Introduction to the Critical Role of Tensile Peel Testing Machines for Plastics
The integrity and longevity of plastic products hinge on precise mechanical characterization, making tensile peel testing machines indispensable across various sectors. As manufacturing standards tighten and regulatory scrutiny intensifies, stakeholders demand reliable data on bond strength, surface adhesion, and material cohesion. Tensile peel testing evaluates the force required to separate laminated layers, films, or coatings under controlled conditions, providing critical insights into product performance and quality assurance.
Advancements in instrumentation-ranging from enhanced load cells to high-resolution sensors-have elevated testing accuracy, while integration with digital platforms enables real-time monitoring and seamless data management. This convergence of hardware precision and software intelligence empowers engineers to identify failure modes early, optimize material selection, and validate manufacturing processes. Moreover, the proliferation of innovative plastics-such as bioplastics and multilayer composites-underlines the need for adaptable testing solutions that can address emerging material complexities.
In this context, organizations must navigate a rapidly evolving landscape where performance requirements intersect with environmental imperatives and regulatory mandates. Understanding the foundational role of tensile peel testing machines is the first step toward building robust quality ecosystems, reducing product recalls, and driving continuous improvement efforts.
Transformative Shifts Redefining Plastics Tensile Peel Testing
Over the past decade, the tensile peel testing arena has undergone seismic shifts driven by technological breakthroughs and market dynamics. Automation integration has transformed manual operations into high-throughput workflows, with robotic handling and recipe-driven test sequences minimizing human error and accelerating cycle times. Simultaneously, the rise of advanced sensor technologies-such as optical displacement sensors and high-precision strain gauges-has enhanced data fidelity, enabling nuanced analysis of peel behavior under diverse loading conditions.
Moreover, the convergence of data analytics and predictive modeling is redefining test strategies. Machine learning algorithms can now identify subtle patterns in failure curves, offering predictive insights that guide material formulation and process optimization. Control systems have likewise evolved, transitioning from analog interfaces to fully digital platforms that support remote calibration, automated compliance checks, and seamless integration with enterprise quality management systems.
Material innovation also plays a pivotal role. The increasing adoption of bioplastics, nanocomposites, and functional coatings demands versatile testing architectures capable of adjusting preload, peel rate, and environmental conditioning. These transformative shifts not only enhance operational efficiency but also empower decision-makers to respond swiftly to evolving regulatory requirements and consumer expectations.
Cumulative Impact of United States Tariffs in 2025 on Testing Equipment
The introduction of new United States tariffs in 2025 has reverberated throughout the plastics testing equipment market, altering procurement strategies and cost structures. Tariff escalations on imported components-ranging from precision load cells to specialized electronic modules-have increased landed equipment costs, prompting many organizations to reevaluate global supply chains. In response, several instrument manufacturers have reshored critical manufacturing processes or sought regional assembly partners to mitigate tariff exposure and maintain competitive pricing.
These adjustments have also influenced vendor selection criteria. Buyers now place greater emphasis on local support networks, spare parts availability, and maintenance scheduling to reduce downtime risks associated with cross-border logistics. Furthermore, procurement teams are negotiating longer-term service agreements to lock in equipment costs and safeguard against future tariff shifts.
On a strategic level, tariff-induced pricing pressures have accelerated collaborations between instrument makers and material suppliers. Joint development initiatives focus on standardizing test fixtures and protocols, reducing custom tooling costs and streamlining regulatory validation. Ultimately, the 2025 tariff landscape underscores the importance of agile sourcing strategies and collaborative industry partnerships in preserving testing excellence without compromising financial performance.
Key Segmentation Insights for Plastics Tensile Peel Testing Market
Analysis based on industry application reveals that automotive manufacturers prioritize peel testing for critical interior adhesives while consumer goods producers emphasize film lamination integrity; medical device developers demand rigorous validation of coatings; and packaging firms focus on both cosmetic packaging and food packaging performance to ensure shelf-life and safety. From a material characteristics perspective, variations in material thickness challenge test calibration, and plastic grade classifications-from bioplastics to high density and low density polymers-require tailored force application, while surface treatment techniques influence adhesion measurements. Examining product performance, end users assess elasticity profiles under dynamic peeling scenarios, quantify peel strength across different substrates, and gauge tensile strength through both dynamic strength and static strength methodologies.
When considering testing methodology, some organizations adopt customized testing to address unique sample geometries, whereas others rely on standardized testing protocols, including ASTM methods and ISO methods, for regulatory compliance. Quality compliance criteria spotlight material certification processes, rigorous process validation practices, and adherence to evolving regulatory frameworks. Operational efficiency drivers include seamless automation integration, advanced data analytics for trend analysis, and proactive maintenance scheduling to maximize instrument uptime. Finally, instrumentation and control segmentation underscores the choice between analog control systems and digital control architectures, complemented by sensor technology options that span optical sensors and high-precision strain gauges.
