Revolutionizing High-Purity Fluid Handling for Next-Gen Chips
The relentless pursuit of miniaturization and performance in semiconductor manufacturing has placed ultra high purity stainless steel fittings at the forefront of technology infrastructure. As chip geometries shrink and contamination tolerances tighten to the atomic scale, traditional fluid handling components no longer meet the rigorous demands of advanced wafer fabrication. Ultra high purity stainless steel fittings deliver the chemical inertness, exceptional cleanliness, and mechanical integrity required to maintain pristine process environments.
This introduction outlines the critical role these specialized fittings play across each stage of semiconductor processing, from chemical mechanical planarization and deposition to photolithography and etching. By eliminating particle generation and trace-metal ion leaching, these components safeguard product yields and enhance process reliability. The remainder of this report presents a comprehensive analysis of recent industry shifts, tariff impacts, key segmentation and regional trends, major market participants, and actionable recommendations to navigate the evolving landscape of ultra high purity stainless steel fittings in semiconductor production.
Emerging Dynamics Redefining Ultra High Purity Component Requirements
Semiconductor manufacturing is experiencing transformative shifts driven by technological innovation and evolving market demands. The rise of advanced packaging techniques, such as 3D integration and heterogeneous integration, has heightened the need for fittings that withstand aggressive chemistries while maintaining ultra low particulate generation. Concurrently, environmental sustainability initiatives are prompting fabs to adopt closed-loop chemical systems that rely on fittings capable of enduring frequent cleaning cycles without compromise.
Artificial intelligence and machine learning are also making their mark on fab operations, enabling predictive maintenance strategies that flag early signs of component degradation. These digital tools demand fittings with consistent performance metrics and traceable quality documentation. Moreover, the transition toward larger wafer sizes further escalates fluid flow volumes and pressures, placing greater emphasis on robust end connection types and pressure rating capabilities. As a result, manufacturers are recalibrating their R&D roadmaps to deliver fittings that align with these disruptive shifts and support the next wave of semiconductor innovation.
Navigating the Tariff-Driven Supply Chain Realignment
The introduction of cumulative tariffs in 2025 has reshaped the global supply chain for ultra high purity stainless steel fittings, compelling stakeholders to reassess sourcing strategies and cost structures. Tariff impositions on raw stainless steel and finished fittings have elevated input costs and compressed margins, prompting some manufacturers to relocate production closer to key semiconductor hubs or to diversify their supplier base beyond traditional trade partners.
These trade measures have also led to fluctuating inventory levels as companies seek to hedge against further tariff escalations, resulting in intermittent supply constraints that ripple through wafer fabrication facilities. In response, leading wafer foundries and chemical delivery system integrators are negotiating long-term agreements with domestic and regional producers to secure preferential pricing and mitigate logistical uncertainties. While these shifts introduce near-term cost pressures, they have simultaneously spurred innovation in metallurgical alloys and fabrication methods, yielding fittings that better resist corrosion and maintain integrity under repetitive cleaning regimens, ultimately reinforcing supply chain resilience.
Dissecting Market Segments to Pinpoint Growth Trajectories
The market’s complexity becomes apparent when examining how end connection types dictate performance and compatibility. Clamp connections, whether Iso Kf or Tri Clover, excel in modular assemblies and rapid maintenance, whereas compression variants featuring double ferrule and single ferrule designs ensure precise, leak-free seals. Slip On and Weld Neck flanges deliver high structural integrity for demanding process lines, while butt weld and socket weld connections offer seamless flow paths that minimize contamination risk. In parallel, fitting types such as adapters, couplings, crosses, elbows, tees, unions, and valves each address specific routing, flow control, and assembly requirements, creating a versatile toolkit for system architects.
Material grade selection further refines performance parameters: the stainless steel 300 Series balances cost and corrosion resistance, 400 Series provides enhanced strength, duplex and super duplex grades push the envelope in mechanical durability and chemical endurance, and nickel alloys cater to the most aggressive chemistries. Application-specific demands-from chemical mechanical planarization through chemical vapor deposition, deposition, etching, and photolithography to wafer cleaning-drive fitting geometry and surface finish specifications. Finally, pressure rating categories, spanning low pressure to medium and high pressure, align with the varied flow rates and containment needs of modern semiconductor process steps, underscoring the importance of precise segmentation in market strategy.
This comprehensive research report categorizes the Ultra High Purity Stainless Steel Fittings for Semiconductor market into clearly defined segments, providing a detailed analysis of emerging trends and precise revenue forecasts to support strategic decision-making.
