Navigating the Expanding Vacuum Aluminum Casting Sector with Strategic Insights, Emerging Trends, and Industry Evolution Overview
The vacuum aluminum casting process has emerged as a critical manufacturing technique for industries demanding high precision, lightweight construction, and exceptional mechanical performance. Combining the advantages of aluminum’s favorable strength-to-weight ratio with vacuum-assisted casting methods enables the production of defect-free components that meet rigorous quality and dimensional requirements. As markets worldwide pursue efficiency and sustainability, vacuum aluminum casting bridges the gap between traditional metal forming and advanced manufacturing, ensuring manufacturability of lightweight structural and functional parts at scale.
Recent advances in materials science have introduced next-generation aluminum alloys that offer improved corrosion resistance, thermal stability, and fatigue life. These innovations are pivotal in applications ranging from intricate electronic housings to large structural elements in aerospace platforms. Concurrently, the integration of digital manufacturing tools-such as real-time data analytics and process simulation-has elevated the predictability and repeatability of vacuum casting workflows, enabling manufacturers to fine-tune parameters and reduce scrap rates significantly.
Looking ahead, vacuum aluminum casting stands at the intersection of technological innovation and market demand. With global supply chain complexities and heightened regulatory scrutiny around emissions and energy consumption, manufacturers are reengineering their operations to incorporate closed-loop recycling systems and energy-efficient melting technologies. This executive summary provides a concise yet comprehensive overview of the industry’s current state, transformative trends, regulatory impacts, segmentation analyses, regional dynamics, competitive landscape, and strategic recommendations to guide decision-makers navigating this dynamic sector.
Unveiling the Groundbreaking Technological and Sustainable Transformations That Are Reshaping Vacuum Aluminum Casting Processes
The vacuum aluminum casting landscape has undergone a series of profound transformations driven by technological, material, and environmental imperatives. One of the most significant shifts is the widespread adoption of digital twins and Industry 4.0 methodologies, which allow manufacturers to construct virtual replicas of casting processes. These digital frameworks facilitate real-time monitoring of mold temperatures, pressure profiles, and fill rates, enabling proactive adjustments that mitigate defect rates and optimize cycle times. By embedding IoT sensors within casting cells and integrating machine learning algorithms, foundries achieve unprecedented levels of process control, reducing unplanned downtime by up to 25 percent.
In parallel, materials innovation has introduced high-performance aluminum alloys-enriched with magnesium, copper, and silicon-that deliver superior strength-to-weight ratios and enhanced thermal stability essential for aerospace and automotive structural components. These next-generation alloys expand the design envelope, permitting thinner wall sections and more complex geometries without compromising mechanical integrity. Furthermore, vacuum-assisted melting techniques, such as vacuum evaporation and vacuum induction melting, are being employed to minimize gas entrapment, improve cleanliness, and reduce porosity, thereby meeting stringent quality standards for critical applications.
Sustainability considerations have also reshaped the industry, as leading casting operations implement closed-loop recycling systems that reincorporate aluminum scrap into the production cycle. This circular approach not only lowers raw material costs by up to 40 percent but also aligns with global CO₂ reduction targets. Manufacturers are investing in energy-efficient furnaces and advanced heat recovery systems to curtail power usage, ensuring that vacuum aluminum casting evolves in concert with environmental governance and corporate responsibility initiatives.
Assessing the Far-Reaching Consequences of 2025 United States Aluminum Tariffs on Vacuum Casting Supply Chains and Cost Structures
The introduction of United States tariffs on aluminum imports in early 2025 represents a pivotal inflection point for vacuum aluminum casting supply chains. By targeting a broad array of aluminum products with duties ranging from 10 percent to 25 percent, the policy has reverberated through every layer of the value chain, from smelters to finished-component manufacturers. These levies aim to strengthen domestic production capacity and insulate U.S. foundries from lower-cost foreign competitors, yet they also precipitate cost escalations that end customers inevitably absorb.
Original equipment manufacturers across automotive, aerospace, and industrial machinery sectors have been prompted to renegotiate long-term contracts with domestic smelting partners and reassess near-sourcing strategies. In response, several leading foundries have accelerated automation investments-such as advanced vacuum induction melting and high-efficiency vacuum evaporation systems-to offset higher feedstock prices through productivity and yield improvements. Simultaneously, multinational casting firms are pursuing joint ventures within the United States to maintain tariff-free status on key aluminum feedstocks and preserve supply continuity for major account portfolios.