This comprehensive research report categorizes the Tensile Peel Testing Machine For Plastic market into clearly defined segments, providing a detailed analysis of emerging trends and precise revenue forecasts to support strategic decision-making.
- Industry Application
- Material Characteristics
- Product Performance
- Testing Methodology
- Quality Compliance
- Operational Efficiency
- Instrumentation And Control
Key Regional Insights Shaping Global Testing Demand
In the Americas region, strong demand stems from robust automotive and packaging sectors, underpinned by a focus on reshoring and regional compliance standards that favor locally certified testing equipment. North American laboratories increasingly adopt integrated data analytics platforms to streamline quality assurance workflows, while maintenance scheduling and rapid spare-parts delivery are pivotal service differentiators.
Europe, Middle East & Africa exhibit diverse regulatory landscapes, with European Union directives driving harmonization around ASTM and ISO test methods. Manufacturers in this region emphasize material certification and process validation to meet stringent environmental and safety mandates. In Middle Eastern markets, rapid infrastructure development fuels demand for high-precision instrumentation, whereas Africa’s expanding consumer goods segment calls for cost-effective, standardized testing solutions.
Asia-Pacific represents the fastest-growing regional market, with expanding medical, consumer electronics, and food packaging industries fueling investment in advanced tensile peel testing machines. Local instrument makers compete intensely by offering modular automation integration, advanced sensor packages, and tailored control systems designed to accommodate high-volume testing across varied material grades. Regional service networks and strategic partnerships are increasingly critical to support rapid deployment and ongoing calibration requirements.
This comprehensive research report examines key regions that drive the evolution of the Tensile Peel Testing Machine For Plastic market, offering deep insights into regional trends, growth factors, and industry developments that are influencing market performance.
- Americas
- Asia-Pacific
- Europe, Middle East & Africa
Leading Companies Driving Innovation in Tensile Peel Testing
Prominent suppliers such as Accutek Instruments, Inc., Advanced Materials Testing Corporation, Advanced Polymer Test Laboratories and Agilent Technologies, Inc. have advanced the field through comprehensive test platforms, while Brookfield Engineering Laboratories, Inc., CDC Plastics Inspection Technologies LLC, Dielectric Testing Equipment Corp. and DynaTest Instruments Corporation specialize in niche instrumentation. Epsilon Testing Instruments, LLC, Innovatech Materials Testing Inc., Instron, Inc. and Instronics Testing Devices Ltd. deliver robust solutions with extensive calibration services, and LET Testing Systems, LLC, Materials Integrity Solutions LLC, Mecmesin Ltd. and MTS Systems Corporation emphasize high-precision control systems paired with automated data management. Firms like NuTest Solutions Ltd., OmniTest Instruments Inc., Phoenix Testing Technologies and Plastec Testing Solutions Inc. innovate in surface treatment and material thickness applications, alongside Plastic Properties Testing Laboratories, Inc., Polymer Test Solutions Inc., PolyTest Engineering Inc. and Precision Polymer Testing Corporation. Emerging players such as Promaterial Testing Solutions, QTest Plastics Corporation, S.A.F. Testing Solutions Inc. and Shimadzu Corporation balance broad portfolios with regional support, while SimTest Mechanics Corporation, TechTest Materials & Plastics Inc., Tinius Olsen Testing Machine Company, Inc., Vantage Testing Systems Ltd. and ZwickRoell Group advance sensor technology and digital control integration to meet evolving market demands.
This comprehensive research report delivers an in-depth overview of the principal market players in the Tensile Peel Testing Machine For Plastic market, evaluating their market share, strategic initiatives, and competitive positioning to illuminate the factors shaping the competitive landscape.
- Accutek Instruments, Inc.
- Advanced Materials Testing Corporation
- Advanced Polymer Test Laboratories
- Agilent Technologies, Inc.
- Brookfield Engineering Laboratories, Inc.
- CDC Plastics Inspection Technologies LLC
- Dielectric Testing Equipment Corp.
- DynaTest Instruments Corporation
- Epsilon Testing Instruments, LLC
- Innovatech Materials Testing Inc.
- Instron, Inc.
- Instronics Testing Devices Ltd.
- LET Testing Systems, LLC
- Materials Integrity Solutions LLC
- Mecmesin Ltd.
- MTS Systems Corporation
- NuTest Solutions Ltd.
- OmniTest Instruments Inc.
- Phoenix Testing Technologies
- Plastec Testing Solutions Inc.
- Plastic Properties Testing Laboratories, Inc.
- Polymer Test Solutions Inc.
- PolyTest Engineering Inc.
- Precision Polymer Testing Corporation
- Promaterial Testing Solutions
- QTest Plastics Corporation
- S.A.F. Testing Solutions Inc.
