Introduction to Vacuum Evaporation Coating Material
Vacuum evaporation coating has emerged as a cornerstone technology for enabling high-performance surfaces across diverse industries. By evaporating specialized materials under high vacuum and depositing ultra-thin films onto substrates, manufacturers achieve tailored optical, electrical, mechanical, and protective properties. This process underpins critical applications ranging from anti-reflective optical layers and decorative metallic finishes to advanced electronic components and corrosion-resistant barriers. As demand intensifies for miniaturized electronics, lightweight automotive components, and durable solar and wind energy systems, vacuum evaporation coating is positioned to address evolving performance requirements and sustainability goals.
Recent advances in deposition hardware, material chemistries, in-situ monitoring, and process automation are driving unprecedented precision and throughput. Concurrently, regulatory shifts and trade policies are reshaping cross-border supply chains and competitive dynamics. Within this context, understanding transformative technology trends, segmentation-based growth drivers, regional market characteristics, and leading solution providers is essential for stakeholders aiming to capture new opportunities. This executive summary distills these critical insights, empowering decision-makers to formulate strategic initiatives that capitalize on emerging trends while navigating the complexities of tariffs, regulations, and global competition.
Transformative Shifts in the Vacuum Evaporation Landscape
Over the past decade, vacuum evaporation coating has undergone a metamorphosis driven by converging trends in materials science, equipment design, and digitalization. First, the proliferation of advanced metals, nitrides, oxides, and sulfides with engineered stoichiometries is enabling customized film properties that were once unattainable. Second, next-generation deposition systems now integrate real-time process control via spectroscopic ellipsometry and mass spectrometry, ensuring film thickness and composition meet sub-nanometer tolerances. Third, additive manufacturing techniques and hybrid processes are emerging, blending vacuum evaporation with inkjet printing and laser patterning to reduce waste and accelerate prototyping.
As these technological innovations converge, stakeholders are shifting from cost-driven procurement models toward value-centric partnerships that emphasize co-development of new materials, application-specific process recipes, and lifecycle services. This transition is disrupting conventional supplier-end user dynamics, steering the market toward collaborative ecosystems. In parallel, digital twins and predictive maintenance are enhancing equipment uptime, lowering total cost of ownership, and further differentiating technology providers.
Cumulative Impact of United States Tariffs 2025
In early 2025, the United States implemented a revised tariff regime targeting imports of vacuum evaporation coating materials and related components. Cumulative duties have increased production costs for downstream manufacturers that rely on imported source materials and equipment, creating short-term margin pressures. Companies with vertically integrated supply chains have achieved a competitive edge by sourcing raw metals and specialized compounds domestically or through tariff-exempt trade agreements.
Moreover, tariff-driven cost escalation has accelerated regionalization of supply chains. North American deposition equipment vendors are localizing component fabrication while establishing strategic partnerships with material producers to mitigate duty impacts. Conversely, importers in Asia-Pacific and Europe Middle East & Africa have absorbed a portion of increased costs to maintain customer loyalty, which has compressed profitability in those regions.
These trade measures have also triggered procurement strategies that prioritize long-term contractual agreements and hedging instruments to stabilize input costs. As a result, firms with robust risk management frameworks are better equipped to navigate tariff-induced volatility, while smaller players face capital constraints in stockpiling materials or renegotiating supply contracts.
Key Segmentation Insights
Analysis across material type reveals that metals such as aluminum copper gold silver and titanium lead growth due to their excellent conductivity reflectivity and corrosion resistance while nitrides including aluminum nitride and titanium nitride are gaining traction for their superior hardness and thermal stability. Oxides such as aluminum oxide silicon dioxide and titanium dioxide dominate optical and dielectric applications because of their high refractive index uniformity and chemical inertness while sulfides like cadmium sulfide and zinc sulfide serve niche photochemical and sensor uses.
