Exploring the Unmatched Mechanical Performance and Growing Strategic Significance of Ultra-High Strength Aluminum Alloy Across Modern Industries
Ultra-high strength aluminum alloys represent a new frontier in lightweight materials engineering, delivering exceptional mechanical performance through tensile strengths often exceeding 700 MPa and fatigue resistance that outperforms conventional alloys. Recent advancements in processing-such as advanced powder metallurgy and hypersonic liquid atomization-have yielded experimental compositions like A-1500, which achieve tensile strengths beyond 1,200 MPa while retaining practical ductility above 5 percent thanks to nanoscale grain refinement and precise alloying with zinc, magnesium, and copper. These innovations build on the legacy of 7000-series alloys like 7075-T6 and 7068, which established the benchmark for high-performance applications in aerospace and defense.
How Novel Material Innovations and Regulatory Dynamics Are Rapidly Reshaping the Ultra-High Strength Aluminum Alloy Competitive Landscape
Regulatory and policy frameworks across major economies are driving a fundamental reconfiguration of the ultra-high strength aluminum alloy market. The European Union’s Circular Economy Action Plan mandates minimum recycled content thresholds, while China’s 2025 Industrial Green Development Plan compels non-ferrous industries to achieve rigorous recycling targets. Simultaneously, chemical substance regulations such as EU REACH and California Proposition 65 are restricting hazardous additives, compelling alloy producers to innovate eco-friendly compositions that maintain performance while ensuring compliance and market access.
Unpacking the Compound Effects of the 2025 United States Aluminum Tariff Escalations on Supply Chains and Cost Structures
The United States’ aluminum tariff regime underwent two significant escalations in 2025. On March 12, the Section 232 tariff rate for aluminum articles and derivatives was raised from 10 percent to 25 percent ad valorem, ending country exemptions and phasing out general approved exclusions under Proclamation 9959. A subsequent proclamation on June 4 further increased the rate to 50 percent ad valorem, while aligning tariff measures with the U.S.–UK Economic Prosperity Deal and modifying applicability for derivative articles to protect national security interests.
Illuminating Cross-Segment Demand Drivers and Application-Specific Performance Trends in the Ultra-High Strength Aluminum Alloy Market
Across end-use industries, aerospace remains the foremost adopter of ultra-high strength aluminum alloys, leveraging the material’s high strength-to-weight ratio for both commercial aircraft structures and military platforms, with primary uses spanning landing gear, fuselage skins, and critical fasteners. Automotive manufacturers divide their use between commercial vehicles and passenger cars, integrating these alloys into chassis frames and battery housings to boost safety and range efficiency. Construction applications are split between facades and structural components, where corrosion resistance and long-term durability are paramount. In defense, armor systems and weapons & ammunition benefit from alloys that deliver battlefield resilience, while marine applications extend to offshore platforms and shipbuilding, capitalizing on superior performance in harsh saltwater environments.
This comprehensive research report categorizes the Ultra-high Strength Aluminum Alloy market into clearly defined segments, providing a detailed analysis of emerging trends and precise revenue forecasts to support strategic decision-making.
- End-Use Industry
- Product Form
- Alloy Grade
- Production Method
- Sales Channel
Examining Regional Market Dynamics and Strategic Opportunities Across North America, Europe, Middle East & Africa, and Asia-Pacific Geographies
North America’s advanced aerospace and automotive sectors continue to underpin demand for ultra-high strength aluminum alloys, supported by strong domestic R&D, sustainable recycling initiatives, and investments in onshore smelting and fabrication capacity. The United States, in particular, is focused on energy cost mitigation and supply chain resilience to offset global volatility 【turn3search1】【turn6search2】. Europe, the Middle East & Africa region leverages mature regulatory frameworks such as the EU’s Circular Economy Action Plan and chemical safety directives to drive adoption of high-recycled-content alloys across automotive production in Germany, construction in the Gulf, and defense modernization programs in the UK and France. Asia-Pacific stands out with the most rapid growth, fueled by China’s extensive industrial expansion, India’s infrastructure investments under “Make in India,” and Japan’s aerospace initiatives, all supported by supportive government incentives and burgeoning EV and renewable energy projects.
This comprehensive research report examines key regions that drive the evolution of the Ultra-high Strength Aluminum Alloy market, offering deep insights into regional trends, growth factors, and industry developments that are influencing market performance.
- Americas
- Europe, Middle East & Africa
- Asia-Pacific
Profiling Leading Innovators and Sustainability Champions Driving the Evolution of Ultra-High Strength Aluminum Alloy Supply Chains
Alcoa has intensified its focus on alloy innovation and energy efficiency, unveiling the A210 ExtruStrong™ 6000-series extrusion alloy that delivers over 40 percent strength gains and reduced thickness for transport and construction applications. Its C611 EZCast™ alloy eliminates the need for dedicated heat treatment by achieving final properties through standard automotive paint-baking processes, thus cutting both energy use and manufacturing complexity. Constellium is bolstering its sustainable leadership through major circular economy initiatives such as the £10 million CirConAl project to develop ultra-low carbon, recycled-content extrusions, while simultaneously advancing additive manufacturing capabilities via its Aheadd® CP1 alloy in a U.S. Department of Defense-funded partnership to qualify aluminum powders for defense and aerospace components. Novelis remains the world’s leading rolling and recycling specialist, maintaining over 60 percent recycled content in its product portfolio and commissioning a $4.1 billion Bay Minette, Alabama facility to expand low-carbon rolling and recycling capacity in support of beverage packaging and automotive sheet customers worldwide.
