Introduction: Smart Inspection Robotics Transforming Manufacturing Quality Assurance
Smart inspection robots are redefining quality assurance by integrating advanced sensors, artificial intelligence, and autonomous navigation into manufacturing workflows. As production lines evolve to meet stringent standards and faster cycle times, these robotic systems offer real-time anomaly detection, precise defect classification, and predictive maintenance insights. Leading manufacturers are leveraging chemical, gas, and proximity sensors in synergy with centralized control software and SLAM-based navigation to inspect complex assemblies with unprecedented accuracy. This convergence of technologies not only reduces downtime and scrap rates but also enhances worker safety by automating hazardous inspection tasks. With modular designs ranging from articulated six-axis arms to crawler configurations, inspection robots adapt to diverse payload capacities, power sources, and connectivity requirements. By bridging the gap between digital twins and physical assets, organizations can transition from reactive problem solving to proactive quality management. In this context, smart inspection robotics emerges as a cornerstone of Industry 4.0, enabling companies to sustain competitive advantages through optimized throughput, consistent product quality, and scalable operations.
Transformative Technological Shifts Driving the Inspection Robot Landscape
The inspection robot landscape has undergone transformative shifts fueled by breakthroughs in sensor technology, machine learning, and edge computing. Recent advances in chemical sensors-spanning electrical, electrochemical, and optical modalities-enable more granular detection of contaminants or material inconsistencies. Simultaneously, gas sensors utilizing infrared absorption, metal-oxide semiconductors, and photoionization techniques identify volatile compounds in real time. Proximity sensors now blend inductive, optical, and ultrasonic methods to map three-dimensional geometries with sub-millimeter precision.
Machine vision and navigation have also matured. Centralized control software orchestrates complex multi-robot cells, while decentralized architectures distribute intelligence for fault tolerance. Dead reckoning remains a cost-effective navigation solution in structured environments, and SLAM (Simultaneous Localization and Mapping) empowers robots to navigate dynamic or unstructured workspaces. Furthermore, integration with digital twins and predictive analytics platforms has shifted inspection from isolated checkpoints to continuous monitoring.
In parallel, regulatory compliance and sustainability mandates are raising the bar for defect traceability and waste reduction. As robotic fleets become more connected via Ethernet, USB, Bluetooth, and Wi-Fi, enterprises can harness IIoT data streams to refine inspection protocols. These converging trends underscore a new era in which inspection robots not only detect anomalies but also drive holistic process optimization.
Analyzing the Cumulative Impact of United States Tariffs in 2025 on Smart Inspection Robotics
The introduction of United States tariffs in 2025 has reshaped cost structures and supply chain strategies for smart inspection robotics. Tariffs levied on key components-such as high-precision steel, semiconductor chips, and advanced sensor modules-increased imported unit costs by double-digit percentages. As a result, manufacturers have pursued localized sourcing and slowed capital investments in regions severely affected by import duties.
In response, several robot producers relocated critical fabrication processes closer to end markets, balancing tariff exposure against labor and infrastructure expenses. For instance, sensor integrators in North America expanded in-house production of metal-oxide gas detectors, while European firms diversified procurement to mitigate volatility. The cumulative impact of these measures has been a temporary contraction in equipment orders in tariff-sensitive segments, offset by growing demand for domestically assembled inspection solutions.
Simultaneously, suppliers with global manufacturing footprints leveraged internal transfer pricing and free-trade agreements to shield customers from full tariff pass-through. This strategic flexibility has highlighted the importance of agile supply chains and cross-border partnerships. Looking ahead, industry leaders are evaluating long-term tariff scenarios and investing in tariff-resilient architectures, such as modular sensor packages that can be sourced or reconfigured within multiple trade zones.
Key Segmentation Insights: Sensor, Design, Software, Industry, Power, Payload, Connectivity, and Application
A nuanced examination of market segments reveals differentiated growth trajectories. Sensor technology encompasses chemical detectors-spanning electrical, electrochemical, and optical designs-as well as gas sensors utilizing infrared absorption, metal-oxide semiconductors, and photoionization techniques. Proximity sensing capabilities draw from inductive, optical, and ultrasonic modules. In terms of robot design, articulated platforms include six-axis and multi-axis arms optimized for intricate assembly inspections, while crawler configurations offer legged variants that combine bipedal or quadrupedal mobility with tracked or wheeled bases for uneven terrain.
