Introduction to Wafer Plating Hoods: Foundations and Market Relevance
Wafer plating hoods serve as critical enclosures that maintain the controlled atmospheres necessary for precision deposition processes in semiconductor manufacturing. By regulating chemical vapors, plasma discharges, and particulate containment, these systems underpin the fabrication of advanced nodes and compound semiconductor devices. As device geometries shrink and yield targets rise, the design and performance of plating hoods have become central to reducing contamination risk and ensuring uniform film characteristics.
Recent industry drivers, including the surge in multi-chip module packages and the transition to 3D stacking technologies, place new demands on hood materials, airflow management, and automation. Suppliers are responding by integrating advanced filtration media, corrosion-resistant alloys, and real-time sensor arrays to monitor humidity, temperature, and contaminant levels. Global semiconductor shortages have spurred capacity expansion, driving increased demand for scalable and modular hood solutions that can adapt to high-volume production environments. Additionally, growing emphasis on energy efficiency and environmental sustainability has led OEMs and fab integrators to seek hoods that minimize waste streams and reduce overall facility carbon footprints.
This report introduces the foundational elements of wafer plating hood technology, examines the strategic role these solutions play in modern fabs, and sets the stage for deeper insight into emerging trends, regulatory influences, and competitive dynamics that will shape the market in the years ahead.
Transformative Shifts Shaping the Wafer Plating Hood Industry
In recent years, the landscape for wafer plating hoods has been reshaped by multiple transformative forces. One pivotal shift arises from increased automation and digitalization: robotics and closed-loop control systems now enable dynamic adjustments to chemical flow rates and plasma parameters, enhancing uniformity across large wafer volumes. Concurrently, the proliferation of IoT-enabled sensors and cloud analytics provides manufacturers with real-time insights into process stability, facilitating proactive maintenance and reducing unplanned downtime.
Sustainability imperatives are also driving design innovation, prompting the adoption of recyclable materials and low-energy exhaust and filtration systems that align with global decarbonization targets. At the same time, partnerships between equipment vendors and semiconductor fabricators are accelerating, fostering co-development of modular hoods that can be rapidly reconfigured for multiple applications. Another key trend lies in the emergence of digital twin modeling, which allows engineers to simulate airflow dynamics and contaminant behavior before capital deployment, cutting validation cycles by weeks.
Moreover, in response to recent supply chain disruptions, manufacturers are diversifying supplier networks and exploring nearshoring strategies to ensure continuity of critical hood components such as blower assemblies, gasket materials, and optical sensors. Regulatory compliance demands, particularly in regions with stringent emissions and worker safety standards, further incentivize continuous product refinement and localized service ecosystems. Advances in nanostructured coatings are expanding functional capabilities, endowing hoods with self-cleaning surfaces and enhanced chemical resistance. These converging trends are redefining competitive advantage in wafer plating hood design, emphasizing flexibility, intelligence, and sustainability as the hallmarks of next-generation equipment.
Cumulative Impact of U.S. Tariffs in 2025 on Wafer Plating Hood Ecosystem
Beginning in early 2025, the United States introduced a structured set of tariffs targeting the import of specialized semiconductor manufacturing equipment, including wafer plating hood assemblies and critical consumables. The cumulative effect of these measures has been a pronounced rise in landed costs for metallic components such as stainless steel and aluminum, as well as for certain polymeric substrates. In response, many OEMs have accelerated the shift toward localized production, establishing fabrication hubs in tariff-exempt zones and forging strategic alliances with domestic sheet metal and composite suppliers.
End-users have mitigated cost exposure by renegotiating service contracts to encompass parts, maintenance, and upgrade modules under extended warranties. These adjustments have altered procurement timelines, with capital expenditure approvals now incorporating total cost of ownership assessments that account for duty rates and potential trade policy changes. The tariffs have also catalyzed innovation in material sourcing, as engineers experiment with alternative alloys and high-performance coatings to balance durability, contamination control, and cost-effectiveness.
At the same time, the specter of additional duties has prompted broader supply chain risk management practices, including dual sourcing and buffer stock strategies. As companies monitor impending trade negotiations and assess the likelihood of reciprocal measures abroad, they are poised to refine their competitive playbooks, balancing near-term operational demands with long-term strategic resilience. Collectively, these developments underscore the importance of agility in equipment design, supplier engagement, and corporate planning to navigate evolving trade landscapes.
Comprehensive Segmentation Insights across Materials, Industries, Technologies, and Applications
A granular examination of the wafer plating hood market reveals seven critical segmentation dimensions that inform competitive strategies and product development roadmaps. Material type considerations span composite enclosures, notably fiberglass reinforced panels, alongside metallic variants such as aluminum and stainless steel, with plastic alternatives including ABS, polycarbonate, and PVC addressing cost-sensitive or weight-restricted applications. End-user industries range from aerospace and defense-where hoods support both aircraft systems and space exploration components-to electronics, serving both consumer and industrial segments, and semiconductor manufacturing, which encompasses chip fabrication facilities and microelectromechanical systems producers.
