Laying the Foundation for Stainless Steel’s Role in Semiconductor Production
The integration of stainless steel into semiconductor manufacturing processes has been instrumental in advancing wafer fabrication, chemical delivery, and thermal management systems. This executive summary introduces the fundamental properties that make stainless steel indispensable-from its corrosion resistance in ultra-pure environments to its mechanical strength under high-temperature cycling. By exploring the material’s critical role in chamber components, process piping, heat exchangers, and wafer carriers, we underscore how strategic alloy selection and surface treatment optimize yield and reliability.
As semiconductor nodes shrink and device architectures become more complex, the demand for precision-engineered stainless steel components intensifies. This section establishes the foundation for understanding why material performance, contamination control, and manufacturing scalability are intertwined. Readers will gain clarity on how stainless steel innovations support the industry’s relentless pursuit of higher throughput, lower defect rates, and cost efficiency. With this overview, stakeholders are equipped to appreciate the intricate balance between metallurgical science and production imperatives.
Navigating Transformative Shifts Reshaping the Stainless Steel Landscape
Over the past decade, several transformative shifts have reshaped the stainless steel landscape within semiconductor fabrication. Accelerated by global supply chain disruptions and intensified by sustainability mandates, producers have adopted digital twins and predictive analytics to anticipate material performance and manage inventory more efficiently. Concurrently, advancements in additive manufacturing techniques have enabled complex geometries and localized alloy customization, reducing lead times and waste.
Moreover, the industry’s carbon footprint has come under scrutiny, propelling investments in hydrogen-based steelmaking and closed-loop water systems. Such green initiatives are redefining the competitive landscape, as early adopters gain regulatory incentives and reputational advantage. In parallel, the proliferation of 5G and AI-driven fabrication tools demands ultra-high-purity stainless steel alloys with stringent surface finishes. By harnessing real-time process monitoring and machine learning, material suppliers and fabs collaborate closely to refine contamination control protocols. These shifts collectively signal a new era where agile, sustainable, and technologically empowered stainless steel solutions drive semiconductor innovation.
Unpacking the Cumulative Impact of U.S. 2025 Tariffs on Industry Dynamics
The imposition of United States tariffs on imported stainless steel in 2025 has introduced far-reaching implications for cost structures and supply chain resilience. Fabricators now face increased raw material expenses, prompting many to explore alternative alloy grades and diversify purchasing strategies across global markets. Domestic mill expansions have accelerated, yet capacity constraints persist, compelling some semiconductor manufacturers to lock in multi-year contracts at premium rates.
Simultaneously, the tariff-driven price escalation has incentivized investments in waste reduction and recycling initiatives, as companies seek to mitigate margin erosion. Suppliers are collaborating with end users to implement closed-loop scrap recovery systems, thereby improving metal utilization and reducing reliance on tariff-exposed imports. Additionally, regional sourcing hubs have expanded to serve as buffer stocks, smoothing supply fluctuations. Through these adaptive strategies, the industry is demonstrating resilience, though volatility in steel pricing continues to pose planning challenges for capital-intensive fab projects.
Deep Dive into Application, Product, Alloy, Surface, and Thickness Segmentation Insights
Insightful segmentation reveals how stainless steel applications are tailored to meet distinct semiconductor manufacturing needs. Chamber components, which encompass electrostatic chucks, liners, and susceptors, demand alloys with precise thermal conductivity and chemical compatibility. Heat exchangers-ranging from plate and frame to shell and tube as well as spiral designs-necessitate customized stainless steel grades to manage extreme temperature differentials with minimal fouling. In critical fluid transport networks, chemical delivery piping, gas distribution lines, and ultra-pure water conduits rely on meticulously polished surfaces to prevent contamination and maintain process integrity. Wafer carriers, including FOUPs, mandrels, and SMIF pods, integrate high-purity stainless steel to protect delicate wafers during automated handling.
Product segmentation further highlights the diverse forms in which stainless steel is deployed. Bar and rod stock serve precision mechanical fixtures, while sheet and plate materials address large-format chamber liners. Strip and foil products-spanning cold-rolled strip, foil, and hot-rolled strip-enable thin-film deposition tools to achieve uniform coating. Tube and pipe offerings, from seamless tubes to welded pipe, underpin high-pressure and high-purity process loops. Wire is often employed for fine-detail fixtures and connectors. Alloy grade segmentation underscores the prevalence of 304, 316L, 321, and duplex stainless steel, each selected for its unique corrosion resistance and mechanical strength under process stresses.
