Introduction to Polymer Stabilizers and Market Drivers
Polymer stabilizers are indispensable additives designed to protect polymer chains from degradation induced by thermal, oxidative, and photolytic stress. As polymers become the material of choice across industries-from automotive components to flexible packaging-the demand for robust stabilization solutions has intensified. Modern formulations must address a spectrum of performance criteria: antioxidants prevent radical‐mediated breakdown, heat stabilizers inhibit thermal scission during processing, and light stabilizers shield against ultraviolet‐driven discoloration and embrittlement. Processing aids further enhance melt flow and surface finish, ensuring reliable manufacturing workflows.
Against a backdrop of evolving environmental regulations and heightened consumer expectations for durability, manufacturers are investing in next‐generation compounds that combine efficacy with sustainability. Emerging bio-based and multifunctional stabilizers are gaining traction as formulators seek to minimize additive loading while maximizing protective performance. Moreover, digital process controls and real-time monitoring technologies are enabling tighter control of stabilization during polymer extrusion and molding.
This introduction sets the stage for an in-depth examination of disruptive trends, regulatory shifts, and strategic priorities shaping the stabilizer landscape into 2025 and beyond.
Transformative Shifts Driving Innovation and Sustainability
The stabilizer landscape is undergoing transformative shifts propelled by technological innovation, stringent regulations, and evolving material requirements. Sustainability has emerged as a core driver: formulators are replacing legacy metallic salts and halogenated compounds with eco-friendly organic stabilizers and biopolymer-compatible antioxidants. At the same time, advanced hindered amine light stabilizers are being engineered at the molecular level to deliver extended UV protection with minimal migration in flexible films and molded parts.
Regulatory frameworks in key markets are tightening, with new restrictions on heavy metals and volatile organic components prompting suppliers to innovate rapidly. In parallel, digitalization of manufacturing processes is enabling real-time additive dosing and adaptive control of thermal profiles, reducing waste and improving batch consistency. Supply chain volatility, exacerbated by raw material price swings, has accelerated the adoption of alternative chemistries and regional sourcing strategies.
Collectively, these forces are redefining product portfolios, sparking collaborations between additive specialists and polymer producers, and driving investment in research and pilot‐scale production. The result is a dynamic ecosystem in which performance, compliance, and sustainability goals converge to reshape market competition.
Cumulative Impact of United States Tariffs 2025
With the onset of new United States tariffs in 2025, the stabilizer sector is experiencing a cumulative impact across raw material procurement, pricing strategies, and global trade flows. Import duties on key antioxidant and light stabilizer intermediates have elevated input costs, prompting manufacturers to reassess supplier portfolios and negotiate long-term contracts to hedge against volatility. Consequently, some end-use producers have shifted toward domestic or near-shored sources to mitigate tariff exposure and ensure supply continuity.
These trade measures have also accelerated vertical integration moves, as major chemical producers seek to internalize critical precursor synthesis. Companies are exploring cooperative ventures with regional distributors to better absorb tariff burdens and maintain competitive pricing for automotive, construction, and packaging customers. Meanwhile, formulators are prioritizing multifunctional stabilizers that can replace multiple additives in a single package, offsetting cost increases through additive reduction and streamlined inventory management.
Ultimately, the 2025 tariff landscape has compelled industry participants to adopt agile sourcing frameworks, diversify their supply chains, and deepen collaboration across the value chain. The resulting strategic realignments promise greater resilience but also highlight the necessity of proactive risk management.
Key Segmentation Insights Across Types and Applications
Segmentation by type reveals that antioxidants continue to dominate, driven by the necessity for both aminic and phenolic variants. Within phenolic antioxidants, bifunctional and monofunctional derivatives cater to high-performance applications demanding superior thermal stability. Heat stabilizers, comprising metallic salts and organic stabilizers, remain essential for PVC and engineering resins, while the expanding portfolio of hindered amine light stabilizers and UV absorbers-such as benzophenones and benzotriazoles-addresses UV degradation in outdoor films and automotive coatings. Processing aids, particularly lubricants and plasticizers, optimize flow and surface quality in extrusion and injection molding.
