Setting the Stage for Thermoplastic Evolutions
The evolution of automotive interiors has never been more pronounced, driven by the industry’s relentless pursuit of lighter, more durable, and sustainable components. Thermoplastic vulcanizates (TPVs) have emerged at this nexus of demand, offering a unique blend of elastomeric performance and thermoplastic processability. As consumer expectations shift toward premium tactile experiences, and as regulatory bodies mandate stricter emissions and recyclability standards, TPVs are positioned to redefine interior surfaces, seals, and modules.
This executive summary distills the critical trends, market forces, and strategic imperatives shaping the TPV materials ecosystem for automotive interiors. It provides a concise yet comprehensive exploration of transformative shifts, the latest trade policy impacts, granular segmentation insights, regional dynamics, leading supplier strategies, and actionable recommendations. By weaving together empirical analysis and expert perspectives, this report lays the groundwork for informed decision-making and sustained competitive advantage in a rapidly evolving marketplace.
Navigating Transformative Shifts in Automotive Interiors
A confluence of technological innovation and shifting market expectations has catalyzed a transformative phase in automotive interior design. Electrification continues to accelerate, prompting material scientists to optimize TPV formulations for lightweighting without compromising acoustic insulation or tactile quality. Simultaneously, the industry’s pivot toward circularity compels developers to integrate recycled resin streams and adopt design-for-disassembly principles.
Against this backdrop, regulatory bodies worldwide are enacting more stringent end-of-life vehicle directives and volatile trade regulations, prompting supply chain realignments. Consumers now demand interiors that convey both luxury and sustainability, elevating surface finishes and colorfastness to new importance. In parallel, advanced manufacturing techniques-ranging from high-precision injection molding to thermoforming-are unlocking novel TPV geometries and textures. Collectively, these forces are redefining the role of TPVs as more than mere functional polymers, positioning them as strategic enablers of next-generation interior experiences.
Assessing the Impact of US Tariff Revisions on TPV Flows
In 2025, a recalibration of United States tariff schedules on polymer imports has reverberated across the global TPV supply chain. Heightened duty rates on specific thermoplastic elastomer categories have elevated landed costs for raw materials, compelling both domestic and international suppliers to reassess their trade hubs and inventory buffers. Tier-one integrators are navigating this new cost landscape by accelerating near-shoring initiatives and fostering long-term offtake agreements with North American resin producers.
This tariff environment has also amplified the appeal of domestic compounding facilities, which offer greater lead-time reliability amid disrupted ocean freight lanes. However, capacity constraints at these sites have spotlighted bottlenecks in secondary processing, driving innovation in continuous extrusion and low-pressure injection systems to boost throughput. As stakeholders adapt, the net effect will be a redistribution of global TPV trade flows, with some regions experiencing tighter supply and others establishing new export corridors. Strategic procurement teams must therefore realign sourcing strategies to balance cost, quality, and regulatory compliance.
Decoding the Market Through Material, Product, and Process Lenses
A nuanced understanding of market segmentation reveals where value and growth converge in the TPV space. By material type, acrylonitrile butadiene styrene remains a mainstay for high-rigidity trim applications, while polypropylene grades command significant share in center console and dashboard overlays. Polyvinyl chloride, though facing sustainability headwinds, continues to serve niche headliner and door-panel skins that require premium surface finishes. Thermoplastic elastomer and thermoplastic polyolefin blends are gaining traction in floor mats and pillar trim, thanks to their superior resilience and simplified recycling at end of life.
Examining the product landscape, center consoles and dashboards represent the lion’s share of TPV usage, driven by OEMs’ desire for integrated features and haptic differentiation. Door trim and seats follow closely, where acoustic sealing and comfort performance are paramount. Headliners and pillar trim present untapped design potential as manufacturers explore lightweighting and modular assembly. Vehicle-type segmentation underscores the growing influence of electric platforms: battery electric, hybrid electric, and plug-in hybrid architectures demand specialized TPV formulations that withstand higher under-hood temperatures and resist coolant exposures.
Manufacturing processes further shape competitive positioning. Blow molding and extrusion processes enable continuous production of high-volume components, whereas injection molding and thermoforming support complex geometries and rapid color changeovers. In distribution, original equipment manufacturers maintain rigorous qualification protocols, while the aftermarket segment drives opportunities for retrofit and customization. Together, these segmentation lenses illuminate the critical intersections where technical performance, cost efficiency, and regulatory alignment determine market success.
