The Thermal Barrier Coatings Market size was estimated at USD 22.22 billion in 2024 and expected to reach USD 23.98 billion in 2025, at a CAGR 7.82% to reach USD 34.93 billion by 2030.

Unleashing the Potential of Advanced Thermal Protection
Thermal barrier coatings represent a critical innovation at the intersection of materials science and high-performance engineering. Designed to shield components from extreme temperatures, these advanced ceramic layers enable gas turbines, aircraft engines, and automotive systems to operate at peak efficiency while mitigating thermal fatigue. As global energy demands rise and manufacturers seek greater fuel economy, the sophistication and reliability of thermal protection solutions have become central to engineering breakthroughs. Technological advancements in deposition methods and material formulations have redefined what is possible, driving the coatings market into a new era of performance and durability.
Against a backdrop of stricter emissions regulations and intensifying pressure to reduce operational costs, industry stakeholders are prioritizing coatings that extend maintenance intervals and enhance component lifespans. Leading original equipment manufacturers and aftermarket service providers are investing in research and collaboration to fine-tune microstructures, optimize bond coats, and tailor topcoat compositions. These efforts not only improve thermal resistance but also address adhesion challenges and resistance to oxidation. In this dynamic environment, understanding the evolving landscape of thermal barrier coatings is essential for decision-makers seeking to capitalize on emerging opportunities and navigate competitive pressures.
Revolutionizing Thermal Barrier Coatings for Next-Gen Applications
The thermal barrier coatings landscape is undergoing a profound transformation fueled by breakthroughs in deposition technology and process integration. Traditional air plasma spray methods are giving way to more precise techniques such as electron beam physical vapor deposition, which delivers highly controlled columnar microstructures and superior strain tolerance. High velocity oxy-fuel processes, meanwhile, are enabling denser, more uniform coatings that balance thermal protection with mechanical resilience. As manufacturers refine application parameters and incorporate in-situ monitoring, the production of consistent, high-performance layers has become more scalable and repeatable than ever before.
Material innovation is equally impactful, with rare earth zirconate compositions expanding the operational temperature envelope beyond that of conventional yttria stabilized zirconia. These new ceramic topcoats resist phase transformation and sintering, preserving thermal insulating properties under prolonged exposure. Multilayer architectures and graded bond coats are further enhancing adhesion and mitigating thermal mismatch stresses. The shift toward these advanced material systems reflects a broader industry commitment to pushing the boundaries of component longevity.
Digital transformation is also reshaping the coatings ecosystem, as data-driven process control and predictive analytics enable real-time adjustments and proactive maintenance. By coupling thermal imaging and machine learning algorithms, service providers can anticipate coating degradation and schedule recoating operations precisely, reducing unplanned downtime. This fusion of materials expertise and digital engineering is setting a new standard for reliability, cost efficiency, and sustainability in thermal barrier applications.
Navigating the Ripple Effects of 2025 U.S. Tariffs on Coating Supply Chains
The implementation of United States tariffs in 2025 has introduced a new set of challenges across thermal barrier coating supply chains. Import duties on key ceramic powders and raw materials have increased input costs, prompting manufacturers to reassess sourcing strategies. This cost shift has not only affected direct materials but has also reverberated through logistics, as suppliers adjust shipping routes and inventory policies to absorb tariff impacts. In response, some producers have accelerated efforts to secure long-term supply contracts, while others have sought alternative materials with comparable performance and lower duty burdens.
These trade measures have catalyzed a reoptimization of global production footprints. Nearshoring initiatives have gained traction as companies establish or expand domestic coating facilities, reducing exposure to volatile tariff policies and minimizing transit delays. Investments in capacity enhancement at local sites are now accompanied by automation upgrades to maintain productivity and quality standards. At the same time, strategic partnerships between raw material suppliers and process houses are being formed to ensure stable access to advanced ceramic feedstocks.
End users in aerospace and power generation have felt the downstream effects as coating service rates have gradually adjusted to reflect increased operational costs. While some organizations have absorbed these expenses to preserve program schedules, others are leveraging multi-sourcing strategies and exploring aftermarket alternatives to mitigate price escalation. Ultimately, the tariff environment is reshaping purchasing behaviors and reinforcing the importance of supply chain resilience in sustaining continuous, cost-effective thermal protection.
Deep-Dive into Market Segmentation Driving Coating Demand
Analyzing the market through the lens of application reveals that combustor components demand coatings engineered for rapid thermal transients, whereas exhaust manifolds require systems that resist corrosive gas compositions and cyclic oxidation. Turbine blades, operating under the most severe thermal gradients, prioritize coatings with exceptional strain tolerance, and turbine vanes benefit from formulations that optimize heat flux management at varying pressure stages.
When viewed by technology, air plasma spray maintains its prevalence for widespread coverage and cost-effective production, though electron beam physical vapor deposition has surged in specialized applications that require columnar microstructures and precise thickness control. High velocity oxy-fuel deposition occupies a middle ground, offering a balance between deposition efficiency and coating density, making it an attractive option for service providers emphasizing throughput and consistency.
