Exploring the Evolving Role of Advanced Steel Structure Shot Blasting Machines in Modern Manufacturing Environments Shaping Operational Efficiency
Steel structure shot blasting machines represent a cornerstone in contemporary surface preparation, delivering precision cleaning and finishing that underpin downstream fabrication and coating processes. These robust systems propel abrasive media at high velocity to remove rust, scale, paint, and other surface contaminants, thereby ensuring optimal adhesion and material integrity in applications ranging from structural steel beams to large-scale industrial components. As manufacturers across aerospace, automotive, shipbuilding, and infrastructure sectors demand ever-higher levels of quality and throughput, the role of shot blasting equipment has become increasingly strategic in maintaining operational efficiency and regulatory compliance.
In addition to traditional abrasive mechanics, modern shot blasting solutions integrate advanced controls, customized media selection, and modular designs to align with diverse production environments. Consequently, leaders in fabrication and maintenance are reevaluating legacy equipment in favor of systems that not only deliver reliable cleaning performance but also reduce energy consumption, minimize media waste, and support real-time monitoring. By understanding the fundamental principles of shot blasting technology and recognizing its critical position within the broader manufacturing workflow, decision-makers can better evaluate emerging offerings and future-proof their surface treatment capabilities.
Unveiling Key Technological And Regulatory Shifts Redefining The Global Steel Structure Shot Blasting Machine Landscape In Recent Years
Over the past few years, the steel structure shot blasting machine landscape has witnessed transformative shifts driven by converging technological, environmental, and economic forces. First, the adoption of digital machine controls and Industry 4.0 connectivity has enabled remote diagnostics, predictive maintenance, and process optimization that were once the exclusive domain of high-end automotive and aerospace applications. Machine builders are embedding sensors to capture real-time abrasive velocity, media degradation, and component wear, allowing operators to reduce downtime and extend equipment lifecycles without sacrificing throughput.
Simultaneously, sustainability imperatives and tightening environmental regulations have compelled manufacturers to embrace low-dust enclosures, closed-loop media recycling, and energy-efficient power systems. This trend has been reinforced by global commitments to reduce carbon footprints, incentivizing investment in pneumatic and hydraulic drives that balance force output with reduced electricity consumption. Moreover, the integration of advanced abrasive materials-such as engineered steel grit with controlled angularity or spherical shot grades-has elevated cleaning precision while lowering media attrition rates, further aligning with circular economy goals.
As supply chain resilience becomes a competitive differentiator, companies are also reevaluating equipment sourcing strategies. Localized production partnerships and modular machine architectures are gaining traction, enabling rapid scalability and customization without dependence on lengthy import cycles. In this context, leading equipment suppliers leverage digital twins and virtual commissioning to validate process parameters before physical installation, ensuring seamless integration and accelerated time-to-value.
Analyzing The Compounding Effects Of 2025 United States Steel Import Tariffs On The Dynamics And Cost Structures Of Shot Blasting Machine Suppliers
The continuation of United States steel import tariffs into 2025 has generated significant ripple effects across the shot blasting machine ecosystem. Initially introduced under Section 232 to protect domestic steel producers, these duties have elevated raw material prices for carbon steel components that form the core of machine frames, impellers, and wear parts. As a result, equipment manufacturers face heightened production costs, which cascade through to end users in the form of elevated capital expenditure and maintenance budgets.
In response, machine suppliers have pursued two complementary strategies. On one hand, several manufacturers have reshored critical fabrication processes to regional facilities in North America, thereby mitigating tariff exposure and shortening lead times. On the other hand, some suppliers are innovating with hybrid material approaches, incorporating high-strength alloys and composite reinforcements to achieve comparable performance while reducing steel volume. Both paths demand rigorous quality validation and strategic capital allocation but underscore a clear imperative: controlling steel content and leveraging local supply chains enhances competitiveness in a tariff-impacted market.
Moreover, the tariff landscape has indirectly influenced end-user procurement practices. Fabrication and maintenance managers increasingly factor in total cost of ownership rather than initial purchase price alone, taking into account media consumption rates, energy efficiency, and lifecycle warranties. Consequently, vendors that can substantiate long-term value through extended service agreements, performance guarantees, and data-driven reliability insights are better positioned to secure orders despite the elevated baseline costs associated with steel content tariffs.
