Introduction to Undercutting End Mills
Undercutting end mills have emerged as indispensable tools for modern machining operations, enabling precise internal profiling and undercut geometries that traditional cutters struggle to achieve. As component designs grow increasingly complex-driven by miniaturization in electronics, stringent weight requirements in aerospace, and tight tolerance demands in medical device manufacturing-undercutting tools unlock design possibilities that enhance performance and reduce assembly steps. This introduction explores how these specialized cutters support innovation across industries, balancing the need for surface integrity and efficient material removal. By leveraging advanced materials and geometries, undercutting end mills deliver reliable performance even in high-volume production, reflecting a shift from generic tooling toward application-specific solutions. Moreover, the integration of advanced coatings and cutting-edge flute designs has elevated tool life and machining stability, reducing downtime and optimizing cost per finished part. As we delve into transformative trends, tariff impacts, and strategic insights, this overview sets the stage for an in-depth analysis of how undercutting end mills are reshaping manufacturing workflows and unlocking new levels of productivity.
Transformative Shifts in the Undercutting End Mills Landscape
In recent years, several transformative shifts have redefined the undercutting end mills market. First, the rise of additive-subtractive hybrid manufacturing has driven demand for tools capable of both rough stock preparation and fine-detail undercuts, prompting manufacturers to innovate multi-functional geometries. Secondly, growing emphasis on sustainability has accelerated adoption of wear-resistant coatings and eco-friendly coolant strategies, reducing tool replacement frequency and minimizing environmental footprint. Thirdly, digital integration-spanning toolpath simulation, in-machine tool monitoring, and predictive maintenance-has enhanced process reliability and shortened development cycles. Consequently, tool designers are collaborating closely with software developers to ensure seamless data exchange and real-time performance feedback. Additionally, the trend toward decentralized production in emerging economies has spurred localized tool customization, empowering machine shops to tailor undercutting solutions to specific material and process requirements. Collectively, these shifts emphasize the convergence of digitalization, sustainability, and application-driven design, elevating undercutting end mills from commodity items to strategic enablers of manufacturing excellence.
Cumulative Impact of United States Tariffs 2025
The imposition of new tariffs on cutting tools in 2025 has generated multifaceted effects across the value chain. Manufacturers that rely on imported carbide and coated end mills have encountered higher input costs, compelling many to reassess supplier relationships and explore domestic sourcing for critical inventory. End users in the automotive and aerospace sectors, traditionally major consumers of precision tooling, have experienced elevated procurement expenses, incentivizing investments in tool refurbishment and advanced coatings to extend service life. Meanwhile, distributors have diversified their portfolios by expanding private-label offerings that combine local manufacturing with global design expertise, mitigating margin pressures. On the engineering front, design teams are increasingly optimizing toolpaths and machining parameters to maximize dwell time and reduce overall tool consumption. Despite short-term cost increases, the tariff-induced focus on supply-chain resilience has stimulated research into alternative substrate materials and coating technologies, setting the stage for long-term enhancements in performance and reliability. Ultimately, the 2025 tariff landscape has accelerated the transition toward vertically integrated operations and closer collaboration among material suppliers, toolmakers, and end users.
Key Segmentation Insights
A granular look at segmentation reveals diverse performance requirements and growth drivers across multiple dimensions. In terms of material substrates, advanced ceramics and cermet offerings cater to high-temperature applications, while cobalt and high-speed steel variants provide cost-effective solutions for general machining; solid carbide remains the workhorse for high-feed operations, and diamond-coated and tungsten carbide formulations address ultra-fine finishing and abrasive composites. Diameter classifications range from micro tools as small as one-tenth of a millimeter for electronics and medical micromachining up to robust cutters exceeding eleven millimeters for structural component profiling. Flute architectures vary from single-flute designs optimized for deep undercuts to multi-flute and variable-helix configurations that balance chip evacuation with surface finish, encompassing two-, three-, and four-flute geometries as well. Application-specific categories span from roughing and high-performance cutting to general-purpose, finishing, and specialty tasks such as cross-hole milling. End geometry choices include ball and corner-radius ends for contouring, square ends for slotting, and chamfering tools that combine profiling with deburring. Coating strategies cover aluminum chromium nitride, titanium aluminum nitride, titanium carbonitride, titanium nitride, diamond coatings, and uncoated tools, each tailored for wear resistance, heat management, or surface integrity. Cutting-edge profiles encompass helical flutes, non-center-cutting edges, standard straight edges, and advanced variable-index designs. Shank configurations extend from straight shanks and tapered designs to Weldon shanks, ensuring secure tool holding across diverse machine interfaces. Industry use cases span aerospace structural components, automotive engine blocks, electronics and electrical housings, medical implants and devices, and tool-and-die fabrication. Manufacturing processes include conventional and high-efficiency milling alongside emerging 3D milling techniques. Finally, compatibility with BT, CAPTO, CAT and HSK holders and chip-breaking solutions-offered in high-performance and standard rotation variants-underscore the breadth of customization that empowers manufacturers to precisely match tool attributes with specific production goals.
