Discover the Critical Significance and Integral Role of Advanced Wafer Grinding and Polishing Solutions in Semiconductor Manufacturing Excellence
Wafer grinding and polishing machines serve as the foundational pillar of semiconductor wafer fabrication, ensuring critical surface planarity and defect-free finishes that enable high-yield device manufacturing. These precision systems remove subsurface damage and microscopic irregularities post-wafer slicing, preparing substrates for advanced lithography and doping processes. As semiconductor nodes shrink below seven nanometers, the tolerance for surface variation tightens dramatically, driving demand for ultra-precise material removal and uniformity across ever-larger wafer diameters.
Moreover, the diversification of wafer applications beyond traditional logic and memory chips has elevated the strategic importance of grinding and polishing equipment. The rise of microelectromechanical systems, imaging sensors, photonics, and power electronics introduces varied surface finish requirements-from mirror-like optical surfaces to finely lapped semiconductors. Consequently, equipment providers and end users alike are investing in advanced machine architectures, novel abrasive formulations, and integrated process monitoring to maintain competitive edge and satisfy stringent quality benchmarks.
Uncover the Disruptive Technological and Operational Transformations Reshaping the Wafer Grinding and Polishing Landscape Worldwide
The landscape of wafer grinding and polishing is witnessing unprecedented transformation driven by technological convergence and shifting operational imperatives. Manufacturers are increasingly integrating Internet of Things connectivity and embedded sensors within process chambers to enable real-time monitoring of parameters such as downforce, vibration signatures, and abrasive consumption rates. These developments facilitate predictive maintenance, minimize unplanned downtime, and ensure consistent throughput by adjusting process recipes on the fly.
Furthermore, the incorporation of advanced machine vision and artificial intelligence algorithms is revolutionizing in-line defect detection, allowing automated identification of micro-cracks or edge chipping before they propagate into yield losses. Hybrid grinding polishing platforms, combining coarse grinding wheels with superabrasive pads in a single machine footprint, are emerging as a compelling solution to reduce cycle times and floor space requirements. At the same time, sustainability considerations are reshaping equipment design: closed-loop coolant recycling systems and water-based, biodegradable slurry formulations are reducing waste and cutting environmental impact.
In tandem, facility managers are gravitating toward modular machine architectures that support rapid reconfiguration for multi-wafer diameters and diverse substrate materials. This emphasis on flexibility and adaptive automation underscores a broader shift from fixed-function tooling toward agile, software-defined manufacturing ecosystems that can respond swiftly to evolving chip design roadmaps and end-market demands.
Analyze the Comprehensive Effects of the 2025 United States Tariff Adjustments on Wafer Grinding and Polishing Equipment Supply Chains and Costs
In 2025, a series of applied tariffs on imported equipment components and consumables has materially altered cost structures across the wafer grinding and polishing ecosystem within the United States. Tariffs levied under Section 301 on specific Chinese-origin machinery and abrasive materials have increased landed costs by as much as twenty percent, compelling original equipment manufacturers and end-user fabs to reassess long-standing sourcing strategies.
The imposition of these trade measures has had a cascading effect: higher procurement prices for superabrasive inserts and ceramic grinding wheels have raised per-wafer processing expenses, while delays at port inspections have extended lead times for critical spare parts. To mitigate these challenges, several domestic manufacturers have accelerated the localization of component production, establishing joint ventures with North American tooling suppliers and investing in in-house abrasive media development. Likewise, some fabs have initiated multi-sourcing agreements to blend imports from non-tariffed regions with domestic inventory buffers.
These adaptive measures reflect a broader trend of supply chain resilience, with stakeholders diversifying procurement channels and building strategic stockpiles of high-turn consumables. Although short-term cost pressures remain elevated, the evolving tariff landscape is catalyzing a reconfiguration of industry partnerships, prompting equipment providers to offer extended service contracts and on-site refurbishment programs that reduce total cost of ownership for users.
Illuminate the Critical Market Segmentation Insights Spanning Equipment Types Applications End Users Automation Levels Abrasive Materials and Speed Tiers
Market segmentation unveils a multifaceted view of the wafer grinding and polishing equipment space, beginning with equipment types that range from dedicated grinding systems to hybrid grinding polishing machines and specialized polishing-only platforms. Distinct applications extend across the finishing of microelectromechanical systems wafers, high-precision optical substrates, semiconductor wafer lapping, and high-volume solar wafer grinding, each imposing unique surface requirement demands. Within the customer ecosystem, wafer producers span fabless design houses, large-scale foundries, integrated device manufacturers, and outsourced semiconductor assembly and test providers, underscoring a diversity of production volumes and quality tolerances.