This comprehensive research report delivers an in-depth overview of the principal market players in the Ultra-high Strength Aluminum Alloy market, evaluating their market share, strategic initiatives, and competitive positioning to illuminate the factors shaping the competitive landscape.
- Constellium SE
- Novelis Inc.
- Arconic Corporation
- Kaiser Aluminum Corporation
- UACJ Corporation
- Rio Tinto plc
- Norsk Hydro ASA
- China Zhongwang Holdings Limited
- Sumitomo Light Metal Industries, Ltd.
- Shandong Nanshan Aluminum Co., Ltd.
Strategic Imperatives and Actionable Roadmap for Industry Stakeholders Seeking to Harness Ultra-High Strength Aluminum Alloy Advantages
Pursue advanced materials R&D by collaborating with academic and national laboratory partners to develop next-generation alloy chemistries and processing routes, including hypersonic atomization and novel precipitate-strengthening mechanisms, to achieve tensile strengths surpassing 1,000 MPa without sacrificing ductility or corrosion resistance. Diversify supply chains and secure alternative sources of primary and recycled aluminum to mitigate the evolving Section 232 tariff landscape, leveraging existing trade agreements and optimizing domestic production capabilities to stabilize input costs and protect margins. Accelerate circular economy integration by investing in on-site recycling centers, advanced scrap sorting technologies, and partnerships across the value chain to meet regional minimum recycled content mandates and reduce overall carbon footprints, thereby unlocking new contract awards and regulatory incentives.
Comprehensive Methodological Framework Underpinning Market Insights Through Rigorous Primary and Secondary Research Techniques
This research combines a robust secondary research phase-encompassing government publications, trade association reports, technical journals, and corporate disclosures-with a comprehensive primary research program. Interviews were conducted with C-level executives, R&D directors, procurement managers, and sustainability officers across the value chain to validate market trends, segment dynamics, and regional nuances. Data triangulation and statistical modeling techniques, including top-down and bottom-up approaches, were applied to ensure consistency and reliability. Insights were subjected to peer review and expert validation to reinforce the credibility of conclusions and recommendations.
Explore AI-driven insights for the Ultra-high Strength Aluminum Alloy market with ResearchAI on our online platform, providing deeper, data-backed market analysis.
Ask ResearchAI anything
World's First Innovative Al for Market Research
Drawing Conclusive Perspectives on Market Positioning, Technological Trajectories, and Future Resilience in Ultra-High Strength Aluminum Alloy Use
In conclusion, ultra-high strength aluminum alloys have transcended traditional applications to become strategic enablers of weight reduction, fuel efficiency, and sustainability across diverse industries. Technological advances in alloy chemistry and processing, coupled with shifting regulatory landscapes and escalating trade measures, are reshaping supply chains and competitive dynamics. Stakeholders who integrate advanced R&D, diversify sourcing strategies, and commit to circular economy principles will secure resilient market positions and capitalize on emerging growth opportunities. As global industrial priorities evolve toward electrification, emissions reduction, and defense modernization, these alloys will remain integral to delivering high-performance, low-carbon solutions.
This section provides a structured overview of the report, outlining key chapters and topics covered for easy reference in our Ultra-high Strength Aluminum Alloy market comprehensive research report.
- Preface
- Research Methodology
- Executive Summary
- Market Overview
- Market Dynamics
- Market Insights
- Cumulative Impact of United States Tariffs 2025
- Ultra-high Strength Aluminum Alloy Market, by End-Use Industry
- Ultra-high Strength Aluminum Alloy Market, by Product Form
- Ultra-high Strength Aluminum Alloy Market, by Alloy Grade
- Ultra-high Strength Aluminum Alloy Market, by Production Method
- Ultra-high Strength Aluminum Alloy Market, by Sales Channel
- Americas Ultra-high Strength Aluminum Alloy Market
- Europe, Middle East & Africa Ultra-high Strength Aluminum Alloy Market
- Asia-Pacific Ultra-high Strength Aluminum Alloy Market
- Competitive Landscape
- ResearchAI
- ResearchStatistics
- ResearchContacts
- ResearchArticles
- Appendix
- List of Figures [Total: 28]
- List of Tables [Total: 2154 ]
Secure the Full Ultra-High Strength Aluminum Alloy Market Intelligence by Engaging with Ketan Rohom for Bespoke Research Acquisition
To access the full breadth of proprietary analysis, detailed segment breakdowns, and region-specific intelligence on the ultra-high strength aluminum alloy landscape, you are invited to engage directly with Ketan Rohom, Associate Director, Sales & Marketing. Ketan will guide you through tailored package options, answer all your questions about methodology and coverage, and ensure you secure the critical insights needed to drive strategic decisions and competitive advantage. Reach out to Ketan Rohom today to obtain your comprehensive report and stay ahead in this dynamic market
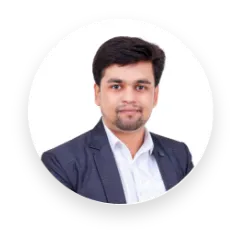
- When do I get the report?
- In what format does this report get delivered to me?
- How long has 360iResearch been around?
- What if I have a question about your reports?
- Can I share this report with my team?
- Can I use your research in my presentation?