Material differentiation underscores diverse performance priorities. Mullite coatings deliver cost advantages and thermal stability for moderate-temperature components, while rare earth zirconate compositions expand the protective range to ultra-high-temperature zones. Yttria stabilized zirconia continues to serve as a versatile workhorse, balancing thermal insulation with proven reliability across numerous engine platforms.
End use industry analysis highlights that aerospace applications, spanning business jets, commercial airliners, and military aircraft, account for a significant proportion of coating demand, driven by rigorous performance criteria and long-term maintenance cycles. Automotive sectors focus on exhaust systems and turbochargers to meet fuel economy and emissions targets, whereas power generation facilities leverage coatings in aero gas turbines and industrial gas turbines to enhance efficiency and extend service intervals.
Process stage dynamics reveal that OEM programs prioritize rigorous qualification and standardized application protocols during initial assembly, while aftermarket services emphasize rapid turnaround, refurbishment capabilities, and field repair solutions. This duality underscores the need for flexible coating strategies that cater to both new-build and maintenance-driven markets.
This comprehensive research report categorizes the Thermal Barrier Coatings market into clearly defined segments, providing a detailed analysis of emerging trends and precise revenue forecasts to support strategic decision-making.
- Application
- Technology
- Material
- End Use Industry
- Process Stage
Regional Dynamics Shaping the Global Thermal Barrier Landscape
In the Americas, demand for thermal barrier coatings is anchored by a strong aerospace manufacturing industry and a robust power generation sector that includes conventional gas turbine plants and emerging clean energy initiatives. Regional coating suppliers are capitalizing on proximity to prime OEM customers and leveraging advanced deposition hubs to deliver responsive service and support tight program timelines. Government incentives and defense contracts further reinforce investment in specialized coating capabilities across the United States and Canada.
Europe, Middle East & Africa presents a diversified landscape where stringent emissions regulations and a legacy of gas turbine innovation drive adoption. European coating producers emphasize sustainability, integrating life-cycle analysis and low-environmental-impact materials into their offerings. Meanwhile, Middle Eastern power generation projects, fueled by rapid infrastructure expansion, place a premium on high-throughput coating services that minimize station downtime. In Africa, growth in aviation and energy sectors is prompting targeted infrastructure investments that include modern coating facilities.
Asia-Pacific stands out as a high-growth region fueled by large-scale manufacturing hubs in China, Japan, South Korea, and India. Ambitious aerospace development programs and the proliferation of gas turbine installations in emerging economies are underpinning strong coating uptake. Local players are scaling capabilities rapidly, investing in electron beam deposition, advanced automation, and quality control systems. Strategic collaborations with Western technology partners are further accelerating the adoption of next-generation ceramic compositions and application techniques across the region.
This comprehensive research report examines key regions that drive the evolution of the Thermal Barrier Coatings market, offering deep insights into regional trends, growth factors, and industry developments that are influencing market performance.
- Americas
- Europe, Middle East & Africa
- Asia-Pacific
Leading Innovators Shaping the Thermal Barrier Coating Sector
Industry leadership in thermal barrier coatings is characterized by continuous innovation and strategic partnerships. Key players have pursued advanced deposition technologies, with some firms bolstering their electron beam vapor deposition expertise through targeted acquisitions. Others have expanded their process footprints to include high velocity oxy-fuel capabilities, positioning themselves to meet both OEM specifications and aftermarket turnaround demands.
Major technology providers have cultivated exclusive relationships with engine manufacturers to co-develop proprietary coating recipes that optimize component performance under specific operating profiles. These collaborations extend to joint research centers focused on next-generation ceramics, where material scientists work alongside process engineers to refine particle morphology and bond coat architectures. Licensing agreements and royalty models have emerged as viable alternatives to traditional supply contracts, enabling coating specialists to monetize intellectual property while maintaining strong OEM affiliations.
On the logistics side, top-tier service providers leverage global networks of coating facilities to offer standardized quality across continents, facilitating maintenance campaigns for international fleet operators. Investments in automation, real-time monitoring, and digital traceability systems have enhanced reproducibility and reduced cycle times. Additionally, some organizations are diversifying into complementary surface treatments, corrosion protection, and thermal management solutions, creating integrated portfolios that address broader component lifecycle requirements.
This comprehensive research report delivers an in-depth overview of the principal market players in the Thermal Barrier Coatings market, evaluating their market share, strategic initiatives, and competitive positioning to illuminate the factors shaping the competitive landscape.
- Praxair Surface Technologies, Inc.
- Sulzer Metco AG
- Bodycote plc
- OC Oerlikon Balzers Coating AG
- Saint-Gobain Coating Solutions SAS
- IHI Corporation
- Howmet Aerospace Inc.
- Kawasaki Heavy Industries, Ltd.
- Sandvik AB
- Shin-Etsu Chemical Co., Ltd.
