Introduction: The Evolving Role of Powder Feeders in Spray Systems
In the rapidly advancing field of surface engineering, powder feeders serve as the critical interface between bulk material handling and precision coating application. Over recent years, the technology underpinning these feeders has matured significantly, enabling manufacturers to achieve tighter tolerances, higher throughput, and better repeatability. As industries seek coatings that deliver enhanced corrosion resistance, wear protection, and aesthetic finishes, the feeder’s ability to maintain consistent powder flow under challenging operating conditions has become paramount.
The increasing complexity of powder chemistries, ranging from ceramic composites to precious metal alloys, demands feeder solutions that can adapt to diverse particle shapes, sizes, and densities without compromising process stability. Moreover, the integration of advanced sensor suites and real-time control algorithms has transformed traditional volumetric and gravimetric feeders into intelligent assets within the coating line. These developments not only reduce waste and energy consumption but also empower operators with data-driven insights for rapid process optimization.
This executive summary provides a concise yet comprehensive overview of the emerging trends, regulatory pressures, segmentation dynamics, regional priorities, and competitive landscape shaping the powder feeder market. In addition, it outlines recommended strategic actions for industry leaders aiming to capitalize on these opportunities and navigate potential headwinds. Throughout, the focus remains on delivering actionable intelligence that supports informed decision-making and sustainable growth.
Transformative Shifts Reshaping Powder Feeder Applications
The convergence of digitalization and automation marks the most significant paradigm shift in powder feeder technology. Traditional manual calibration and operator-driven adjustments are giving way to closed-loop feedback systems that continuously monitor powder mass flow, feeder screw torque, and chamber pressure. This evolution aligns with Industry 4.0 objectives, enabling predictive maintenance schedules and minimizing unplanned downtime through early fault detection.
Simultaneously, heightened environmental and safety regulations are driving the adoption of containment and inert gas delivery options within feeder assemblies. Manufacturers now require hermetically sealed feed housings, integrated dust collection, and compliance with stringent emission standards. These advancements facilitate the handling of explosive or moisture-sensitive powders while safeguarding operator health and meeting regulatory mandates.
Moreover, material innovation has accelerated demand for feeders capable of processing novel feedstock formulations. High-entropy alloys, nano-structured ceramics, and specialized composite powders introduce unique flow characteristics that necessitate precise control over vibratory and screw-based feeder designs. As a result, suppliers are investing in modular architectures that allow quick changeover between material sets without extensive downtime.
Finally, the expansion of electric and hybrid mobility platforms, coupled with increased offshore and renewable energy projects, underscores the need for robust corrosion-protection coatings. Powder feeder systems that can deliver uniform deposition rates across large, complex geometries are essential to meeting the performance and longevity requirements of these applications. In this context, agility, scalability, and data connectivity have emerged as the cornerstones of next-generation feeder solutions.
Cumulative Impact of United States Tariffs (2025) on Powder Feeder Supply Chains
Recently implemented and announced tariff measures on imported powders and feeder components have prompted manufacturers to reassess their global sourcing strategies. Aluminum oxide and zirconium oxide, often sourced from non-domestic suppliers, have seen cost fluctuations that reverberate throughout the value chain. As these raw materials constitute a substantial portion of total input costs, tariff-induced price increases have pressured end-users to seek alternative supply channels or negotiate long-term agreements with domestic producers.
Beyond raw ceramic and metallic powders, tariffs have also affected critical feeder subcomponents, including precision machined parts, electronic sensors, and control module chips. Many OEMs have begun localizing production or establishing co-development partnerships to mitigate the risk of supply interruptions. In parallel, some integrators are stockpiling key items to buffer against future policy changes, while others are evaluating dual-sourcing strategies across the Americas and Asia to maintain competitive lead times.