This comprehensive research report categorizes the TPV Materials for Automotive Interiors market into clearly defined segments, providing a detailed analysis of emerging trends and precise revenue forecasts to support strategic decision-making.
- Material Type
- Product
- Vehicle Type
- Manufacturing Process
- Distribution Channel
Regional Dynamics Shaping TPV Material Demand
Regional dynamics exert a profound influence on TPV adoption and innovation. In the Americas, ongoing investments in light-weight automotive platforms and the rise of near-shoring initiatives have stimulated demand for domestically compounded TPV resins. Local OEMs are prioritizing supply chain resilience, leveraging regional free-trade agreements to optimize cost structures and lead times.
Across Europe, Middle East & Africa, stringent emissions regulations and circular-economy mandates are the primary drivers. European automakers collaborate closely with polymer innovators to develop bio-based TPV variants and closed-loop recycling streams. In the Middle East, burgeoning production hubs target both local assembly plants and export markets, while Africa’s emerging automotive clusters are beginning to explore cost-effective TPV solutions for commercial vehicle cabins.
The Asia-Pacific region leads in both manufacturing capacity and end-market consumption. Chinese and Southeast Asian automakers integrate TPVs at scale for door trims and seats, supported by rapidly expanding compounding facilities. Japan and Korea, home to advanced elastomer research institutes, are pushing the frontiers of flame retardancy and UV stability for harsh climate conditions. This geographic mosaic underscores the importance of tailored strategies that align material innovations with regional regulatory frameworks and consumer preferences.
This comprehensive research report examines key regions that drive the evolution of the TPV Materials for Automotive Interiors market, offering deep insights into regional trends, growth factors, and industry developments that are influencing market performance.
- Americas
- Europe, Middle East & Africa
- Asia-Pacific
Profiling Leaders Driving Thermoplastic Innovation
Industry leaders are differentiating through a blend of technological innovation, strategic partnerships, and operational excellence. Leading polymer producers have invested heavily in proprietary catalyst systems and continuous compounding lines to enhance batch consistency and throughput. Several have formed joint ventures with automotive OEMs and tier-one suppliers to co-develop interior modules, accelerating time-to-market for advanced TPV compounds tailored to specific vehicle architectures.
Meanwhile, specialty chemical firms are expanding their service portfolios to include in-house testing laboratories and digital simulation platforms, enabling faster validation of color matching, UV resistance, and low-temperature flexibility. A subset of manufacturers has pursued backward integration, securing key elastomer feedstocks and stabilizer packages to mitigate raw-material volatility. At the same time, contract processors are differentiating on agility, offering rapid tooling and small-batch production runs that support low-volume luxury and concept vehicle programs.
Collectively, these strategies are fostering a more resilient and innovative TPV ecosystem. Companies that excel are those that align material R&D with the functional and aesthetic demands of modern interiors, while maintaining rigorous cost discipline and environmental stewardship.
This comprehensive research report delivers an in-depth overview of the principal market players in the TPV Materials for Automotive Interiors market, evaluating their market share, strategic initiatives, and competitive positioning to illuminate the factors shaping the competitive landscape.
- ExxonMobil Chemical Company
- Hexpol Compounding AB
- Teknor Apex Company
- Kraiburg TPE GmbH & Co. KG
- Zeon Corporation
- Avient Corporation
- Kuraray Co., Ltd.
- Daikin Industries, Ltd.
- Mitsui Chemicals, Inc.
- RTP Company
Strategic Actions for Sustained Competitive Edge
To thrive in the TPV materials arena, industry leaders should first optimize their material portfolios for the unique demands of electric vehicle platforms, focusing on heat-resistant and lightweight formulations that enhance both performance and range. Next, investments in advanced extrusion and low-pressure injection molding technologies will unlock new shape and texture possibilities, while reducing cycle times and energy consumption.
Parallel to process enhancements, forging collaborative R&D partnerships with OEM design teams will ensure that TPV compounds meet exacting specifications for haptic feedback and integration with emerging infotainment architectures. Supply chain resilience can be bolstered by diversifying sourcing across multiple geographies and securing long-term offtake agreements with key compounders. Implementing digital twin simulations for interior components will further reduce prototyping cycles and accelerate time to production.