This comprehensive research report categorizes the Undercutting End Mills market into clearly defined segments, providing a detailed analysis of emerging trends and precise revenue forecasts to support strategic decision-making.
- Material Type
- Diameter Size
- Flute Count
- Application
- End Type
- Coating
- Cutting Edge
- Shank Type
- Industry Use
- Manufacturing Process
- Tool Holder Compatibility
- Chip Breaking Performance
Key Regional Insights
Regional dynamics in the undercutting end mills market reflect distinct industrial priorities and supply-chain frameworks. In the Americas, robust demand from automotive manufacturing hubs in the United States and precision machining clusters in Mexico has reinforced investments in high-speed and high-feed undercutting tools, with localized production centers strengthening resilience against tariff fluctuations. Europe, the Middle East and Africa showcase a blend of advanced aerospace engineering in Western Europe, petrochemical sector needs in the Middle East, and growing manufacturing capabilities in Africa; this diversity fuels demand for specialized coatings and materials that withstand extreme temperatures and abrasive environments. Asia-Pacific leads in volume consumption, driven by electronics and semiconductor equipment production in China, Japan and South Korea, as well as growing medical device manufacturing in Southeast Asia; here, adoption of high-efficiency milling and micro-undercut solutions is particularly pronounced. Across all regions, ongoing investments in automation and Industry 4.0 initiatives are increasingly shaping tool selection criteria, with digital readiness and remote monitoring capabilities becoming as critical as raw cutting performance.
This comprehensive research report examines key regions that drive the evolution of the Undercutting End Mills market, offering deep insights into regional trends, growth factors, and industry developments that are influencing market performance.
- Americas
- Asia-Pacific
- Europe, Middle East & Africa
Key Companies Insights
Market leadership in the undercutting segment is defined by innovation in carbide formulations, coating technologies and digital integration. Emuge-FRANKEN USA stands out for its precision thread milling and undercut strategies, while Garr Tool Company leverages cutting-edge geometries for high-performance applications. Harvey Tool Company, LLC has built a niche in miniature and specialty tools, complemented by HARVI, a Kennametal brand, which focuses on aggressively coated solutions for aerospace machining. Kennametal Inc. continues to drive material science breakthroughs, and Lakeshore Carbide Inc. distinguishes itself through rapid prototyping and custom carbide grades. MA Ford Manufacturing Co., Inc. specializes in micro end mills for electronics and medical components, whereas OSG Corporation excels in multi-layer coatings and super-hard substrates. Sandvik Coromant brings advanced tool monitoring and data analytics to the table, and Seco Tools AB emphasizes sustainable machining with eco-friendly coatings. Together, these companies shape the competitive landscape, fostering collaboration with end users and software providers to deliver turnkey undercutting strategies.
This comprehensive research report delivers an in-depth overview of the principal market players in the Undercutting End Mills market, evaluating their market share, strategic initiatives, and competitive positioning to illuminate the factors shaping the competitive landscape.
- Emuge-FRANKEN USA
- Garr Tool Company
- Harvey Tool Company, LLC
- HARVI, a Kennametal Brand
- Kennametal Inc.
- Lakeshore Carbide Inc.
