Solder Innovations Driving the New Energy Vehicle Revolution
The evolution of new energy vehicles hinges on the seamless integration of advanced materials, with solder alloys playing a foundational role in ensuring electrical reliability, thermal management, and long-term durability. As battery systems and power electronics become increasingly sophisticated, the demand for solder solutions that balance conductivity, mechanical strength, and environmental compliance has surged. This introduction outlines the critical context for understanding how emerging solder technologies underpin the performance and safety benchmarks of modern electric drivetrains.
As we embark on this examination, we will trace the transformative shifts in material science that are redefining the solder landscape. We will assess the cumulative impact of forthcoming United States tariffs on supply chains and cost structures. By delving into key segmentation insights-ranging from alloy compositions to application niches, form factors, production processes, and end-use channels-we will reveal nuanced pockets of opportunity and risk. Complementing these insights, regional analyses will highlight geographic dynamics, while competitive profiling dissects the strategies of leading suppliers. Finally, we will offer actionable recommendations and a transparent research methodology, closing with a compelling invitation to secure the full market research report.
Shifting Foundations: Material Science Transformations
The last decade has witnessed a seismic shift in how solder materials are developed and deployed across electric vehicles. Traditional tin-lead formulations have given way to a new generation of lead-free alloys engineered for higher melting points, enhanced fatigue resistance, and superior thermal conductivity. Coupled with stricter environmental regulations and industry standards, this transition has fueled innovation in alloy design, prompting chemists to explore combinations that optimize electrical performance while minimizing expensive elements such as silver.
Simultaneously, the miniaturization of power electronics and the demand for increased power density have placed unprecedented thermal and mechanical stresses on solder joints. Manufacturers have responded by fine-tuning metallurgical compositions, experimenting with tin-bismuth blends for low-temperature assembly and tin-zinc mixes for cost-effective yet resilient connectivity. Flux chemistries have also evolved, offering no-clean, rosin-based, and water-soluble options that align with various assembly environments and post-process cleaning requirements. These transformative material and process innovations are reshaping supplier portfolios and redefining performance benchmarks across battery management systems, DC-DC converters, inverters, and onboard chargers.
Assessing the 2025 United States Tariff Ripple Effects
The United States’ announcement of new tariffs set to take effect in 2025 has introduced an added layer of strategic complexity for solder material suppliers and automotive OEMs alike. Tariffs on key alloy constituents, particularly silver and specialty intermetallic compounds, threaten to elevate raw material costs and compress margins. In anticipation, procurement teams are reassessing supplier relationships, diversifying sourcing geographies, and exploring alloy formulations that reduce reliance on tariff-exposed components.
Moreover, the specter of trade policy volatility has spurred investments in nearshoring and alternative supply hubs. Automotive manufacturers are conducting sensitivity analyses to determine how cost increases will ripple through total cost of ownership metrics. In parallel, R&D teams are accelerating work on low-silver and bismuth-enhanced alloys that maintain performance while mitigating tariff exposure. As a result, the 2025 tariff framework is not merely a cost pressure; it is a catalyst for supply chain resilience and alloy innovation.
Decoding Market Segments to Unveil Growth Opportunities
A granular view of solder materials reveals distinct segments shaping demand and technology adoption. When considered by alloy type, tin-silver-copper blends such as SAC305, SAC387, and SAC405 lead high-temperature applications, while tin-bismuth grades in 42/58 and 57/43 ratios address low-temperature assembly needs. Cost-sensitive designs often favor tin-copper variants SC0307 and SC1008, whereas tin-zinc alloys like SnZn10 and SnZn8 strike a balance between affordability and mechanical resilience.
Turning to application, the market spans critical vehicle subsystems: sophisticated battery management systems require alloys with fine-pitch reliability; DC-DC converters call for joints that withstand rapid thermal cycling; inverters demand thermal conductivity at elevated currents; and onboard chargers depend on consistent electrical connectivity under varied environmental conditions.
Form factor influences handling and assembly speed. Solid bars serve as bulk input for traditional soldering, while solder paste supports surface-mount reflow processes. Preforms enable precise volume control, and solder wire remains a staple for manual operations. Flux selection-ranging through no-clean, rosin-based, and water-soluble formulations-further shapes process efficiency and post-assembly cleanliness.
