Understanding the Growing Significance of Vinyl Plastisol in Modern Industries and the Purpose of This Comprehensive Executive Summary
Vinyl plastisol has evolved into a cornerstone material for diverse industrial applications, prized for its versatility, durability, and cost-effectiveness. Formulated through the dispersion of polyvinyl chloride resin in a liquid plasticizer matrix, this fluid medium transforms into a solid, flexible polymer upon heating. Its capacity to form precise coatings, inks, and molded parts underpins its widespread use in sectors ranging from automotive interiors to decorative textiles, making it an indispensable material in modern manufacturing.
The purpose of this executive summary is to distill the critical findings of an extensive market study into actionable insights. By outlining key market drivers, technological advancements, regulatory pressures, and strategic imperatives, this document equips decision makers with a clear understanding of how vinyl plastisol dynamics are shifting. Readers will gain a concise yet comprehensive overview of cost challenges, emerging application areas, and competitive forces influencing the landscape, laying the groundwork for informed strategy development and investment prioritization.
Exploring Key Technological Regulatory and Sustainability-Driven Transformations Reshaping the Vinyl Plastisol Market Landscape Today
Over the past several years, the vinyl plastisol landscape has undergone a series of transformative shifts driven by technological breakthroughs and evolving regulatory expectations. Breakthroughs in digital printing and advanced roller coating techniques have enabled manufacturers to achieve finer resolution, greater production speeds, and enhanced color fidelity. Concurrently, process optimization through real-time monitoring and predictive maintenance has reduced waste and improved operational consistency, reshaping production paradigms.
Alongside technological advancement, sustainability considerations have redefined market requirements. Increasingly stringent regulations on phthalate-based plasticizers have prompted formulators to integrate bio-based alternatives, driving research into novel plasticizer chemistries. This regulatory impetus dovetails with corporate commitments to reduce environmental footprints, leading to investments in recyclable formulations and energy-efficient curing processes. As a result, market incumbents and new entrants alike are realigning R&D priorities and capital expenditures toward materials and processes that satisfy both performance and sustainability mandates.
Analyzing the Cumulative Effects of 2025 United States Tariffs on Production Costs Supply Chains and Competitive Dynamics in the Vinyl Plastisol Industry
In 2025, aimed at addressing trade imbalances and protecting domestic industry, the United States implemented a new series of tariffs on PVC resin and certain plasticizer imports. These measures have incrementally increased input costs for vinyl plastisol producers, particularly those reliant on resin sourced from overseas suppliers. As costs have risen, manufacturers have been compelled to reassess pricing strategies and absorb margin pressures, triggering price adjustments in coagulants, coatings, and flexible molding applications.
Beyond the immediate cost impact, these tariffs have spurred a strategic pivot toward localized supply chains. Stakeholders are exploring nearshoring opportunities, forming partnerships with North American resin producers, and increasing on-site resin compounding capabilities to mitigate exposure to trade policy volatility. This realignment not only reduces import dependency but also enhances responsiveness to fluctuations in demand. However, it also raises the bar for capital intensity, requiring expanded warehousing and logistical investments to maintain operational agility while safeguarding profitability.
Unveiling Critical Segmentation Insights in Applications Processes Distribution Channels Viscosity and Plasticizer Types Shaping Market Strategies
A nuanced view of the market emerges through deep segmentation across application, process, distribution, type, and plasticizer categories. Within applications, automotive coatings distinguish between aftermarket refinishing demand and original equipment manufacturing, while construction uses range from weather-resistant exterior facades to decorative interior finishes. Packaging subsegments highlight flexible films that benefit from plastisol’s barrier properties and rigid containers that require precise molding characteristics. Textile markets leverage plastisol inks for high-performance apparel, home furnishings that demand wash durability, and industrial fabrics with specialized performance criteria. In wire and cable, insulation applications call for consistent dielectric strength, whereas jacketing relies on resiliency and abrasion resistance.
