Section 1: Introduction to the Global Tube Winder Market
The global tube winder market is evolving rapidly as manufacturers embrace automation, advanced composite materials, and precision winding techniques. Rising demand for lightweight, high-strength tubes across aerospace, electronics, medical, and industrial sectors is driving innovation in winding technology. Over the past decade, continuous improvements in filament winding, pultrusion, and tape laying have enabled producers to achieve higher throughput and tighter tolerances while reducing material waste. Simultaneously, manual and semi-automatic solutions remain relevant for specialized applications and low-volume production, ensuring flexibility for niche requirements.
Amid shifting supply chains and sustainability mandates, manufacturers are reassessing their equipment portfolios to balance cost, quality, and environmental impact. This executive summary offers a concise overview of the forces reshaping the tube winder industry, examining key market shifts, regulatory influences, customer preferences, and competitive dynamics. It equips decision-makers with the insights needed to navigate tariff headwinds, capitalize on emerging segments, and align operations with regional growth patterns. As we introduce each thematic element, the goal is to provide a coherent narrative that supports strategic planning and investment prioritization across the value chain.
Section 2: Transformative Shifts Driving the Tube Winder Industry
The tube winder landscape is in the midst of transformative change driven by technological breakthroughs and shifting end-user demands. Automation has transitioned from optional to essential, with fully automatic winding cells delivering repeatable results at speeds once unattainable by manual or semi-automatic systems. At the same time, composite winding techniques have moved beyond filament winding into hybrid approaches that integrate pultrusion and tape laying, enabling complex geometries and multi-material constructions.
Concurrently, sustainability imperatives are reshaping raw material selection and process design. Manufacturers are exploring recyclable thermoplastics and low-emission curing systems, prompted by customer and regulatory pressure to reduce carbon footprints. In parallel, digitalization is weaving through every stage of production: real-time monitoring, predictive maintenance algorithms, and simulation-driven process optimization are becoming standard practice rather than pilot experiments.
These converging trends are recalibrating cost structures and competitive positions. Companies that master advanced composite winding technology while maintaining flexibility for low-volume, high-customization runs will emerge as market leaders. The ability to pivot between filament winding, continuous and discontinuous pultrusion, and tape laying without sacrificing throughput or quality will define the next wave of industry frontrunners.
Section 3: Analysis of U.S. Tariff Impacts on Tube Winding Equipment
The imposition of new tariffs on imported tubes and winding equipment in 2025 has introduced a complex set of challenges and opportunities across the supply chain. Manufacturers sourcing winding machinery from abroad faced immediate cost increases, prompting many to renegotiate contracts or accelerate near-shoring initiatives. End-users sensitive to pricing began evaluating alternative suppliers, which in some cases accelerated partnerships with domestic equipment builders and local service providers.
Meanwhile, suppliers adapted by reconfiguring production footprints and expanding local assembly capabilities to mitigate tariff exposure. Some raw material producers responded by shifting resin and fiber production closer to key markets, optimizing logistics and reducing lead times. These adjustments, while initially costly, have enhanced supply chain resilience and fostered stronger ties between equipment manufacturers and end-users seeking turnkey solutions.
Importantly, the tariff landscape has underscored the value of flexible manufacturing strategies. Companies with modular equipment designs, configurable software platforms, and in-house engineering expertise have navigated the new regime more smoothly. As the dust settles, stakeholders are placing greater emphasis on strategic sourcing, robust supplier qualification processes, and cross-border collaboration to insulate operations from future trade disruptions.
Section 4: Critical Segmentation Insights Driving Targeted Strategies
A nuanced understanding of market segmentation is essential for targeting growth opportunities and tailoring product offerings. Based on product type, the industry encompasses automatic tube winders optimized for high-volume continuous operations, manual tube winders designed for prototyping or specialized tasks, and semi-automatic tube winders that bridge the gap between flexibility and throughput. Technological segmentation reveals a clear divide between conventional winding systems and advanced composite winding technology, the latter encompassing filament winding, pultrusion, and tape laying; pultrusion itself splits into continuous and discontinuous processes to serve varied production scales.
Looking at end-user industries, aerospace applications demand cable harnesses and composite components that withstand extreme conditions, while electronics producers focus on cable manufacturing and optical fiber production driven by data center and telecom growth. The industrial segment covers metal tubing production and paper processing, each with unique winding speeds and tension control requirements. In healthcare settings, catheter production and syringe manufacturing impose stringent cleanliness and precision standards. Textile applications, including thread manufacturing and yarn processing, lean on helical and layered winding methods to achieve consistent tension and uniform layering.
