Setting the Stage for Hygienic Pressure Measurement
Stainless steel hygienic diaphragm pressure gauges represent the intersection of robust industrial measurement and stringent sanitary requirements. Constructed from high-grade stainless steel and featuring a flexible diaphragm barrier, these gauges ensure accurate pressure indication while isolating delicate sensing components from corrosive or fouling media. Their seamless design addresses the critical safety and purity mandates that underpin operations in biotechnology, food processing, pharmaceutical manufacturing and water treatment facilities.
Hygienic diaphragm gauges have gained prominence as operational stakeholders navigate complex regulatory landscapes and aim to safeguard product integrity. The elimination of crevices and the adoption of FDA and EHEDG-compliant finishes minimize contamination risks, while the diaphragm’s rapid response characteristics deliver real-time feedback essential for precise process control.
This executive summary synthesizes the key technological advances, regulatory drivers and strategic considerations influencing the market. It highlights the transformative shifts redefining competitive dynamics, examines tariff-induced supply chain adjustments and distills segmentation and regional perspectives. Through an authoritative yet accessible lens, the analysis equips decision-makers with a clear understanding of current challenges and emerging opportunities, laying the groundwork for informed strategic planning.
Recent integration of digital outputs and IoT-enabled diagnostics further elevates the value proposition of these gauges. By enabling remote calibration alerts and predictive maintenance analytics, manufacturers can reduce downtime and optimize total cost of ownership. As industries strive for enhanced operational efficiency and zero-tolerance contamination strategies, the fusion of hygienic design and smart instrumentation has become a cornerstone of modern process control frameworks.
Uncovering Industry's Most Disruptive Technological and Regulatory Shifts
Innovation in sensor technology and data connectivity has ushered in a new era for pressure measurement instrumentation. IoT-enabled diaphragm gauges now deliver continuous, high-fidelity pressure data streams directly into analytics platforms, empowering engineers to anticipate deviations and enact corrective measures before disruptions occur. The convergence of digital diagnostics, wireless communication protocols and cloud-based monitoring has redefined maintenance paradigms, moving from reactive interventions to proactive asset management. These capabilities have elevated the role of pressure gauges from passive indicators to active contributors within automated process ecosystems.
Meanwhile, regulatory frameworks have intensified their focus on product hygiene and environmental stewardship. Global food safety standards and pharmaceutical validation guidelines demand equipment that can withstand rigorous clean-in-place procedures without compromising performance. The drive for sustainable manufacturing has also catalyzed the adoption of eco-friendly metal finishes and the minimization of waste through precision fabrication techniques. As a result, material science advancements-such as the introduction of corrosion-resistant stainless steel alloys with enhanced pitting resistance-have become pivotal enablers of next-generation hygienic instruments.
At the same time, additive manufacturing and advanced machining processes allow for complex diaphragm geometries and seamless gauge bodies that further reduce contamination vectors. Customization at scale has become feasible through modular design platforms, providing industry stakeholders with tailored solutions for niche applications. Supply chain strategies are evolving to balance global sourcing efficiencies with the resilience of localized production, thereby mitigating geopolitical risks and aligning with new tariff environments.
These transformative shifts coalesce to redefine competitive advantage, placing a premium on agility, technological leadership and regulatory compliance. Understanding these dynamics is essential for stakeholders seeking to navigate an increasingly complex and opportunity-rich landscape.
Assessing the Ripple Effects of US Tariffs on Stainless Steel Gauges
The introduction of elevated tariffs on imported stainless steel and related pressure measurement equipment has introduced a new variable into procurement decisions and cost management strategies. With duties fluctuating in response to geopolitical tensions and trade policy revisions, original equipment manufacturers and end users alike are reassessing supplier portfolios and negotiating new contractual terms to maintain financial predictability. The cumulative imposition of duties on raw materials, intermediate components and finished diaphragm gauges has incrementally increased landed costs, challenging stakeholders to absorb these expenses or pass them through within increasingly price-sensitive markets.
To offset tariff-related cost pressures, many enterprises are shifting procurement toward domestic manufacturers or to regions with preferential trade agreements. This strategic realignment often entails higher labor and compliance expenditures but offers the advantage of reduced exposure to abrupt policy changes and enhanced visibility into production processes. Some operators are also engaging in dual sourcing strategies, splitting orders across low-tariff countries and domestic suppliers to balance cost, quality and delivery lead times.
