Surface Finishing and Polishing Machines: Setting the Stage for Industrial Excellence
Surface finishing and polishing machinery stands at the heart of modern manufacturing, transforming raw components into precision parts that meet the highest standards of durability, appearance, and performance. As industries from automotive to aerospace demand ever-greater consistency and quality in surface treatments, these machines play an indispensable role in ensuring that complex geometries and sensitive materials emerge with flawless finishes. The integration of advanced abrasives, automation, and real-time monitoring has elevated surface finishing from a manual art to a sophisticated engineering discipline that underpins the reliability of countless products.
Against the backdrop of technological innovation and increasing regulatory scrutiny, manufacturers of surface finishing and polishing equipment are tasked with balancing throughput, energy efficiency, and environmental compliance. Market leaders are investing heavily in next-generation systems that reduce cycle times while minimizing waste and energy consumption. At the same time, end users expect seamless integration with digital platforms that deliver actionable insights into process optimization and predictive maintenance. In this evolving landscape, understanding the drivers, constraints, and competitive dynamics is essential for stakeholders at every level.
Emerging Forces Redefining Surface Treatment Technologies
The industry is undergoing transformative shifts driven by converging technological, environmental, and market forces. Smart factory initiatives now demand that finishing equipment interface seamlessly with plant-wide IoT frameworks, enabling machine-to-machine communication and data-driven decision making. Artificial intelligence algorithms analyze sensor data to detect tool wear, predict failures, and optimize abrasive selection in real time, thereby reducing downtime and enhancing overall equipment effectiveness.
Simultaneously, sustainability imperatives have taken center stage in boardrooms and regulatory bodies alike. Manufacturers are designing machines that consume less power, recycle abrasive media, and capture particulate emissions through advanced filtration systems. This eco-conscious mindset extends across the supply chain, prompting equipment suppliers to explore circular business models that refurbish and remanufacture critical components.
Market demand for miniaturized electronics and medical implants has added further complexity, as finishing processes must adapt to micro-scale tolerances and biocompatible surface textures. In aerospace, the shift toward lightweight composite airframes challenges conventional grinding and polishing methodologies, catalyzing the development of hybrid abrasive technologies. These convergent trends are reshaping the competitive landscape and setting new benchmarks for performance and sustainability.
United States Tariffs 2025: Navigating the New Trade Landscape
The introduction of new tariffs by the United States in 2025 has created significant ripples across global trade patterns for surface finishing machinery. Additional duties on imports from key manufacturing hubs have elevated landed costs, compelling OEMs to reevaluate sourcing strategies. Companies reliant on cost-competitive producers in Asia and Europe are now exploring domestic suppliers or regional manufacturing partnerships to mitigate tariff exposure and safeguard delivery timelines.
This recalibration of supply chains carries downstream effects for end-user industries such as automotive and aerospace, where component prices and lead times are under intense scrutiny. Pass-through costs have become a critical variable in contract negotiations, prompting greater collaboration between machine builders and parts manufacturers to share efficiency gains. At the same time, trade associations and industry consortia are intensifying advocacy efforts, seeking targeted exclusions and longer phase-in periods to ease the transition.
In response, strategic players have accelerated investments in near-shore production facilities and modular machine architectures that can be locally assembled. These adaptive strategies not only address tariff pressures but also strengthen resilience against future trade disruptions, ensuring that manufacturers can maintain continuity in high-precision finishing operations.
Deep Dive into Market Segments Revealing Key Growth Drivers
A multifaceted segmentation framework reveals the nuanced drivers of demand across end-use markets and technology choices. In aerospace, the balance between commercial and military aircraft production dictates demand for specialty polishing solutions capable of handling composite and metal components, while in automotive, a divergence between commercial and passenger vehicle manufacturers influences preferences for belt and disc sanders in prototyping versus high-volume production environments. Consumer electronics and industrial electronics markets require precise buffing and polishing processes that achieve uniform finishes on delicate plastic or metal housings, whereas medical applications demand stringent surface textures for implantable devices and surgical instruments. Metalworking operations, spanning casting and forging, rely on robust vibratory or barrel finishing systems to remove burrs and achieve consistent metallurgical properties.
Analyzing machine types underscores the importance of versatility and throughput. Barrel finishing systems excel at batch processing of small parts, whereas portable and stationary belt sanders offer flexibility for large or irregular components. Disc sanders, whether mobile or fixed, provide fine-tuned surface grain control, and vibratory finishing solutions deliver uniform media motion for high-volume applications. Within each technology, the choice of process-ranging from color buffing and cut buffing to precision and rough grinding-determines the achievable surface integrity and finish quality. High-gloss and satin polishing variants address aesthetic and functional requirements, while general and precision ultrasonic methods enable flawless finishes on intricate geometries.
