Introduction to the Steel Cryogenic Gate Valve Market
The steel cryogenic gate valve market has emerged as a critical component in industries requiring precise flow control at extremely low temperatures. These valves are engineered to maintain structural integrity and operational reliability in environments that can plunge below -150°F, making them indispensable for sectors such as liquefied natural gas, petrochemicals, and industrial gas processing. As global energy demands evolve and supply chains expand, the relevance of high-performance cryogenic gate valves intensifies. Their ability to ensure leak-tight sealing, reduce maintenance downtime, and withstand thermal cycling positions them at the forefront of downstream infrastructure deployments.
This executive summary delves into the key drivers reshaping this market, analyzes the implications of impending United States tariffs, and highlights segmentation, regional, and competitive insights. The goal is to equip industry leaders with a comprehensive understanding of current dynamics and strategic considerations. By synthesizing emerging trends, regulatory shifts, and best practices, decision-makers can prioritize investments, refine procurement strategies, and collaborate more effectively with valve manufacturers and suppliers. In an era defined by technological innovation and tightening regulations, this analysis provides the clarity needed to navigate complex market conditions and capitalize on growth opportunities.
Transformative Shifts in the Steel Cryogenic Gate Valve Landscape
Over the past decade, technological innovation has redefined performance benchmarks for cryogenic gate valves. Advances in material metallurgy-such as optimized duplex steel alloys and enhanced stainless steel formulations-have improved resistance to embrittlement and extended service life under repeated thermal cycling. Furthermore, digital integration through sensor-embedded actuators now allows real-time monitoring of valve position, temperature differentials, and wear indicators. This convergence of metallurgy and automation has shifted the competitive landscape toward suppliers that can deliver fully integrated valve systems rather than standalone mechanical components.
Simultaneously, sustainability considerations have prompted a pivot toward low-temperature carbon capture and storage applications. Cryogenic gate valves designed for hydrogen liquefaction and clean fuel distribution illustrate how market demands are evolving beyond traditional oil and gas sectors. Moreover, stricter safety regulations in petrochemical and industrial gas operations are driving increased adoption of safety-certified valve solutions. Consequently, suppliers must continuously innovate to comply with international standards such as ISO 21012 and TA-Luft while maintaining cost-effectiveness.
Cumulative Impact of United States Tariffs 2025
In 2025, newly announced United States tariffs on imported steel products are poised to reverberate through the cryogenic gate valve value chain. Tariffs targeting finished valves and critical raw materials could drive up input costs, prompting OEMs and EPC contractors to reevaluate sourcing strategies. For instance, reliance on imported carbon steel or alloy steel components could translate into a notable increase in landed costs, compelling end users to negotiate long-term supply agreements or pursue domestic manufacturing partnerships.
Moreover, ancillary industries such as LNG terminals and petrochemical plants may experience project delays as procurement teams assess the total cost impact. Some operators might accelerate capital expenditure to secure existing inventory at pre-tariff pricing, while others could defer expansion plans until trade policy clarity emerges. Ultimately, the cumulative effect of these tariffs will depend on the duration of trade measures, potential exemptions for specialized cryogenic steels, and reciprocal responses from key trading partners. Strategic collaboration among valve manufacturers, raw material suppliers, and downstream stakeholders will be essential to mitigate cost pressures and maintain project timelines.
Key Segmentation Insights
Material type plays a pivotal role in valve performance at cryogenic temperatures. Alloy steel variants are prized for their high strength-to-weight ratio, enabling compact actuator designs for applications needing rapid response. Conversely, carbon steel remains the most economical choice when operating temperatures do not exceed the moderate cryogenic range. Duplex steel strikes a balance by offering superior corrosion resistance in harsh chemical and marine environments, while stainless steel grades deliver unmatched longevity for ultra-low-temperature operations below -150°F.
Valve dimensions also shape procurement decisions. Valves up to two inches in diameter typically serve instrumentation and pilot lines, benefitting from fast-acting designs and minimal thermal lag. Sizes ranging from two to four inches accommodate moderate flow control requirements in processing units, whereas four- to eight-inch valves are favored in bulk transfer systems within LNG terminals. Above eight inches, valves demand specialized fabrication techniques to ensure uniform wall thickness and prevent thermal gradients that could induce material fractures.
End-user industries dictate specification stringency. The chemical and petrochemical sector often requires valves with specialized coatings to withstand aggressive media, while food and beverage operations prioritize hygienic design and ease of maintenance. In LNG and LPG infrastructures, valves must adhere to rigorous insulation and sealing standards to minimize boil-off gas. Marine applications demand resistance to saltwater corrosion and shock loads, and oil and gas facilities emphasize compliance with API and NACE certifications. Pharmaceutical plants, meanwhile, leverage cryogenic valves for controlled freezing processes and cryo-preservation, where contamination control and traceability are paramount.