Concurrently, manufacturers of hygienic diaphragm gauges are responding by optimizing production footprints, investing in regional fabrication hubs and exploring vertical integration opportunities. These initiatives not only mitigate tariff impact but also shorten supply chains and facilitate faster customization. By leveraging local inventories and regional service networks, gauge producers can improve lead times and strengthen customer relationships.
Over the longer term, the shifting tariff landscape is driving a reevaluation of total cost of ownership frameworks. Stakeholders are placing greater emphasis on end-to-end transparency, risk-sharing partnerships and adaptive logistics solutions. Navigating this evolving environment requires a nuanced understanding of tariff schedules, trade agreements and jurisdictional compliance requirements, which are integral to securing supply chain resilience and maintaining competitive margins.
Deep-Dive into Market Segmentation Drivers and Technical Requirements
Detailed analysis across multiple segmentation vectors reveals distinct consumption patterns and technical requirements for hygienic diaphragm gauges. Industrial end users within biotechnology prioritize gauges fabricated from 316L stainless steel diaphragms, leveraging high corrosion resistance for sensitive production and research applications. In chemical and petrochemical environments, where processes range from agrochemical production to specialty chemical synthesis, the need for robust pressure ranges up to and beyond 25 MPa drives adoption of flanged connections and advanced seal materials like PTFE to handle aggressive media.
In the food and beverage sector, hygiene credentials are paramount; dairy and brewery operations favor tri-clamp end connections and EPDM seals for their rapid clean-in-place compatibility and minimal hold-up volumes. Meat processing facilities and soft drink manufacturers similarly demand flush or panel mounting configurations to facilitate regular washdowns and inspection. Within pharmaceutical manufacturing-spanning biopharma, generic drug production and vaccine formulation-the emphasis falls on traceability and sterilizability, leading to widespread use of threaded or tri-clamp interfaces coupled with FKM seals for their broad chemical compatibility.
Water and wastewater applications, whether municipal or industrial, often utilize direct or wall-mounted gauges with pressure ranges calibrated to lower thresholds such as 0–1 MPa and 1–10 MPa. Here, the cost-to-performance balance is at the forefront, prompting selection of 304 stainless steel diaphragms and simplified connections to streamline maintenance.
Mounting preferences also reflect operational priorities, with panel-mount designs gaining traction in process control units where instrument consolidation and user ergonomics are essential. Across all application domains-be it flow, level, pressure measurement or closed-loop process management-the convergence of diaphragm material properties, seal chemistries and connection types defines the performance envelope. These segmentation insights equip stakeholders with the nuanced understanding needed to align product specifications with application demands and regulatory mandates.
This comprehensive research report categorizes the Stainless Steel Hygienic Diaphragm Pressure Gauge market into clearly defined segments, providing a detailed analysis of emerging trends and precise revenue forecasts to support strategic decision-making.
- Industry
- End Connection
- Pressure Range
- Mounting Type
- Seal Material
- Application
- Diaphragm Material
Mapping Regional Trends Shaping Global Adoption Patterns
Regional dynamics exert a profound influence on the adoption trajectory of stainless steel hygienic diaphragm pressure gauges. In the Americas, robust investment in food and beverage, biopharma and water treatment infrastructure underpins sustained demand. North American manufacturers often lead in customization, offering integrated digital monitoring modules that align with industry 4.0 initiatives. Meanwhile, Latin American markets are increasingly prioritizing hygienic instrumentation to support burgeoning dairy and brewery sectors as consumer preferences shift toward high-quality processed foods.
Across Europe, Middle East and Africa, stringent regulatory regimes drive equipment specifications in regulated industries. European Union directives and Middle Eastern quality standards mandate rigorous clean-in-place validation and material traceability, elevating demand for gauges that meet EHEDG and 3-A Sanitary Standards. In Africa, major urbanization projects and investments in municipal water systems are creating fresh opportunities for hygienic pressure measurement solutions, albeit tempered by cost-sensitive procurement practices.
In the Asia-Pacific region, expanding chemical manufacturing hubs and rapidly developing pharmaceutical complexes fuel market growth. Nations in East and Southeast Asia are adopting advanced diaphragm gauges to enhance process reliability, while India’s focus on pharmaceutical exports is catalyzing demand for certified hygienic instrumentation. Concurrently, water scarcity challenges in Australia and parts of Southeast Asia amplify the need for precise pressure monitoring in wastewater recycling and desalination processes.
Regional supply chains are adapting to these trends through localized production facilities and service centers that provide rapid calibration, certification and field support. Understanding these divergent regional priorities enables market participants to tailor offerings and channel strategies in accordance with local regulatory, economic and operational factors.