- Shimadzu Corporation
- SimTest Mechanics Corporation
- TechTest Materials & Plastics Inc.
- Tinius Olsen Testing Machine Company, Inc.
- Vantage Testing Systems Ltd.
- ZwickRoell Group
Actionable Recommendations for Industry Leaders
Industry leaders should invest in modular automation integration to scale testing capacity while reducing manual intervention and variability. Embracing advanced data analytics platforms will enable teams to detect trending anomalies in peel force curves and implement proactive quality improvements. Companies must prioritize collaboration with certification bodies to streamline material certification and process validation workflows, thereby accelerating time-to-market and reducing regulatory risk.
Integrating next-generation sensor technology-such as high-resolution optical sensors and precision strain gauges-can significantly enhance measurement accuracy, especially when characterizing novel bioplastics or multi-layer composites. Additionally, deploying predictive maintenance scheduling tools minimizes unscheduled downtime and optimizes overall equipment effectiveness. Strategic supply chain diversification ensures resilience against tariff fluctuations and component shortages; aligning with regional partners can provide agility in maintenance and spare parts provisioning.
Upskilling the technical workforce on both analog control principles and digital control architectures will facilitate seamless transitions between legacy systems and modern platforms. Finally, adopting industry 4.0 frameworks-leveraging IoT connectivity, cloud-based data repositories and digital twins-will empower organizations to simulate test scenarios, optimize machine configurations and maintain competitive advantage.
Explore AI-driven insights for the Tensile Peel Testing Machine For Plastic market with ResearchAI on our online platform, providing deeper, data-backed market analysis.
Ask ResearchAI anything
World's First Innovative Al for Market Research
Conclusion: Strengthening Testing Strategies for Competitive Edge
As market dynamics and regulatory landscapes continue to evolve, tensile peel testing machines will remain central to ensuring product quality, safety and compliance in the plastics industry. The convergence of automation, advanced sensor technologies and data-driven analytics presents a unique opportunity for organizations to elevate their quality assurance capabilities while reducing operational costs. Meanwhile, tariff-driven supply chain adjustments underscore the importance of agile sourcing strategies and regional support networks.
Segmentation insights reveal that tailored solutions-whether addressing specific industry applications such as automotive or cosmetic packaging, or accommodating unique testing methodologies like customized fixtures or standardized ASTM and ISO protocols-can unlock new value. Regional trends indicate that local compliance requirements and market growth trajectories demand targeted deployment strategies, while leading companies continue to innovate through precision controls and comprehensive service offerings.
By implementing the actionable recommendations outlined earlier, industry stakeholders can enhance testing accuracy, streamline workflows and future-proof their operations against emerging challenges. Ultimately, a strategic focus on holistic quality ecosystems will drive product excellence, foster customer trust and sustain competitive differentiation.
This section provides a structured overview of the report, outlining key chapters and topics covered for easy reference in our Tensile Peel Testing Machine For Plastic market comprehensive research report.
- Preface
- Research Methodology
- Executive Summary
- Market Overview
- Market Dynamics
- Market Insights
- Cumulative Impact of United States Tariffs 2025
- Tensile Peel Testing Machine For Plastic Market, by Industry Application
- Tensile Peel Testing Machine For Plastic Market, by Material Characteristics
- Tensile Peel Testing Machine For Plastic Market, by Product Performance
- Tensile Peel Testing Machine For Plastic Market, by Testing Methodology
- Tensile Peel Testing Machine For Plastic Market, by Quality Compliance
- Tensile Peel Testing Machine For Plastic Market, by Operational Efficiency
- Tensile Peel Testing Machine For Plastic Market, by Instrumentation And Control
- Americas Tensile Peel Testing Machine For Plastic Market
- Asia-Pacific Tensile Peel Testing Machine For Plastic Market
- Europe, Middle East & Africa Tensile Peel Testing Machine For Plastic Market
- Competitive Landscape
- ResearchAI
- ResearchStatistics
- ResearchContacts
- ResearchArticles
- Appendix
- List of Figures [Total: 30]
- List of Tables [Total: 590 ]
Call-To-Action: Engage with Ketan Rohom to Access the Full Report
To gain comprehensive insights and detailed analysis on the tensile peel testing machine market-including in-depth segmentation breakdowns, regional dynamics and vendor profiles-reach out to Ketan Rohom, Associate Director, Sales & Marketing. Leverage expert guidance to secure your copy of the full market research report and equip your organization with the data-driven intelligence needed to optimize testing strategies and drive growth.
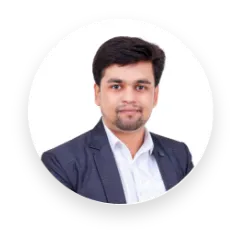
- When do I get the report?
- In what format does this report get delivered to me?
- How long has 360iResearch been around?
- What if I have a question about your reports?
- Can I share this report with my team?
- Can I use your research in my presentation?