Different applications further refine valve selection. Flow control architectures integrate precision gate designs with positioners and feedback loops to maintain stable pressure differentials. Isolation functions rely on resilient seating mechanisms to achieve absolute shutoff during maintenance or emergency scenarios. Safety applications incorporate fail-safe actuators and redundant monitoring to guarantee rapid closure in overpressure events, safeguarding personnel and equipment.
Operating temperature thresholds impose critical material and design constraints. Valves rated up to -100°F can utilize standard low-temperature steel formulations, while those required to operate between -100°F and -150°F often incorporate specialized cryogenic alloys to prevent ductile-to-brittle transitions. Below -150°F, only the most advanced stainless steel or nickel-based alloys maintain structural integrity and toughness, ensuring reliable performance under extreme conditions.
This comprehensive research report categorizes the Steel Cryogenic Gate Valve market into clearly defined segments, providing a detailed analysis of emerging trends and precise revenue forecasts to support strategic decision-making.
- Material Type
- Product Size
- End-User Industry
- Applications
- Operating Temperature
Key Regional Insights
Regional dynamics exert a profound influence on market opportunities and supply chain configurations. In the Americas, expanding LNG export capacities along both U.S. Gulf Coast and Canadian coasts stimulate demand for cryogenic gate valves with high throughput and low leakage rates. Meanwhile, environmental regulations in the United States and Canada incentivize investments in gas capture and hydrogen liquefaction, further diversifying end-user requirements.
Europe, the Middle East & Africa presents a fragmented landscape. Western Europe’s mature petrochemical infrastructures seek valve retrofits to meet tightening emissions standards, whereas the Middle East’s upstream oil and gas expansion demands robust, large-bore valves capable of enduring desert conditions. Africa’s burgeoning gas-to-power initiatives and nascent LNG projects offer greenfield opportunities, albeit with logistical challenges related to remote deployment and local fabrication capabilities.
In Asia-Pacific, the rapid industrialization of Southeast Asia and the strategic drive toward energy security in China and India accelerate cryogenic valve adoption. Major LNG import terminals in Japan and South Korea continue to retrofit aging assets, while emerging markets in Australia and Southeast Asia emphasize modular plant designs, necessitating valves that are both globally certified and locally serviceable. Tariff fluctuations and currency volatility in the region underscore the importance of flexible supply agreements and dual sourcing strategies.
This comprehensive research report examines key regions that drive the evolution of the Steel Cryogenic Gate Valve market, offering deep insights into regional trends, growth factors, and industry developments that are influencing market performance.
- Americas
- Asia-Pacific
- Europe, Middle East & Africa
Key Companies Insights
The competitive landscape features a mix of global conglomerates and specialized valve manufacturers. Acme Cryogenics Inc. and Bestobell Valves deliver custom-engineered solutions for upstream and midstream applications, leveraging decades of cryogenic expertise. Control Seal NL and Crane Co. integrate advanced actuator technologies to optimize valve responsiveness, while Cryocomp Corp. focuses on compact, lightweight designs tailored to tight installation footprints. Edmund Valve Company and Emerson Electric Co. offer modular valve packages with seamless integration into distributed control systems.
Everest Valve Co., Ltd. and Flowell Corporation cater to Asia-Pacific markets with localized production and service networks, whereas Flowserve Corporation and KSB Group provide end-to-end supply chain management across multiple industries. Herose GmbH and IMI plc emphasize compliance with European pressure equipment directives and environmental standards. Regional specialists such as Kavaata Valves and Valmatic Inc. address niche requirements in food, beverage, and pharmaceutical sectors. Meanwhile, KITZ Corporation and Multivalve Flow Solutions Ltd. support flexible manufacturing for emerging markets. Leading conglomerates such as Pentair plc, Samson AG, and Velan Inc. combine extensive product portfolios with global aftermarket services. Sealexcel India Private Limited and TVI Valves Belgium excel in customized valve trims for corrosive applications, while Sure Flow Equipment Inc. and Valvias S.L. innovate in actuator and positioner technologies.
This comprehensive research report delivers an in-depth overview of the principal market players in the Steel Cryogenic Gate Valve market, evaluating their market share, strategic initiatives, and competitive positioning to illuminate the factors shaping the competitive landscape.
- Acme Cryogenics Inc.
- Bestobell Valves
- Control Seal NL
- Crane Co.