Process distinctions matter as well. Manual soldering offers flexibility for prototyping and aftermarket repair, even as wave and reflow soldering technologies drive high-throughput OEM production. Finally, end-use segmentation divides the landscape between OEM volume assembly lines with strict quality metrics and aftermarket channels valuing serviceability and warranty support. Together, these segmentation lenses elucidate where R&D, production, and marketing resources should be concentrated to capture growth and maintain resilience.
This comprehensive research report categorizes the Solder Materials for New Energy Vehicles market into clearly defined segments, providing a detailed analysis of emerging trends and precise revenue forecasts to support strategic decision-making.
- Alloy Type
- Application
- Form Factor
- Process
- End Use
Regional Dynamics Shaping Solder Material Adoption
Regional demand for solder materials in new energy vehicles exhibits pronounced variation driven by manufacturing capacity, regulatory frameworks, and infrastructure development. In the Americas, advanced automotive research centers and pilot production lines in North America prioritize alloys that satisfy both high reliability and compliance with stringent environmental standards. Latin American markets, though smaller in scale, demonstrate growing interest in aftermarket solutions that support an expanding EV fleet.
The Europe, Middle East & Africa region combines Europe’s rigorous REACH and RoHS directives with a rapidly rising appetite for electrification across the Middle East. North African and Sub-Saharan markets remain nascent, presenting strategic entry points for suppliers that can tailor flux and alloy compositions to cost-sensitive applications.
Asia-Pacific remains the epicenter of battery and power electronics manufacturing. Northeast Asian powertrain producers drive demand for ultra-high-purity tin-silver-copper alloys, while emerging Southeast Asian assembly plants seek flexible processes that integrate no-clean and water-soluble flux technologies. Across this diverse landscape, local content mandates and government incentives continue to shape sourcing strategies and technology adoption.
This comprehensive research report examines key regions that drive the evolution of the Solder Materials for New Energy Vehicles market, offering deep insights into regional trends, growth factors, and industry developments that are influencing market performance.
- Americas
- Europe, Middle East & Africa
- Asia-Pacific
Competitive Landscape: Leading Companies and Their Strategies
The competitive landscape for solder materials in new energy vehicles is defined by a handful of specialized suppliers distinguished by their metallurgical expertise, global footprint, and collaboration with OEMs. Leading chemical producers have invested heavily in high-purity alloy production lines, ensuring consistent batch quality and tight composition tolerances. At the same time, niche players have carved out expertise in low-temperature bismuth formulations and zinc-enhanced solder, challenging incumbents with cost-effective alternatives.
Many top suppliers have forged long-term partnerships with major vehicle manufacturers, co-developing alloys that align with proprietary power electronics architectures. Others have augmented their portfolios with complementary flux chemistries and solder paste formulations, offering integrated solutions that improve process yields and reduce defect rates. Consolidation through mergers and strategic investments has further intensified competition, as companies seek scale and enhanced R&D capabilities to meet evolving performance and sustainability criteria.
This comprehensive research report delivers an in-depth overview of the principal market players in the Solder Materials for New Energy Vehicles market, evaluating their market share, strategic initiatives, and competitive positioning to illuminate the factors shaping the competitive landscape.
- Heraeus GmbH
- Indium Corporation
- Koki Holdings Co., Ltd
- Nihon Superior Co., Ltd
- Element Solutions Inc.
- AIM Solder Ltd.
- Alpha Assembly Solutions LLC
- Stannol GmbH
- Balver Zinn GmbH & Co. KG
- JX Nippon Mining & Metals Co., Ltd
Strategic Imperatives for Industry Leaders to Capitalize
Industry leaders must adopt a multifaceted approach to capitalize on burgeoning opportunities in the new energy vehicle sector. First, R&D teams should prioritize low-silver and bismuth-enhanced alloys that address cost pressures from regulatory tariffs while maintaining thermal and mechanical benchmarks. Concurrently, investments in advanced flux chemistries can streamline assembly throughput and support RoHS-compliant cleaning processes.
Supply chain diversification is equally critical. Establishing regional production hubs not only mitigates tariff risks but also reduces lead times and transportation costs. Collaboration with OEMs on joint qualification programs can accelerate time to market for novel alloys, while digital traceability systems enhance quality control and warranty management. Leaders should also explore circular economy initiatives, partnering with end users to facilitate solder recovery and recycling efforts.
