Introduction to the Stainless Steel Wire for Welding Market
The stainless steel wire for welding sector plays a critical role in joining corrosion-resistant alloys across a broad range of industrial applications. From automotive assembly lines to high-precision aerospace fabrications, these specialized wires deliver the strength, ductility and chemical resilience required to meet rigorous performance standards. Recent years have seen sustained demand driven by infrastructure development, rising defense budgets and a resurgence in energy projects, prompting manufacturers to refine alloy compositions and enhance production efficiencies. As stakeholders seek lower total cost of ownership, alloy designers and welders alike are focusing on flux-cored solutions, novel coating techniques and automated welding systems to optimize deposition rates and reduce spatter. Moreover, tightening environmental regulations are accelerating the adoption of nickel- and tin-coated wires that minimize harmful emissions during welding. In this context, understanding the evolving competitive landscape, emerging technologies and regulatory shifts is essential for decision-makers aiming to maintain market share and capitalize on new growth pockets. This introduction lays the groundwork for an in-depth examination of key market forces, tariff implications and strategic imperatives shaping the stainless steel wire welding arena.
Transformative Shifts in the Welding Wire Landscape
In recent years, the stainless steel welding wire market has undergone transformative shifts driven by digitalization, advanced metallurgy and heightened sustainability mandates. Additive manufacturing techniques and real-time process monitoring are no longer experimental; they underpin production protocols that deliver consistent wire diameter and alloy uniformity. Simultaneously, flux-cored and continuous welded wire solutions have matured, enabling fabricators to fine-tune deposition rates, penetration profiles and spatter control across automated robotic welding cells. At the same time, electromagnetic interference mitigation wires are gaining traction in electrical and electronics industries, addressing signal-integrity challenges in consumer and industrial devices. Sustainability pressures are also reshaping material choices: manufacturers increasingly prioritize copper-coated and nickel-coated wires that facilitate cleaner weld pools, reduce post-weld cleaning and lower energy consumption. Beyond materials, advancements in artificial intelligence-driven quality inspection are redefining process control, enabling predictive maintenance and real-time defect detection. Together, these technological and operational shifts are expanding the value proposition of stainless steel welding wires, spurring competition among legacy suppliers and agile newcomers alike.
Cumulative Impact of United States Tariffs in 2025 on Market Dynamics
Effective January 2025, a new tariff regime targeting specific stainless steel wire imports has reverberated across supply chains, prompting steel mills and welding consumable producers to reassess sourcing strategies. The additional duties have elevated landed costs for imported flux-cored and coated wires by up to 15%, compelling end users to explore domestic manufacturers or nearshore alternatives. As a result, fabricators in critical infrastructure and automotive sectors have accelerated qualification of locally produced bare and flux-cored MIG wires, while select asset owners have invested in backward integration to secure alloy feedstock. Tariff-induced cost pressures have also catalyzed renegotiation of long-term supply contracts, with many buyers seeking index-linked pricing or volume discounts to offset higher duties. In parallel, some wire suppliers are leveraging tariff exclusions and antidumping measures to maintain competitive pricing for specialized products. Looking ahead, the cumulative impact of these trade measures is anticipated to foster greater regional self-sufficiency, encourage strategic alliances between mill and wire producers, and drive continued innovation in coating formulations designed to deliver cost-effective performance under constrained budgets.