Process segmentation further clarifies operator decision points, from dip coating techniques suited for continuous profiles to gravure printing and screen printing processes that enable intricate patterning on films and fabrics. Roller coating offers high throughput for large-format substrates, each mode bearing distinct equipment and operational requirements. Distribution channels reveal diverging strategies, with direct sales fostering deep technical partnerships, distributors delivering broad geographic reach, and online platforms catering to low-volume or specialized purchases. Viscosity types span high-, low-, and standard-viscosity plastisols, informing equipment selection and end-use performance. Plasticizer choice, whether phthalate-based for historic formulations or non-phthalate alternatives - both bio-based and oil-based - reflects cost, regulatory, and sustainability trade-offs that shape product portfolios.
This comprehensive research report categorizes the Vinyl Plastisol market into clearly defined segments, providing a detailed analysis of emerging trends and precise revenue forecasts to support strategic decision-making.
- Application
- Process
- Distribution Channel
- Type
- Plasticizer Type
Highlighting Regional Variations and Growth Patterns Across Americas Europe Middle East Africa and Asia Pacific Vinyl Plastisol Demand Dynamics
Regional dynamics underscore how macroeconomic trends, regulatory environments, and end-user industries drive demand. In the Americas, mature automotive and construction markets in the United States and Canada continue to deploy plastisol for value-added coatings and safety-critical components, while growing infrastructure projects in Latin America are fueling incremental demand for durable exterior and flexible packaging solutions. Cross-border trade agreements and nearshoring strategies in this region further influence supply chain configuration and pricing strategies.
Across Europe, the Middle East, and Africa, robust regulatory frameworks such as REACH in the European Union have accelerated the phase-out of legacy plasticizers, prompting widespread adoption of renewable and non-phthalate formulations. Simultaneously, expanding healthcare infrastructure and luxury goods manufacturing in the Middle East and North Africa are driving specialized textile and decorative applications. In Asia-Pacific, rapid urbanization, automotive production growth in China and India, and booming electronics assembly are delivering strong momentum for wire and cable insulation, flexible packaging films, and digital printing consumables, positioning the region as a pivotal engine of global growth.
This comprehensive research report examines key regions that drive the evolution of the Vinyl Plastisol market, offering deep insights into regional trends, growth factors, and industry developments that are influencing market performance.
- Americas
- Europe, Middle East & Africa
- Asia-Pacific
Dissecting Leading Companies’ Strategies Technological Innovations and Partnerships Driving Competitive Advantage in the Vinyl Plastisol Sector
Leading chemical and specialty manufacturers are deploying differentiated strategies to capture value in the evolving vinyl plastisol landscape. Multinational firms are leveraging global R&D networks to accelerate development of next-generation non-phthalate plasticizers, while forming strategic partnerships with resin producers to secure feedstock reliability. Concurrently, several regional players are carving out niches by offering tailored formulations for specific industries such as medical device coatings and high-performance industrial textiles.
Innovation extends beyond chemistry, with key companies investing in digital tools for color matching, process simulation, and predictive maintenance to enhance customer service and minimize downtime. Mergers and acquisitions have consolidated capabilities in processing equipment, enabling integrated solutions that span formulation, compounding, and application services. This convergence of chemical expertise, equipment proficiency, and service-oriented business models is establishing new competitive frontiers in the vinyl plastisol sector.
This comprehensive research report delivers an in-depth overview of the principal market players in the Vinyl Plastisol market, evaluating their market share, strategic initiatives, and competitive positioning to illuminate the factors shaping the competitive landscape.
- Arkema S.A.
- The Lubrizol Corporation
- Teknor Apex Company
- Wacker Chemie AG
- Valtris Specialty Chemicals LLC
- Krempel GmbH
- Vertellus Specialties Inc.
- Polynt-Reichhold S.p.A.
- Ferro Corporation
- Clariant AG
Formulating Actionable Roadmaps for Industry Leaders to Leverage Operational Efficiency Sustainability and Market Differentiation in Vinyl Plastisol
Industry leaders should prioritize the integration of bio-based and oil-based non-phthalate plasticizers to align product portfolios with evolving regulatory frameworks and sustainability commitments. By investing in advanced process technologies such as gravure printing and real-time equipment monitoring, manufacturers can reduce cycle times, lower waste, and deliver consistent quality across diverse application segments. Moreover, establishing strategic alliances with resin suppliers in key regions will help mitigate tariff impacts and stabilize supply chains.
