Executive Overview of Vertical Boring Mill Market Dynamics
The vertical boring mill market stands at the intersection of traditional manufacturing excellence and modern industrial innovation. As manufacturing facilities worldwide seek greater precision, speed, and flexibility, these machines have emerged as indispensable workhorses for processing large, heavy components. From aerospace landing gear parts to oil and gas drilling components, they ensure dimensional accuracy and structural integrity where tight tolerances and surface finish quality are non-negotiable. Recent advances in computer numerical control (CNC) integration and automation have catalyzed a shift from manual operations to digitally driven workflows, empowering machine shops to meet shorter lead times and evolving design complexities. Moreover, heightened environmental regulations and supply chain disruptions have underscored the need for resilient, energy-efficient equipment that can adapt to fluctuating raw material availability. This executive summary outlines key market transformations, regulatory impacts, critical segmentation insights, regional dynamics, competitive landscapes, actionable recommendations, and a clear path to securing the comprehensive research report.
Key Technological and Regulatory Shifts Reshaping the Industry
Manufacturers are experiencing a profound transformation driven by digitalization, automation, and sustainability imperatives. The integration of smart sensors and IoT connectivity has enabled real-time monitoring of spindle vibrations, tool wear, and power consumption, laying the groundwork for predictive maintenance and minimized downtime. Coupled with advancements in five-axis CNC control, companies can now execute complex geometries in a single chucking, reducing part handling and improving surface finish consistency. At the same time, rising demand for lightweight materials in automotive and aerospace sectors is prompting machine builders to refine spindle speeds and coolant delivery systems for aluminum alloys, ensuring chip evacuation without compromising stability. Regulatory shifts, including stricter emissions standards and waste management policies, are steering investment toward eco-friendly hydraulic systems and closed-loop coolant circuits. Meanwhile, supply chain disruptions have accelerated adoption of localized production, prompting collaborations between equipment OEMs and regional service providers to guarantee spare parts availability and technical support. These transformative shifts are redefining benchmarks for precision, throughput, and environmental stewardship in heavy-duty machining.
Combined Effects of the 2025 U.S. Tariff Adjustments
In 2025, new tariff measures on imported machine tools and raw materials are exerting a dual-edged influence on market participants. Increased duties on steel and aluminum feedstock have elevated production costs, compelling equipment manufacturers to optimize supply chains and seek alternative sourcing strategies. At the same time, higher import levies on foreign-made CNC controllers and spindles have created a window of opportunity for domestic producers to gain market share. Some domestic OEMs are leveraging this environment to accelerate capacity expansions, investing in modular manufacturing lines that can adapt to shifting tariff schedules. However, end users reliant on advanced European and Japanese components are grappling with extended lead times and cost pass-throughs. As a result, partnerships between machine shops and local automation integrators have intensified, focused on retrofitting legacy vertical boring mills with in-house CNC packages. These dynamics are reshaping supplier relationships, driving a strategic realignment that balances cost containment with technological access.
Comprehensive Segmentation Insights Across Six Dimensions
A detailed examination of the market through multiple lenses reveals nuanced opportunities and challenges across applications, product formats, technologies, end-user sectors, material preferences, and business models. When categorized by application, aerospace manufacturing-spanning landing gear parts and turbine blades-demands exceptionally tight tolerances and superior surface finishes, while automotive assembly lines utilize chassis components, engine parts, gear box assemblies, and prototype models to validate design integrity. Machine shops focusing on custom equipment and prototyping benefit from flexible set-ups that can accommodate short production runs, whereas oil and gas operators relying on drilling and pipeline components prioritize heavy-duty rigidity and extended service life. In terms of product type, floor mounted boring mills featuring both CNC-controlled and manual variants offer larger work envelops for heavy components, contrasted with table type systems that excel in versatility and footprint efficiency on shop floors. Technologically, the shift toward CNC solutions-whether in horizontal or vertical configurations-has eclipsed conventional platforms reliant on alignment features, providing enhanced positioning accuracy and automated tool changes. End-user industries diversify further: heavy equipment sectors, including mining equipment producers, demand robustness under harsh operating conditions, while manufacturing segments such as automotive, aviation, and precision tooling seek consistency, repeatability, and integration with digital workflows. Material selection also influences equipment choice: aluminum alloys and pure aluminum workpieces necessitate spindle adaptations for chip control, whereas carbon and stainless steels require robust spindle bearings and optimized coolant flow. Finally, business models bifurcate into aftermarket services-encompassing machine refurbishment and maintenance contracts-and streamlined B2B supply chains focused on direct sales, ensuring that both one-time purchasers and long-term service clients receive tailored support.
This comprehensive research report categorizes the Vertical Boring Mill market into clearly defined segments, providing a detailed analysis of emerging trends and precise revenue forecasts to support strategic decision-making.
- Application
- Product Type
- Technology
- End-User Industry
- Material Type
- Business Model
Regional Dynamics Driving Vertical Boring Mill Adoption
Market momentum varies notably by region, shaped by economic priorities, infrastructure programs, and industrial capabilities. In the Americas, strong automotive production hubs and resurgence in oil and gas exploration drive steady demand for heavy-duty vertical boring mills, with a growing emphasis on retrofit projects to modernize aging fleets. Meanwhile, Europe, the Middle East, and Africa benefit from coordinated industrial initiatives promoting sustainable manufacturing; stringent emissions targets accelerate uptake of energy-efficient hydraulics and closed-loop coolant systems, and partnerships with local service providers enhance aftersales support across diverse markets. In the Asia-Pacific region, rapid expansion of construction equipment production in India and Southeast Asia, alongside advanced aerospace programs in China, fuels investment in high-speed CNC boring centers. In addition, regional governments are incentivizing domestic machine tool inventories through import substitution policies, further stimulating localized manufacturing and technical workforce development in key hubs such as Japan, South Korea, and Australia.