Key Segmentation Insights Driving Market Differentiation
A nuanced segmentation framework reveals the diverse drivers and growth vectors within the welding wire market. By product type, the analysis encompasses Stainless Steel MIG Wire differentiated into bare wire and flux-cored wire, Stainless Steel Stick Electrodes further classified as basic electrodes and cellulosic electrodes, and Stainless Steel TIG Wire available in both bare and flux-cored variants. End-use industry segmentation captures the aerospace sector-spanning commercial aircraft and defense aircraft-alongside automotive applications in passenger vehicles and commercial vehicles, construction projects comprising residential construction and infrastructure construction, and the oil and gas domain which includes upstream and downstream operations. Application insights cover automotive components such as chassis parts and exhaust systems, bridge and highway construction activities including bridge repair and maintenance as well as new bridge initiatives, electrical and electronics markets addressing consumer electronics and industrial electronics, and industrial machinery applications in manufacturing equipment and machinery repair. Diameter range segmentation categorizes wire sizes below 0.8 mm, between 0.8 mm and 1.2 mm, and above 1.2 mm, while coating type highlights copper-coated, nickel-coated and tin-coated offerings. Finally, technological segmentation distinguishes continuous welded wire solutions from electromagnetic interference (EMI) wires, each tailored to specific process requirements and environmental constraints.
This comprehensive research report categorizes the Stainless Steel Wire for Welding market into clearly defined segments, providing a detailed analysis of emerging trends and precise revenue forecasts to support strategic decision-making.
- Product Type
- End-Use Industry
- Application
- Diameter Range
- Coating Type
- Technology
Key Regional Insights Highlighting Global Market Trends
Regional dynamics underscore the global breadth of the stainless steel wire market. The Americas region benefits from robust automotive and oil and gas investments, with manufacturers capitalizing on near-shoring to meet domestic content requirements. In the Europe, Middle East & Africa corridor, tight environmental regulations and infrastructure modernization programs are fueling demand for advanced coated and flux-cored wires, while geopolitical shifts in energy policy are reshaping project pipelines. Meanwhile, the Asia-Pacific region remains a powerhouse of sustained growth, led by China’s expansive construction agenda, India’s automotive expansion and Southeast Asia’s evolving industrial base. Local wire producers in Asia-Pacific are rapidly integrating digital quality controls and green-chemistry coatings to secure export markets, creating competitive pressure on global suppliers. These regional variances not only highlight diverse end-use demands but also underscore the importance of strategic footprint optimization and tailored product portfolios to serve local market conditions effectively.
This comprehensive research report examines key regions that drive the evolution of the Stainless Steel Wire for Welding market, offering deep insights into regional trends, growth factors, and industry developments that are influencing market performance.
- Americas
- Asia-Pacific
- Europe, Middle East & Africa
Key Company Insights Shaping Competitive Dynamics
Competitive dynamics in the welding wire arena are influenced by a mix of legacy conglomerates, specialized alloy makers and up-and-coming technology innovators. Major players such as Colfax Corporation, Elga AB, ESAB Group, Inc. and the Harris Products Group continue to leverage scale, integrated supply chains and broad product portfolios to serve large industrial accounts. Specialist producers including Hobart Brothers Company, Hyundai Welding Co., Ltd. and Luvata Group are driving innovation in coating formulations and automate process adaptability. At the same time, conglomerates like Illinois Tool Works Inc. and Lincoln Electric Holdings, Inc. are investing in digital welding platforms and joint ventures to enhance process control and service differentiation. Nippon Steel Corporation, Kobe Steel, Ltd. (KOBELCO) and Sandvik Materials Technology are deepening alloy R&D to deliver next-generation nickel-rich and low-spatter wires. Meanwhile, niche players Select-Arc, Inc., Special Metals Corporation, Novametal SA, Voestalpine Bohler Welding and Washington Alloy Company are cultivating strong footholds in targeted end-use verticals, from high-precision aerospace welds to demanding offshore oil and gas applications. Collectively, these companies are shaping a competitive ecosystem defined by product innovation, regional agility and service excellence.
This comprehensive research report delivers an in-depth overview of the principal market players in the Stainless Steel Wire for Welding market, evaluating their market share, strategic initiatives, and competitive positioning to illuminate the factors shaping the competitive landscape.
- Colfax Corporation (parent to ESAB)
- Elga AB
- ESAB Group, Inc.
- Harris Products Group (a Lincoln Electric company)
- Hobart Brothers Company
- Hyundai Welding Co., Ltd.
- Illinois Tool Works Inc. (ITW)
- Kobe Steel, Ltd. (KOBELCO)
- Lincoln Electric Holdings, Inc.