- Cryocomp Corp.
- Edmund Valve Company
- Emerson Electric Co.
- Everest Valve Co., Ltd.
- Flowell Corporation
- Flowserve Corporation
- Herose GmbH
- IMI plc
- Kavaata Valves
- KITZ Corporation
- KSB Group
- Meca-Inox SAS
- Multivalve Flow Solutions Ltd.
- Pentair plc
- Samson AG
- Sealexcel India Private Limited
- Sure Flow Equipment Inc.
- TVI Valves Belgium
- Valmatic Inc.
- Valvias S.L.
- Velan Inc.
Actionable Recommendations for Industry Leaders
To thrive amid evolving regulations and competitive pressures, industry leaders should adopt a multi-pronged strategy. First, deepen collaborative R&D partnerships with material science institutes to develop next-generation alloys that extend temperature thresholds and reduce reliance on tariff-impacted imports. Second, invest in digital twin and predictive maintenance platforms that leverage IoT sensors to forecast valve performance, reducing unplanned downtime and optimizing lifecycle costs.
Third, negotiate framework agreements with multiple raw material suppliers across geographies to buffer against trade policy volatility. Fourth, expand service networks in emerging markets by establishing regional repair hubs and certified training programs, ensuring rapid response and local compliance. Fifth, integrate sustainability metrics into product roadmaps, such as lifecycle carbon footprint assessments and recyclable component designs, to align with corporate decarbonization targets.
Finally, leverage modular manufacturing techniques-such as additive manufacturing for bespoke valve components-to accelerate lead times and enhance customization capabilities. This flexibility will be critical as end users demand more application-specific solutions, from ultra-high-purity pharmaceutical valves to heavy-duty marine isolation systems.
Explore AI-driven insights for the Steel Cryogenic Gate Valve market with ResearchAI on our online platform, providing deeper, data-backed market analysis.
Ask ResearchAI anything
World's First Innovative Al for Market Research
Conclusion
The steel cryogenic gate valve market stands at the nexus of technological innovation, regulatory complexity, and shifting energy paradigms. As operators expand LNG terminals, retrofit petrochemical plants, and explore hydrogen infrastructures, the demand for valves that combine low-temperature resilience, precision control, and cost-efficiency will intensify. Manufacturers that proactively address trade policy risks, accelerate digitalization efforts, and deepen their material science expertise are positioned to lead the next wave of growth.
Moreover, the fragmentation of regional requirements underscores the importance of agile supply chains and localized support networks. By balancing global best practices with tailored regional strategies, companies can capture emerging opportunities across the Americas, Europe, Middle East & Africa, and Asia-Pacific. Continued collaboration among OEMs, EPC contractors, and end users will drive innovation in cryogenic valve design and accelerate the deployment of safe, reliable, and sustainable low-temperature systems.
This section provides a structured overview of the report, outlining key chapters and topics covered for easy reference in our Steel Cryogenic Gate Valve market comprehensive research report.
- Preface
- Research Methodology
- Executive Summary
- Market Overview
- Market Dynamics
- Market Insights
- Cumulative Impact of United States Tariffs 2025
- Steel Cryogenic Gate Valve Market, by Material Type
- Steel Cryogenic Gate Valve Market, by Product Size
- Steel Cryogenic Gate Valve Market, by End-User Industry
- Steel Cryogenic Gate Valve Market, by Applications
- Steel Cryogenic Gate Valve Market, by Operating Temperature
- Americas Steel Cryogenic Gate Valve Market
- Asia-Pacific Steel Cryogenic Gate Valve Market
- Europe, Middle East & Africa Steel Cryogenic Gate Valve Market
- Competitive Landscape
- ResearchAI
- ResearchStatistics
- ResearchContacts
- ResearchArticles
- Appendix
- List of Figures [Total: 26]
- List of Tables [Total: 241 ]
Call-To-Action: Connect with Ketan Rohom for the Full Market Research Report
For a deeper analysis of market dynamics, tariff implications, and strategic insights customized to your organization’s objectives, reach out to Ketan Rohom, Associate Director, Sales & Marketing. Secure your copy of the comprehensive market research report today to inform your capital planning, procurement decisions, and innovation roadmap.
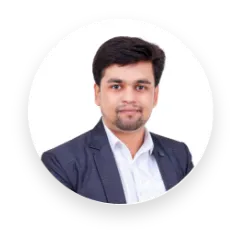
- When do I get the report?
- In what format does this report get delivered to me?
- How long has 360iResearch been around?
- What if I have a question about your reports?
- Can I share this report with my team?
- Can I use your research in my presentation?