Navigating the Emergence of Waterborne Industrial Anti-Corrosion Coatings
Waterborne industrial anti-corrosion coatings have become pivotal in safeguarding critical infrastructure, driven by an intensified focus on environmental stewardship and regulatory compliance. As global stakeholders seek sustainable solutions, waterborne systems offer a compelling alternative to solvent-borne formulations, reducing volatile organic compound emissions while delivering robust barrier performance. The shift toward waterborne technologies reflects broader industry trends: heightened scrutiny of ecological footprints, tighter emission limits, and the pursuit of cost-efficient maintenance regimes.
Manufacturers are now harnessing advances in polymer science and formulation chemistry to optimize adhesion, chemical resistance, and durability. These innovations enable waterborne coatings to match or exceed the performance of traditional solvent-based counterparts, even under demanding operational conditions. Concurrently, emerging applications across construction, energy, marine, and oil & gas sectors underscore the versatility of waterborne anti-corrosion systems, from protecting offshore platforms to reinforcing bridge superstructures.
This introduction sets the stage for a detailed exploration of transformative market forces, tariff impacts, segmentation nuances, regional dynamics, and competitive strategies. By unpacking these dimensions, industry leaders can navigate the evolving landscape with clarity, align investments with future priorities, and capitalize on the rapid momentum behind waterborne anti-corrosion coatings.
Key Drivers Reshaping the Anti-Corrosion Coating Landscape
The anti-corrosion coating landscape is undergoing transformative shifts driven by regulatory, technological, and market imperatives. Stringent environmental regulations in major economies are accelerating the phase-out of high-VOC solvent-based formulations, prompting widespread adoption of waterborne alternatives. In parallel, growing corporate sustainability commitments are elevating green coating credentials as a strategic differentiator.
Technological breakthroughs in nanomaterials and self-healing chemistries are enhancing coating longevity and reducing total lifecycle costs. Digitalization is also making inroads, with predictive maintenance platforms leveraging sensor-embedded coatings to monitor corrosion activity in real time. These platforms enable proactive intervention, extending asset service life and minimizing downtime. Moreover, the integration of bio-based additives and recycled content reflects a holistic approach to circularity, further strengthening environmental value propositions.
Transitioning from conventional methods, key players are reengineering supply chains to source sustainable raw materials and streamline production processes. This agility positions them to respond swiftly to emerging market demands, from renewable energy installations to next-generation marine vessels. As a result, waterborne anti-corrosion coatings are not merely incremental improvements but catalysts of a broader industrial transformation, reshaping competitive dynamics and creating new opportunities for innovators.
Assessing the Cumulative Effects of 2025 U.S. Tariffs on Coatings
The cumulative impact of United States tariffs on imports of coating raw materials and equipment has reshaped cost structures and sourcing strategies across the industry. Since the introduction of Section 232 steel and aluminum tariffs and Section 301 measures on specialty chemicals, manufacturers have encountered elevated input costs and supply chain volatility. Domestic producers have responded by diversifying supplier portfolios, forging deeper partnerships with local chemical manufacturers, and negotiating long-term contracts to stabilize pricing.
In response, several coating formulators have relocated key processing steps closer to raw material sources or invested in backward integration to mitigate exposure. These measures have alleviated tariff-induced pressures but have also driven consolidation among mid-sized players unable to absorb sustained cost increases. Conversely, leading multinational suppliers have leveraged their global footprint to arbitrage regional cost differentials, shifting production volumes to non-tariffed markets and optimizing logistics networks.
Looking ahead, the lingering effects of these measures underscore the importance of supply chain resilience. Companies that proactively map tariff vulnerabilities, implement agile procurement protocols, and engage in strategic hedging will be best positioned to maintain margin stability and competitive pricing. This environment also favors those capable of rapidly recalibrating manufacturing footprints to align with evolving trade policies.
