior Co., Ltd.
- Henkel AG & Co. KGaA
- Kester Incorporated
- Alpha Assembly Solutions, Inc.
- Senju Metal Industry Co., Ltd.
- JX Nippon Mining & Metals Corporation
- Hitachi Metals, Ltd.
- AIM Solder Interconnect Solutions, LLC
- Materion Corporation
Strategies to Secure Sustainable Competitive Advantage
Industry leaders must prioritize process automation and real-time quality analytics to stay ahead of emerging quality and throughput expectations. Investing in programmable selective soldering and laser rework systems will enable rapid adaptation to increasingly complex PCB layouts. Organizations should also establish cross-functional teams to accelerate alloy and flux co-development, ensuring materials are tailored precisely to end-use environments, from high-temperature power electronics to miniaturized medical implants.
Supply chain resilience must be reinforced through multi-sourcing strategies and strategic reserves of critical raw materials. Firms should explore near-shoring opportunities in the Americas and EMEA to mitigate tariff exposure and logistics disruptions. Moreover, digital traceability platforms can enhance visibility across the value chain, allowing proactive risk management and streamlined compliance reporting. By embedding sustainability metrics into procurement decisions-such as lifecycle carbon footprints and end-of-life recyclability-companies will not only meet regulatory demands but also unlock operational efficiencies.
Rigorous Methodology Underpinning Our Findings
This analysis is grounded in a multi-tiered research framework comprising both primary and secondary data sources. The secondary research phase included a comprehensive review of industry publications, technical white papers, regulatory filings, and patent databases to map technological trajectories and market drivers. During the primary research phase, we conducted in-depth interviews with senior executives, process engineers, and procurement specialists across key geographies, ensuring practical insights into adoption barriers and future requirements.
Quantitative analysis involved the integration of company financial disclosures, customs data, and trade associations’ export-import records to trace volume and value flows. A robust validation protocol included cross-referencing data points with expert opinions and triangulating findings through multiple independent sources. Segmentation assumptions were stress-tested against scenario analyses to confirm their relevance under varying market conditions. The resulting methodology provides confidence in the accuracy and objectivity of the insights presented, offering a reliable foundation for strategic decision-making.
Explore AI-driven insights for the Solder Materials market with ResearchAI on our online platform, providing deeper, data-backed market analysis.
Ask ResearchAI anything
World's First Innovative Al for Market Research
Charting a Course Through Market Complexity
The solder materials market is poised for sustained growth underpinned by accelerating electronics miniaturization, stringent environmental mandates, and geopolitical shifts in manufacturing footprints. Process innovation and alloy diversification will remain central to meeting the evolving demands of high-reliability sectors, including aerospace, automotive, and medical devices. Simultaneously, regional supply realignments-driven by tariff adjustments and near-shoring incentives-will create both challenges and opportunities for materials suppliers and end-users alike.
As the landscape evolves, success will hinge on the ability to integrate advanced materials with automated processing platforms while maintaining rigorous quality and sustainability standards. Organizations that foster collaborative R&D, invest in digital traceability, and build resilient sourcing networks will be best positioned to capitalize on emerging trends. The insights contained herein offer a strategic roadmap for navigating the complexities of this dynamic market and achieving long-term competitive advantage.
This section provides a structured overview of the report, outlining key chapters and topics covered for easy reference in our Solder Materials market comprehensive research report.
- Preface
- Research Methodology
- Executive Summary
- Market Overview
- Market Dynamics
- Market Insights
- Cumulative Impact of United States Tariffs 2025
- Solder Materials Market, by Process
- Solder Materials Market, by Alloy Type
- Solder Materials Market, by End Use
- Solder Materials Market, by Flux Type
- Solder Materials Market, by Form
- Americas Solder Materials Market
- Europe, Middle East & Africa Solder Materials Market
- Asia-Pacific Solder Materials Market
- Competitive Landscape
- ResearchAI
- ResearchStatistics
- ResearchContacts
- ResearchArticles
- Appendix
- List of Figures [Total: 26]
- List of Tables [Total: 784 ]
Take the Next Step with Expert Guidance
If you are ready to harness the full potential of the solder materials market and secure a competitive advantage, reach out to Ketan Rohom, Associate Director, Sales & Marketing. He can guide you through the insights and tailor solutions to your strategic needs. Connect today to discuss how our comprehensive report can inform your investment decisions, optimize your supply chain, and drive growth. Don’t miss the opportunity to turn data into actionable strategy-partner with Ketan Rohom to elevate your market intelligence.
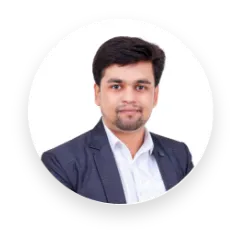
- How big is the Solder Materials Market?
- What is the Solder Materials Market growth?
- When do I get the report?
- In what format does this report get delivered to me?
- How long has 360iResearch been around?
- What if I have a question about your reports?
- Can I share this report with my team?
- Can I use your research in my presentation?