Introduction
Wafer grinding wheels play a pivotal role in semiconductor fabrication by ensuring wafer surface flatness, thickness control and surface integrity. As chipmakers push node sizes down, wafer thinning and backside processing requirements have grown more stringent, elevating the performance criteria for abrasive tools. The relentless drive towards 5G connectivity, high-performance computing and electric vehicles is fueling wafer demand across diverse substrates, from silicon to gallium nitride. Manufacturers face mounting pressure to optimize throughput, reduce defect rates and implement environmentally compliant processes, catalyzing innovations in wheel design and process automation. With trade policy shifts and growing geopolitical tensions adding complexity to global sourcing, a holistic perspective on material selection, manufacturing alliances and regional capabilities becomes indispensable. This summary synthesizes these dynamics to equip executives, process engineers and procurement leaders with actionable intelligence for informed decision-making.
Transformative Shifts Reshaping the Wafer Grinding Wheel Arena
The wafer grinding wheel landscape is undergoing a profound transformation driven by material science breakthroughs, digital integration and sustainability imperatives. High-hardness abrasives such as diamond and cubic boron nitride are increasingly supplanting traditional aluminum oxide for applications demanding sub-micron surface finishes. Simultaneously, hybrid bond solutions that blend the toughness of metal matrices with the resilience of resin systems are gaining traction to balance tool life and finish quality. Moreover, the integration of sensors and real-time data analytics within grinding spindles enables predictive maintenance, reducing unplanned downtime and improving yield consistency. Environmental regulations are accelerating the adoption of water-based coolants and closed-loop filtration to minimize waste and ensure worker safety. At the same time, machine-tool manufacturers are embedding advanced motion control and feedback systems to enhance accuracy at higher spindle speeds. As a result, the sector is shifting towards holistic solutions that merge advanced materials, smart equipment and sustainable practices, creating new value propositions for wafer producers.
Assessing the 2025 United States Tariffs and Their Cumulative Impact
The introduction of elevated import duties on wafer grinding wheels and associated abrasive materials by the United States in 2025 has reverberated throughout the supply chain. Manufacturers relying on overseas suppliers have experienced increased landed costs, prompting procurement teams to diversify sourcing strategies and qualify domestic or nearshore vendors. These tariffs have also accelerated vertical integration initiatives, as wafer fabrication facilities seek to internalize wheel production or partner closely with tool makers to mitigate margin pressure. In parallel, extended lead times and customs delays have led to buffer stock strategies, increasing inventory carrying costs and tying up working capital. Equipment OEMs and third-party distributors are adjusting price lists and service agreements to reflect higher cost bases, with some entering cost-share arrangements to maintain competitive pricing. Despite these challenges, the policy shift has incentivized innovation in local manufacturing, and suppliers investing in regional production capabilities are gaining strategic advantage by offering shorter delivery cycles and customized bonding solutions.
Key Segmentation Insights for Abrasive Materials and Bonding Technologies
Material selection and bond technology emerge as critical levers for performance differentiation. Abrasive types range from cost-effective aluminum oxide to ultra-hard CBN, diamond and silicon carbide, each tailored to specific wafer thinning, backside grinding and surface finish requirements. Aluminum oxide remains prevalent for general-purpose grinding, while diamond wheels dominate in high-precision, high-hardness contexts. Silicon carbide abrasives find specialized use in niche applications requiring controlled abrasive wear. On the bonding front, resin bonds offer flexibility and shock resistance, making them suitable for complex geometries. Metal bonded wheels provide rigidity and thermal stability essential for high-speed operations. Vitrified bonds deliver dimensional stability and porosity control, critical for ultra-fine finishing. Hybrid bonds combine these attributes to meet evolving demands for both flatness and surface quality. By aligning abrasive type and bond chemistry with process requirements, manufacturers can optimize wheel life, throughput and yield.
This comprehensive research report categorizes the Wafer Grinding Wheel market into clearly defined segments, providing a detailed analysis of emerging trends and precise revenue forecasts to support strategic decision-making.
- Abrasive Material Type
- Bonding Agent Type
Regional Dynamics Driving Demand Across Key Geographies
Demand patterns vary significantly across the Americas, Europe, Middle East & Africa, and Asia-Pacific regions. In the Americas, a resurgence in domestic chip manufacturing and reshoring initiatives is driving demand for local wheel production, with automotive and aerospace fabs seeking supply chain resilience. In Europe, Middle East & Africa, government-backed semiconductor alliances and sustainability mandates are fostering investments in wafer grinding technologies that support clean production, particularly for power electronics. Asia-Pacific remains the largest regional consumer, powered by established fab hubs in Taiwan, South Korea, Japan and China. Rapid capacity additions in these markets are fueling demand for both standard aluminum oxide wheels and ultra-precision CBN and diamond solutions. Regional service networks and localized technical support capabilities are becoming key differentiators for suppliers seeking to capture share in each geography.
This comprehensive research report examines key regions that drive the evolution of the Wafer Grinding Wheel market, offering deep insights into regional trends, growth factors, and industry developments that are influencing market performance.