Despite these headwinds, a silver lining has emerged in the form of increased investment in domestic powder processing facilities. Companies that previously relied on imports are now exploring joint ventures or setting up brownfield expansions within tariff-exempt zones. This shift promises to bolster local capacity, reduce dependency on vulnerable trade lanes, and enhance overall supply resilience. However, navigating the evolving regulatory environment requires ongoing vigilance and proactive engagement with policymakers to ensure that industry needs are adequately represented.
Key Segmentation Insights Informing Strategic Focus
An in-depth analysis across end-user industries reveals that the aerospace segment, encompassing both manufacturing and repair-and-overhaul operations, demands feeders with exceptional precision and traceability. Consistency in powder feed rate directly correlates with critical performance attributes of turbine blades and structural panels. In parallel, the automotive sector presents a bifurcated opportunity: OEM manufacturers prioritize high-volume, standardized coating processes, while aftermarket service providers require flexible systems to handle diverse substrate geometries and rapid changeovers.
Within the construction and infrastructure realm, contractor services and material suppliers emphasize equipment portability and ease of setup, reflecting the on-site nature of protective coating applications. The electronics sector’s consumer and industrial subdivisions present unique challenges as well, with delicate consumer device housings requiring low-impact powder delivery, whereas industrial electronics benefit from robust feeders capable of handling higher mass flows to achieve thicker protective layers. Meanwhile, the energy sector is split between oil and gas applications-where extreme corrosion protection under harsh conditions is paramount-and renewable energy solutions that increasingly call for lightweight ceramic and composite coatings to optimize efficiency. Finally, the medical devices market, spanning implantable devices and surgical instruments, places a premium on sterility and minimal particulate contamination, driving the adoption of sealed feeder designs with integrated cleaning protocols.
From a technology perspective, cold spraying systems built around binder and feedstock subsystems are gaining traction due to their lower thermal impact and ability to deposit hard metals. Within these setups, material compositions and powder types vary widely, necessitating feeders that can accommodate irregular particle morphologies without clogging. Thermal spraying-specifically plasma spraying focusing on ceramic coatings-remains indispensable for high-performance oxide and non-oxide ceramics, demanding feeder units that ensure stable flow under high gas temperatures and elevated plasma velocities.
Application segmentation further highlights that corrosion protection use-cases bifurcate into industrial and marine environments. Industrial applications, spanning chemical processing and heavy machinery, often require dense, uniform coatings to withstand abrasive and corrosive media. Marine applications add the complexity of saltwater exposure and fluctuating temperatures, prompting feeder designs with moisture-control features and humidity-resistant seals.
Material segmentation underscores the dichotomy between ceramic and metallic powders. Non-oxide ceramics, such as carbides and nitrides, deliver outstanding hardness but exhibit poor flow characteristics, requiring precision vibratory feeding. Oxide ceramics-including aluminum oxide and zirconium oxide-offer better flowability yet demand feed rate adjustments to prevent gas blockages. On the metallic side, precious metals like gold and silver, used primarily for conductive or decorative finishes, necessitate contamination-free environments. Steel and iron alloys, ranging from stainless steel to tool steel, call for feeders that balance abrasion resistance with minimal mechanical wear on moving parts.
Finally, feeder types themselves fall under the volumetric category, with screw and vibratory feeders each offering distinct advantages. Screw feeders excel at maintaining constant volumetric output over long runs, making them ideal for high-throughput production. Vibratory feeders, on the other hand, enable rapid start-stop cycles and gentle handling of fragile powders, catering to specialized coating recipes that demand frequent material changes.
This comprehensive research report categorizes the Spray System Powder Feeder market into clearly defined segments, providing a detailed analysis of emerging trends and precise revenue forecasts to support strategic decision-making.