Automation emerges as a critical axis of differentiation, with fully automatic configurations available in both inline and standalone layouts, manual offerings represented by bench top and portable stations, and semi automatic options realized in bench top and floor mounted designs. The choice of abrasive material further segments the market, as users select between cubic and polycrystalline cubic boron nitride media, aluminum oxide or silicon carbide ceramics, and natural or synthetic diamond agents to balance cost, material removal rate, and surface finish quality. Process speed constitutes another layer of segmentation, with low-speed operations below one thousand revolutions per minute reserved for delicate finishing, standard speed runs between one thousand and two thousand rpm for general-purpose throughput, and high-speed applications exceeding two thousand rpm to maximize production efficiency when tolerances allow.
Together, these segmentation insights enable equipment developers and end users to align machine specifications with precise operational requirements, optimize total cost of ownership, and plan capacity expansions that target specific process niches and emerging wafer technology trends.
This comprehensive research report categorizes the Wafer Grinding & Polishing Machine market into clearly defined segments, providing a detailed analysis of emerging trends and precise revenue forecasts to support strategic decision-making.
- Type
- Application
- End User
- Automation Level
- Abrasive Material
- Speed
Explore the Distinct Regional Dynamics Impacting Wafer Grinding and Polishing Market Performance Across the Americas Europe Middle East Africa and Asia Pacific
Regional dynamics play a pivotal role in shaping the competitive landscape for wafer grinding and polishing equipment. In the Americas, robust semiconductor manufacturing investments across the United States and Mexico have spurred demand for high-throughput grinding lines and advanced polishing platforms, particularly to support logic and memory fabs ramping to sub-10-nanometer nodes. Government incentives aimed at reshoring chip production have further accelerated capital equipment procurement and fostered collaborations between domestic vendors and global technology partners.
Across Europe, the Middle East, and Africa, emphasis on specialty applications such as automotive sensor wafers, optical components for industrial imaging, and power electronics substrates has guided equipment selection toward versatile machines capable of handling varied wafer sizes and materials. Regulatory pressures related to sustainability are driving interest in solvent-free slurry systems and water reclamation units, prompting providers to tailor solutions that align with regional environmental standards and circular economy objectives.
In Asia-Pacific, leading markets in Taiwan, South Korea, Japan, and China continue to anchor growth, fueled by extensive foundry operations and consumer electronics supply chains. High-volume solar wafer grinding requirements in certain APAC countries also drive adoption of robust, durable machine frameworks. Meanwhile, emerging Southeast Asian and Indian wafer fabrication hubs are increasingly investing in semi automatic and manual polishing stations as cost-effective entry points, creating a tiered demand pattern within the region that spans basic throughput enhancement to fully automated, industry 4.0–compliant lines.
This comprehensive research report examines key regions that drive the evolution of the Wafer Grinding & Polishing Machine market, offering deep insights into regional trends, growth factors, and industry developments that are influencing market performance.
- Americas
- Europe, Middle East & Africa
- Asia-Pacific
Unveil the Strategic Positions and Innovative Offerings of Leading Manufacturers Driving Competition and Growth in the Wafer Grinding and Polishing Equipment Arena
The competitive environment is defined by an interplay of established global equipment manufacturers and emerging regional specialists offering differentiated service models and technology bundles. Key players have expanded their portfolios to include modular grinding and polishing lines, integrated automation platforms, and digital process monitoring suites, targeting high-mix, low-volume as well as high-volume production segments.
Innovations such as adaptive wheel dressing modules, closed-loop coolant filtration systems, and real-time surface metrology interfaces have become standard offerings among market leaders vying for installed-base growth. Strategic partnerships between machine tool providers and abrasive media suppliers enable bundled service agreements that promise fixed processing costs per wafer, further intensifying competition. At the same time, newer entrants are capturing niche segments by offering portable lapping stations and compact bench top finishers optimized for research labs and small-batch production.
Across the board, aftermarket support and global service networks remain pivotal differentiators. Manufacturers that provide rapid-response maintenance, remote troubleshooting capabilities, and on-site consumable replenishment programs are securing long-term relationships with wafer fabricators and assembly houses, reinforcing their position amid a landscape of continually rising performance expectations.
This comprehensive research report delivers an in-depth overview of the principal market players in the Wafer Grinding & Polishing Machine market, evaluating their market share, strategic initiatives, and competitive positioning to illuminate the factors shaping the competitive landscape.
- Applied Materials, Inc.
- DISCO Corporation
- Okamoto Machine Tool Works, Ltd.
- Lapmaster Wolters LLC
- Ebara Corporation
- Strasbaugh, Inc.
- Peter Wolters GmbH & Co. KG
- SpeedFam Europe N.V.
Define Actionable Strategic Recommendations for Industry Leaders to Capitalize on Emerging Technologies Operational Efficiencies and Market Expansion
Industry leaders can capitalize on market momentum by embedding automation advancements throughout their production workflows, leveraging inline defect detection and adaptive process controls to boost yield and throughput. Collaborative sourcing strategies that combine regional suppliers for high-turn consumables with global partners for precision components will mitigate tariff-induced cost pressures and enhance supply chain agility. Investing in hybrid grinding polishing equipment can consolidate process steps, reduce floor space requirements, and lower total cost of ownership while maintaining the flexibility to support evolving wafer applications.