Comprehensive Insights Across Market Segmentation Dimensions
A multi-dimensional segmentation framework reveals nuanced opportunities across the waterborne industrial anti-corrosion market. In terms of type, acrylic variants-ranging from solvent-based acrylic to waterborne acrylic-offer cost-effective, fast-drying options, while epoxy categories such as fusion bonded epoxy, two-component epoxy, and waterborne epoxy deliver superior mechanical strength and chemical resistance. Aliphatic and aromatic polyurethane formulations provide UV stability and abrasion resistance, catering to applications with aesthetic and durability demands.
Examining end-use industries, coating specifications vary significantly between construction ventures-encompassing bridges, roads, and tunnels-and energy installations where conventional power plants and renewable energy platforms demand rigorous protection. Marine applications for commercial shipping and naval vessels impose strict performance benchmarks in corrosive saltwater environments, whereas offshore platforms and pipelines in the oil & gas sector require coatings that withstand extreme temperatures and hydrocarbon exposure.
Coating technology segmentation highlights powder coating subdivisions-thermoplastic and thermoset-and solvent-borne options including high solids and low solvent formulations. Within waterborne systems, distinctions between coalescing agents and self-crosslinking coatings influence application efficiency and film hardness. Application methods-detail brush, flat brush, microfiber and short nap rollers, airless and conventional spray-further refine performance characteristics and labor requirements. Functionality segmentation underscores the strategic choice between barrier protection such as vapor barriers and waterproofing, cathodic protection via impressed current or sacrificial anode systems, and inhibitor protection mechanisms ranging from organic inhibitors to reactive pigments. Lastly, formulation considerations weigh single-component pre-catalyzed or post-catalyzed options against multi-component systems offering tailored component ratios for specialized performance.
This comprehensive research report categorizes the Waterborne Industrial Anti-Corrosion Coating market into clearly defined segments, providing a detailed analysis of emerging trends and precise revenue forecasts to support strategic decision-making.
- Type
- End-Use Industry
- Coating Technology
- Application Method
- Functionality
- Formulation
Regional Dynamics Defining Waterborne Coating Adoption
Regional dynamics continue to shape waterborne anti-corrosion coating adoption, driven by local regulations, infrastructure projects, and industrial growth trajectories. In the Americas, stringent environmental mandates in North America and growing infrastructure investment in Latin America have elevated demand for low-VOC, high-performance solutions. Manufacturers are capitalizing on near-shoring trends and leveraging regional free trade agreements to optimize supply chains.
Europe, the Middle East and Africa present a diverse regulatory landscape where the European Union’s Green Deal targets have accelerated the transition to waterborne systems, while Gulf Cooperation Council nations prioritize corrosion control for oil and gas assets. African markets, though nascent, are witnessing gradual uptake as modernization programs expand power generation and transportation networks.
The Asia-Pacific region remains the largest consumption hub, propelled by rapid industrialization, renewable energy projects, and maritime trade expansion. China’s rigorous air quality standards and India’s infrastructure modernization are catalyzing local production capacities, whereas Southeast Asian economies are emerging as strategic export bases. Collectively, these regional trends underscore the need for tailored market entry strategies that account for regulatory variability, logistical complexities, and end-user requirements.
This comprehensive research report examines key regions that drive the evolution of the Waterborne Industrial Anti-Corrosion Coating market, offering deep insights into regional trends, growth factors, and industry developments that are influencing market performance.
- Americas
- Asia-Pacific
- Europe, Middle East & Africa
Competitive Landscape: Leading Players Driving Innovation
The competitive landscape is characterized by both global conglomerates and specialized innovators, each leveraging unique strengths to capture market share. 3M Company focuses on advanced polymer research and integrated corrosion monitoring systems, enhancing product differentiation. AkzoNobel N.V. emphasizes sustainability pledges, channeling R&D into low-emission waterborne formulations. Axalta Coating Systems, LLC integrates digital application technologies to streamline on-site performance validation.