Moreover, the tariff landscape has galvanized the recycling of aluminum scrap and recycled billets, both to dilute the impact of import duties and to support sustainability commitments. However, integrating higher proportions of recycled materials demands rigorous metallurgical controls to ensure consistent chemical composition and mechanical properties. Ultimately, while the 2025 U.S. tariffs have introduced near-term cost pressures, they have also accelerated modernization and domestic capacity expansion, fostering a more resilient vacuum aluminum casting ecosystem.
Decoding Market Dynamics Through Application, Process, Alloy, and Product-Type Segmentation to Reveal Emerging Growth Opportunities
A comprehensive view of the vacuum aluminum casting environment can be achieved by examining the market through layered segmentation lenses that reveal nuanced growth patterns. When looking at applications, aerospace casting demands the highest levels of dimensional tolerance and material cleanliness, encompassing both commercial and military aircraft programs. Automotive components, spanning commercial vehicles and passenger cars, are driving significant demand for lightweight structural parts that enhance fuel efficiency. Within consumer goods, vacuum cast aluminum is leveraged for durable household appliances and high-performance sporting equipment that require aesthetic finishes and tight tolerances. In the electronics sector, both consumer devices and industrial electronics enclosures benefit from vacuum casting’s capacity for precise thin-wall geometries, while industrial machinery components-such as agricultural and construction equipment-rely on robust cast parts that withstand extreme mechanical stresses. The medical segment includes diagnostic equipment housings and surgical instrument frames, all demanding biocompatibility and stringent surface quality.
Process type analysis further demarcates the market into gravity die casting, which offers low initial tooling investment for smaller batches; low pressure die casting, favored for medium-volume runs with improved feeding characteristics; and pressure die casting, which yields high throughput and excellent surface finish for large-scale production. Alloy selection plays a critical role, with the 2xxx series valued for its high strength in structural aerospace applications, the 6xxx series prized for formability and corrosion resistance in consumer and automotive parts, and the 7xxx series selected for premium strength-to-weight performance in advanced industrial and defense programs. Finally, product-type segmentation highlights engine components such as cylinder blocks and heads, heat exchangers crucial for thermal management subsystems, structural components forming load-bearing frameworks, and valve bodies instrumental in precise fluid control. Understanding these intersecting dimensions of application, process type, alloy chemistry, and product function illuminates strategic pathways for targeted investment and product development initiatives.
This comprehensive research report categorizes the Vacuum Aluminum Casting market into clearly defined segments, providing a detailed analysis of emerging trends and precise revenue forecasts to support strategic decision-making.
- Application
- Process Type
- Alloy Type
- Product Type
Exploring Regional Market Dynamics across Americas, Europe, Middle East & Africa, and Asia-Pacific to Illuminate Growth Hotspots
Regional dynamics in the vacuum aluminum casting sector demonstrate distinct drivers and strategic imperatives across the Americas, Europe, Middle East & Africa, and Asia-Pacific. In the Americas, mature automotive and aerospace supply chains in the United States and Canada underpin a stable demand for high-precision cast parts, while growing opportunities in Latin America center on modernization of existing foundries and expansion of prototyping capabilities. Manufacturers in North America are placing a premium on digital integration and sustainability, leveraging advanced casting cells alongside renewable energy to reduce costs and carbon footprints.
Across Europe, Middle East & Africa, stringent regulatory regimes-most notably the European Green Deal-drive the adoption of eco-friendly casting processes and recycled aluminum feedstocks. European foundries are pioneering energy-efficient furnace designs and closed-loop water systems to comply with net-zero targets, while Middle Eastern infrastructure projects and nascent regional aerospace initiatives foster demand for bespoke casting solutions. In select African markets, low-cost casting services carve out niches in commodity applications, promoting local industrial diversification and export potential.
The Asia-Pacific region stands as the growth leader, buoyed by rapid industrialization in China, India, Japan, and South Korea. Automotive electrification trends and consumer electronics innovation are primary catalysts for vacuum casting adoption, with OEMs and startups alike leveraging vacuum-assisted processes to accelerate prototyping and small-batch production. Competitive labor costs and government incentives for advanced manufacturing further amplify the region’s appeal, positioning Asia-Pacific as the most dynamic market segment for vacuum aluminum casting technologies.