This comprehensive research report examines key regions that drive the evolution of the Vertical Boring Mill market, offering deep insights into regional trends, growth factors, and industry developments that are influencing market performance.
- Americas
- Asia-Pacific
- Europe, Middle East & Africa
Competitive Landscape and Leading Industry Players
The competitive landscape is anchored by global OEMs and specialist integrators who differentiate through technological leadership, service networks, and strategic alliances. DMG MORI and Haas Automation have set benchmarks in user-friendly CNC interfaces and modular automation cells, while Doosan Machine Tools and FPT Industrie S.p.A. emphasize robust spindles and hydraulic systems suited for heavy-duty workloads. European players such as PAMA S.p.A., Fives Group, and Waldrich Siegen Werkzeugmaschinen GmbH leverage deep expertise in large-scale machine construction, often collaborating with alignment feature specialists like TOSHULIN and KURAKI Co., Ltd. to deliver turnkey solutions. In Asia, HYUNDAI WIA Corporation and Toshiba Machine Co., Ltd. combine vertical CNC innovations with extensive local service footprints, while emerging contenders like MAG IAS, LLC and WELE Mechatronic Co., Ltd. are gaining traction through agile manufacturing practices. Meanwhile, niche providers such as Kraft Machinery and EMCO Group excel in refurbishment and aftermarket services, strengthening long-term relationships with manufacturers seeking to extend machine lifecycles.
This comprehensive research report delivers an in-depth overview of the principal market players in the Vertical Boring Mill market, evaluating their market share, strategic initiatives, and competitive positioning to illuminate the factors shaping the competitive landscape.
- DMG MORI
- Doosan Machine Tools
- EMCO Group
- Fives Group
- FPT Industrie S.p.A.
- Haas Automation, Inc.
- HYUNDAI WIA Corporation
- Kraft Machinery
- KURAKI Co., Ltd.
- MAG IAS, LLC
- PAMA S.p.A.
- Toshiba Machine Co., Ltd.
- TOSHULIN, a.s.
- Waldrich Siegen Werkzeugmaschinen GmbH
- WELE Mechatronic Co., Ltd.
Actionable Recommendations for Maximizing Market Position
Industry leaders should prioritize digital transformation by integrating IoT-enabled sensors and advanced analytics to transition from reactive to predictive maintenance models. Investing in multi-axis CNC upgrades for legacy vertical boring mills will enhance throughput and part complexity without significant floor space expansions. To mitigate tariff exposure, companies must adopt flexible sourcing strategies, including dual-sourcing key components and cultivating partnerships with domestic controller and spindle manufacturers. Emphasizing sustainability initiatives-such as closed-loop coolant systems and energy-efficient drives-will not only reduce operational costs but also align with tightening environmental regulations. Strengthening aftermarket services through proactive refurbishment programs and remote diagnostics can generate recurring revenue streams and deepen customer loyalty. Finally, cross-industry collaborations between aerospace, automotive, and heavy equipment sectors will foster best-practice sharing, driving innovation in tooling, fixturing, and process optimization.
Explore AI-driven insights for the Vertical Boring Mill market with ResearchAI on our online platform, providing deeper, data-backed market analysis.
Ask ResearchAI anything
World's First Innovative Al for Market Research
Summarized Conclusions and Strategic Takeaways
The vertical boring mill market is undergoing rapid evolution as digital, material, and regulatory forces converge. Detailed segmentation analysis highlights where precision requirements, production volumes, and business models intersect to unlock competitive advantages. Regional variances underscore the importance of localized strategies that account for tariff frameworks, sustainability mandates, and infrastructure investments. Leading OEMs and service providers are distinguished by their ability to blend advanced CNC technologies with robust support networks, creating resilient value chains that can adapt to shifting market dynamics. By focusing on predictive maintenance, tariff mitigation, sustainability, and aftermarket excellence, industry stakeholders can steer through current complexities and emerge stronger in an increasingly demanding manufacturing environment.
This section provides a structured overview of the report, outlining key chapters and topics covered for easy reference in our Vertical Boring Mill market comprehensive research report.
- Preface
- Research Methodology
- Executive Summary
- Market Overview
- Market Dynamics
- Market Insights
- Cumulative Impact of United States Tariffs 2025
- Vertical Boring Mill Market, by Application
- Vertical Boring Mill Market, by Product Type
- Vertical Boring Mill Market, by Technology
- Vertical Boring Mill Market, by End-User Industry
- Vertical Boring Mill Market, by Material Type
- Vertical Boring Mill Market, by Business Model
- Americas Vertical Boring Mill Market
- Asia-Pacific Vertical Boring Mill Market
- Europe, Middle East & Africa Vertical Boring Mill Market
- Competitive Landscape
- ResearchAI
- ResearchStatistics
- ResearchContacts
- ResearchArticles
- Appendix
- List of Figures [Total: 28]
- List of Tables [Total: 893 ]
Secure Your Comprehensive Market Research Report Now
To access the full breadth of detailed analysis, strategic insights, and implementation frameworks, please reach out to Ketan Rohom, Associate Director, Sales & Marketing, to purchase the comprehensive market research report. His expertise will guide you through tailored solutions and data-driven recommendations designed to inform your next phase of growth.
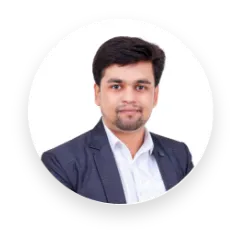
- When do I get the report?
- In what format does this report get delivered to me?
- How long has 360iResearch been around?
- What if I have a question about your reports?
- Can I share this report with my team?
- Can I use your research in my presentation?