On the software front, control systems range from centralized orchestration frameworks to decentralized, edge-based architectures that deliver resilience against network disruptions. Navigation software further bifurcates into time-tested dead reckoning approaches and advanced SLAM (Simultaneous Localization and Mapping) implementations for dynamic environments. End-use industries span aerospace with dedicated assembly and maintenance protocols, automotive focused on inspection and production workflows, and electronics where PCB inspection and semiconductor manufacturing demand micron-level precision.
Power preferences divide between battery-powered platforms, leveraging lithium-ion or nickel-metal hydride chemistries, and environmentally friendly solar-powered solutions for remote applications. Payload categories differentiate heavy-duty robots handling 10–20 kg or above 20 kg from light-duty counterparts in the 5–10 kg or sub-5 kg classes. Connectivity options include wired interfaces-Ethernet and USB-alongside wireless links via Bluetooth or Wi-Fi. Finally, application areas range from facility management tasks such as energy auditing and HVAC maintenance to infrastructure inspection scenarios including bridge and pipeline evaluations.
This comprehensive research report categorizes the Train Smart Inspection Robot market into clearly defined segments, providing a detailed analysis of emerging trends and precise revenue forecasts to support strategic decision-making.
- Sensor Technology
- Robot Design
- Software Components
- End-Use Industry
- Power Source
- Payload Capacity
- Connectivity
- Application Area
Key Regional Insights Shaping Smart Inspection Robot Adoption Worldwide
Regional dynamics continue to influence the adoption and customization of inspection robots across three primary markets. In the Americas, a robust manufacturing base combined with incentives for domestic automation has led to early adoption of heavy-duty crawlers for aerospace maintenance and light-duty articulated arms in electronics production. North American suppliers have optimized supply chains to mitigate recent tariff pressures, fostering partnerships that blend local assembly with global component sourcing.
Europe, the Middle East & Africa exhibit strong demand for decentralized control software and SLAM-capable platforms, driven by the need to inspect legacy infrastructure in harsh environments. Government funding programs in the European Union support integration of wireless sensors for energy auditing and pipeline integrity checks. Middle Eastern oil and gas operators are deploying crawler robots with bipedal and quadrupedal configurations to access confined spaces.
In Asia-Pacific, rapid expansion of automotive and semiconductor facilities underscores the importance of centralized orchestration frameworks paired with high-resolution chemical and gas detection. Battery-powered robots predominate due to flexible deployment requirements, while solar-powered systems gain traction in remote infrastructure monitoring. Regional integrators have tailored solutions for PCB inspection and assembly line quality checks, reinforcing the area’s status as a global hub for inspection automation.
This comprehensive research report examines key regions that drive the evolution of the Train Smart Inspection Robot market, offering deep insights into regional trends, growth factors, and industry developments that are influencing market performance.
- Americas
- Asia-Pacific
- Europe, Middle East & Africa
Leading Company Profiles Highlighting Innovation and Market Leadership
The competitive landscape features established industrial automation giants and specialized robotics innovators collaborating to push inspection capabilities forward. ABB Ltd combines deep experience in six-axis articulated arms with digital twin integration for end-to-end traceability. Adept Technology, Inc. leverages miniature proximity sensors and decentralized control architectures to serve electronics manufacturers. Bosch Rexroth AG focuses on modular crawler platforms optimized for infrastructure inspections under extreme conditions.
Cognex Corporation and SICK AG partner to marry high-resolution vision systems with metal-oxide and infrared gas detection, enhancing defect identification. Fanuc Corporation and Yaskawa Electric Corporation continue to refine multi-axis kinematics for high-speed PCB inspection, while Faro Technologies, Inc. addresses metrology challenges with portable SLAM-enabled scanners. GE Appliances, a Haier Company integrates battery-powered robots into appliance assembly lines, and Honeywell International Inc. offers wireless sensor networks for HVAC maintenance.
KUKA AG, Mitsubishi Electric Corporation, and Omron Corporation champion centralized control software that scales across diverse payload capacities and connectivity standards. Rockwell Automation, Inc. and Schneider Electric SE excel in combining Ethernet-based orchestration with USB-linked peripheral modules. Siemens AG and Universal Robots A/S both emphasize collaborative inspection robots that safely operate alongside human workers, unlocking new hybrid workflow efficiencies.
This comprehensive research report delivers an in-depth overview of the principal market players in the Train Smart Inspection Robot market, evaluating their market share, strategic initiatives, and competitive positioning to illuminate the factors shaping the competitive landscape.
- ABB Ltd
- Adept Technology, Inc.
- Bosch Rexroth AG
- Cognex Corporation
- Fanuc Corporation
- Faro Technologies, Inc.
- GE Appliances, a Haier Company
- Honeywell International Inc.
- KUKA AG
- Mitsubishi Electric Corporation
- Omron Corporation
- Rockwell Automation, Inc.