Technology type segmentation differentiates chemical vapor deposition methods, including atmospheric and metal–organic CVD, from electroplating approaches like barrel and rack plating, as well as physical vapor deposition processes such as evaporation and sputtering. Application-level insights cover decorative coatings focused on aesthetic design and surface finish, functional coatings aimed at conductivity enhancement and optical performance, and protective coatings that deliver corrosion protection and wear resistance. Component type analysis distinguishes chamber components, plating hoods, and wafer categories, with wafers further segmented into compound semiconductor and silicon variants.
Equipment classifications include fully automated systems integrated into assembly lines, traditional manual setups, and semi-automated units requiring operator assistance. Finally, market player types are defined by business models-spanning B2B and B2C frameworks-and by establishment types, from OEMs to third-party service providers. These segmentation insights provide a comprehensive framework for aligning product features with evolving market demands.
This comprehensive research report categorizes the Wafer Plating Hood market into clearly defined segments, providing a detailed analysis of emerging trends and precise revenue forecasts to support strategic decision-making.
- Material Type
- End-user Industry
- Technology Type
- Application Type
- Component Type
- Equipment Type
- Market Player Type
Key Regional Insights Informing Strategic Approaches
The wafer plating hood market exhibits distinct regional characteristics driven by local manufacturing priorities, regulatory frameworks, and investment trends. In the Americas, the combination of established semiconductor fabs in the United States and Canada, along with emerging capacity in Mexico and Brazil, generates demand for high-throughput automation and robust contamination control systems. US regulatory agencies’ focus on worker safety and emissions further elevates the importance of compliance-ready exhaust and filtration technologies.
In Europe, Middle East & Africa, mixed regulatory environments and a strong emphasis on standardization have led to widespread adoption of modular hood platforms that can be configured to meet varied national standards across the region. Sustainability targets within the European Union and Middle Eastern free zones underscore the need for energy-efficient designs and materials recycling initiatives, while growing fab investments in Israel and Turkey introduce niche opportunities for specialized hood configurations.
The Asia-Pacific region remains the largest market, propelled by aggressive expansion in China, Taiwan, South Korea, and Japan. Here, gigafab projects and advanced node transitions demand hoods equipped with real-time monitoring and predictive maintenance capabilities, supported by local service networks. Across all regions, collaboration between global technology providers and regional integrators ensures solutions can be tailored to specific end-user requirements and supply chain dynamics.
This comprehensive research report examines key regions that drive the evolution of the Wafer Plating Hood market, offering deep insights into regional trends, growth factors, and industry developments that are influencing market performance.
- Americas
- Asia-Pacific
- Europe, Middle East & Africa
Key Company Profiles and Competitive Dynamics
The competitive landscape for wafer plating hoods is shaped by a mix of global leaders and regional innovators, each leveraging distinct strengths to capture market share. Applied Materials, Inc. invests in advanced flow-control mechanisms and sensor integration to boost hood throughput and process stability, while ASM International N.V. applies its deposition expertise to refine hood-enclosure interfaces for critical node applications. ASM Pacific Technology Ltd. and Axcelis Technologies, Inc. focus on expanding their field service capabilities to deliver end-to-end deployment support, complemented by Hitachi High-Tech Corporation’s precision machining and material science advancements.
KLA Corporation and Lam Research Corporation integrate cutting-edge metrology and process control software into their hood systems, enabling seamless data exchange with fab networks. Lattice Semiconductor Corporation explores next-generation coating chemistries to enhance functional performance, as Rudolph Technologies under Onto Innovation Inc. tailors solutions for niche wafer formats. Samsung Foundry’s internal developments set high benchmarks for reliability and cycle efficiency, while SCREEN Holdings Co., Ltd. and Semes Co., Ltd. strengthen regional after-sales support across APAC.
Shibaura Mechatronics Corporation and Tokyo Electron Limited (TEL) emphasize modular architectures that facilitate rapid reconfiguration for multi-product lines. Veeco Instruments Inc. rounds out the field by targeting specialized applications in compound semiconductor wafer processing. Together, these companies drive innovation through strategic partnerships, R&D investments, and service network expansion, shaping the future direction of wafer plating hood technology.
This comprehensive research report delivers an in-depth overview of the principal market players in the Wafer Plating Hood market, evaluating their market share, strategic initiatives, and competitive positioning to illuminate the factors shaping the competitive landscape.
- Applied Materials, Inc.
- ASM International N.V.
- ASM Pacific Technology Ltd.
- Axcelis Technologies, Inc.
- Hitachi High-Tech Corporation
- KLA Corporation
- Lam Research Corporation
- Lattice Semiconductor Corporation
- Rudolph Technologies, Inc. (Onto Innovation Inc.)
