Revolutionizing Woodworking with Next-Gen Combined Machines
The surfacing-thickness planer combined machine stands at the confluence of productivity and precision, enabling manufacturers to streamline woodworking operations within a single footprint. By integrating planing and thicknessing functionalities, this technology elevates throughput while minimizing manual handling and material waste. The advent of hybrid machining cells caters to the evolving needs of furniture producers, custom shop operators, and construction fabricators seeking leaner workflows and superior surface quality.
Technological advancements in control systems and toolpath optimization have further cemented the machine’s role as a cornerstone in advanced manufacturing environments. Its modular architecture allows rapid reconfiguration for diverse wood types and dimensional specifications, thereby supporting highly customized outputs without compromising cycle times. As global demand for efficient, high-quality woodworking solutions intensifies, the combined surfacing-thickness planer emerges as a pivotal investment for organizations committed to operational agility and relentless quality standards.
Pioneering Forces Reshaping the Surfacing-Thickness Planer Landscape
A wave of digitalization is sweeping the woodworking landscape, fundamentally transforming how surfacing-thickness planers are designed, operated, and maintained. Embedded sensors, real-time data analytics, and connected tooling systems are enabling predictive maintenance protocols that minimize unplanned downtime and extend machine lifespan. The shift toward smart manufacturing is evident in the proliferation of CNC-driven cells, where five-axis and three-axis toolpaths deliver complex geometries with exceptional repeatability.
Concurrently, sustainability and energy efficiency have become paramount. Manufacturers are embracing modular power units and multi-function tooling that optimize raw material usage and reduce carbon footprints. This emphasis on green machining aligns with global initiatives to decarbonize industrial processes and enhances corporate social responsibility credentials.
Moreover, the growing appetite for customization has spurred the development of semi-automatic and fully automatic configurations. These versatile platforms bridge the gap between manual flexibility and high-volume precision, offering tailored solutions for bespoke furniture makers and large-scale cabinet producers alike. As the smart factory paradigm continues to mature, combined machines will converge further with robotics, artificial intelligence, and digital twin simulations, charting a new frontier of operational excellence.
Assessing the 2025 US Tariff Ripple Effect on Equipment Trade
The introduction of cumulative United States tariffs in 2025 has reverberated across global equipment supply chains, compelling manufacturers and distributors to reassess procurement strategies. Tariff escalations on imported components and finished machines have elevated landed costs, prompting a scale shift in sourcing decisions. Many original equipment manufacturers are exploring alternative suppliers in regions with favorable trade agreements or accelerating local production to mitigate cost pressures.
This realignment has introduced complexity into inventory management, with companies balancing higher safety stock levels against intensified working capital demands. Forward-looking organizations have responded by leveraging long-term supplier contracts and leveraging collaborative planning tools to cushion against tariff volatility. The ripple effect extends downstream, where end users are encountering incremental price adjustments and evaluating total cost of ownership more rigorously.
Despite these headwinds, the tariff environment has catalyzed domestic innovation as companies invest in redesigning machine components for greater inward content. By localizing critical subassemblies and optimizing manufacturing footprints, industry leaders are carving out new competitive advantages. As the trade landscape evolves, stakeholders who adapt with agility and foresight will emerge stronger in the redefined market order.
Unraveling Market Dynamics through Segmentation Lenses
Deep insights into market segmentation reveal nuanced demand patterns shaped by end user requirements, technology preferences, distribution strategies, and power output classifications. Based on end user industry, the market encompasses the Construction Sector and DIY Home Workshops alongside Furniture Manufacturing, which itself subdivides into Kitchen Cabinet Manufacturers, Panel Furniture Makers, and Solid Wood Furniture Makers. Within the kitchen cabinet sphere, demand bifurcates between Solid Wood Cabinets and Veneer Cabinets, while panel furniture applications span Custom Installations, Modular Systems, and Office Partitioning.
Turning to technology frameworks, CNC platforms lead the transformation with five-axis and three-axis variants delivering superior surface finishes and geometric accuracy. Fully automatic configurations satisfy high-volume operations, whereas manual and semi-automatic setups continue to serve niche artisans and lower throughput scenarios. Distribution channels further diversify access, with direct sales fostering close customer relationships, distributor networks offering aftermarket and OEM support, and e-commerce portals-both B2B platforms and manufacturer websites-streamlining digital procurement.