Illuminating Crucial Market Segmentation Dimensions Revealing Diverse Machine Configurations Automation Preferences And End User Demands
The market for steel structure shot blasting machines is dissected through multiple segmentation lenses, each shedding light on how specialized customer demands shape equipment design and service offerings. Based on machine type, analysis spans belt type continuous conveyors, hook type systems for suspended workpieces, hopper type enclosures for batch processing, and table type turntables for uniform exposure. The interplay between production volume, part geometry, and floor space availability informs the optimal configuration selection, prompting suppliers to offer modular options that can transition between these formats over a machine’s lifecycle.
Another dimension explores automation level, differentiated into fully automated solutions that integrate robotics and programmable logic control, semi-automated machinery offering manual load-and-unload with automated blasting cycles, and manual systems where operators oversee the entire process. This segmentation underscores the spectrum of capital investment, workforce skill requirements, and throughput expectations, guiding stakeholders in aligning technology adoption with operational maturity and labor availability.
When examining abrasive media, the market is examined across slag, steel grit, and steel shot. Within steel grit, distinctions emerge between angular grit-preferred for aggressive surface profiling-and spherical grit-valued for high finish consistency. Steel shot itself bifurcates into cast steel shot, which balances durability with cost-effectiveness, and cut wire shot, renowned for its recyclability and uniform particle shape. This granular breakdown illustrates how media selection directly impacts cleaning efficacy, surface roughness targets, and machine wear rates.
End user industries-spanning aerospace, automotive, construction, railway, and shipbuilding-further refine the competitive landscape by imposing unique surface treatment specifications, cycle time constraints, and regulatory compliance requirements. Finally, power source segmentation explores electric drive systems for precise speed control, hydraulic drives for high-torque applications, and pneumatic configurations for lightweight, portable solutions. Collectively, these segmentation insights enable stakeholders to navigate technology trade-offs, cost considerations, and performance benchmarks across diverse operational scenarios.
This comprehensive research report categorizes the Steel Structure Shot Blasting Machines market into clearly defined segments, providing a detailed analysis of emerging trends and precise revenue forecasts to support strategic decision-making.
- Machine Type
- Automation Level
- Abrasive Media
- End User Industry
- Power Source
Exploring Regional Variations And Growth Trajectories Shaping The Adoption Of Steel Structure Shot Blasting Machines Across Key Global Territories
Regional dynamics play a pivotal role in shaping demand patterns and technological adoption for steel structure shot blasting machines. In the Americas, the revitalization of infrastructure programs and the refurbishment of aging industrial assets drive a steady appetite for robust, high-capacity systems. Fabricators and maintenance shops in this region emphasize quick change-over capabilities, localized after-sales support, and compliance with environmental regulations that mandate dust capture and media recycling.
Meanwhile, Europe, Middle East & Africa present a multifaceted environment where regulatory scrutiny on surface preparation quality and emissions standards is especially stringent. Enterprises in Western Europe often adopt advanced closed-loop media handling and remote monitoring to satisfy both productivity and sustainability mandates, whereas emerging markets in the Middle East and Africa prioritize modular, cost-effective solutions that can withstand harsh climatic conditions.
Across Asia-Pacific, rapid expansion in shipbuilding yards, railway electrification initiatives, and automotive manufacturing hubs underpins vigorous investments in both standardized and custom shot blasting installations. Stakeholders in this region are keenly focused on scalable automation and digital connectivity features, seeking to align with broader smart factory goals and drive continuous process improvement through performance analytics and real-time diagnostics.
This comprehensive research report examines key regions that drive the evolution of the Steel Structure Shot Blasting Machines market, offering deep insights into regional trends, growth factors, and industry developments that are influencing market performance.
