Unleashing the Power of Pumped Sputtering for Next-Generation Coatings
Pumped sputtering deposition coater technology stands at the forefront of advanced surface engineering processes, enabling precise thin film coatings across a diverse spectrum of industries. This sophisticated method leverages a controlled plasma environment to deposit uniform layers of metals, oxides, nitrides, or semiconductor materials onto substrates. The resulting films exhibit superior adhesion, enhanced durability, and tailored optical or electrical properties, making this technology indispensable within sectors that demand exacting performance standards.
Recent advancements in power supply design, process control, and vacuum instrumentation have propelled pumped sputtering systems into new realms of capability. Innovations such as high-power pulsed DC supplies and hybrid magnetron configurations have optimized deposition rates while preserving film integrity. As manufacturers confront ever-evolving material requirements-from ultra-thin transparent conductive layers for display panels to robust wear-resistant coatings for aerospace components-the pumped sputtering deposition coater has emerged as a versatile, reliable solution.
Within this report’s executive summary, readers will uncover transformative technological shifts reshaping the landscape, assess the implications of impending tariff measures, and explore high-value segmentation insights. Strategic recommendations for decision-makers and a thorough exposition of regional and competitive dynamics ensure that stakeholders gain a comprehensive understanding of this dynamic market.
Navigating Transformative Shifts Shaping Deposition Coater Technologies
Innovation trajectories in pumped sputtering deposition have undergone a paradigm shift as demand for miniaturized electronics and sustainable manufacturing intensified. Leading equipment OEMs have integrated real-time analytics into their coater platforms, enabling closed-loop monitoring of plasma uniformity and substrate temperature. This fusion of digital instrumentation with advanced deposition modules has unlocked new levels of process repeatability. Consequently, manufacturers can achieve tighter thickness tolerances and richer compositional control without sacrificing throughput.
Concurrently, the ascendancy of flexible electronics and curved displays has spurred the development of low-temperature sputtering processes that accommodate polymer and metal substrates. These breakthroughs have catalyzed adoption in consumer electronics segments, where form factor innovation is paramount. Meanwhile, the drive toward energy-efficient photovoltaics has encouraged exploration of novel metal oxide targets, optimizing optical bandgaps for enhanced light absorption. As Industry 4.0 principles permeate R&D and production lines, interoperability between sputtering tools and factory-wide automation systems continues to evolve, heralding a new era of agile, data-driven deposition coater operations.
Assessing the Ripple Effects of 2025 US Tariff Measures on Sputtering Markets
With the introduction of new United States tariffs in 2025, supply chains for pumped sputtering equipment and critical target materials face unprecedented complexity. Components such as power supplies, vacuum pumps, and control modules sourced from overseas suppliers may encounter elevated import duties, driving up acquisition costs. In response, OEMs and end users alike are reassessing sourcing strategies, with some electing to diversify supplier portfolios or explore regional manufacturing partnerships to mitigate tariff exposure and maintain budgetary discipline.
These trade measures have also prompted recalibration of product roadmaps. Companies prioritizing high-value segments-such as semiconductors and flat panel displays-are particularly sensitive to cost pressures and may accelerate efforts to localize production of key assemblies. Yet even as manufacturers adjust procurement and operational footprints, the broader industry remains committed to preserving technological edge. Incremental cost increases are likely to be offset by process efficiency gains and strategic investments in automation, ensuring that the long-term trajectory of pumped sputtering adoption remains on a growth path despite short-term trade challenges.
Decoding Market Layers Through Multifaceted Segmentation Perspectives
An in-depth examination of application tiers reveals that decorative coating demands precise color fidelity and corrosion resistance for consumer goods, while flat panel displays leverage advanced thin films for LCD and OLED screens that require exceptional uniformity across large substrates. Hard coating applications in tools and machinery benefit from optimized tribological properties, whereas optical components necessitate films with tailored refractive indices. Photovoltaic modules depend on transparent conductive oxides to balance conductivity with light transmittance, and semiconductor use cases span integrated circuits, memory devices, and sensor platforms, each demanding its own deposition recipe.
Target material considerations further refine equipment selection, as processes handling metal oxides must account for target poisoning, and metallic sputtering must ensure high purity to meet conductivity benchmarks. Nitrides require reactive sputtering capabilities, and semiconductor targets call for contamination control at sub-ppm levels. Process architectures vary from DC and RF systems to ion beam and magnetron approaches, with pulsed DC solutions bridging the gap between traditional direct current and high-frequency alternatives. System configuration also plays a pivotal role, as batch tools support research flexibility, cluster tools enable multi-chamber throughput, inline designs favor continuous production, and load lock setups minimize vacuum cycle times.