Examining end-use industries, agriculture’s greenhouse and mulch films rely on advanced light stabilizers for UV resistance; automotive exterior and interior components necessitate heat and oxidative stabilizers for durability; construction pipes, fittings, profiles, and panels depend on long-term thermal and UV protection; consumer electronics and appliances require color retention and mechanical anti-aging solutions; packaging segments-including flexible and rigid formats-prioritize food-contact compliant stabilizers.
From a polymer perspective, polyethylene-both high-density and low-density-remains the largest base, followed by polypropylene variants, polyethylene terephthalate, polystyrene, and PVC. Functions such as color retention and mechanical anti-aging dominate, with processing facilitation growing in tandem. Applications span adhesives and sealants, extruded parts like foils, films, pipes, and sheets, fibers, textiles, and molded parts. Raw material choices between inorganic and organic compounds hinge on regulatory requirements and performance targets.
This comprehensive research report categorizes the Stabilizer for Polymers market into clearly defined segments, providing a detailed analysis of emerging trends and precise revenue forecasts to support strategic decision-making.
- Type
- End-Use Industry
- Polymer Type
- Function
- Application
- Raw Material
Key Regional Dynamics Shaping Stabilizer Demand
In the Americas, regulatory clarity and access to feedstock drive steady uptake of next-generation stabilizers. Local producers are leveraging integrated manufacturing hubs to optimize logistics and meet the stringent standards of automotive and packaging customers. Meanwhile, Europe, the Middle East & Africa are characterized by robust regulatory frameworks that incentivize low-emission chemistries and circularity initiatives; the region is at the forefront of developing compostable and recyclable polymer systems requiring tailored stabilization solutions. In Asia-Pacific, burgeoning infrastructure projects, expanding automotive production, and growing consumer electronics demand underpin rapid adoption, but price sensitivity and localized raw material supply chains influence formulators to focus on cost-effective organic stabilizers and regional collaborations.
Cross-regional trade flows are adapting accordingly: North American manufacturers are exporting specialized additives to Latin America; European suppliers are forging distribution partnerships across the Gulf and Africa; and Asian producers are scaling capacity to serve both domestic markets and export corridors. This dynamic regional interplay underscores the need for flexible supply chain models that can pivot in response to tariff shifts, raw material scarcities, or regulatory updates.
This comprehensive research report examines key regions that drive the evolution of the Stabilizer for Polymers market, offering deep insights into regional trends, growth factors, and industry developments that are influencing market performance.
- Americas
- Asia-Pacific
- Europe, Middle East & Africa
Key Company Strategies and Innovations
Leading additive suppliers are doubling down on R&D to deliver multifunctional and sustainable stabilizer systems. Industry incumbents such as BASF SE and AkzoNobel N.V. are expanding pilot facilities to test novel organic heat stabilizers, while companies like Songwon Industrial Co., Ltd. and Adeka Corporation are focusing on high-performance hindered amine light stabilizers tailored for high-molecular-weight polymers. Specialty distributors, including Brenntag AG and 3V Sigma S.p.A., are forging strategic alliances to streamline global logistics and inventory management.
At the same time, firms such as LG Chemical Ltd and Evonik Industries AG are integrating value-added services-like formulation consultancy and predictive maintenance tools-to differentiate their offerings. Consolidation and M&A activity remain pronounced, evidenced by Solvay S.A.’s acquisition of Cytec Industries and Clariant’s strategic divestments, which are reshaping competitive dynamics. Emerging players, including Mayzo Inc. and PCC Rokita SA, are carving niches in bio-derived antioxidants and non-discoloring stabilizers for food-grade applications.
Collectively, these companies underscore a trend toward collaboration, end-to-end supply chain transparency, and sustainable innovation as the foundations for future growth.
This comprehensive research report delivers an in-depth overview of the principal market players in the Stabilizer for Polymers market, evaluating their market share, strategic initiatives, and competitive positioning to illuminate the factors shaping the competitive landscape.
- 3V Sigma S.p.A.
- Addivant USA LLC
- Adeka Corporation
- AkzoNobel N.V.