- Americas
- Asia-Pacific
- Europe, Middle East & Africa
Competitive Landscape: Profiles of Leading Wafer Grinding Wheel Manufacturers
The competitive landscape is shaped by a diverse set of innovators and incumbents. 3M India leverages its materials expertise to deliver advanced multi-layer abrasive coatings, while Asahi Diamond Industrial Co., Ltd. focuses on precision-engineered diamond wheels for high-hardness applications. Cemat Silicon S.A. specializes in silicon carbide formulations optimized for thin-wafer processing, and Disco Corporation leads in ultra-fine CBN products integrated with automated dressing systems. EHWA Diamond Industrial Co., Ltd. pioneers novel bond matrices, and Husqvarna AB combines global reach with heavy-duty grinding solutions. Kinik Company bridges material science and automation, whereas Mitsubishi Electric Corporation offers fully integrated grinding modules within its semiconductor equipment portfolio. Norton Abrasives prioritizes sustainability in its binder chemistry, and Okamoto Machine Tool Works, Ltd. delivers tightly coupled machine-wheel systems. Saint-Gobain Abrasives, Inc. commands a strong presence in vitrified bonds, Sharp Corp advances micro-abrasive technologies, Shin-Etsu Chemical Co., Ltd. innovates in resin bond resin design, Sumitomo Electric Industries, Ltd. enhances wheel performance with proprietary diamond grades, and Toyoda Van Moppes Ltd. specializes in high-precision ceramic bond solutions.
This comprehensive research report delivers an in-depth overview of the principal market players in the Wafer Grinding Wheel market, evaluating their market share, strategic initiatives, and competitive positioning to illuminate the factors shaping the competitive landscape.
- 3M India
- Asahi Diamond Industrial Co., Ltd.
- Cemat Silicon S.A.
- Disco Corporation
- EHWA Diamond Industrial Co., Ltd.
- Husqvarna AB
- Kinik Company
- Mitsubishi Electric Corporation
- Norton Abrasives
- Okamoto Machine Tool Works, Ltd.
- Saint-Gobain Abrasives, Inc.
- Sharp Corp
- Shin-Etsu Chemical Co., Ltd.
- Sumitomo Electric Industries, Ltd.
- Toyoda Van Moppes Ltd.
Actionable Recommendations for Industry Leaders
Leaders should prioritize a dual approach that couples material innovation with digital enablement. First, invest in next-generation abrasives such as diamond and CBN to support high-hardness and ultra-thinning applications. Second, deploy sensor-based monitoring and predictive analytics to reduce unplanned downtime and ensure consistent surface quality. Third, diversify the supplier base by qualifying regional vendors and forging strategic partnerships to mitigate tariff exposure and logistics disruptions. Fourth, collaborate with equipment integrators to co-develop bonding chemistries and wheel designs tailored to specific process recipes. Fifth, implement circular economy practices by reclaiming worn wheel fragments and engaging recyclers to reclaim valuable abrasive media. Finally, upskill technical teams through targeted training programs on emerging materials, dressing techniques and process controls to accelerate adoption and maintain competitive differentiation.
Explore AI-driven insights for the Wafer Grinding Wheel market with ResearchAI on our online platform, providing deeper, data-backed market analysis.
Ask ResearchAI anything
World's First Innovative Al for Market Research
Conclusion: Navigating Complexity to Achieve Precision
The wafer grinding wheel sector stands at the intersection of advanced materials science, digital transformation and trade policy complexities. Organizations that navigate the cumulative effects of new tariff structures, align material and bond segmentation with process demands, and leverage regional production capabilities will establish a robust competitive position. Integrating smart diagnostics with precision wheel designs can unlock productivity gains, reduce defect rates and lower total cost of ownership. Strategic collaboration across the supply chain-from abrasive manufacturers to equipment OEMs and wafer producers-will be essential to meet the stringent quality requirements of next-generation semiconductor devices. By executing on these strategic imperatives, stakeholders can secure the reliability, efficiency and sustainability needed to thrive in an increasingly demanding market environment.
This section provides a structured overview of the report, outlining key chapters and topics covered for easy reference in our Wafer Grinding Wheel market comprehensive research report.
- Preface
- Research Methodology
- Executive Summary
- Market Overview
- Market Dynamics
- Market Insights
- Cumulative Impact of United States Tariffs 2025
- Wafer Grinding Wheel Market, by Abrasive Material Type
- Wafer Grinding Wheel Market, by Bonding Agent Type
- Americas Wafer Grinding Wheel Market
- Asia-Pacific Wafer Grinding Wheel Market
- Europe, Middle East & Africa Wafer Grinding Wheel Market
- Competitive Landscape
- ResearchAI
- ResearchStatistics
- ResearchContacts
- ResearchArticles
- Appendix
- List of Figures [Total: 20]
- List of Tables [Total: 103 ]
Call to Action: Secure Comprehensive Analysis with Ketan Rohom
To access the complete report and unlock detailed analysis across these critical themes, connect with Ketan Rohom, Associate Director, Sales & Marketing. Secure your copy today to inform strategic decisions with in-depth insights and expert guidance.
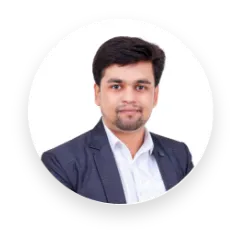
- When do I get the report?
- In what format does this report get delivered to me?
- How long has 360iResearch been around?
- What if I have a question about your reports?
- Can I share this report with my team?
- Can I use your research in my presentation?