Power output profiles delineate machine capabilities across three categories. High-power units exceeding 15HP break down into 15 to 20HP and greater than 20HP classes, catering to heavy-duty industrial demands. Medium offerings between 5 and 15HP, segmented into 5 to 10HP and 10 to 15HP, strike a balance between versatility and performance. Low-power models below 5HP, subdivided into less than 3HP and 3 to 5HP, address compact workshops and entry-level operations.
This multidimensional segmentation framework empowers decision-makers to align solution portfolios with precise user profiles, optimizing capital allocation and aftermarket strategies.
This comprehensive research report categorizes the Surfacing-Thickness Planer Combined Machine market into clearly defined segments, providing a detailed analysis of emerging trends and precise revenue forecasts to support strategic decision-making.
- End User Industry
- Technology
- Distribution Channel
- Power Output
Decoding Regional Variations in Machine Adoption
Regional trajectories underscore distinct adoption patterns influenced by economic structures, regulatory environments, and industrial ecosystems. In the Americas, strong construction activity and the resurgence of domestic manufacturing have elevated demand for robust, high-throughput planer combinations capable of handling diverse timber species. Regional incentives for nearshoring have driven equipment investments in key industrial corridors.
Across Europe, Middle East & Africa, stringent environmental standards and energy efficiency mandates are shaping machine specifications. Market players are prioritizing models with integrated dust extraction, carbon footprint monitoring, and modular energy recuperation systems. In the Middle East and Africa, growing infrastructure projects and emergent woodworking clusters are creating new pockets of demand.
In the Asia-Pacific region, vibrant furniture manufacturing hubs and a thriving DIY culture are sustaining demand across the technology spectrum. Price-sensitive buyers are drawn to manual and semi-automatic variants, while premium manufacturers are upgrading to five-axis CNC platforms to compete on quality and customization. Government initiatives supporting industrial automation and skill development are further accelerating machine penetration, creating opportunities for both global and local suppliers.
This comprehensive research report examines key regions that drive the evolution of the Surfacing-Thickness Planer Combined Machine market, offering deep insights into regional trends, growth factors, and industry developments that are influencing market performance.
- Americas
- Europe, Middle East & Africa
- Asia-Pacific
Profiling Key Innovators Driving Industry Forward
Leading equipment providers are differentiating through technological leadership, service excellence, and strategic alliances. Homag has distinguished itself with advanced five-axis CNC systems and a comprehensive digital suite for remote monitoring and maintenance, while SCM Group leverages its global service network to deliver rapid field support and flexible financing options. Biesse Group focuses on integrated software ecosystems that synchronize machine tools with enterprise resource planning systems, driving end-to-end operational transparency.
Meanwhile, Weinig emphasizes eco-design principles by introducing energy recovery modules and smart dust-management solutions. Anderson Group targets niche segments with modular portfolio offerings that accommodate rapid reconfiguration for specialized woodworking tasks. Each of these players underscores the critical role of innovation, aftermarket services, and customer training programs in securing market share and fostering long-term partnerships.
This comprehensive research report delivers an in-depth overview of the principal market players in the Surfacing-Thickness Planer Combined Machine market, evaluating their market share, strategic initiatives, and competitive positioning to illuminate the factors shaping the competitive landscape.
- HOMAG Group AG
- SCM Group S.p.A.
- Biesse Group S.p.A.
- Weinig AG
- FELDER GmbH
- Robert Altendorf GmbH & Co. KG
- Ledinek d.o.o.
- Robland NV
- Griggio S.r.l.
- Martin GmbH & Co. KG
Strategic Imperatives to Capitalize on Emerging Opportunities
Industry leaders should prioritize investment in advanced CNC capabilities to capture premium segments and deliver consistent precision across complex geometries. Parallel efforts to expand aftermarket service networks, including digital maintenance platforms and localized technical support, will strengthen customer loyalty and generate recurring revenue streams. Supply chain diversification, driven by a combination of regional sourcing and strategic alliances, will hedge against trade uncertainties and tariff impacts.
Adopting modular architecture in new machine designs can facilitate rapid product updates and customization, aligning with the trend toward personalized manufacturing. Furthermore, embedding energy recovery and emission control features will address the growing demand for sustainable production and compliance with environmental standards. Collaborative innovation initiatives with material suppliers and end users can accelerate the development of optimized tooling solutions, enhancing overall process efficiency.