- End-User Industry
- Technology Type
- Application
- Material Used
- Feeder Type
Key Regional Insights Driving Market Priorities
In the Americas, the United States and Canada represent the epicenter of advanced manufacturing initiatives, with powder feeders integrated extensively into aerospace, automotive, and defense supply chains. Recent policy incentives aimed at revitalizing domestic production have spurred investments in feeder R&D and manufacturing capacity, reinforcing North America’s position as a technology leader. Similarly, Latin American economies are beginning to adopt powder coating solutions for infrastructure maintenance, creating nascent demand for entry-level feeder systems.
Europe, Middle East & Africa (EMEA) stand at the intersection of stringent environmental regulations and established industrial clusters. Western Europe’s rigorous emissions standards have accelerated the uptake of closed-loop feeder technologies with built-in environmental controls. At the same time, the Middle East is channeling significant capital into oil, gas, and renewable energy infrastructure, driving demand for rugged powder feeding systems that can perform under high ambient temperatures. In Africa, urbanization and infrastructure expansion are fueling interest in cost-effective coating solutions, prompting feeder suppliers to introduce modular, adaptable products that can be retrofitted onto existing lines.
The Asia-Pacific region continues to register the fastest growth trajectory, led by China and India’s burgeoning automotive, electronics, and energy sectors. Domestic manufacturers are rapidly scaling up powder feeder production to meet local content requirements, while strategic partnerships with global technology providers facilitate knowledge transfer. Southeast Asian nations are also emerging as attractive manufacturing hubs for specialty coatings, leveraging favorable trade agreements to import feeder subcomponents and assemble turnkey systems for export.
This comprehensive research report examines key regions that drive the evolution of the Spray System Powder Feeder market, offering deep insights into regional trends, growth factors, and industry developments that are influencing market performance.
- Americas
- Asia-Pacific
- Europe, Middle East & Africa
Key Companies Insights Highlighting Competitive Dynamics
The competitive landscape features a mix of established OEMs and innovative entrants. Gema Switzerland GmbH has built a reputation for high-precision electrostatic powder application and feeder integration, offering turnkey packages tailored for demanding industrial environments. Graco Inc. leverages its fluid handling expertise to deliver feeder solutions with advanced digital controls and remote diagnostics, enabling predictive maintenance across dispersed production sites. Hitachi High-Tech Corporation excels in precision feed systems, combining proprietary sensor technology with robust mechanical design to maintain consistency across diverse powder formulations.
In parallel, ITW Gema continues to expand its portfolio with modular feeder platforms that facilitate rapid changeover and minimize cleaning downtime. METCO Division of Oerlikon Group integrates its metallurgical know-how to optimize feeder performance for high-temperature coatings used in aerospace and power generation. Nordson Corporation strengthens its position through a broad suite of feeder and coating equipment, offering seamless integration across the pre-treatment, feed, and application stages. Praxair Surface Technologies, Inc. leverages the legacy of gas and coating science to refine feeder architectures for specialized material sets.
Emerging players are carving out niches by addressing specific pain points. Resodyn Acoustic Mixers, Inc. applies ultrasonic vibration principles to enhance powder flow uniformity within feeder hoppers. Saint-Gobain focuses on developing next-generation ceramic powders engineered for streamlined feeder transport. Sulzer Ltd brings expertise in fluidic metering to volumetric feeders, ensuring high precision under varying environmental conditions. Thermion Inc. and TRUmachine a USA Manufacturing Solutions Company differentiate themselves through localized engineering services, rapid prototyping capabilities, and turnkey support that reduce time to production for new coating lines.
This comprehensive research report delivers an in-depth overview of the principal market players in the Spray System Powder Feeder market, evaluating their market share, strategic initiatives, and competitive positioning to illuminate the factors shaping the competitive landscape.
- Gema Switzerland GmbH
- Graco Inc.
- Hitachi High-Tech Corporation
- ITW Gema
- METCO Division- Oerlikon
- Nordson Corporation
- Oerlikon Group
- Praxair Surface Technologies, Inc.
- Resodyn Acoustic Mixers, Inc.