Substrate diversity encompasses glass panes for displays, metal sheets for architectural finishes, polymers for flexible devices, and silicon wafers for chip fabrication, each introducing unique thermal and mechanical constraints. Power supply footprints range from compact units delivering under two kilowatts for prototyping to robust sources exceeding ten kilowatts for large-area deposition. End user dynamics highlight aerospace and automotive requirements for lightweight, durable coatings, electronics demands across consumer and industrial segments for miniaturized film stacks, and healthcare needs for sterile, biocompatible surfaces. This intricate segmentation matrix underscores the strategic importance of configuring pumped sputtering systems to align with precise market demands.
This comprehensive research report categorizes the Turbo - Pumped Sputtering Deposition Coater market into clearly defined segments, providing a detailed analysis of emerging trends and precise revenue forecasts to support strategic decision-making.
- Application
- Target Material
- Process Type
- System Configuration
- Substrate
- Power Supply
- End User
Unearthing Regional Dynamics Highlighting Global Growth Pathways
Regional demand patterns for pumped sputtering deposition equipment diverge significantly across global markets. In the Americas, robust growth in semiconductor capital expenditure and automotive electronics integration has fueled investments in both research-grade and high-volume sputtering platforms. The emphasis on reshoring manufacturing and developing domestic supply chains has further amplified equipment procurement. In the Europe, Middle East & Africa territory, stringent regulatory frameworks and sustainability mandates have accelerated adoption of low-temperature processes and recycling programs for sputtering targets, while collaborative research initiatives have driven coater innovation in optics and photovoltaics.
Across the Asia-Pacific region, rapid expansion of consumer electronics manufacturing hubs and renewable energy deployments has positioned pumped sputtering as a critical enabler. Strategic government incentives for local component fabrication have attracted foreign direct investment in deposition tool production. Meanwhile, rising demand for flexible displays and next-generation sensors has prompted regional OEMs to form technology partnerships with global equipment providers, creating a dynamic ecosystem of co-development and localization that continues to reshape competitive positioning.
This comprehensive research report examines key regions that drive the evolution of the Turbo - Pumped Sputtering Deposition Coater market, offering deep insights into regional trends, growth factors, and industry developments that are influencing market performance.
- Americas
- Europe, Middle East & Africa
- Asia-Pacific
Spotlight on Leading Innovators Driving Pumped Sputtering Advances
Competitive rivalry within the pumped sputtering deposition coater market has intensified as both established players and agile challengers vie for leadership. Major equipment manufacturers have pursued forward integration by incorporating advanced automation modules and in situ metrology options into their tool offerings, aiming to differentiate through value-added functionalities. Strategic alliances between vacuum pump suppliers and control system providers have further enhanced system interoperability, raising the bar for turnkey solutions.
At the same time, emerging companies with specialized expertise in pulsed DC sources and high-speed magnetron arrays have carved out niches in research and pilot production segments. These innovators often emphasize modular tool architectures and rapid reconfiguration, appealing to customers operating across multiple material systems. Mergers and acquisitions have also played a role in consolidating technological assets, enabling incumbents to absorb cutting-edge process patents and expand aftermarket service networks. The resulting landscape demands that market participants continuously refine their value propositions through rigorous product roadmaps and strategic partnerships.
This comprehensive research report delivers an in-depth overview of the principal market players in the Turbo - Pumped Sputtering Deposition Coater market, evaluating their market share, strategic initiatives, and competitive positioning to illuminate the factors shaping the competitive landscape.
- Applied Materials, Inc.
- ULVAC, Inc.
- Veeco Instruments Inc.
- AJA International, Inc.
- Angstrom Engineering Inc.
- Kurt J. Lesker Company
- Denton Vacuum LLC
- Hauzer Techno Coating B.V.
- Plasma-Therm LLC
- Plasmion S.A.
Strategic Imperatives to Propel Your Coating Operations Forward
To capitalize on the momentum of pumped sputtering adoption, industry stakeholders should prioritize end-to-end process integration by implementing unified control software that harmonizes deposition parameters with factory automation systems. This holistic approach will streamline production workflows and reduce error rates. Moreover, decision-makers are advised to cultivate strategic supplier relationships that deliver co-development opportunities for next-generation target materials and cathode designs, ensuring early access to performance breakthroughs and cost optimizations.