Technology adoption patterns show that electron beam evaporation delivers high-purity films for semiconductor applications, pulsed laser deposition excels in complex oxide formation, resistive heating evaporation remains cost-effective for decorative coatings, sputtering offers uniform coverage over large areas, and thermal evaporation satisfies flexible substrate requirements.
End-use industries span aerospace and defense where weight reduction and heat shielding are critical, automotive manufacturers pursuing decorative and protective finishes, electronics and semiconductor segments including data storage devices display panels and MEMS, healthcare applications such as dental equipment and medical devices, and industrial and energy sectors focused on solar cells and wind turbines.
Application demands range from barrier coatings that provide chemical or water protection to decorative surfaces with aesthetic finishes optical coatings for anti-reflective and filter functions electronic device substrates including circuit boards and sensors and robust protective layers against abrasion and wear. Material forms encompass granules pellets powders and tablets to optimize feedstock handling while deposition thickness categories separate thick films for structural resilience from thin films for high precision. Deposition rate considerations span high medium and low rates to balance throughput with film quality.
This comprehensive research report categorizes the Vacuum Evaporation Coating Material market into clearly defined segments, providing a detailed analysis of emerging trends and precise revenue forecasts to support strategic decision-making.
- Material Type
- Technology
- End-Use Industry
- Application
- Material Forms
- Thickness
- Deposition Rate
Key Regional Insights
The Americas region exhibits mature supply chains anchored by leading equipment manufacturers and material producers, supported by strong R&D clusters in North America and Brazil’s growing photovoltaic industry. Europe Middle East & Africa is characterized by stringent environmental and safety regulations that drive innovation in low-emission processes and sustainable materials, with hubs in Germany, France, and key Middle Eastern chemical parks. Asia-Pacific commands the largest share of manufacturing output, fueled by electronics and semiconductor fabs in China, South Korea, Japan, and India’s expanding defense and automotive coatings markets. Rapid urbanization, renewable energy deployments, and government initiatives for domestic high-tech industries are strengthening regional demand dynamics across all three zones.
This comprehensive research report examines key regions that drive the evolution of the Vacuum Evaporation Coating Material market, offering deep insights into regional trends, growth factors, and industry developments that are influencing market performance.
- Americas
- Asia-Pacific
- Europe, Middle East & Africa
Key Companies Insights
Leading market participants span a spectrum of material scientists, equipment OEMs and service providers. Advanced Coating Materials (ACM) and AJA International, Inc. excel in specialty powder and pellet formulations, while American Elements and Angstrom Engineering Inc. focus on high-purity metals and compounds. Angstrom Sciences, Inc. and Az Electronic Materials offer bespoke chemistries for niche optical and electronic applications; Denton Vacuum, LLC Evatec AG and Oerlikon Leybold Vacuum GmbH provide turnkey deposition systems optimized for throughput and precision. Goodfellow Corporation acts as a distributor for diverse raw materials, whereas Kurt J. Lesker Company and Materion Corporation offer vertically integrated solutions covering everything from source material to deposition hardware. Plasma-Therm, LLC and PVD Products, Inc. drive process innovation with advanced plasma and vapor technologies, SCOTT Glass Technologies, Inc. specializes in optical-grade substrates, and Torrey Hills Technologies, LLC along with TrumPower Corporation deliver configurable thermal evaporation modules. ULVAC, Inc. and Umicore Thin Film Products enhance the ecosystem with cutting-edge vacuum pumps and thin film materials, while Vac-Tech Systems Pvt. Ltd. supports custom system integration for emerging markets.
This comprehensive research report delivers an in-depth overview of the principal market players in the Vacuum Evaporation Coating Material market, evaluating their market share, strategic initiatives, and competitive positioning to illuminate the factors shaping the competitive landscape.
- Advanced Coating Materials (ACM)
- AJA International, Inc.
- American Elements
- Angstrom Engineering Inc.
- Angstrom Sciences, Inc.