- Americas
- Europe, Middle East & Africa
- Asia-Pacific
Highlighting Leading Innovators And Strategic Players Driving Competitive Advances In Steel Structure Shot Blasting Technologies Around The World
A competitive ecosystem of machinery manufacturers, specialized component suppliers, and automation integrators underpins the evolution of steel structure shot blasting technologies. Leading OEMs have differentiated themselves through vertical integration of critical sub-assemblies, investment in proprietary media recycling systems, and strategic partnerships with robotics and controls vendors. These companies prioritize research programs that span material science, wear alloy formulation, and machine learning for adaptive process control.
In parallel, niche players focusing on aftermarket services-such as wear part refurbishment, on-site machine audits, and operator training programs-have gained traction by offering comprehensive lifecycle solutions. By combining rapid spare part delivery networks with data-driven maintenance scheduling, these service-oriented organizations help end users maximize uptime and optimize maintenance budgets.
Furthermore, several emerging disruptors are leveraging additive manufacturing to produce complex impeller geometries and customized nozzle arrays, unlocking performance improvements and weight reductions that traditional casting methods cannot achieve. Through these strategic approaches, the competitive landscape continues to balance the strengths of established brands with the innovative potential of agile technology providers.
This comprehensive research report delivers an in-depth overview of the principal market players in the Steel Structure Shot Blasting Machines market, evaluating their market share, strategic initiatives, and competitive positioning to illuminate the factors shaping the competitive landscape.
- Norican Group A/S
- Walther Trowal GmbH
- Metalltechnik Shot Blasting Machinery Limited
- Empire Abrasive Equipment Company
- Blastman International Oy
- BlastOne International Pty Ltd
- Clemco Industries Corp.
- Curotec Inc.
- Daljit Industries
- Hi-Tech Engineers Private Limited
Strategic Actionable Recommendations For Industry Leaders To Capitalize On Emerging Opportunities And Mitigate Challenges In Shot Blasting Machine Operations
To thrive in the evolving shot blasting machine market, industry leaders should prioritize investments in modular automation platforms that can seamlessly transition between belt, hook, hopper, and table configurations. By adopting flexible architectures early, manufacturers can respond swiftly to shifting production demands without incurring the costs and delays associated with bespoke system redesigns.
Simultaneously, organizations must broaden their abrasive media portfolios to include a spectrum of slag, steel grit, and steel shot options, enabling precise matching of media characteristics to surface finish targets and throughput requirements. Engaging with media specialists to develop custom blends and exploring hybrid media formulations can yield performance gains and material cost savings.
Supply chain resilience emerges as another critical focus area. Leaders can strengthen competitive positioning by forging partnerships with regional steel fabricators, insulating themselves from tariff uncertainties and leveraging just-in-time delivery models. Concurrently, investing in energy-efficient electric drives and exploring pneumatic-electric hybrid power systems will not only reduce operational costs but also align with tightening environmental directives.
Finally, forging strategic alliances with controls and data analytics providers will empower manufacturers to harness real-time process data for predictive maintenance and quality control. By embedding sensors and analytics platforms into new machine installations, stakeholders can transform surface preparation from a manual operational function into a data-driven capability that delivers measurable ROI.
Comprehensive Research Methodology Combining Primary Interviews Data Triangulation And Rigorous Analytical Frameworks Ensuring Integrity And Relevance
The research underpinning this analysis employs a structured methodology integrating both primary and secondary data sources to ensure robust, unbiased insights. Primary research involved in-depth interviews with industry executives, equipment engineers, and end users across key segments such as aerospace, automotive, and infrastructure maintenance. These conversations provided qualitative perspectives on technology adoption drivers, cost pressures, and service requirements.
Secondary research comprised a systematic review of technical whitepapers, regulatory publications, and patent filings to contextualize emerging innovations in digital controls, abrasive materials, and media recycling technologies. Additionally, proprietary databases were leveraged to track historical equipment deployment patterns and to identify leading suppliers based on revenue, geographic footprint, and technological differentiation.
Data triangulation was achieved by cross-referencing primary feedback with secondary findings, validating hypotheses through iterative consultation with an advisory panel of subject-matter experts. Rigorous analytical frameworks-encompassing SWOT analysis, value chain assessment, and competitive benchmarking-ensured that conclusions are both actionable and grounded in empirical evidence. Throughout the process, quality checks were implemented to maintain consistency, accuracy, and relevance to stakeholders.