- BASF SE
- Brenntag AG
- Chemtura Corporation
- Ciba Specialty Chemicals Inc. (A Subsidiary of BASF)
- Clariant International Ltd.
- Cytec Industries Inc. (Acquired by Solvay)
- Eastman Chemical Company
- Evonik Industries AG
- LG Chemical Ltd
- Mayzo Inc.
- Milliken & Company
- Mitsui Chemicals, Inc.
- PCC Rokita SA
- Solvay S.A.
- Songwon Industrial Co., Ltd
Actionable Recommendations for Industry Leaders
Industry leaders should prioritize the development of bio-based and multifunctional stabilizer platforms that reduce additive loadings while meeting stringent performance targets. Establishing cross-functional innovation teams with polymer producers can accelerate the translation of lab-scale breakthroughs into commercial formulations. To mitigate tariff-driven cost pressures, companies must diversify raw material sourcing by cultivating partnerships across key regions and exploring local manufacturing or toll-processing arrangements.
Moreover, investing in advanced digital tools for process analytics will enhance real-time monitoring of stabilization kinetics, reducing waste and ensuring consistent product quality. Leaders should also engage proactively with regulatory bodies to shape forthcoming compliance standards and secure early insights into evolving environmental requirements. Finally, offering value-added services-such as custom application support, predictive maintenance, and virtual training-can differentiate stabilizer portfolios in competitive end-use segments.
Explore AI-driven insights for the Stabilizer for Polymers market with ResearchAI on our online platform, providing deeper, data-backed market analysis.
Ask ResearchAI anything
World's First Innovative Al for Market Research
Conclusion and Strategic Imperatives
As the stabilizer market continues to evolve under the influence of sustainability mandates, tariff realignments, and technological advancements, stakeholders must adopt a proactive stance. Integrating eco-friendly chemistries, harnessing digital manufacturing platforms, and forging agile supply chains will define success. Cross-industry collaborations-spanning raw material suppliers, additive formulators, and polymer processors-are essential to de-risk product launches and accelerate time to market.
By aligning strategic investments with regional dynamics and regulatory trajectories, companies can capture emerging opportunities in high-growth end-use segments such as automotive lightweighting, sustainable packaging, and UV-resistant agricultural films. Ultimately, the ability to anticipate market disruptions and respond with innovative, compliant stabilization solutions will secure competitive advantage and drive long-term value creation.
This section provides a structured overview of the report, outlining key chapters and topics covered for easy reference in our Stabilizer for Polymers market comprehensive research report.
- Preface
- Research Methodology
- Executive Summary
- Market Overview
- Market Dynamics
- Market Insights
- Cumulative Impact of United States Tariffs 2025
- Stabilizer for Polymers Market, by Type
- Stabilizer for Polymers Market, by End-Use Industry
- Stabilizer for Polymers Market, by Polymer Type
- Stabilizer for Polymers Market, by Function
- Stabilizer for Polymers Market, by Application
- Stabilizer for Polymers Market, by Raw Material
- Americas Stabilizer for Polymers Market
- Asia-Pacific Stabilizer for Polymers Market
- Europe, Middle East & Africa Stabilizer for Polymers Market
- Competitive Landscape
- ResearchAI
- ResearchStatistics
- ResearchContacts
- ResearchArticles
- Appendix
- List of Figures [Total: 28]
- List of Tables [Total: 989 ]
Contact Ketan Rohom to Access the Full Market Research Report
For a comprehensive analysis of market dynamics, competitive landscapes, and emerging opportunities in the polymer stabilizer sector, contact Ketan Rohom (Associate Director, Sales & Marketing) to explore the full research report. Gain detailed insights, actionable data, and expert guidance to inform your strategic planning and drive growth initiatives.
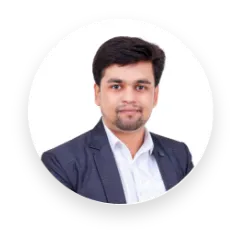
- When do I get the report?
- In what format does this report get delivered to me?
- How long has 360iResearch been around?
- What if I have a question about your reports?
- Can I share this report with my team?
- Can I use your research in my presentation?