Application-based insights differentiate communication tubes, electrical conduits, packaging tubes, and structural components-packaging tubes further specialize into cosmetic and pharmaceutical packaging, while structural components include automobile tubing and construction pipes. Material preferences range from carbon fiber and glass fiber composite tubes to aluminum and stainless steel metallic tubes, and polyethylene and PVC plastic tubes. Production volume considerations span high, medium, and low volume production runs, influencing machine size, automation level, and changeover complexity. This multi-dimensional segmentation framework enables providers to align product development, service models, and sales strategies with precise customer requirements.
This comprehensive research report categorizes the Tube Winder market into clearly defined segments, providing a detailed analysis of emerging trends and precise revenue forecasts to support strategic decision-making.
- Product Type
- Technology
- End-User Industry
- Application
- Material
- Winding Method
- Production Volume
Section 5: Geographic Insights into Regional Market Dynamics
Regional dynamics play a pivotal role in shaping demand patterns, investment priorities, and competitive landscapes. In the Americas, robust infrastructure spending and expanding aerospace and automotive sectors are fueling demand for high-precision winding equipment. Domestic manufacturers have responded by enhancing service networks and establishing regional assembly hubs, cutting lead times and curbing import costs.
Europe, Middle East & Africa present a complex mosaic: stringent EU regulations on sustainability and emissions are accelerating the adoption of low-waste winding processes, while Middle Eastern petrochemical producers drive demand for metallic tube winding solutions. In Africa, burgeoning industrial projects in mining and construction create new opportunities for equipment suppliers that can offer modular, low-maintenance systems suitable for remote locations.
In Asia-Pacific, the rapid expansion of electronics manufacturing and renewable energy installations-particularly wind turbine blade production-has elevated the importance of advanced composite winding technology. Local governments in key markets are incentivizing domestic equipment production and R&D, leading to a proliferation of joint ventures and technology licensing agreements. The interplay of regulatory impetus, capital investment, and technological transfer in each region informs where companies should prioritize market entry and capacity expansion initiatives.
This comprehensive research report examines key regions that drive the evolution of the Tube Winder market, offering deep insights into regional trends, growth factors, and industry developments that are influencing market performance.
- Americas
- Asia-Pacific
- Europe, Middle East & Africa
Section 6: Competitive Landscape and Leading Industry Players
The competitive landscape is characterized by a diverse array of established OEMs and specialized equipment builders. ASHE Converting Equipment and Atlas Converting Equipment Ltd. lead in modular, high-precision winding cells, while Catbridge Machinery and Comexi Group Industries S.A.U. excel in custom solutions for the packaging and textile sectors. Deacro Industries Ltd. and Elite Cameron Ltd. offer robust manual and semi-automatic platforms favored by low-volume producers. GIFFORDS and Goebel Schneid- und Wickelsysteme GmbH have carved niches in pultrusion and tape-laying process integration.
Kimberly-Clark Professional and Laem System S.r.l. deliver turnkey systems that combine winding machinery with complementary converting equipment. Marchant Dice Ltd. and Marshall & Williams Plastics provide specialty winding machines tailored for high-temperature and chemical-resistant applications. Asian manufacturers such as Nishimura Mfg. Co., Ltd. and SP Ultraflex Systems Ltd. emphasize competitive pricing and rapid local support. Parkinson Technologies Inc. and Pasaban S.A. are renowned for innovation in filament winding controls, while Reifenhäuser Group and SOMA Engineering push the envelope on digitalization and Industry 4.0 integration.
Universal Converting Equipment and Valmet Oyj round out the field with platforms designed for scale-up and continuous operation, often bundled with predictive maintenance services. Together, these companies define the technological benchmarks, service expectations, and price points that shape customer purchasing decisions globally.
This comprehensive research report delivers an in-depth overview of the principal market players in the Tube Winder market, evaluating their market share, strategic initiatives, and competitive positioning to illuminate the factors shaping the competitive landscape.
- ASHE Converting Equipment
- Atlas Converting Equipment Ltd.
- Catbridge Machinery
- Comexi Group Industries S.A.U.
- Deacro Industries Ltd.
- Elite Cameron Ltd.
- GIFFORDS
- Goebel Schneid- und Wickelsysteme GmbH
- Kimberly-Clark Professional
- Laem System S.r.l.
