Introduction
The solder and metal-based thermal interface material sector serves as a critical enabler for high-performance electronic systems, bridging the thermal gap between heat-generating components and heat-dissipating surfaces. As device power densities rise in aerospace, automotive, industrial, and consumer markets, the demand for robust thermal pathways continues to accelerate. Engineers and procurement teams alike face mounting pressure to identify materials that not only deliver low thermal resistance and superior conductivity but also withstand harsh operating conditions over extended service lives.
In the wake of miniaturization trends and electrification across industries, solder and metal-based compounds have evolved beyond simple filler materials to become engineered solutions tailored to specific applications. From tin silver alloys optimized for high-flux environments to bismuth-based solders designed for low-temperature processes, each formulation addresses a unique intersection of performance requirements and manufacturing constraints. This introduction sets the stage for an in-depth exploration of market dynamics, regulatory influences, segmentation strategies, regional trends, competitive positioning, and actionable guidance for leaders who seek to maintain a competitive edge in this rapidly shifting landscape.
Transformative Shifts in the Landscape
The landscape of solder and metal-based thermal interface materials is undergoing transformative shifts driven by several converging factors. First, advancements in semiconductor packaging, such as three-dimensional stacking and heterogeneous integration, demand materials that can accommodate tighter interconnect pitches while sustaining high thermal throughput. Simultaneously, the push toward electrification in automotive and industrial applications has elevated thermal management from a supporting discipline to a strategic priority, prompting OEMs to seek solutions with prolonged reliability under cyclical and high-temperature conditions.
Moreover, environmental and regulatory pressures have accelerated the transition to lead-free solders and compliance with international standards, reshaping supply chains and driving innovation in alloy development. Nanocomposite solders reinforced with carbon nanotubes and hybrid materials that blend metal matrices with phase-change elements illustrate the industry’s response to performance and sustainability mandates. Alongside material innovation, process integration techniques such as flip chip assembly, wire bonding, and low-temperature reflow methods are redefining manufacturing workflows, requiring thermal interface developers to collaborate more closely with equipment suppliers and end users to ensure seamless adoption.
Collectively, these shifts underscore a market in flux, where product performance, regulatory alignment, and process compatibility converge to dictate competitive advantage. The following sections unpack the impact of recent policy changes, segmentation insights, regional dynamics, and key players shaping the future of this vital materials category.
Cumulative Impact of United States Tariffs 2025
In 2025, new tariff measures imposed by the United States on a range of imported metals and solder compounds have introduced substantial cost pressures across the thermal interface material supply chain. Components sourced from traditional manufacturing hubs have become more expensive, leading many suppliers to reevaluate their vendor portfolios and consider nearshoring or reshoring strategies to mitigate tariff-related surcharges. As a result, inventories of lead-free solders and specialized alloys have realigned toward domestic production, while buyers negotiate longer lead times and differentiated pricing models to secure critical raw materials.
These tariffs have also prompted a reexamination of material compositions. Indium-based alloys and bismuth-based solders, which may have previously been imported at lower cost, are now scrutinized for their total landed expense, spurring interest in tin copper alternatives and hybrid composite formulations that bypass restricted tariff classifications. End users in automotive electronics and high-power applications are balancing these shifts against performance imperatives, often absorbing incremental costs to maintain system reliability.
Ultimately, the cumulative impact of the 2025 tariffs extends beyond immediate price increases. It has catalyzed strategic partnerships between material suppliers and domestic smelters, encouraged investments in alloy recycling, and accelerated the development of alternative chemistries that sidestep tariff burdens. Stakeholders who anticipate these changes and adapt their sourcing strategies proactively will navigate the evolving trade environment with greater resilience.
Key Segmentation Insights
Analysis of market segmentation reveals distinct growth vectors across material composition, end user industry, performance characteristics, process integration, application area, quality standard, market availability, and product innovation. Within material composition, bismuth based solders and indium based alloys cater to low-temperature and high-flux requirements, while lead containing solders remain in legacy applications. Lead free solders dominate modern device assembly, with tin copper alloys serving cost-sensitive segments and tin silver alloys-especially high flux variants-addressing extreme thermal conductivity demands.
From an end user perspective, aerospace and defense systems rely on proven reliability metrics, whereas automotive electronics have bifurcated into electric vehicle power modules and infotainment subsystems. Consumer electronics branch into smart devices and wearable technology, each demanding form factor flexibility. Industrial electronics focus on automation controls and precision sensors, and medical devices prioritize biocompatibility and sterilization resilience.
Performance characteristics further differentiate offerings: extended service life materials excel under cyclical thermal stress, high temperature endurance formulations withstand sustained heat, high thermal conductivity solders facilitate rapid heat transfer, and low thermal resistance interfaces minimize junction temperatures. Process integration modalities shape selection, too-flip chip assembly requires ultra-thin interconnects, surface mount technology offers both lead free reflow and low temperature reflow pathways, and wire bonding demands compatibility with ultra-fine pitch leads.