- Az Electronic Materials
- Denton Vacuum, LLC
- Evatec AG
- Goodfellow Corporation
- Kurt J. Lesker Company
- Materion Corporation
- Oerlikon Leybold Vacuum GmbH
- Plasma-Therm, LLC
- PVD Products, Inc.
- SCOTT Glass Technologies, Inc.
- Torrey Hills Technologies, LLC
- TrumPower Corporation
- ULVAC, Inc.
- Umicore Thin Film Products
- Vac-Tech Systems Pvt. Ltd.
Actionable Recommendations for Industry Leaders
Industry leaders should prioritize vertical integration by forging partnerships that link raw material sourcing to end-use applications, thereby insulating supply chains against tariff volatility. Investing in modular deposition platforms with open architecture allows rapid reconfiguration to accommodate new material chemistries and process recipes. Adopting digital twins to simulate chamber dynamics and predictive analytics for maintenance will improve yield and reduce downtime.
Furthermore, companies can differentiate through sustainability by developing low-carbon source materials, implementing closed-loop recycling of target remnants, and sourcing renewable energy for vacuum systems. Collaborations with academic institutions and cross-industry consortia will accelerate innovation in high-performance nitrides and oxides. Finally, expanding service offerings-such as process consulting, on-site training, and rapid prototyping-will deepen customer engagement and create recurring revenue streams.
Explore AI-driven insights for the Vacuum Evaporation Coating Material market with ResearchAI on our online platform, providing deeper, data-backed market analysis.
Ask ResearchAI anything
World's First Innovative Al for Market Research
Conclusion and Strategic Outlook
Vacuum evaporation coating materials and technologies stand at the nexus of critical growth areas including advanced electronics, sustainable energy, and high-value defense applications. By understanding the transformative shifts in material chemistries and deposition processes, as well as the implications of evolving tariff structures, stakeholders can position themselves to lead in an increasingly competitive landscape. The convergence of digitalization, sustainability, and collaborative innovation models will define market leaders over the next decade.
This section provides a structured overview of the report, outlining key chapters and topics covered for easy reference in our Vacuum Evaporation Coating Material market comprehensive research report.
- Preface
- Research Methodology
- Executive Summary
- Market Overview
- Market Dynamics
- Market Insights
- Cumulative Impact of United States Tariffs 2025
- Vacuum Evaporation Coating Material Market, by Material Type
- Vacuum Evaporation Coating Material Market, by Technology
- Vacuum Evaporation Coating Material Market, by End-Use Industry
- Vacuum Evaporation Coating Material Market, by Application
- Vacuum Evaporation Coating Material Market, by Material Forms
- Vacuum Evaporation Coating Material Market, by Thickness
- Vacuum Evaporation Coating Material Market, by Deposition Rate
- Americas Vacuum Evaporation Coating Material Market
- Asia-Pacific Vacuum Evaporation Coating Material Market
- Europe, Middle East & Africa Vacuum Evaporation Coating Material Market
- Competitive Landscape
- ResearchAI
- ResearchStatistics
- ResearchContacts
- ResearchArticles
- Appendix
- List of Figures [Total: 30]
- List of Tables [Total: 734 ]
Call to Action: Engage with Ketan Rohom for Full Report
To gain full access to in-depth analyses, proprietary data, and strategic guidance, reach out to Ketan Rohom, Associate Director, Sales & Marketing, today. Secure your copy of the comprehensive market research report to drive informed decision-making and capitalize on the latest advancements in vacuum evaporation coating.
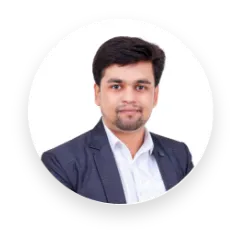
- When do I get the report?
- In what format does this report get delivered to me?
- How long has 360iResearch been around?
- What if I have a question about your reports?
- Can I share this report with my team?
- Can I use your research in my presentation?