- Samsung Foundry
- SCREEN Holdings Co., Ltd.
- Semes Co., Ltd.
- Shibaura Mechatronics Corporation
- Tokyo Electron Limited (TEL)
- Veeco Instruments Inc.
Actionable Recommendations for Industry Leadership and Growth
To thrive in the evolving wafer plating hood market, industry leaders must adopt a multi-faceted approach that balances technological innovation, operational resilience, and customer-centric service models. First, investing in advanced sensor networks and IoT platforms will enable real-time process monitoring and predictive maintenance, reducing unplanned downtime and enhancing overall equipment effectiveness. Diversifying supply chains by establishing relationships with regional fabricators and alternative raw material suppliers will mitigate exposure to trade policy fluctuations and logistical disruptions.
Embracing modular hood designs with standardized interfaces accelerates installation timelines and simplifies future upgrades, while digital twin simulations can validate performance parameters before physical deployment, reducing commissioning cycles. Sustainability should be integrated into product development, with a focus on energy-efficient exhaust systems, recyclable materials, and closed-loop chemical recycling processes that align with global environmental regulations. Strengthening cross-functional collaboration between R&D, manufacturing, and field service teams will foster rapid innovation and streamline feedback loops.
Developing targeted workforce training programs in smart manufacturing and contamination-control best practices will equip engineers and technicians to manage increasingly complex hood systems. Finally, engaging in strategic partnerships with academic institutions and industry consortia can drive joint research initiatives, ensuring access to emerging materials and process breakthroughs that deliver competitive differentiation.
Explore AI-driven insights for the Wafer Plating Hood market with ResearchAI on our online platform, providing deeper, data-backed market analysis.
Ask ResearchAI anything
World's First Innovative Al for Market Research
Conclusion: Charting a Path Forward in Wafer Plating Hood Innovation
As wafer plating hoods become ever more integral to advanced semiconductor and compound wafer production, the convergence of digitalization, automation, and sustainability will define the next generation of system design. The strategic integration of real-time monitoring, modular architectures, and eco-friendly materials will empower manufacturers to meet aggressive performance and environmental targets. Regional market nuances-shaped by local regulations, investment incentives, and supply chain configurations-underscore the necessity of adaptable solutions that can be customized for specific fab environments.
Trade policies and tariff measures have highlighted the importance of supply chain agility, prompting a reevaluation of sourcing strategies and nearshoring opportunities. By synthesizing segmentation insights across materials, technologies, applications, and end-user industries, stakeholders can align product roadmaps with evolving customer needs. Collaboration between equipment vendors, service providers, and fabricators will remain crucial for accelerating innovation cycles and maintaining operational excellence.
Ultimately, organizations that embrace a proactive approach to design optimization, strategic partnerships, and sustainability will secure a competitive advantage in the dynamic wafer plating hood market, ensuring high yields, improved throughput, and resilient manufacturing ecosystems.
This section provides a structured overview of the report, outlining key chapters and topics covered for easy reference in our Wafer Plating Hood market comprehensive research report.
- Preface
- Research Methodology
- Executive Summary
- Market Overview
- Market Dynamics
- Market Insights
- Cumulative Impact of United States Tariffs 2025
- Wafer Plating Hood Market, by Material Type
- Wafer Plating Hood Market, by End-user Industry
- Wafer Plating Hood Market, by Technology Type
- Wafer Plating Hood Market, by Application Type
- Wafer Plating Hood Market, by Component Type
- Wafer Plating Hood Market, by Equipment Type
- Wafer Plating Hood Market, by Market Player Type
- Americas Wafer Plating Hood Market
- Asia-Pacific Wafer Plating Hood Market
- Europe, Middle East & Africa Wafer Plating Hood Market
- Competitive Landscape
- ResearchAI
- ResearchStatistics
- ResearchContacts
- ResearchArticles
- Appendix
- List of Figures [Total: 30]
- List of Tables [Total: 1114 ]
Take the Next Step: Secure In-Depth Market Research Insight Today
For a comprehensive understanding of these strategic insights and to access detailed analysis across technologies, regions, and competitive landscapes, connect with Ketan Rohom, Associate Director, Sales & Marketing. Explore how tailored market intelligence can inform your strategic planning, product development, and investment decisions. Reach out today to secure your copy of the full market research report and position your organization at the leading edge of wafer plating hood innovation.
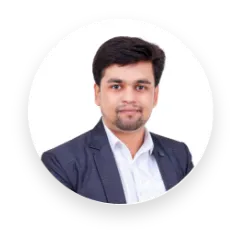
- When do I get the report?
- In what format does this report get delivered to me?
- How long has 360iResearch been around?
- What if I have a question about your reports?
- Can I share this report with my team?
- Can I use your research in my presentation?