- End Connection Type
- Fitting Type
- Material Grade
- Application
- Pressure Rating
How Regional Forces Shape Ultra High Purity Fittings Demand
Regional dynamics exert a profound influence on market evolution as semiconductor clusters expand and regulatory landscapes diverge. In the Americas, established wafer fabrication hubs in the United States and emerging capacity in Mexico are driving sustained demand for high-purity fittings capable of supporting advanced node production. Meanwhile, in Europe, Middle East & Africa, stringent environmental and safety standards in Germany, France, and the United Kingdom are elevating the quality bar for fluid handling components, while nascent fabs in the Middle East explore domestic supply partnerships to localize critical infrastructure.
Asia-Pacific remains the powerhouse of semiconductor manufacturing, with Taiwan, South Korea, Japan, and China spearheading capacity expansions for both logic and memory applications. The region’s rapid fab build-outs and aggressive adoption of cutting-edge process technologies sustain unparalleled demand for ultra high purity connections. Concurrent regional trade agreements and tiered incentives are reshaping procurement strategies, as fab operators seek to stabilize costs while ensuring compliance with evolving import regulations, further reinforcing Asia-Pacific’s central role in the global fittings market.
This comprehensive research report examines key regions that drive the evolution of the Ultra High Purity Stainless Steel Fittings for Semiconductor market, offering deep insights into regional trends, growth factors, and industry developments that are influencing market performance.
- Americas
- Europe, Middle East & Africa
- Asia-Pacific
Competitive Landscape Insights and Innovation Drivers
The competitive landscape is anchored by established engineering specialists and materials innovators, each vying to deliver unmatched cleanliness standards and traceable quality. Leading industrial suppliers have expanded their portfolios to include enhanced surface passivation, electropolishing processes, and proprietary alloy formulations that address the full spectrum of semiconductor applications. Strategic partnerships with fab OEMs and chemical delivery system integrators have enabled these companies to co-develop next-generation fittings that integrate sensor ports and RFID traceability for advanced process monitoring.
At the same time, emerging challengers leverage lean manufacturing and digital platforms to offer custom-configured fittings with rapid lead times, appealing to smaller fabs and R&D facilities. Mergers, acquisitions, and joint ventures continue to reshape market share distribution, as players pursue geographic expansion and specialized niche capabilities. Cross-industry collaborations, particularly with pharmaceutical and biotechnology fluid handling experts, are further accelerating product innovation, driving continuous enhancements in particulate control and chemical compatibility across the ultra high purity fittings ecosystem.
This comprehensive research report delivers an in-depth overview of the principal market players in the Ultra High Purity Stainless Steel Fittings for Semiconductor market, evaluating their market share, strategic initiatives, and competitive positioning to illuminate the factors shaping the competitive landscape.
- The Swagelok Company
- Parker-Hannifin Corporation
- Entegris, Inc.
- Fujikin Incorporated
- Asahi Kinzoku Corporation
- Hy-Lok Corporation
- Beijing DK Technic Co., Ltd.
- Uras Techno Co., Ltd.
- Taewon Metal Co., Ltd.
- Nikkiso Co., Ltd.
Strategic Imperatives to Seize Market Leadership
Industry leaders must prioritize a multifaceted strategy to capitalize on growth opportunities. First, accelerating investments in advanced surface treatments and metallurgical research will support the development of fittings that exceed emerging purity and durability requirements. Second, forging strategic alliances with wafer fab OEMs and chemical delivery integrators can secure early access to process roadmaps, enabling co-engineering of bespoke solutions. Third, establishing regional manufacturing or assembly capabilities-particularly in key Asia-Pacific clusters-will mitigate tariff exposure and improve responsiveness to dynamic demand shifts.
In addition, integrating digital traceability features such as embedded sensors or RFID tagging into fitting designs will facilitate predictive maintenance and quality assurance initiatives. Firms should also explore circular economy models, offering cleaning, refurbishment, and certification services to extend component lifecycles and reinforce sustainability credentials. Finally, aligning product portfolios with major environmental, health, and safety regulations by pursuing relevant certifications will strengthen market positioning and support long-term customer retention in stringent semiconductor environments.