This comprehensive research report examines key regions that drive the evolution of the Vacuum Aluminum Casting market, offering deep insights into regional trends, growth factors, and industry developments that are influencing market performance.
- Americas
- Europe, Middle East & Africa
- Asia-Pacific
Profiling Leading Industry Players Driving Innovation and Competitive Advantage in the Vacuum Aluminum Casting Market
The competitive landscape of vacuum aluminum casting is defined by a cohort of global leaders whose technological prowess and operational scale set industry benchmarks. Nemak, headquartered in Mexico, is renowned for its high-pressure die casting solutions, delivering structural automotive components with proprietary mega-casting methodologies and closed-loop recycling achieving upwards of 95 percent material utilization. Ryobi Limited in Japan has pioneered vacuum-assisted die casting since the early 1990s, boasting automated cycle times under 15 seconds and material science innovations in Al-Si-Cu alloys for critical electronics and lightweight automotive parts.
U.S.-based Dynacast specializes in high-precision components for electric vehicle battery and motor housings, leveraging proprietary Thixomolding processes that produce magnesium and aluminum parts with exceptional dimensional accuracy. GF Casting Solutions, a division of Switzerland’s Georg Fischer, operates state-of-the-art die casting plants across Europe and Asia, focusing on fluid system components with advanced digital twin quality control frameworks. Pace Industries in North America offers modular vacuum casting production lines, streamlining multi-step processing to support rapid scale-up for commercial and defense programs. Additional notable players include Endurance Technologies in India, Martinrea International in Canada, and Shiloh Industries in the United States, each distinguished by specialized capabilities spanning engine components, structural castings, and permanent mold expertise.
This comprehensive research report delivers an in-depth overview of the principal market players in the Vacuum Aluminum Casting market, evaluating their market share, strategic initiatives, and competitive positioning to illuminate the factors shaping the competitive landscape.
- Nemak, S.A.B. de C.V.
- Georg Fischer AG
- Ryobi Limited
- Magna International Inc.
- Dynacast International Inc.
- Teksid S.p.A.
- Shiloh Industries, Inc.
- Linamar Corporation
- Lfoundry S.p.A.
- Mercury Castings, LLC
Implementing Targeted Strategies for Industry Leaders to Enhance Operational Efficiency, Innovation, and Competitive Resilience
Industry leaders must embrace a multifaceted strategy to capitalize on emerging opportunities and navigate ongoing challenges. First, prioritizing the integration of digital twin and Industry 4.0 infrastructures will enable real-time process optimization and predictive maintenance protocols. Deploying AI-driven quality control systems can further reduce scrap and rework, fostering leaner production cycles and cost efficiencies. Second, strengthening closed-loop recycling frameworks for aluminum scrap not only mitigates exposure to fluctuating raw material prices and tariff volatility but also aligns with corporate sustainability mandates. Implementing advanced sorting and alloy verification systems ensures that recycled feedstocks meet stringent purity requirements for vacuum casting applications.
Strategic partnerships with domestic smelters and investment in high-efficiency vacuum induction melting capacities are essential steps to offset the 2025 tariff impacts. Collaborative joint ventures can secure preferential access to tariff-free feedstocks, stabilize input costs, and support long-term growth trajectories. Additionally, diversifying alloy portfolios by exploring novel chemistries-such as high-zinc 7xxx series alloys for aerospace grade parts-can open new market segments and enhance material performance differentiation. Finally, workforce development programs that focus on advanced casting techniques, data analytics proficiency, and sustainability practices will equip teams to drive continuous innovation and maintain competitiveness in an evolving market landscape.
Detailing the Comprehensive Research Methodology Underpinning Market Analysis and Ensuring Data Reliability and Analytical Rigor
This market analysis is underpinned by a rigorous research methodology designed to ensure comprehensive data collection and analytical integrity. The process commenced with extensive secondary research, encompassing peer-reviewed journals, industry whitepapers, regulatory filings, and publicly available corporate disclosures. This desk research established foundational market parameters, technological trends, and competitive landscapes.