Surface finish is equally pivotal: electro-polished treatments deliver exceptional smoothness to reduce particle entrapment, mirror polishing achieves ultra-low roughness for critical optical applications, passivation enhances chromium oxide layers to guard against corrosion, and pickling removes surface contaminants after fabrication. Finally, thickness gauge distinctions-from sub-millimeter foil to plates exceeding three millimeters-determine structural rigidity and thermal mass, aligning material choice with equipment specifications. Together, these segmentation insights offer a holistic view of how stainless steel variants are meticulously aligned with semiconductor fabrication requirements.
This comprehensive research report categorizes the Stainless Steel for Semiconductor market into clearly defined segments, providing a detailed analysis of emerging trends and precise revenue forecasts to support strategic decision-making.
- Application
- Product
- Alloy Grade
- Surface Finish
- Thickness Gauge
Regional Dynamics Driving Demand Across the Globe
Regional dynamics play a crucial role in shaping stainless steel demand for semiconductor fabs. In the Americas, robust capital investments in advanced logic and memory fabs have bolstered consumption of high-purity alloys and precision-formed components. Local content requirements and infrastructure incentives have spurred domestic mill expansions, while cross-border trade agreements continue to influence procurement strategies.
Europe, Middle East, and Africa present a multifaceted landscape where stringent environmental regulations and circular economy directives drive the adoption of recycled stainless steel. Advanced packaging and photonics hubs in Western Europe rely on specialized surface finishes and customized alloy grades to meet exacting performance criteria. Meanwhile, emerging markets in the Middle East are investing in greenfield fabrication facilities, creating new opportunities for suppliers to introduce next-generation stainless steel solutions.
Asia-Pacific remains the largest region by volume, fueled by sustained growth in wafer fab capacity across China, Taiwan, South Korea, and Japan. High-throughput fabs demand ever-greater precision in chamber components and piping systems, pushing suppliers to innovate in alloy development and process control. Government support for semiconductor self-sufficiency and extensive R&D collaborations underline the region’s critical importance to the global stainless steel ecosystem.
This comprehensive research report examines key regions that drive the evolution of the Stainless Steel for Semiconductor market, offering deep insights into regional trends, growth factors, and industry developments that are influencing market performance.
- Americas
- Europe, Middle East & Africa
- Asia-Pacific
Competitive Landscape and Leading Innovators in Stainless Steel
The competitive landscape in stainless steel for semiconductor manufacturing is characterized by strategic consolidation, technology-driven differentiation, and collaborative innovation. Market leaders are expanding their portfolios through mergers and acquisitions, integrating capabilities in advanced alloy development, precision machining, and digital supply chain platforms. Strategic partnerships between material suppliers and equipment OEMs are accelerating co-development initiatives aimed at optimizing chamber component lifecycles and minimizing contamination risks.
Innovative firms are investing heavily in R&D to engineer next-generation stainless steel alloys with enhanced hydrogen embrittlement resistance and improved surface stability under plasma exposure. Proprietary surface treatment processes, coupled with real-time process analytics, allow companies to offer performance guarantees that align with customers’ yield and uptime targets. Additionally, sustainability leaders are distinguishing themselves by achieving high recycled content and lower carbon footprints through green steelmaking and energy-efficiency upgrades.
As smaller specialized vendors focus on niche applications-such as ultra-thin foil for advanced packaging-larger players leverage scale to deliver integrated solutions spanning global logistics, inventory management, and technical support. These complementary strategies demonstrate a vibrant ecosystem where collaboration and competition drive continuous improvement.
This comprehensive research report delivers an in-depth overview of the principal market players in the Stainless Steel for Semiconductor market, evaluating their market share, strategic initiatives, and competitive positioning to illuminate the factors shaping the competitive landscape.
- Tsingshan Holding Group Co., Ltd.
- Pohang Iron and Steel Company, Ltd.
- Aperam S.A.
- Jindal Stainless Limited
- Outokumpu Oyj
- Acerinox Sociedad Anónima
- thyssenkrupp AG
- JFE Steel Corporation
- Nippon Steel Corporation
- China Baowu Steel Group Corporation Limited
Actionable Strategies for Industry Leaders to Capitalize on Emerging Trends
To capitalize on emerging opportunities, industry leaders must adopt a multifaceted approach that spans supply chain optimization, technological investment, and sustainability leadership. Strengthening supplier partnerships through long-term agreements and joint risk-sharing models can stabilize raw material supply and insulate operations from tariff volatility. Investing in digital platforms for real-time inventory management and predictive maintenance will improve operational agility and reduce downtime costs.