To differentiate in a competitive market, companies must enhance digital engagement through online platforms that support rapid prototyping and small-batch orders, addressing the needs of niche end markets. Expanding direct technical services for formulation optimization and application training can strengthen customer loyalty and justify premium pricing. Finally, continuous investment in R&D to develop low-VOC and high-durability formulations will unlock opportunities in emerging industries, from flexible electronics encapsulation to sustainable building materials.
Detailing Rigorous Research Methodology Including Data Collection Analysis Approaches and Validation Techniques Underpinning This Vinyl Plastisol Study
The research underpinning this study employed a dual-pronged approach, combining extensive secondary data analysis with targeted primary research. Secondary sources included industry journals, regulatory filings, and corporate disclosures, which provided a comprehensive view of market trends, material innovations, and policy developments. Primary insights were gathered through in-depth interviews with manufacturers, distributors, and end-users to validate findings and uncover emerging priorities.
Data triangulation techniques were applied to reconcile quantitative and qualitative inputs, ensuring consistency across demand drivers, cost structures, and technological adoption rates. Segmentation frameworks were rigorously tested through expert panels and field surveys, while supply chain mapping and trade flow analyses provided a clear picture of distribution channel dynamics. All findings were subjected to internal peer review and methodological audits to ensure robust, unbiased conclusions that can inform strategic decision making.
Explore AI-driven insights for the Vinyl Plastisol market with ResearchAI on our online platform, providing deeper, data-backed market analysis.
Ask ResearchAI anything
World's First Innovative Al for Market Research
Summarizing the Strategic Imperatives Growth Opportunities and Future Outlook Shaping the Vinyl Plastisol Market Landscape for Decision Makers
In closing, the vinyl plastisol market is at a critical juncture where innovation, regulation, and trade policy converge to redefine competitive landscapes. Companies that successfully navigate tariff-induced cost pressures and proactively embrace sustainable plasticizer technologies will secure leadership positions. Growth opportunities abound in digital printing, flexible packaging, and specialty coatings, provided organizations invest wisely in process enhancements and strategic partnerships.
Looking ahead, ongoing regulatory shifts will continue to emphasize non-phthalate formulations and circular economy principles, making agility and differentiation vital strategic imperatives. Decision makers should harness the insights presented here to align R&D roadmaps, optimize supply chains, and explore new application frontiers, ensuring that their organizations remain resilient and forward-thinking amidst evolving market complexities.
This section provides a structured overview of the report, outlining key chapters and topics covered for easy reference in our Vinyl Plastisol market comprehensive research report.
- Preface
- Research Methodology
- Executive Summary
- Market Overview
- Market Dynamics
- Market Insights
- Cumulative Impact of United States Tariffs 2025
- Vinyl Plastisol Market, by Application
- Vinyl Plastisol Market, by Process
- Vinyl Plastisol Market, by Distribution Channel
- Vinyl Plastisol Market, by Type
- Vinyl Plastisol Market, by Plasticizer Type
- Americas Vinyl Plastisol Market
- Europe, Middle East & Africa Vinyl Plastisol Market
- Asia-Pacific Vinyl Plastisol Market
- Competitive Landscape
- ResearchAI
- ResearchStatistics
- ResearchContacts
- ResearchArticles
- Appendix
- List of Figures [Total: 28]
- List of Tables [Total: 1002 ]
Engage with Associate Director of Sales and Marketing to Secure Your Comprehensive Vinyl Plastisol Market Research Report Today
To gain access to the full depth of analysis and strategic guidance contained in the comprehensive vinyl plastisol market research report, reach out directly to Ketan Rohom, Associate Director of Sales & Marketing. Ketan brings a wealth of industry knowledge and can provide tailored information on report scope, pricing, and customization options that align with your organizational priorities.
Whether you seek to validate strategic initiatives, explore bespoke data segments, or understand competitive benchmarks in greater detail, Ketan will guide you through the purchasing process. Engage with him today to secure your copy of the report and start leveraging critical market insights that drive growth and innovation in the vinyl plastisol sector.
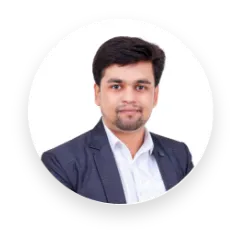
- When do I get the report?
- In what format does this report get delivered to me?
- How long has 360iResearch been around?
- What if I have a question about your reports?
- Can I share this report with my team?
- Can I use your research in my presentation?