Operational considerations further segment the market. Fully automatic machines offer end-to-end process control and minimal human intervention, semi-automatic solutions combine robotics with manual oversight for complex tasks, and manual systems remain relevant for bespoke or small-batch operations. Power source preferences vary by application, with electric machines dominating standardized production lines, hydraulically powered systems used where high torque is required, and pneumatic options favored in explosion-proof or cleanroom environments. Material compatibility spans composites, glass, plastic, wood, and metal substrates, including both ferrous and non-ferrous alloys, each demanding tailored abrasive formulations. Sales channels-from direct engagement with OEMs to distributor partnerships and online platforms-shape accessibility and after-sales support offerings, influencing purchasing decisions across geographies.
This comprehensive research report categorizes the Surface Finishing & Polishing Machine market into clearly defined segments, providing a detailed analysis of emerging trends and precise revenue forecasts to support strategic decision-making.
- End-User Industry
- Type
- Process
- Operation Mode
- Power Source
- Material
- Sales Channel
Regional Dynamics Shaping Global Innovation and Demand
Regional dynamics continue to redefine where and how surface finishing and polishing machinery evolves. In the Americas, established automotive hubs in the United States and Mexico coexist with emerging production facilities in Brazil, driving demand for mid-scale finishing lines and service networks that support lean manufacturing practices. Latin American markets are increasingly investing in aftermarket solutions to extend the life of existing equipment amid budget constraints.
Across Europe, the Middle East and Africa, mature aerospace clusters in Western Europe maintain appetite for ultra-precision grinding and polishing systems, while emerging markets in Eastern Europe and the Gulf region expand capacity for medical device and electronics manufacturing. The emphasis on energy efficiency and stringent environmental regulations pushes suppliers to localize production and collaborate with regional authorities on filtration and waste management standards.
The Asia-Pacific region remains the largest growth engine, led by high-volume automotive and electronics manufacturing in China, Japan and South Korea. India’s rapid industrialization fuels demand for cost-effective surface treatment equipment, and Southeast Asian countries are investing in semi-automatic and portable systems to modernize small and medium-sized enterprises. Japan’s advanced materials sector drives innovation in ultrasonic and high-precision polishing technologies, positioning the region at the cutting edge of next-generation finishing solutions.
This comprehensive research report examines key regions that drive the evolution of the Surface Finishing & Polishing Machine market, offering deep insights into regional trends, growth factors, and industry developments that are influencing market performance.
- Americas
- Europe, Middle East & Africa
- Asia-Pacific
Top Industry Players Steering Technological Advancement
A handful of leading manufacturers shape the competitive landscape through relentless innovation and strategic expansion. Certain global equipment suppliers have broadened their portfolios via acquisitions, integrating abrasive media, filtration systems and automation controls into turnkey solutions. Others focus on niche applications, delivering specialized machines tailored for ultra-fine polishing in semiconductor or medical implant production. Partnerships with software developers and sensor providers have become commonplace, creating ecosystems that offer predictive maintenance, remote monitoring and digital twin capabilities.
Emerging challengers from Asia are leveraging cost advantages and rapid product development cycles to capture share in mid-tier markets, while established European and North American players reinforce their positions through brand reputation and service excellence. Joint ventures and research collaborations between machine builders and materials science institutes are accelerating breakthroughs in hybrid abrasive formulations and eco-friendly consumables. These strategic alliances underscore the importance of a collaborative approach to innovation, as companies aim to meet the evolving demands of sophisticated end users.
This comprehensive research report delivers an in-depth overview of the principal market players in the Surface Finishing & Polishing Machine market, evaluating their market share, strategic initiatives, and competitive positioning to illuminate the factors shaping the competitive landscape.
- Rösler Oberflächentechnik GmbH
- Walther Trowal GmbH
- OTEC Präzisionsfinish GmbH
- SINTOKOGIO, LTD.
- Ecoclean GmbH
- Fintur Finishing Technologies A/S
- TAVATEC SP. Z O.O.
- GF Machining Solutions AG
- Daifuku Co., Ltd.
- EMAG GmbH & Co. KG
Strategic Imperatives to Propel Competitive Advantage
Industry leaders must pursue a multipronged strategy to stay ahead in a rapidly evolving market. First, investment in smart automation and data analytics platforms will create substantial productivity gains and differentiate offerings. Companies should integrate advanced sensors and machine-learning algorithms into their equipment to enable real-time quality control and process optimization. Second, diversifying manufacturing footprints through near-shore facilities or modular production architectures will mitigate trade uncertainties and accelerate customer responsiveness.