- Schneider Electric SE
- SICK AG
- Siemens AG
- Universal Robots A/S
- Yaskawa Electric Corporation
Actionable Recommendations for Industry Leaders to Capitalize on Inspection Robotics
Industry leaders should prioritize sensor fusion strategies that integrate chemical, gas, and proximity data streams to unlock higher defect detection rates. Investing in modular robot architectures-capable of swapping between six-axis arms and crawler frames-will enhance responsiveness to diverse inspection environments. Firms should negotiate multi-zone manufacturing partnerships to mitigate tariff exposure and maintain cost competitiveness.
Adopting hybrid control software that combines centralized orchestration for precision tasks with decentralized edge intelligence for resilience will reduce downtime and optimize throughput. Organizations must also expand skill development initiatives, equipping engineers with expertise in SLAM, AI-driven anomaly classification, and remote diagnostic tools. Collaborations with metrology specialists can accelerate the validation of novel sensor technologies, while co-innovation agreements with semiconductor fabs will ensure early access to advanced detection modules.
Finally, executives should deploy pilot programs in key end-use segments-such as aerospace maintenance and pipeline inspection-to validate ROI under real-world conditions. These trials will inform scaling strategies, refine safety protocols, and create compelling case studies that drive broader adoption across the enterprise.
Explore AI-driven insights for the Train Smart Inspection Robot market with ResearchAI on our online platform, providing deeper, data-backed market analysis.
Ask ResearchAI anything
World's First Innovative Al for Market Research
Conclusion: Advancing Operational Excellence with Smart Inspection Robotics
Smart inspection robots have transitioned from experimental novelties to mission-critical assets that drive quality, efficiency, and safety across manufacturing sectors. By harnessing advances in sensor technology, modular robot design, and AI-enabled navigation, organizations can achieve unprecedented defect detection precision while reducing inspection cycle times. Resilient supply chain architectures and strategic tariff mitigation have proven essential to maintaining cost discipline amid shifting trade policies.
As companies integrate inspection fleets into broader Industry 4.0 initiatives, continuous data streams from decentralized control systems and SLAM-equipped platforms will inform predictive maintenance schedules and adaptive process controls. Regional insights highlight the necessity of tailoring solutions to specific regulatory and environmental requirements, whether in North American electronics plants, European infrastructure networks, or Asia-Pacific semiconductor fabs.
Ultimately, future competitiveness will hinge on the ability to orchestrate human-robot collaboration, leverage modular payload capacities, and scale software frameworks that bridge edge intelligence with enterprise analytics. Organizations that embrace these principles will unlock new levels of operational excellence and set the standard for the next generation of manufacturing quality assurance.
This section provides a structured overview of the report, outlining key chapters and topics covered for easy reference in our Train Smart Inspection Robot market comprehensive research report.
- Preface
- Research Methodology
- Executive Summary
- Market Overview
- Market Dynamics
- Market Insights
- Cumulative Impact of United States Tariffs 2025
- Train Smart Inspection Robot Market, by Sensor Technology
- Train Smart Inspection Robot Market, by Robot Design
- Train Smart Inspection Robot Market, by Software Components
- Train Smart Inspection Robot Market, by End-Use Industry
- Train Smart Inspection Robot Market, by Power Source
- Train Smart Inspection Robot Market, by Payload Capacity
- Train Smart Inspection Robot Market, by Connectivity
- Train Smart Inspection Robot Market, by Application Area
- Americas Train Smart Inspection Robot Market
- Asia-Pacific Train Smart Inspection Robot Market
- Europe, Middle East & Africa Train Smart Inspection Robot Market
- Competitive Landscape
- ResearchAI
- ResearchStatistics
- ResearchContacts
- ResearchArticles
- Appendix
- List of Figures [Total: 32]
- List of Tables [Total: 1161 ]
Call to Action: Partner with Ketan Rohom to Unlock In-Depth Market Intelligence
To explore comprehensive insights on market segmentation, regional dynamics, leading companies, and actionable strategies, contact Ketan Rohom, Associate Director, Sales & Marketing. Engage his expertise to acquire the full market research report and empower your organization to implement cutting-edge inspection robotics solutions.
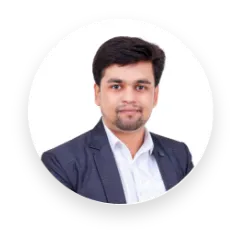
- When do I get the report?
- In what format does this report get delivered to me?
- How long has 360iResearch been around?
- What if I have a question about your reports?
- Can I share this report with my team?
- Can I use your research in my presentation?