Primary research complemented these insights through targeted interviews with C-level executives, plant managers, process engineers, and procurement specialists across key vacuum aluminum casting operations worldwide. These qualitative discussions provided real-world perspectives on emerging challenges, investment priorities, and strategic initiatives. Quantitative modeling and data triangulation techniques were employed to cross-verify inputs from secondary sources and primary feedback, ensuring alignment between market observations and stakeholder experiences.
Statistical analyses, including trending algorithms and scenario simulations, facilitated exploration of tariff impacts, regional growth differentials, and segmentation dynamics. All findings underwent multi-tier validation by subject matter experts to confirm accuracy and relevance. This blended approach of secondary desk research, primary stakeholder engagement, and rigorous quantitative verification delivers a high-fidelity portrayal of the vacuum aluminum casting market, enabling decision-makers to act with confidence.
Explore AI-driven insights for the Vacuum Aluminum Casting market with ResearchAI on our online platform, providing deeper, data-backed market analysis.
Ask ResearchAI anything
World's First Innovative Al for Market Research
Synthesizing Insights on Market Evolution and Strategic Imperatives to Guide Decision-Makers in Vacuum Aluminum Casting
The vacuum aluminum casting market is at a pivotal juncture, driven by a confluence of technological innovation, regulatory evolution, and shifting supply chain paradigms. Emerging materials and process automation are unlocking new capabilities in component complexity, performance, and production efficiency. Simultaneously, geopolitical measures such as the 2025 U.S. aluminum tariffs have catalyzed domestic capacity enhancements and renewed focus on alloy recycling, reshaping cost dynamics and sourcing strategies.
Segmented analysis reveals that aerospace, automotive, consumer electronics, industrial machinery, and medical markets each offer distinct value propositions, underpinned by specific alloy and process requirements. Regionally, Asia-Pacific’s rapid industrial growth contrasts with the mature, sustainability-driven landscapes of Americas and Europe, Middle East & Africa. Leading companies with robust R&D pipelines, digital infrastructures, and global footprint are best positioned to capture growth and mitigate risks.
As the industry advances, strategic recommendations emphasize digital integration, circular economy adoption, and targeted partnerships to secure feedstock continuity. This holistic view equips stakeholders with a clear roadmap for navigating market complexities and capitalizing on emerging opportunities.
This section provides a structured overview of the report, outlining key chapters and topics covered for easy reference in our Vacuum Aluminum Casting market comprehensive research report.
- Preface
- Research Methodology
- Executive Summary
- Market Overview
- Market Dynamics
- Market Insights
- Cumulative Impact of United States Tariffs 2025
- Vacuum Aluminum Casting Market, by Application
- Vacuum Aluminum Casting Market, by Process Type
- Vacuum Aluminum Casting Market, by Alloy Type
- Vacuum Aluminum Casting Market, by Product Type
- Americas Vacuum Aluminum Casting Market
- Europe, Middle East & Africa Vacuum Aluminum Casting Market
- Asia-Pacific Vacuum Aluminum Casting Market
- Competitive Landscape
- ResearchAI
- ResearchStatistics
- ResearchContacts
- ResearchArticles
- Appendix
- List of Figures [Total: 26]
- List of Tables [Total: 914 ]
Seize Strategic Market Intelligence: Connect with Ketan Rohom to Secure Your Comprehensive Vacuum Aluminum Casting Market Research Report
To access the full depth of strategic analysis and granular data presented in this report, reach out directly to Ketan Rohom, Associate Director of Sales & Marketing. Engaging with Ketan will ensure personalized guidance on how the report’s insights can be applied to your organization’s objectives, whether you are aiming to optimize supply chains, refine material sourcing strategies, or accelerate technology adoption. By connecting with Ketan, you will receive tailored support to navigate procurement steps, explore bespoke data packages, and unlock actionable market intelligence. Position your business at the forefront of the vacuum aluminum casting industry by leveraging this comprehensive research resource. Contacting Ketan today is the definitive step toward informed decision-making and sustained competitive advantage.
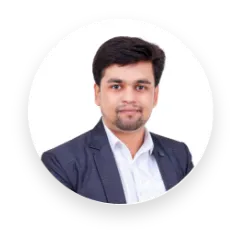
- When do I get the report?
- In what format does this report get delivered to me?
- How long has 360iResearch been around?
- What if I have a question about your reports?
- Can I share this report with my team?
- Can I use your research in my presentation?