This comprehensive research report examines key regions that drive the evolution of the Stainless Steel Hygienic Diaphragm Pressure Gauge market, offering deep insights into regional trends, growth factors, and industry developments that are influencing market performance.
- Americas
- Europe, Middle East & Africa
- Asia-Pacific
Profiling Leading Innovators Driving Market Evolution
In an increasingly competitive landscape, key manufacturers are differentiating through technological prowess and strategic service networks. Leading global instrument makers have expanded their portfolios to include smart hygienic diaphragm gauges that integrate predictive analytics and remote diagnostics. These companies often leverage established channel partnerships to secure footholds in regulated industries such as pharmaceuticals and food processing, where turnkey solutions and compliance expertise are highly valued.
Some enterprises have pursued targeted acquisitions to bolster their sanitary instrumentation capabilities, acquiring specialized diaphragm manufacturing facilities or digital sensing startups to accelerate innovation cycles. Others focus on joint development agreements with process automation integrators, embedding pressure gauge modules within broader control system architectures to deliver seamless data workflows and unified maintenance platforms.
A subset of regional and niche players emphasizes rapid customization and localized support, offering modular designs that can be tailored to unique process requirements and delivered with expedited lead times. Their agility in manufacturing and certification empowers end users to deploy application-specific solutions without incurring long delivery delays. Service differentiation also manifests through comprehensive aftermarket packages, including on-site calibration, preventive maintenance contracts and spare parts optimization programs.
Collectively, these competitive dynamics underscore a market where technological integration, deep regulatory understanding and customer-centric service models define leadership. Stakeholders seeking to maintain or enhance their market positions must evaluate these strategic plays and consider partnerships or investments that align with evolving customer demands and compliance landscapes.
This comprehensive research report delivers an in-depth overview of the principal market players in the Stainless Steel Hygienic Diaphragm Pressure Gauge market, evaluating their market share, strategic initiatives, and competitive positioning to illuminate the factors shaping the competitive landscape.
- Emerson Electric Co.
- WIKA Alexander Wiegand SE & Co. KG
- Ashcroft Inc.
- Endress+Hauser AG
- VEGA Grieshaber KG
- ABB Ltd
- Yokogawa Electric Corporation
- IFM Electronic GmbH
- Dwyer Instruments, LLC
- OMEGA Engineering, Inc.
Strategic Playbook for Strengthening Competitive Advantage
To capitalize on emerging opportunities, industry leaders should prioritize the integration of smart connectivity features within hygienic diaphragm pressure gauges. Embedding real-time diagnostics and wireless communication capabilities will enable predictive maintenance and minimize unplanned downtime, delivering immediate value to process operators. Concurrently, strategic investments in advanced material science-such as next-generation stainless steel alloys with superior fatigue resistance-can broaden application scopes and create differentiation.
Supply chain resilience requires a reevaluation of sourcing strategies in light of recent tariff fluctuations. Establishing dual or multi-sourcing arrangements, together with selective localization of critical components, will buffer against policy-driven cost volatility and ensure consistent delivery performance. Collaboration with regional manufacturing partners can also facilitate faster customization, aligning product portfolios with local regulatory standards and customer preferences.
Moreover, cultivating deeper partnerships with regulatory bodies and industry consortia can streamline certification processes and amplify the credibility of new product introductions. Leaders should also expand service offerings to encompass holistic asset management packages, uniting instrumentation, calibration, spare parts and technical support under a single contractual umbrella. This consultative approach not only strengthens customer loyalty but also generates recurring revenue streams.
Finally, allocating resources toward comprehensive training programs will empower field teams and end users with the expertise needed to optimize gauge performance and maintain hygienic integrity. Through these targeted actions, organizations can fortify their competitive positioning and drive sustainable growth within the hygienic instrumentation market.
Robust Research Framework Underpinning the Analysis
A rigorous two-pronged research methodology formed the foundation of this analysis, combining extensive primary engagement with authoritative secondary sources. Primary research encompassed in-depth interviews with instrumentation engineers, procurement managers and regulatory specialists across key end-user industries. These conversations yielded nuanced insights into application challenges, decision-making criteria and evolving technical requirements for hygienic diaphragm pressure gauges.
Simultaneously, comprehensive secondary research involved a systematic review of industry publications, standards documentation and patent databases to validate technology trends and compliance considerations. Trade association reports, regulatory bulletins and quality guidelines provided a structured framework for understanding certification requirements across different regions. This desk-based analysis also examined corporate filings and public disclosures to map competitive strategies and identify recent product launches.