- Marchant Dice Ltd.
- Marshall & Williams Plastics
- Nishimura Mfg. Co., Ltd.
- Parkinson Technologies Inc.
- Pasaban S.A.
- Reifenhäuser Group
- SOMA Engineering
- SP Ultraflex Systems Ltd.
- Universal Converting Equipment
- Valmet Oyj
Section 7: Actionable Recommendations for Market Leadership
To capitalize on emerging opportunities and navigate trade disruptions, industry leaders should adopt a multi-pronged strategy. First, invest in modular equipment architectures that support rapid changeovers and multi-material winding to meet evolving customer demands without extensive capital outlays. Second, develop local assembly and service capabilities in tariff-affected markets to minimize duty exposure and strengthen regional customer relationships.
Third, prioritize digital transformation by integrating IoT sensors, predictive analytics, and remote monitoring into winding platforms; these enhancements not only improve uptime but also create new revenue streams through service contracts. Fourth, partner with raw material suppliers to co-develop recyclable resin systems and energy-efficient curing methods, aligning product portfolios with tightening sustainability regulations.
Fifth, refine go-to-market approaches by leveraging the detailed segmentation framework: tailor sales engagements according to product type, technology preference, end-user application, material requirements, and production volume. Finally, build strategic alliances with regional distributors and end-user consortiums to capture early insights into infrastructure projects, aerospace contracts, and telecommunication rollouts, ensuring equipment roadmaps remain aligned with long-term market trajectories.
Explore AI-driven insights for the Tube Winder market with ResearchAI on our online platform, providing deeper, data-backed market analysis.
Ask ResearchAI anything
World's First Innovative Al for Market Research
Section 8: Conclusion and Strategic Imperatives
The tube winder industry stands at a crossroads where technological innovation, regulatory pressures, and geopolitical developments intersect. Companies that proactively embrace advanced composite winding methods, digitalization, and sustainable practices will differentiate themselves in a competitive environment shaped by tariffs and shifting supply chains. By leveraging detailed segmentation and regional insights, equipment providers can align product development and service delivery with the unique needs of aerospace, electronics, medical, industrial, and textile customers.
Building flexible, modular platforms not only mitigates the risks associated with trade policies but also enhances the agility required to serve low-volume, high-customization applications. Similarly, strengthening local assembly and support networks in the Americas, Europe, Middle East & Africa, and Asia-Pacific regions will reduce lead times and improve customer satisfaction.
Ultimately, success hinges on collaboration-uniting cross-functional expertise in engineering, sustainability, data analytics, and sales to deliver holistic winding solutions. As the market evolves, maintaining a pulse on tariff developments, material innovations, and end-user trends will ensure that strategic investments deliver maximum return and sustainable growth.
This section provides a structured overview of the report, outlining key chapters and topics covered for easy reference in our Tube Winder market comprehensive research report.
- Preface
- Research Methodology
- Executive Summary
- Market Overview
- Market Dynamics
- Market Insights
- Cumulative Impact of United States Tariffs 2025
- Tube Winder Market, by Product Type
- Tube Winder Market, by Technology
- Tube Winder Market, by End-User Industry
- Tube Winder Market, by Application
- Tube Winder Market, by Material
- Tube Winder Market, by Winding Method
- Tube Winder Market, by Production Volume
- Americas Tube Winder Market
- Asia-Pacific Tube Winder Market
- Europe, Middle East & Africa Tube Winder Market
- Competitive Landscape
- ResearchAI
- ResearchStatistics
- ResearchContacts
- ResearchArticles
- Appendix
- List of Figures [Total: 30]
- List of Tables [Total: 857 ]
Section 9: Call-to-Action to Engage with Ketan Rohom for the Full Report
Unlock deeper insights and a comprehensive roadmap for growth by securing the full market research report today. Reach out to Ketan Rohom, Associate Director, Sales & Marketing, for a personalized consultation and tailored quote. Elevate your strategic planning with data-driven analysis and actionable intelligence designed to position your organization at the forefront of the tube winder industry.
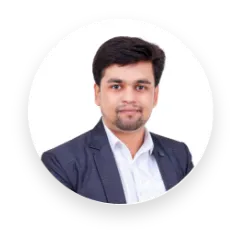
- When do I get the report?
- In what format does this report get delivered to me?
- How long has 360iResearch been around?
- What if I have a question about your reports?
- Can I share this report with my team?
- Can I use your research in my presentation?