Finally, forging alliances across the value chain-from chemical suppliers to equipment manufacturers and end customers-creates a robust ecosystem capable of responding swiftly to market shifts. By integrating material innovation with process intelligence and supply chain agility, leading companies can reinforce their competitive advantage and drive long-term growth.
Rigorous Research Framework Underpinning Insights
The insights presented in this report derive from a rigorous, multi-phase research framework. Initially, secondary research gathered data from industry publications, technical white papers, regulatory filings, and corporate disclosures to map the competitive and technological landscape. This was complemented by primary interviews with metallurgists, quality engineers, procurement managers, and senior executives at vehicle OEMs and tier-one suppliers to validate emerging trends and quantify strategic priorities.
Data triangulation ensured that alloy performance claims, cost dynamics, and supply chain structures were cross-verified through multiple sources. Competitive profiling employed a relative scoring methodology to assess R&D capabilities, production capacity, and partnership networks. Regional analyses leveraged trade statistics, government incentive programs, and local content regulations to forecast adoption patterns.
To maintain objectivity, findings were peer-reviewed by external industry experts and benchmarked against case studies of successful material integrations in leading electric vehicle models. The result is a high-fidelity portrayal of the solder materials market, grounded in both qualitative insights and quantitative evidence.
Explore AI-driven insights for the Solder Materials for New Energy Vehicles market with ResearchAI on our online platform, providing deeper, data-backed market analysis.
Ask ResearchAI anything
World's First Innovative Al for Market Research
Conclusion: Consolidating Insights for Strategic Advantage
Throughout this analysis, the critical role of solder materials in enabling the performance, safety, and reliability of new energy vehicles has been made abundantly clear. From alloy innovations that balance cost with conductivity to flux chemistries tailored for diverse assembly processes, each dimension of the market reveals strategic levers for competitive advantage.
The interplay of geopolitical dynamics, such as the 2025 United States tariffs, underscores the urgency of supply chain agility and alloy reformulation. Segmentation by alloy type, application, form factor, process, and end use offers a roadmap for targeting high-value segments, while regional insights highlight where regulatory frameworks and manufacturing capacity converge to shape adoption curves. Competitive profiling and actionable recommendations provide a strategic blueprint for stakeholders seeking to lead in this rapidly evolving industry.
In closing, the solder materials market for new energy vehicles represents a dynamic nexus of material science, process engineering, and global supply chain strategy. Organizations that harness these insights and execute with precision will be best positioned to thrive as electrification accelerates worldwide.
This section provides a structured overview of the report, outlining key chapters and topics covered for easy reference in our Solder Materials for New Energy Vehicles market comprehensive research report.
- Preface
- Research Methodology
- Executive Summary
- Market Overview
- Market Dynamics
- Market Insights
- Cumulative Impact of United States Tariffs 2025
- Solder Materials for New Energy Vehicles Market, by Alloy Type
- Solder Materials for New Energy Vehicles Market, by Application
- Solder Materials for New Energy Vehicles Market, by Form Factor
- Solder Materials for New Energy Vehicles Market, by Process
- Solder Materials for New Energy Vehicles Market, by End Use
- Americas Solder Materials for New Energy Vehicles Market
- Europe, Middle East & Africa Solder Materials for New Energy Vehicles Market
- Asia-Pacific Solder Materials for New Energy Vehicles Market
- Competitive Landscape
- ResearchAI
- ResearchStatistics
- ResearchContacts
- ResearchArticles
- Appendix
- List of Figures [Total: 26]
- List of Tables [Total: 461 ]
Secure Your Access to This Comprehensive Market Evaluation
To explore the full depth of solder materials strategies, innovations, and market drivers shaping the new energy vehicle sector, reach out to Ketan Rohom (Associate Director, Sales & Marketing at 360iResearch). Gain immediate access to exclusive data, advanced analytics, and strategic guidance designed to support critical decision making. Secure your copy of the comprehensive market research report today and position your organization at the forefront of material science excellence.
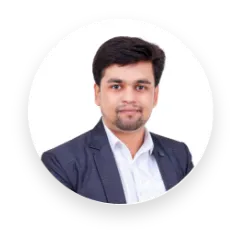
- When do I get the report?
- In what format does this report get delivered to me?
- How long has 360iResearch been around?
- What if I have a question about your reports?
- Can I share this report with my team?
- Can I use your research in my presentation?