Data triangulation played a critical role in ensuring the robustness of conclusions. Insights from primary interviews were cross-verified with secondary findings to reconcile divergent perspectives and reinforce key observations. Analytical techniques included trend mapping, segmentation analysis and impact assessment of trade policies. The resulting data sets underpinned the segmentation, regional and competitive insights presented in this summary, offering stakeholders a defensible and transparent foundation for strategic planning.
Explore AI-driven insights for the Stainless Steel Hygienic Diaphragm Pressure Gauge market with ResearchAI on our online platform, providing deeper, data-backed market analysis.
Ask ResearchAI anything
World's First Innovative Al for Market Research
Synthesizing Insights to Chart Future Trajectories
As the demand for sanitary and reliable pressure measurement continues to accelerate, the stainless steel hygienic diaphragm gauge emerges as a pivotal instrument for modern process industries. Technological innovations in digital diagnostics, advanced materials and modular design are reshaping performance benchmarks, while regulatory imperatives ensure that hygiene and traceability remain non-negotiable attributes.
The ripple effects of US tariff policies underscore the importance of supply chain agility and localized production, compelling stakeholders to adopt flexible procurement strategies and resilient logistics frameworks. Segmentation analysis reveals that application-specific demands-from biopharmaceutical research to wastewater management-require tailored combinations of diaphragm materials, seal chemistries and connection types. Regional insights highlight divergent adoption curves, with growth driven by investment in food and beverage, pharmaceutical exports and water infrastructure across major global markets.
Industry leaders that embrace smart connectivity, deepen regulatory collaborations and invest in after-sales service models will capture the greatest value. By aligning product development with end-user priorities, companies can accelerate innovation cycles and secure stronger market positions. Ultimately, the fusion of hygienic design principles with data-driven process control establishes a compelling value proposition, charting a clear path for future growth and operational excellence within highly regulated environments.
This section provides a structured overview of the report, outlining key chapters and topics covered for easy reference in our Stainless Steel Hygienic Diaphragm Pressure Gauge market comprehensive research report.
- Preface
- Research Methodology
- Executive Summary
- Market Overview
- Market Dynamics
- Market Insights
- Cumulative Impact of United States Tariffs 2025
- Stainless Steel Hygienic Diaphragm Pressure Gauge Market, by Industry
- Stainless Steel Hygienic Diaphragm Pressure Gauge Market, by End Connection
- Stainless Steel Hygienic Diaphragm Pressure Gauge Market, by Pressure Range
- Stainless Steel Hygienic Diaphragm Pressure Gauge Market, by Mounting Type
- Stainless Steel Hygienic Diaphragm Pressure Gauge Market, by Seal Material
- Stainless Steel Hygienic Diaphragm Pressure Gauge Market, by Application
- Stainless Steel Hygienic Diaphragm Pressure Gauge Market, by Diaphragm Material
- Americas Stainless Steel Hygienic Diaphragm Pressure Gauge Market
- Europe, Middle East & Africa Stainless Steel Hygienic Diaphragm Pressure Gauge Market
- Asia-Pacific Stainless Steel Hygienic Diaphragm Pressure Gauge Market
- Competitive Landscape
- ResearchAI
- ResearchStatistics
- ResearchContacts
- ResearchArticles
- Appendix
- List of Figures [Total: 30]
- List of Tables [Total: 555 ]
Secure Your Comprehensive Industry Report Today
For a comprehensive exploration of these insights and a deeper dive into strategic implications, connect with Ketan Rohom, Associate Director of Sales and Marketing, to secure your copy of the full market research report. This report provides an in-depth breakdown of segmentation, tariff impacts, regional dynamics and competitive strategies, equipping you with the actionable intelligence needed to make informed decisions. Reach out today to gain early access to proprietary data, expert analyses and customized advisory support designed to guide your organization through the rapidly evolving landscape of hygienic pressure measurement. Don’t miss the opportunity to leverage this authoritative resource for strategic planning, product development and investment evaluation. Engage with Ketan Rohom to position your organization at the forefront of hygienic instrumentation advancements and secure a competitive edge
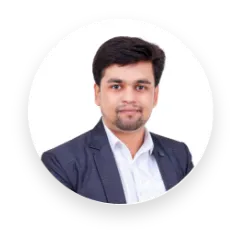
- When do I get the report?
- In what format does this report get delivered to me?
- How long has 360iResearch been around?
- What if I have a question about your reports?
- Can I share this report with my team?
- Can I use your research in my presentation?