- Luvata Group
- Nippon Steel Corporation
- Novametal SA
- Sandvik Materials Technology
- Select-Arc, Inc.
- Special Metals Corporation
- Voestalpine Bohler Welding
- Washington Alloy Company
Actionable Recommendations for Industry Leaders to Accelerate Growth
To thrive amid evolving market conditions, industry leaders should consider a multi-pronged strategy. Invest in product innovation by expanding flux-cored and EMI wire portfolios, emphasizing low-spatter, high-deposition formulas that reduce total welding costs. Diversify supply chains through qualification of domestic and near-shore steel mills to mitigate tariff impacts and logistical uncertainties. Form strategic alliances or joint ventures with equipment OEMs to integrate wires with automated welding platforms, delivering turnkey solutions that enhance end-user value. Amplify focus on sustainability by developing coatings that lower emissions and meet stricter environmental standards, while promoting circularity through scrap-recovery programs. Leverage digital quality inspection and traceability systems to provide real-time weld performance data, enabling predictive maintenance and defect minimization. Finally, deepen engagement with key end-use sectors by tailoring technical support and training services for aerospace, automotive and construction customers, positioning wire offerings as integral components of broader fabrication solutions.
Explore AI-driven insights for the Stainless Steel Wire for Welding market with ResearchAI on our online platform, providing deeper, data-backed market analysis.
Ask ResearchAI anything
World's First Innovative Al for Market Research
Conclusion: Positioning for Sustained Success in Welding Wire Markets
The stainless steel welding wire market is at a pivotal inflection point, shaped by technological breakthroughs, shifting trade policies and regionally nuanced growth drivers. Success will hinge on the ability to innovate alloy compositions, streamline global supply chains and deliver integrated welding solutions that align with stringent performance and sustainability objectives. Companies that proactively address tariff challenges, leverage regional strengths and forge collaborative partnerships across the value chain will be best positioned to capture emerging opportunities. By embracing digital transformation and reinforcing technical support capabilities, wire producers can elevate their competitive advantage and drive long-term value for both industrial fabricators and end-users. This conclusion underscores the importance of strategic agility and continuous investment in R&D to navigate an increasingly complex market environment.
This section provides a structured overview of the report, outlining key chapters and topics covered for easy reference in our Stainless Steel Wire for Welding market comprehensive research report.
- Preface
- Research Methodology
- Executive Summary
- Market Overview
- Market Dynamics
- Market Insights
- Cumulative Impact of United States Tariffs 2025
- Stainless Steel Wire for Welding Market, by Product Type
- Stainless Steel Wire for Welding Market, by End-Use Industry
- Stainless Steel Wire for Welding Market, by Application
- Stainless Steel Wire for Welding Market, by Diameter Range
- Stainless Steel Wire for Welding Market, by Coating Type
- Stainless Steel Wire for Welding Market, by Technology
- Americas Stainless Steel Wire for Welding Market
- Asia-Pacific Stainless Steel Wire for Welding Market
- Europe, Middle East & Africa Stainless Steel Wire for Welding Market
- Competitive Landscape
- ResearchAI
- ResearchStatistics
- ResearchContacts
- ResearchArticles
- Appendix
- List of Figures [Total: 28]
- List of Tables [Total: 766 ]
Contact Ketan Rohom to Secure Your Market Research Report
To obtain the full, detailed market research report and unlock comprehensive insights on stainless steel wire for welding, please contact Ketan Rohom, Associate Director of Sales & Marketing. Reach out directly to secure your copy and support your strategic decision-making.
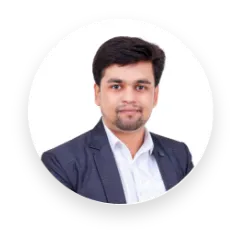
- When do I get the report?
- In what format does this report get delivered to me?
- How long has 360iResearch been around?
- What if I have a question about your reports?
- Can I share this report with my team?
- Can I use your research in my presentation?