On the technology front, directing R&D resources toward next-generation stainless steel alloys-tailored for low-particle surface finishes and enhanced thermal performance-will future-proof component reliability. Embracing circular economy principles by implementing closed-loop scrap recovery and recycling programs will lower costs and reinforce environmental credentials. Leaders should also explore strategic alliances with equipment OEMs and end users to co-develop materials and processes that accelerate fab ramp-up schedules.
Finally, establishing clear ESG targets and transparently reporting progress will differentiate brands and foster trust among investors, regulators, and customers. By aligning strategic initiatives across procurement, engineering, and sustainability teams, organizations can drive innovation, mitigate risk, and secure competitive advantage.
Rigorous Research Methodology Ensuring Market Analysis Accuracy
This analysis is built upon a rigorous research framework combining primary interviews with semiconductor fabricators, stainless steel producers, and industry experts. Secondary research included peer-reviewed journals, trade publications, and regulatory filings to validate market drivers and supply chain dynamics. Data triangulation techniques were employed to reconcile quantitative metrics from government trade databases with proprietary industry surveys.
To ensure robustness, findings were cross-checked against case studies of fab implementations and vendor performance reports. An expert panel reviewed draft insights to confirm technical accuracy and relevance to key stakeholders. All proprietary data sources and methodologies adhere to best practices in market research governance, ensuring that conclusions are reliable and actionable.
Explore AI-driven insights for the Stainless Steel for Semiconductor market with ResearchAI on our online platform, providing deeper, data-backed market analysis.
Ask ResearchAI anything
World's First Innovative Al for Market Research
Key Takeaways Shaping the Future of Stainless Steel in Semiconductors
The strategic importance of stainless steel in semiconductor manufacturing cannot be overstated. From enabling contamination-free fluid delivery to supporting high-temperature processing in chamber components, stainless steel underpins core fab operations. Navigating tariff impacts, regional complexities, and evolving sustainability requirements demands proactive strategies and collaborative innovation.
By leveraging detailed segmentation analysis, industry participants can align material selection with application-specific demands, optimize cost structures, and future-proof their supply chains. As leading players invest in alloy R&D, digital process controls, and green steelmaking, the competitive landscape will continue to evolve. Organizations that integrate these insights into their planning and execution will be well positioned to drive yield improvements, operational resilience, and long-term growth.
This section provides a structured overview of the report, outlining key chapters and topics covered for easy reference in our Stainless Steel for Semiconductor market comprehensive research report.
- Preface
- Research Methodology
- Executive Summary
- Market Overview
- Market Dynamics
- Market Insights
- Cumulative Impact of United States Tariffs 2025
- Stainless Steel for Semiconductor Market, by Application
- Stainless Steel for Semiconductor Market, by Product
- Stainless Steel for Semiconductor Market, by Alloy Grade
- Stainless Steel for Semiconductor Market, by Surface Finish
- Stainless Steel for Semiconductor Market, by Thickness Gauge
- Americas Stainless Steel for Semiconductor Market
- Europe, Middle East & Africa Stainless Steel for Semiconductor Market
- Asia-Pacific Stainless Steel for Semiconductor Market
- Competitive Landscape
- ResearchAI
- ResearchStatistics
- ResearchContacts
- ResearchArticles
- Appendix
- List of Figures [Total: 26]
- List of Tables [Total: 511 ]
Secure Your Comprehensive Market Intelligence Today
Embrace the opportunity to deepen your understanding of the stainless steel market within the semiconductor industry. For tailored insights and strategic guidance, connect with Ketan Rohom, Associate Director, Sales & Marketing, and secure the comprehensive report that will empower your organization to navigate evolving market complexities and drive sustainable growth.
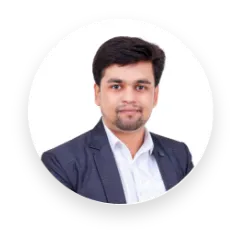
- When do I get the report?
- In what format does this report get delivered to me?
- How long has 360iResearch been around?
- What if I have a question about your reports?
- Can I share this report with my team?
- Can I use your research in my presentation?