In parallel, adopting eco-conscious designs-such as water reclamation units, solvent-free slurries, and energy-efficient drive systems-will align operational practices with regulatory and sustainability benchmarks, enabling firms to differentiate on environmental performance. Rolling out digital twins of grinding and polishing process lines can facilitate rapid scenario testing, empower predictive maintenance programs, and shorten qualification cycles for new wafer technologies. Finally, forging closer partnerships with process materials suppliers and end users will generate co-development opportunities for novel abrasive media and machine configurations tailored to next-generation semiconductor, photonics, and solar wafer requirements.
Explain the Rigorous Research Methodology Employed to Gather Data Insights Validate Findings and Ensure Reliability of Wafer Grinding and Polishing Market
This research combines an exhaustive review of secondary sources-ranging from industry journals and technical white papers to patent filings and regulatory disclosures-with primary interviews conducted with equipment OEM executives, material science experts, and key manufacturing decision-makers. Data points from public financial statements and trade association statistics are cross-validated through triangulation methodologies to ensure consistency and accuracy.
Quantitative analyses rely on detailed process mapping and benchmarking exercises, while qualitative insights are refined through expert panel workshops and structured surveys. All collected information undergoes rigorous validation steps, including back-checks with multiple industry stakeholders and reconciliation against historical performance trends. The resulting data framework is structured to support transparent interpretation of segmentation criteria, regional nuances, and competitive strategies, offering users a robust foundation for informed decision-making.
Explore AI-driven insights for the Wafer Grinding & Polishing Machine market with ResearchAI on our online platform, providing deeper, data-backed market analysis.
Ask ResearchAI anything
World's First Innovative Al for Market Research
Summarize Key Findings and Strategic Insights From the Comprehensive Examination of the Wafer Grinding and Polishing Machine Market Landscape
The wafer grinding and polishing equipment market is characterized by rapid technological innovation, shifting trade dynamics, and increasingly nuanced segmentation spanning equipment types, application requirements, end-user profiles, automation tiers, abrasive materials, and process speeds. Recent tariff measures have catalyzed supply chain diversification and localization efforts, while sustainability imperatives continue to reshape machine design and process chemistries. Region-specific trends reveal a bifurcation of demand between high-volume logic and memory fabs in the Americas and Asia-Pacific, and specialty device manufacturing across Europe, the Middle East, and Africa.
Key market participants are enhancing their value propositions through integrated automation, predictive maintenance, and bundled service agreements, with newer entrants targeting research and small-batch segments via portable and bench top solutions. For stakeholders seeking to thrive in this dynamic environment, a clear strategic focus on hybrid process consolidation, digital integration, and eco-efficient operations will be essential. By aligning investments with evolving customer needs and regulatory landscapes, equipment providers and wafer fabricators can secure competitive advantage and foster sustainable growth in the years ahead.
This section provides a structured overview of the report, outlining key chapters and topics covered for easy reference in our Wafer Grinding & Polishing Machine market comprehensive research report.
- Preface
- Research Methodology
- Executive Summary
- Market Overview
- Market Dynamics
- Market Insights
- Cumulative Impact of United States Tariffs 2025
- Wafer Grinding & Polishing Machine Market, by Type
- Wafer Grinding & Polishing Machine Market, by Application
- Wafer Grinding & Polishing Machine Market, by End User
- Wafer Grinding & Polishing Machine Market, by Automation Level
- Wafer Grinding & Polishing Machine Market, by Abrasive Material
- Wafer Grinding & Polishing Machine Market, by Speed
- Americas Wafer Grinding & Polishing Machine Market
- Europe, Middle East & Africa Wafer Grinding & Polishing Machine Market
- Asia-Pacific Wafer Grinding & Polishing Machine Market
- Competitive Landscape
- ResearchAI
- ResearchStatistics
- ResearchContacts
- ResearchArticles
- Appendix
- List of Figures [Total: 30]
- List of Tables [Total: 1348 ]
Take the Next Step to Empower Strategic Planning by Engaging With Our Associate Director to Unlock Tailored Industry Insights
In today’s fast-evolving wafer grinding and polishing market, access to specialized insights can be the difference between incremental improvement and industry leadership.
Reach out directly to our Associate Director to engage in a constructive dialogue about your unique manufacturing challenges and strategic objectives. Through a personalized consultation, you can explore how cutting-edge machine capabilities, tailored service models, and advanced process optimization techniques align with your operational roadmap. This direct engagement empowers your team to accelerate decision-making, reduce time-to-market, and capture emerging opportunities with confidence by leveraging bespoke market intelligence and expert guidance.
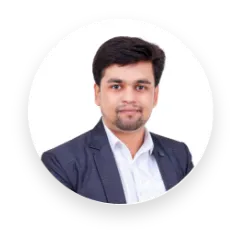
- When do I get the report?
- In what format does this report get delivered to me?
- How long has 360iResearch been around?
- What if I have a question about your reports?
- Can I share this report with my team?
- Can I use your research in my presentation?