Robust Research Framework Underpinning Our Analysis
This research integrates a hybrid methodology combining in-depth primary and secondary data collection, rigorous validation, and multi-layered analysis. Primary research encompassed structured interviews with semiconductor fab managers, fluid handling system integrators, and materials scientists to capture firsthand insights on performance requirements and emerging trends. Complementary site visits and product audits provided empirical evidence of fitting applications across deposition, etching, and cleaning modules.
Secondary research involved exhaustive review of industry publications, patent filings, regulatory standards, and corporate disclosures. Quantitative data was triangulated through cross-referencing trade databases, customs records, and company financial reports to ensure accuracy. Qualitative findings underwent peer review by subject matter experts, while demand and supply-side dynamics were validated through scenario mapping. This rigorous approach ensures the report’s conclusions and recommendations are grounded in objective evidence and reflect the latest developments in ultra high purity stainless steel fittings for semiconductor manufacturing.
Explore AI-driven insights for the Ultra High Purity Stainless Steel Fittings for Semiconductor market with ResearchAI on our online platform, providing deeper, data-backed market analysis.
Ask ResearchAI anything
World's First Innovative Al for Market Research
Key Takeaways for Future-Proofing Fluid Handling Strategies
Ultra high purity stainless steel fittings have emerged as indispensable enablers of semiconductor advancement, delivering the precise chemical resistance, mechanical integrity, and cleanliness demanded by next-gen node production. The convergence of tariff-induced supply realignments, regional manufacturing shifts, and transformative process innovations underscores the critical need for strategic agility. Through detailed segmentation and regional analysis, as well as competitive landscape insights, this report illuminates the myriad factors shaping market evolution.
As semiconductor roadmaps advance toward sub-3nm geometries and 3D integration architectures, the performance bar for fittings will only rise. Companies that embrace collaborative development models, invest in cutting-edge material science, and deploy localized manufacturing strategies will be best positioned to navigate uncertainty and capture emerging growth. This conclusion encapsulates the essential takeaways and highlights the pivotal role ultra high purity fittings will play in sustaining semiconductor progress for years to come.
This section provides a structured overview of the report, outlining key chapters and topics covered for easy reference in our Ultra High Purity Stainless Steel Fittings for Semiconductor market comprehensive research report.
- Preface
- Research Methodology
- Executive Summary
- Market Overview
- Market Dynamics
- Market Insights
- Cumulative Impact of United States Tariffs 2025
- Ultra High Purity Stainless Steel Fittings for Semiconductor Market, by End Connection Type
- Ultra High Purity Stainless Steel Fittings for Semiconductor Market, by Fitting Type
- Ultra High Purity Stainless Steel Fittings for Semiconductor Market, by Material Grade
- Ultra High Purity Stainless Steel Fittings for Semiconductor Market, by Application
- Ultra High Purity Stainless Steel Fittings for Semiconductor Market, by Pressure Rating
- Americas Ultra High Purity Stainless Steel Fittings for Semiconductor Market
- Europe, Middle East & Africa Ultra High Purity Stainless Steel Fittings for Semiconductor Market
- Asia-Pacific Ultra High Purity Stainless Steel Fittings for Semiconductor Market
- Competitive Landscape
- ResearchAI
- ResearchStatistics
- ResearchContacts
- ResearchArticles
- Appendix
- List of Figures [Total: 26]
- List of Tables [Total: 423 ]
Unlock Strategic Insights with Our In-Depth Market Report
Securing detailed, actionable insights into the ultra high purity stainless steel fittings landscape is crucial for staying ahead in semiconductor manufacturing. To gain comprehensive analysis on market dynamics, segmentation trends, and strategic imperatives, connect with Ketan Rohom, Associate Director, Sales & Marketing. His expertise will guide you through tailored solutions that address your unique business needs and help you unlock growth opportunities.
Reach out to arrange a personalized demonstration of the report’s findings and discover how elevated purity standards, evolving regulatory environments, and regional shifts can be leveraged to strengthen your supply chain and drive innovation.
Don’t miss the opportunity to elevate your strategic decision-making with this in-depth market research report. Collaborate with Ketan to secure your copy and position your organization at the forefront of ultra high purity stainless steel fittings for semiconductor applications
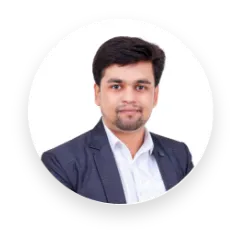
- When do I get the report?
- In what format does this report get delivered to me?
- How long has 360iResearch been around?
- What if I have a question about your reports?
- Can I share this report with my team?
- Can I use your research in my presentation?