Application areas span battery systems cooling in electric vehicles, high power electronics thermal management in data centers, laser diode cooling for optical communication, and LED thermal control in lighting. Compliance with ISO certification, RoHS directives, and UL recognition ensures global acceptance. Market availability differentiates custom formulations from off the shelf options and prototype materials, while product innovation is typified by hybrid materials, nanocomposite solders-particularly those reinforced with carbon nanotubes-and intelligent smart materials that self-adjust thermal properties under varying load conditions.
This comprehensive research report categorizes the Solder & Metal-based Thermal Interface Material market into clearly defined segments, providing a detailed analysis of emerging trends and precise revenue forecasts to support strategic decision-making.
- Material Composition
- End User Industries
- Performance Characteristics
- Process Integration
- Application Areas
- Quality Standards
- Market Availability
- Product Innovation
Key Regional Insights
Regional analysis highlights divergent drivers and adoption rates in the Americas, Europe Middle East & Africa, and Asia-Pacific markets. In the Americas, robust growth in electric vehicle production and data center expansion fuels demand for advanced thermal interface solutions optimized for battery cooling and high power density modules. Supply chain resilience has become a strategic imperative, with local alloy production and recycling initiatives gaining momentum.
Within Europe Middle East & Africa, strict environmental regulations and aggressive decarbonization targets accelerate the transition to lead-free formulations and favor materials compliant with RoHS and ISO standards. The region’s aerospace and defense sectors continue to invest in reliability-focused solders, while emerging renewable energy applications boost demand for high-temperature endurance compounds.
Asia-Pacific remains a powerhouse for consumer electronics and industrial automation, with high volume manufacturing of surface mount technology assemblies and flip chip packaging driving significant uptake of both off the shelf and custom materials. Government incentives for semiconductor fabrication are expanding capacity, elevating requirements for low thermal resistance interfaces that support next-generation chip architectures.
Taken together, each region presents unique regulatory, cost, and performance imperatives. Suppliers who tailor material portfolios and support services to regional priorities will capture the greatest share of emerging opportunities.
This comprehensive research report examines key regions that drive the evolution of the Solder & Metal-based Thermal Interface Material market, offering deep insights into regional trends, growth factors, and industry developments that are influencing market performance.
- Americas
- Asia-Pacific
- Europe, Middle East & Africa
Key Companies Insights
The competitive landscape for solder and metal-based thermal interface materials is characterized by a diverse array of specialized suppliers. Alpha Solder Technologies, Inc. and Apex Soldering Technologies Ltd. lead in advanced alloy R&D, while Beta Thermal Materials LLC and Chi Advanced Thermal LLC have built reputations around reliability testing and custom formulation services. Crest Thermal Management Corp and Delta Thermal Interface Inc. focus on automotive and aerospace segments, respectively, and Epsilon Thermal Solutions LLC emphasizes modular product lines that streamline integration for electronics manufacturers.
Eta Advanced Materials Corporation and Gamma Solder Solutions Inc. differentiate through patented nanocomposite and hybrid technologies. Iota Solder & Interface Technologies Co. and Kappa Thermal Materials Inc. leverage extensive distribution networks to serve global markets, while Lambda Solder and Thermal Company LLC and Mu Metal Interfaces Corp. target high-temperature endurance and specialized military specifications. Nu Heat Transfer Technologies LLC and Omega Solder & Thermal Solutions Inc. bring scale to high-volume consumer electronics, and Omicron Materials and Soldering Ltd. excels in rapid prototyping and small-batch innovation.
Phi Soldering Tech Solutions Corp and Pi Solder and Thermal Solutions Inc. showcase agility in responding to tariff-driven supply disruptions. Pinnacle Solder Systems Inc. and Psi Metal-Based Thermal Corp. emphasize compliance with UL and RoHS standards, whereas Rho Thermal Materials Ltd and Sigma Solder Technologies Corp. invest heavily in process integration partnerships. Summit Thermal Technologies LLC, Tau Thermal Management Systems LLC, and Theta Thermal Dynamics Ltd. expand into turnkey assembly services, while Upsilon Thermal Interfaces Inc., Vertex Thermal Interface Materials Corp, and Xi Thermal Interfaces Inc. prioritize digital ordering platforms. Finally, Zenith Solder & Interface Solutions Inc. and Zeta Metal Soldering Systems Inc. maintain broad portfolios spanning custom, off the shelf, and prototype offerings, anchoring the market’s competitive intensity.
This comprehensive research report delivers an in-depth overview of the principal market players in the Solder & Metal-based Thermal Interface Material market, evaluating their market share, strategic initiatives, and competitive positioning to illuminate the factors shaping the competitive landscape.
- Alpha Solder Technologies, Inc.
- Apex Soldering Technologies Ltd
- Beta Thermal Materials LLC
- Chi Advanced Thermal LLC
- Crest Thermal Management Corp
- Delta Thermal Interface Inc
- Epsilon Thermal Solutions LLC
- Eta Advanced Materials Corporation
- Gamma Solder Solutions Inc
- Iota Solder & Interface Technologies Co.
- Kappa Thermal Materials Inc.