Investment in workforce training and digital competency is equally critical; establishing cross-functional teams versed in plasma physics, materials science, and data analytics will enable organizations to extract maximal value from advanced coater platforms. Furthermore, organizations should evaluate regional tariff exposure and develop agile procurement frameworks that can pivot between global suppliers and localized manufacturing partnerships. Lastly, sustainability considerations must be woven into tool selection and operational protocols, leveraging energy-efficient power supplies and closed-loop target recycling to meet environmental objectives while maintaining competitive cost structures.
Rigorous Methodological Framework Underpinning Our Analysis
This analysis synthesizes insights from comprehensive secondary research, including patent databases, industry journals, and regulatory filings, alongside primary interviews with equipment OEM executives, process engineers, and end-user technical leads. The methodological framework emphasizes data triangulation and cross-validation to ensure that key trends, technological breakthroughs, and market dynamics are anchored in verifiable evidence rather than anecdotal observations.
Quantitative metrics were derived through detailed audits of component shipment records and capital expenditure disclosures, while qualitative inputs stemmed from workshops and expert roundtables that assessed emerging material systems and process innovations. Regional market drivers were mapped against policy landscapes and investment flows to capture the interplay between regulatory incentives and commercial adoption. By integrating both top-down and bottom-up perspectives, this report achieves a balanced, robust portrayal of the pumped sputtering deposition coater ecosystem.
Explore AI-driven insights for the Turbo - Pumped Sputtering Deposition Coater market with ResearchAI on our online platform, providing deeper, data-backed market analysis.
Ask ResearchAI anything
World's First Innovative Al for Market Research
Synthesizing Insights to Chart the Future of Deposition Coating
Bringing together the latest technological trends, tariff landscape shifts, and segmentation insights, this executive summary offers a holistic view of the pumped sputtering deposition coater market. It underscores how advanced process controls and diversified system architectures are meeting the exacting demands of applications ranging from semiconductor fabrication to flexible electronics. The report also highlights how trade policy developments are prompting strategic realignments in supplier networks and manufacturing geographies.
Ultimately, stakeholders are equipped with a clear understanding of the competitive environment, regional growth opportunities, and the critical success factors necessary for sustained leadership. This conclusion sets the stage for targeted decision-making, ensuring that organizations can harness the combined power of innovative technologies, strategic partnerships, and agile operational models to thrive in an increasingly complex and dynamic market.
This section provides a structured overview of the report, outlining key chapters and topics covered for easy reference in our Turbo - Pumped Sputtering Deposition Coater market comprehensive research report.
- Preface
- Research Methodology
- Executive Summary
- Market Overview
- Market Dynamics
- Market Insights
- Cumulative Impact of United States Tariffs 2025
- Turbo - Pumped Sputtering Deposition Coater Market, by Application
- Turbo - Pumped Sputtering Deposition Coater Market, by Target Material
- Turbo - Pumped Sputtering Deposition Coater Market, by Process Type
- Turbo - Pumped Sputtering Deposition Coater Market, by System Configuration
- Turbo - Pumped Sputtering Deposition Coater Market, by Substrate
- Turbo - Pumped Sputtering Deposition Coater Market, by Power Supply
- Turbo - Pumped Sputtering Deposition Coater Market, by End User
- Americas Turbo - Pumped Sputtering Deposition Coater Market
- Europe, Middle East & Africa Turbo - Pumped Sputtering Deposition Coater Market
- Asia-Pacific Turbo - Pumped Sputtering Deposition Coater Market
- Competitive Landscape
- ResearchAI
- ResearchStatistics
- ResearchContacts
- ResearchArticles
- Appendix
- List of Figures [Total: 30]
- List of Tables [Total: 469 ]
Take the Next Step with Ketan Rohom for Customized Market Intelligence
To explore the full breadth of insights and actionable strategies contained in this comprehensive market research report, engage directly with Ketan Rohom, Associate Director, Sales & Marketing. His expertise will guide you through tailored solutions and bespoke analyses that align with your organization’s strategic priorities. By partnering with Ketan, you’ll gain priority access to in-depth competitive intelligence, segmentation deep dives, and regional dynamics that can refine your growth trajectory. Secure the definitive resource on pumped sputtering deposition coater technologies and transform data into decisive advantage by contacting Ketan Rohom today
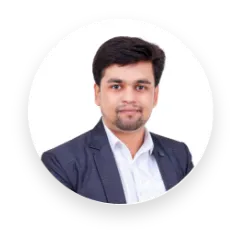
- When do I get the report?
- In what format does this report get delivered to me?
- How long has 360iResearch been around?
- What if I have a question about your reports?
- Can I share this report with my team?
- Can I use your research in my presentation?