- Saint-Gobain
- Sulzer Ltd
- Thermion Inc.
- TRUmachine a USA Manufacturing Solutions Company
Actionable Recommendations for Industry Leaders
To maintain a competitive edge, organizations must prioritize the integration of smart feeder platforms that incorporate real-time monitoring of mass flow, torque, and environmental parameters. Investing in digital twins and simulation tools will enable rapid validation of feeder performance across new powder compositions, reducing trial-and-error cycles.
Diversifying the supply chain by establishing partnerships with domestic powder producers and feeder subcomponent manufacturers can mitigate tariff risks and logistical bottlenecks. Collaborative R&D agreements with material scientists and academic institutions will accelerate the development of next-generation feedstock formulations and feeder designs.
Sustainability should be embedded into product roadmaps, with a focus on energy-efficient feeder drives, closed-loop material recycling, and minimize overspray. Industry leaders must also expand aftermarket service offerings, including predictive maintenance contracts, remote troubleshooting, and operator training programs to drive higher yield and customer retention.
Finally, proactive engagement with regulatory bodies and standards organizations will ensure that feeder technologies remain compliant and that industry perspectives shape forthcoming environmental and safety regulations. By aligning technological innovation with strategic partnerships and regulatory foresight, companies can secure long-term growth and reinforce their leadership position.
Explore AI-driven insights for the Spray System Powder Feeder market with ResearchAI on our online platform, providing deeper, data-backed market analysis.
Ask ResearchAI anything
World's First Innovative Al for Market Research
Conclusion: Positioning for Sustainable Growth
The powder feeder segment within spray coating systems stands at an inflection point, driven by technological breakthroughs, evolving material demands, and shifting geopolitical landscapes. Aligning product strategies with end-user requirements across aerospace, automotive, energy, and medical applications will be critical. Embracing digitalization, green manufacturing principles, and resilient supply chain models can unlock substantial competitive advantages.
As environmental and regulatory pressures mount, the ability to deliver precise, reliable, and compliant feeder solutions will determine market winners. By leveraging detailed segmentation insights, understanding regional priorities, and closely monitoring competitor innovations, industry leaders can craft informed roadmaps that balance short-term performance needs with long-term sustainability goals.
This section provides a structured overview of the report, outlining key chapters and topics covered for easy reference in our Spray System Powder Feeder market comprehensive research report.
- Preface
- Research Methodology
- Executive Summary
- Market Overview
- Market Dynamics
- Market Insights
- Cumulative Impact of United States Tariffs 2025
- Spray System Powder Feeder Market, by End-User Industry
- Spray System Powder Feeder Market, by Technology Type
- Spray System Powder Feeder Market, by Application
- Spray System Powder Feeder Market, by Material Used
- Spray System Powder Feeder Market, by Feeder Type
- Americas Spray System Powder Feeder Market
- Asia-Pacific Spray System Powder Feeder Market
- Europe, Middle East & Africa Spray System Powder Feeder Market
- Competitive Landscape
- ResearchAI
- ResearchStatistics
- ResearchContacts
- ResearchArticles
- Appendix
- List of Figures [Total: 26]
- List of Tables [Total: 1022 ]
Call-To-Action: Connect with Ketan Rohom to Acquire the Full Report
For comprehensive, data-driven analysis and strategic recommendations tailored to your organization’s needs, contact Ketan Rohom (Associate Director, Sales & Marketing at 360iResearch). Secure your copy of the full market research report today and empower your team with actionable insights to lead in the powder feeder market.
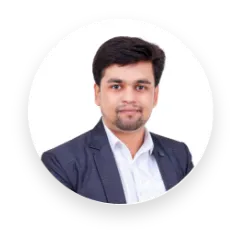
- When do I get the report?
- In what format does this report get delivered to me?
- How long has 360iResearch been around?
- What if I have a question about your reports?
- Can I share this report with my team?
- Can I use your research in my presentation?