Finally, embedding circular-economy principles into product development-through increased use of recycled content and design for disassembly-will not only meet regulatory mandates but also resonate with environmentally conscious consumers. By executing on these strategic initiatives, companies can achieve sustained competitive advantage and capitalize on the rapidly evolving opportunities within automotive interiors.
Rigorous Research Foundations Underpinning Insights
This analysis draws upon a robust mixed-methods approach. Primary research involved in-depth interviews with procurement leaders at OEMs, quality engineers at tier-one suppliers, and technical directors at leading polymer manufacturers. Secondary sources included industry journals, regulatory databases, trade association reports, and patent filings, enabling a comprehensive view of technological trajectories and policy developments.
Data triangulation techniques were applied to validate quantitative insights, while qualitative feedback from expert workshops informed the interpretation of emerging trends. The market was segmented across five key dimensions-material type, product application, vehicle architecture, manufacturing process, and distribution channel-to ensure analytical granularity. Regional focuses spanned the Americas, Europe, Middle East & Africa, and Asia-Pacific, reflecting both established and high-growth markets.
A peer-review process, involving external subject-matter experts, ensured methodological rigor and impartiality. Together, these research foundations underpin the credibility of the strategic recommendations and market dynamics presented herein.
Explore AI-driven insights for the TPV Materials for Automotive Interiors market with ResearchAI on our online platform, providing deeper, data-backed market analysis.
Ask ResearchAI anything
World's First Innovative Al for Market Research
Converging Trends Define the Future of Automotive TPVs
Thermoplastic vulcanizates have transcended their traditional role as secondary sealing materials to become central enablers of modern automotive interior design. The interplay of electrification, sustainability imperatives, and trade policy shifts has created a fertile environment for TPV innovation. Material segmentation reveals rich opportunities across polymers and product types, while regional analysis highlights divergent growth trajectories and supply chain considerations.
Companies that strategically align R&D efforts with evolving OEM requirements, and that invest in next-generation processing technologies, will lead the market. Simultaneously, embedding circular-economy practices will not only ensure compliance with emerging regulations but will also resonate with end-users seeking greener mobility solutions. In sum, the future of automotive interiors will be shaped by the ability of TPV stakeholders to integrate performance, efficiency, and sustainability at every stage of the value chain.
This section provides a structured overview of the report, outlining key chapters and topics covered for easy reference in our TPV Materials for Automotive Interiors market comprehensive research report.
- Preface
- Research Methodology
- Executive Summary
- Market Overview
- Market Dynamics
- Market Insights
- Cumulative Impact of United States Tariffs 2025
- TPV Materials for Automotive Interiors Market, by Material Type
- TPV Materials for Automotive Interiors Market, by Product
- TPV Materials for Automotive Interiors Market, by Vehicle Type
- TPV Materials for Automotive Interiors Market, by Manufacturing Process
- TPV Materials for Automotive Interiors Market, by Distribution Channel
- Americas TPV Materials for Automotive Interiors Market
- Europe, Middle East & Africa TPV Materials for Automotive Interiors Market
- Asia-Pacific TPV Materials for Automotive Interiors Market
- Competitive Landscape
- ResearchAI
- ResearchStatistics
- ResearchContacts
- ResearchArticles
- Appendix
- List of Figures [Total: 26]
- List of Tables [Total: 289 ]
Dive Deeper into the TPV Market with Our Expert Report
To unlock the full depth of these insights and gain a competitive edge in the dynamic thermoplastic vulcanizate (TPV) materials landscape for automotive interiors, reach out to Ketan Rohom, Associate Director of Sales & Marketing. Engage directly with an expert to secure your copy of the comprehensive market research report and empower your strategic decision-making today
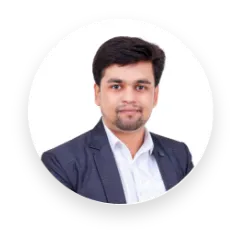
- When do I get the report?
- In what format does this report get delivered to me?
- How long has 360iResearch been around?
- What if I have a question about your reports?
- Can I share this report with my team?
- Can I use your research in my presentation?