Explore AI-driven insights for the Steel Structure Shot Blasting Machines market with ResearchAI on our online platform, providing deeper, data-backed market analysis.
Ask ResearchAI anything
World's First Innovative Al for Market Research
Concluding Perspectives Highlighting Key Takeaways And The Future Outlook For Steel Structure Shot Blasting Machine Innovations And Market Dynamics
In summary, the steel structure shot blasting equipment domain is experiencing a convergence of technological innovation, regulatory scrutiny, and macroeconomic pressures that collectively redefine competitive advantage. Digital integration and Industry 4.0-enabled controls are transitioning surface preparation from a reactive maintenance function to a predictive, analytics-driven operation. Meanwhile, environmental imperatives are accelerating adoption of closed-loop systems and low-dust enclosures, reinforcing a commitment to sustainability.
The persistence of United States steel import tariffs continues to shape sourcing strategies and cost structures, prompting regional manufacturing realignments and material substitution efforts. Detailed segmentation analysis reveals that machine type, automation level, abrasive media selection, end user requirements, and power source preferences all play an integral role in equipment specification and performance outcomes. Concurrently, regional dynamics in the Americas, EMEA, and Asia-Pacific underscore the importance of localized support networks and regulatory compliance.
Against this backdrop, industry leaders must adopt flexible, modular architectures, diversify media options, and fortify supply chains through strategic partnerships. With a clear understanding of competitive positioning and a data-driven approach to maintenance and quality assurance, stakeholders can navigate complexity and capitalize on emerging growth avenues in surface preparation.
This section provides a structured overview of the report, outlining key chapters and topics covered for easy reference in our Steel Structure Shot Blasting Machines market comprehensive research report.
- Preface
- Research Methodology
- Executive Summary
- Market Overview
- Market Dynamics
- Market Insights
- Cumulative Impact of United States Tariffs 2025
- Steel Structure Shot Blasting Machines Market, by Machine Type
- Steel Structure Shot Blasting Machines Market, by Automation Level
- Steel Structure Shot Blasting Machines Market, by Abrasive Media
- Steel Structure Shot Blasting Machines Market, by End User Industry
- Steel Structure Shot Blasting Machines Market, by Power Source
- Americas Steel Structure Shot Blasting Machines Market
- Europe, Middle East & Africa Steel Structure Shot Blasting Machines Market
- Asia-Pacific Steel Structure Shot Blasting Machines Market
- Competitive Landscape
- ResearchAI
- ResearchStatistics
- ResearchContacts
- ResearchArticles
- Appendix
- List of Figures [Total: 28]
- List of Tables [Total: 650 ]
Take The Next Step In Gaining Competitive Advantage By Securing Your Customized Steel Structure Shot Blasting Machine Market Research Report Today
To explore the unparalleled insights and strategic intelligence contained within this comprehensive market research report, engage directly with Ketan Rohom, the Associate Director of Sales & Marketing at 360iResearch. He will guide you in customizing the analysis to address your organization’s unique operational challenges, technological priorities, and investment objectives. By initiating a conversation with Ketan, you can tailor solution packages, secure exclusive add-ons such as in-depth executive briefings or bespoke data workshops, and expedite your access to critical findings that will inform capital allocation, procurement planning, and competitive positioning. Prioritize your decision-making agenda by partnering with an expert who understands the nuanced demands of the shot blasting equipment landscape and can ensure that your team capitalizes on emerging opportunities while mitigating industry-specific risks. Reach out to Ketan today to unlock a strategic perspective that empowers your enterprise to drive innovation, optimize surface preparation processes, and elevate overall productivity with confidence.
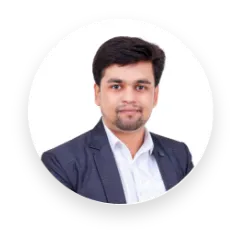
- When do I get the report?
- In what format does this report get delivered to me?
- How long has 360iResearch been around?
- What if I have a question about your reports?
- Can I share this report with my team?
- Can I use your research in my presentation?