Third, a commitment to sustainable design must extend beyond energy efficiency to include closed-loop abrasive recycling, low-emission filtration and end-of-life equipment refurbishing programs. Collaborating with regulatory agencies can expedite eco-innovation and position companies as preferred partners in regions with strict environmental mandates. Fourth, forging strategic alliances with materials suppliers, software developers and academic institutions will foster co-development of next-generation processes, such as precision ultrasonic finishing and hybrid abrasive technologies. Finally, enhancing aftermarket service models-through digital platforms offering remote diagnostics, predictive maintenance and virtual training-will drive recurring revenue streams and strengthen customer loyalty.
Rigorous Framework Underpinning the Research Process
This report synthesizes insights from a robust combination of primary and secondary research. In-depth interviews with C-level executives, plant managers and process engineers across major end-user industries provided firsthand perspectives on emerging trends and pain points. Concurrently, extensive secondary research encompassed corporate filings, regulatory documents, patent analyses and trade association publications to establish historical context and benchmark competitive positioning.
Quantitative data was triangulated through cross-verification of import-export records, industry surveys and technology adoption studies. A rigorous segmentation framework was applied to dissect the market by end-user industry, machine type, process type, operation mode, power source, material compatibility and sales channel. Regional dynamics were analyzed by mapping production footprints, trade flows and regulatory landscapes in the Americas, Europe, the Middle East, Africa and Asia-Pacific. Finally, a peer review process involving subject matter experts ensured the accuracy and relevance of the findings, while continuous quality checks maintained methodological rigor.
Explore AI-driven insights for the Surface Finishing & Polishing Machine market with ResearchAI on our online platform, providing deeper, data-backed market analysis.
Ask ResearchAI anything
World's First Innovative Al for Market Research
Synthesis of Insights Guiding Future Priorities
The convergence of technological innovation, shifting trade policies and evolving end-user requirements underscores the critical need for a nuanced understanding of the surface finishing and polishing machinery sector. Key themes emerged around the integration of automation and digitalization, the importance of sustainable practices, and the strategic realignment of supply chains in response to new tariff regimes. Segmentation analysis revealed distinct value drivers across industries, processes and machine configurations, while regional insights highlighted both established manufacturing hubs and high-growth markets.
Leading companies are charting diverse paths through partnerships, M&A and targeted R&D investments, reinforcing the competitive intensity of the market. For stakeholders seeking to navigate this complexity, the synthesis of these insights provides a clear roadmap for capitalizing on emerging opportunities and mitigating risks. As product lifecycles accelerate and quality expectations rise, adopting a proactive and data-driven approach will be essential for maintaining market leadership.
This section provides a structured overview of the report, outlining key chapters and topics covered for easy reference in our Surface Finishing & Polishing Machine market comprehensive research report.
- Preface
- Research Methodology
- Executive Summary
- Market Overview
- Market Dynamics
- Market Insights
- Cumulative Impact of United States Tariffs 2025
- Surface Finishing & Polishing Machine Market, by End-User Industry
- Surface Finishing & Polishing Machine Market, by Type
- Surface Finishing & Polishing Machine Market, by Process
- Surface Finishing & Polishing Machine Market, by Operation Mode
- Surface Finishing & Polishing Machine Market, by Power Source
- Surface Finishing & Polishing Machine Market, by Material
- Surface Finishing & Polishing Machine Market, by Sales Channel
- Americas Surface Finishing & Polishing Machine Market
- Europe, Middle East & Africa Surface Finishing & Polishing Machine Market
- Asia-Pacific Surface Finishing & Polishing Machine Market
- Competitive Landscape
- ResearchAI
- ResearchStatistics
- ResearchContacts
- ResearchArticles
- Appendix
- List of Figures [Total: 30]
- List of Tables [Total: 860 ]
Unlock the Full Report for Critical Market Intelligence from Ketan Rohom
To obtain the comprehensive market research report and capitalize on these critical insights, reach out directly to Ketan Rohom, Associate Director of Sales & Marketing. Engage in a conversation that will equip your organization with the strategic intelligence required to navigate evolving trade dynamics, leverage emerging technologies, and outperform competitors. Secure your copy today to ensure your leadership team can make data-driven decisions and maintain a competitive edge in the surface finishing and polishing machinery sector
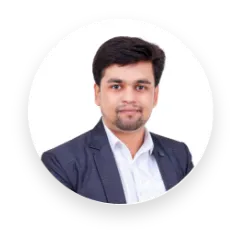
- When do I get the report?
- In what format does this report get delivered to me?
- How long has 360iResearch been around?
- What if I have a question about your reports?
- Can I share this report with my team?
- Can I use your research in my presentation?