Finally, cultivating talent through targeted training programs will ensure that workforce skills keep pace with technological advancements. By fostering a culture of continuous learning and cross-functional collaboration, organizations can maximize machine uptime, elevate product quality, and secure a leadership position in the evolving woodworking equipment landscape.
Robust Methodological Framework Ensuring Research Rigor
This analysis is grounded in a rigorous blend of qualitative and quantitative research methodologies. An extensive review of industry literature, trade publications, and regulatory filings provided a foundational understanding of market dynamics and technology trends. Primary interviews with equipment manufacturers, distributors, and end users yielded deep insights into operational challenges, adoption drivers, and competitive positioning.
To validate findings, data triangulation techniques were applied, cross-referencing information from multiple sources to ensure consistency and reliability. Segmentation structures were developed through iterative consultation with domain experts, enabling precise alignment with industry classifications and customer profiles. Regional and tariff impact analyses leveraged customs data, trade reports, and economic indicators to quantify shifts in sourcing and pricing dynamics.
All insights were subjected to peer review by an internal panel of subject-matter specialists, ensuring methodological rigor and impartiality. This robust approach underpins the credibility of the conclusions and recommendations, equipping stakeholders with actionable intelligence to navigate the complex surfacing-thickness planer combined machine market.
Explore AI-driven insights for the Surfacing-Thickness Planer Combined Machine market with ResearchAI on our online platform, providing deeper, data-backed market analysis.
Ask ResearchAI anything
World's First Innovative Al for Market Research
Synthesis of Insights Guiding Stakeholder Decisions
The surfacing-thickness planer combined machine market stands at an inflection point, shaped by digital transformation, evolving trade policies, and heightened sustainability mandates. Segmentation insights reveal distinct end user, technology, distribution, and power output requirements that must guide product development and go-to-market strategies. Regional analyses highlight divergent adoption drivers across the Americas, Europe Middle East & Africa, and Asia-Pacific, underscoring the need for tailored approaches in each jurisdiction.
Key companies are differentiating through technological leadership, service excellence, and strategic partnerships, setting new benchmarks for performance and customer engagement. Actionable recommendations emphasize the importance of CNC investments, aftermarket service expansion, supply chain resilience, modular design, and talent development. This comprehensive examination equips decision-makers with the clarity to align resources, anticipate market shifts, and capitalize on emerging opportunities.
This section provides a structured overview of the report, outlining key chapters and topics covered for easy reference in our Surfacing-Thickness Planer Combined Machine market comprehensive research report.
- Preface
- Research Methodology
- Executive Summary
- Market Overview
- Market Dynamics
- Market Insights
- Cumulative Impact of United States Tariffs 2025
- Surfacing-Thickness Planer Combined Machine Market, by End User Industry
- Surfacing-Thickness Planer Combined Machine Market, by Technology
- Surfacing-Thickness Planer Combined Machine Market, by Distribution Channel
- Surfacing-Thickness Planer Combined Machine Market, by Power Output
- Americas Surfacing-Thickness Planer Combined Machine Market
- Europe, Middle East & Africa Surfacing-Thickness Planer Combined Machine Market
- Asia-Pacific Surfacing-Thickness Planer Combined Machine Market
- Competitive Landscape
- ResearchAI
- ResearchStatistics
- ResearchContacts
- ResearchArticles
- Appendix
- List of Figures [Total: 24]
- List of Tables [Total: 590 ]
Unlock In-Depth Intelligence with Expert Consultation
Elevate your strategic decisions by securing the full market research report today. Engage with Ketan Rohom, Associate Director of Sales & Marketing, to access comprehensive analyses, proprietary insights, and tailored recommendations that will empower your organization to lead in the surfacing-thickness planer combined machine arena. Reach out now to unlock unparalleled intelligence and chart a path to sustainable growth.
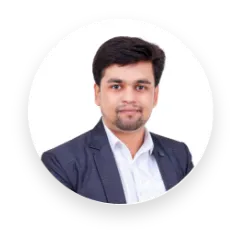
- When do I get the report?
- In what format does this report get delivered to me?
- How long has 360iResearch been around?
- What if I have a question about your reports?
- Can I share this report with my team?
- Can I use your research in my presentation?