Strategic Imperatives for Success in a Competitive Coatings Market
Industry leaders should prioritize the deployment of next-generation deposition platforms, combining electron beam vapor deposition for critical components with high velocity oxy-fuel systems for high-volume operations. By integrating advanced process control and in-situ diagnostics, companies can achieve consistent coating quality and reduce rework rates. Investing in material research partnerships will ensure early access to breakthrough formulations, such as rare earth zirconates and multilayer architectures, that extend performance boundaries.
Supply chain agility is essential in the face of evolving tariff landscapes. Organizations are advised to diversify raw material sources and consider strategic stockpiling of key ceramic powders. Establishing regional coating centers near primary OEM and aftermarket hubs can mitigate logistics risks and accelerate response times. Furthermore, companies should explore collaborative ventures with raw material producers to secure favorable supply agreements and co-invest in capacity expansions.
To strengthen market positioning, firms can expand service offerings to include predictive maintenance analytics powered by thermal imaging and machine learning. By shifting from reactive to proactive maintenance models, service providers help end users optimize downtime and extend component service intervals. Finally, embedding sustainability criteria into product development-through eco-friendly processes and life-cycle assessments-will align coating portfolios with emerging environmental regulations and customer expectations.
Rigorous Research Framework Guiding Our Market Insights
Our analysis is grounded in a comprehensive research framework that combines primary interviews with coating experts, materials scientists, and industry stakeholders across key regions. These direct engagements provided nuanced perspectives on technology adoption, supply chain challenges, and evolving end user priorities. Secondary research encompassed white papers, patent filings, regulatory documents, and corporate reports, ensuring a robust foundation of publicly available intelligence.
Data triangulation was applied to validate insights, cross-referencing interview findings with quantitative data from industry associations and trade publications. This iterative process ensured consistency and credibility, while in-house subject matter reviews refined technical accuracy. Quality control measures included multiple peer reviews, editorial audits, and verification of all cited sources. The result is a holistic, rigorously vetted portrayal of the thermal barrier coatings market that balances depth of analysis with clarity and accessibility.
Explore AI-driven insights for the Thermal Barrier Coatings market with ResearchAI on our online platform, providing deeper, data-backed market analysis.
Ask ResearchAI anything
World's First Innovative Al for Market Research
Synthesizing Key Takeaways to Empower Industry Decision-Making
Thermal barrier coatings are redefining the performance envelope of high-temperature components, driven by material innovation, process advancements, and strategic realignments within global supply chains. The interplay of tariffs, regional dynamics, and technological shifts underscores the importance of agility, collaboration, and forward-thinking investment. As the market moves toward more sophisticated ceramics and data-driven process control, stakeholders who embrace these trends will secure a competitive edge and deliver lasting value.
Navigating this complex environment requires a clear understanding of application-specific demands, regional growth catalysts, and the evolving role of service providers in delivering end-to-end coating solutions. By leveraging the segmentation insights, regional analysis, and company strategies outlined in this report, decision-makers can chart actionable paths for growth, risk mitigation, and technological leadership. The path forward is defined by a commitment to innovation, supply chain resilience, and a relentless focus on performance excellence.
This section provides a structured overview of the report, outlining key chapters and topics covered for easy reference in our Thermal Barrier Coatings market comprehensive research report.
- Preface
- Research Methodology
- Executive Summary
- Market Overview
- Market Dynamics
- Market Insights
- Cumulative Impact of United States Tariffs 2025
- Thermal Barrier Coatings Market, by Application
- Thermal Barrier Coatings Market, by Technology
- Thermal Barrier Coatings Market, by Material
- Thermal Barrier Coatings Market, by End Use Industry
- Thermal Barrier Coatings Market, by Process Stage
- Americas Thermal Barrier Coatings Market
- Europe, Middle East & Africa Thermal Barrier Coatings Market
- Asia-Pacific Thermal Barrier Coatings Market
- Competitive Landscape
- ResearchAI
- ResearchStatistics
- ResearchContacts
- ResearchArticles
- Appendix
- List of Figures [Total: 26]
- List of Tables [Total: 325 ]
Secure Comprehensive Insights with Expert Guidance from Ketan Rohom
Elevate your strategic decision-making by securing access to the full market research report on thermal barrier coatings. Connect directly with Ketan Rohom, Associate Director, Sales & Marketing at 360iResearch to explore tailored insights, discuss bespoke research solutions, and obtain the comprehensive analysis you need to outpace competitors. Reach out today to unlock in-depth intelligence and position your organization for sustained success in an evolving high-temperature protection market.
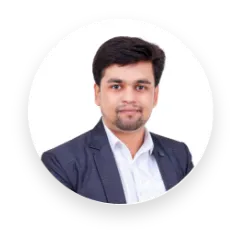
- How big is the Thermal Barrier Coatings Market?
- What is the Thermal Barrier Coatings Market growth?
- When do I get the report?
- In what format does this report get delivered to me?
- How long has 360iResearch been around?
- What if I have a question about your reports?
- Can I share this report with my team?
- Can I use your research in my presentation?