- MA Ford Manufacturing Co., Inc.
- OSG Corporation
- Sandvik Coromant
- Seco Tools AB
Actionable Recommendations for Industry Leaders
- Conduct a comprehensive supply-chain audit to identify critical vulnerabilities in carbide and coating supplies, and establish dual sourcing agreements with regional partners.
- Invest in digital tool management systems that integrate real-time performance data with ERP platforms to optimize replacement cycles and reduce unplanned downtime.
- Collaborate with OEM customers to co-develop application-specific flute geometries and coatings, thereby securing long-term purchase agreements and driving higher-margin tooling solutions.
- Expand service offerings to include on-site tool refurbishment and reconditioning, leveraging in-house coating capabilities to extend tool life and differentiate from commodity suppliers.
- Prioritize sustainability by adopting eco-conscious coolant systems and recyclable packaging, aligning with global ESG objectives and appealing to environmentally focused end users.
- Explore additive manufacturing partnerships to prototype complex undercut geometries rapidly, accelerating time-to-market for new tool lines and customized solutions.
Explore AI-driven insights for the Undercutting End Mills market with ResearchAI on our online platform, providing deeper, data-backed market analysis.
Ask ResearchAI anything
World's First Innovative Al for Market Research
Conclusion
The evolution of undercutting end mills reflects a broader trend toward precision, customization and digital integration in modern manufacturing. By understanding the multifaceted segmentation landscape and regional nuances, industry stakeholders can tailor strategies that maximize tool performance and cost efficiency. The 2025 tariffs have catalyzed a renewed focus on supply-chain resilience and in-house expertise, driving collaborations that extend from material suppliers to software developers. Leading companies are distinguishing themselves through advanced coatings, micro, and high-efficiency solutions, while emerging players leverage rapid prototyping to meet niche requirements. As sustainability and automation continue to shape procurement decisions, successful organizations will be those that balance cutting-edge innovation with pragmatic operational enhancements. In doing so, they will ensure that undercutting end mills remain not only tools of precision but also key drivers of manufacturing competitiveness.
This section provides a structured overview of the report, outlining key chapters and topics covered for easy reference in our Undercutting End Mills market comprehensive research report.
- Preface
- Research Methodology
- Executive Summary
- Market Overview
- Market Dynamics
- Market Insights
- Cumulative Impact of United States Tariffs 2025
- Undercutting End Mills Market, by Material Type
- Undercutting End Mills Market, by Diameter Size
- Undercutting End Mills Market, by Flute Count
- Undercutting End Mills Market, by Application
- Undercutting End Mills Market, by End Type
- Undercutting End Mills Market, by Coating
- Undercutting End Mills Market, by Cutting Edge
- Undercutting End Mills Market, by Shank Type
- Undercutting End Mills Market, by Industry Use
- Undercutting End Mills Market, by Manufacturing Process
- Undercutting End Mills Market, by Tool Holder Compatibility
- Undercutting End Mills Market, by Chip Breaking Performance
- Americas Undercutting End Mills Market
- Asia-Pacific Undercutting End Mills Market
- Europe, Middle East & Africa Undercutting End Mills Market
- Competitive Landscape
- ResearchAI
- ResearchStatistics
- ResearchContacts
- ResearchArticles
- Appendix
- List of Figures [Total: 40]
- List of Tables [Total: 568 ]
Call to Action: Secure Your Undercutting End Mills Market Report
To gain deeper insights and actionable data on undercutting end mills-covering technology trends, segmentation analysis, regional dynamics and competitive benchmarking-contact Ketan Rohom, Associate Director, Sales & Marketing. He can guide you through the comprehensive report and help tailor findings to your specific strategic needs. Secure your copy today and position your organization at the forefront of precision machining.
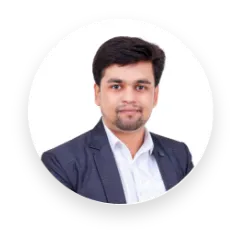
- When do I get the report?
- In what format does this report get delivered to me?
- How long has 360iResearch been around?
- What if I have a question about your reports?
- Can I share this report with my team?
- Can I use your research in my presentation?