- Lambda Solder and Thermal Company LLC
- Mu Metal Interfaces Corp
- Nu Heat Transfer Technologies LLC
- Omega Solder & Thermal Solutions Inc
- Omicron Materials and Soldering Ltd
- Phi Soldering Tech Solutions Corp
- Pi Solder and Thermal Solutions Inc
- Pinnacle Solder Systems Inc
- Psi Metal-Based Thermal Corp
- Rho Thermal Materials Ltd
- Sigma Solder Technologies Corp
- Summit Thermal Technologies LLC
- Tau Thermal Management Systems LLC
- Theta Thermal Dynamics Ltd
- Upsilon Thermal Interfaces Inc.
- Vertex Thermal Interface Materials Corp
- Xi Thermal Interfaces Inc
- Zenith Solder & Interface Solutions Inc
- Zeta Metal Soldering Systems Inc
Actionable Recommendations for Industry Leaders
To navigate the evolving thermal interface market successfully, industry leaders should prioritize a set of targeted actions. First, accelerate investment in next-generation material innovation by allocating resources to develop hybrid, nanocomposite, and smart materials that address performance demands for emerging applications. Second, diversify supply chains by cultivating relationships with domestic and regional alloy suppliers to mitigate tariff exposure and ensure uninterrupted material flows.
Third, establish strategic partnerships with semiconductor foundries, assembly equipment providers, and end users to co-develop process-integrated solutions that streamline adoption and reduce time to market. Fourth, engage proactively with regulatory bodies and standards organizations to anticipate compliance shifts and secure early approval for new formulations, particularly in regions with stringent environmental mandates. Fifth, tailor product portfolios and customer support infrastructure to regional growth vectors, aligning technical training and logistics networks with the unique priorities of the Americas, Europe Middle East & Africa, and Asia-Pacific markets.
By executing these recommendations, leaders can enhance resilience, accelerate innovation, and capture market share in a sector defined by rapid technological change and complex trade dynamics.
Explore AI-driven insights for the Solder & Metal-based Thermal Interface Material market with ResearchAI on our online platform, providing deeper, data-backed market analysis.
Ask ResearchAI anything
World's First Innovative Al for Market Research
Conclusion
The solder and metal-based thermal interface material market stands at a crossroads defined by technological innovation, regulatory evolution, and shifting trade policies. As device architectures become more complex and power densities continue to climb, the importance of selecting the right thermal interface solution has never been greater. This executive summary has explored the market’s transformative shifts, the impact of 2025 tariffs, granular segmentation insights, regional dynamics, and the competitive landscape populated by more than thirty specialized suppliers.
Moving forward, organizations that embrace material diversification, process integration collaboration, and supply chain resilience will be best positioned to address emerging challenges. The collective momentum toward electrification, high-performance computing, and miniaturization underscores the need for dynamic, fit-for-purpose thermal interface materials. By leveraging the insights and recommendations outlined here, decision-makers can forge a strategic path that aligns innovation, compliance, and cost efficiency to drive sustainable business growth.
This section provides a structured overview of the report, outlining key chapters and topics covered for easy reference in our Solder & Metal-based Thermal Interface Material market comprehensive research report.
- Preface
- Research Methodology
- Executive Summary
- Market Overview
- Market Dynamics
- Market Insights
- Cumulative Impact of United States Tariffs 2025
- Solder & Metal-based Thermal Interface Material Market, by Material Composition
- Solder & Metal-based Thermal Interface Material Market, by End User Industries
- Solder & Metal-based Thermal Interface Material Market, by Performance Characteristics
- Solder & Metal-based Thermal Interface Material Market, by Process Integration
- Solder & Metal-based Thermal Interface Material Market, by Application Areas
- Solder & Metal-based Thermal Interface Material Market, by Quality Standards
- Solder & Metal-based Thermal Interface Material Market, by Market Availability
- Solder & Metal-based Thermal Interface Material Market, by Product Innovation
- Americas Solder & Metal-based Thermal Interface Material Market
- Asia-Pacific Solder & Metal-based Thermal Interface Material Market
- Europe, Middle East & Africa Solder & Metal-based Thermal Interface Material Market
- Competitive Landscape
- ResearchAI
- ResearchStatistics
- ResearchContacts
- ResearchArticles
- Appendix
- List of Figures [Total: 32]
- List of Tables [Total: 640 ]
Call-To-Action
For a comprehensive view of market trends, detailed segmentation analysis, and in-depth competitive intelligence, connect with Ketan Rohom, Associate Director of Sales & Marketing. Secure your copy of the full report today to inform strategic decisions and gain a competitive advantage in the thermal interface materials market.
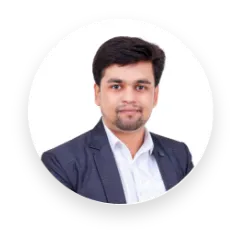
- When do I get the report?
- In what format does this report get delivered to me?
- How long has 360iResearch been around?
- What if I have a question about your reports?
- Can I share this report with my team?
- Can I use your research in my presentation?