BASF SE leads in chemical innovation, with proprietary resin technologies that bolster coating durability. Hempel Group combines marine heritage with green chemistry, targeting offshore and shipping clientele. Jotun Group prioritizes service-oriented models, offering turnkey coating lifecycle management. Kansai Paint Co., Ltd. leverages automotive coating expertise to introduce high-durability waterborne variants into industrial segments.
Nippon Paint Holdings Co., Ltd. invests heavily in regional manufacturing networks, ensuring rapid product localization. PPG Industries, Inc. blends pigment technology with corrosion inhibitors to expand protective functionality. Sherwin-Williams Company employs a broad distribution footprint and technical training programs to support applicators and end users. As each leader refines its strategic focus-be it through acquisitions, joint ventures, or green chemistry partnerships-the race for market primacy intensifies.
This comprehensive research report delivers an in-depth overview of the principal market players in the Waterborne Industrial Anti-Corrosion Coating market, evaluating their market share, strategic initiatives, and competitive positioning to illuminate the factors shaping the competitive landscape.
- 3M Company
- AkzoNobel N.V.
- Axalta Coating Systems, LLC
- BASF SE
- Hempel Group
- Jotun Group
- Kansai Paint Co., Ltd.
- Nippon Paint Holdings Co., Ltd.
- PPG Industries, Inc.
- Sherwin-Williams Company
Strategic Recommendations for Industry Leaders
Industry leaders must adopt a proactive stance to secure sustainable growth and operational resilience in the evolving waterborne anti-corrosion segment. First, prioritize robust R&D investments in next-generation resin chemistries and bio-based additives to anticipate tightening environmental standards. Simultaneously, integrate digital inspection and monitoring platforms to offer value-added services and build closer client relationships.
Second, diversify sourcing strategies by forging strategic partnerships with regional raw material suppliers and exploring backward integration opportunities. This approach will mitigate tariff risks and currency fluctuations while enhancing supply chain transparency. Third, tailor product portfolios to specific end-use requirements by leveraging application-method optimization, functionality layering, and formulation customization to meet nuanced performance benchmarks.
Fourth, deploy localized go-to-market models that account for regional regulatory nuances, infrastructure development pipelines, and cultural preferences. Establish technical training centers to elevate applicator proficiency and foster brand loyalty. Finally, pursue targeted collaborations with industry associations and regulatory bodies to shape emerging standards, ensuring that new regulations align with practical performance criteria and sustainability goals.
Explore AI-driven insights for the Waterborne Industrial Anti-Corrosion Coating market with ResearchAI on our online platform, providing deeper, data-backed market analysis.
Ask ResearchAI anything
World's First Innovative Al for Market Research
Concluding Perspectives on the Market’s Evolution
The waterborne industrial anti-corrosion coating sector stands at a strategic inflection point, where environmental imperatives, technological innovation, and evolving trade policies converge to redefine competitive boundaries. Companies that harness advanced polymer research, embrace digital transformation, and cultivate supply chain agility will unlock new avenues for differentiation. Meanwhile, a clear understanding of segmentation subtleties-from resin types and application methods to regional market idiosyncrasies-will enable precise targeting and enhanced value delivery.
As the market matures, collaboration across the value chain-from raw material suppliers through applicators to end users-will prove instrumental in accelerating adoption and refining performance standards. By aligning strategic investments with these market realities, organizations can both meet regulatory obligations and exceed customer expectations. Ultimately, success will hinge on the ability to anticipate shifts, adapt swiftly, and lead with solutions that balance ecological responsibility and operational excellence.
This section provides a structured overview of the report, outlining key chapters and topics covered for easy reference in our Waterborne Industrial Anti-Corrosion Coating market comprehensive research report.
- Preface
- Research Methodology
- Executive Summary
- Market Overview
- Market Dynamics
- Market Insights
- Cumulative Impact of United States Tariffs 2025
- Waterborne Industrial Anti-Corrosion Coating Market, by Type
- Waterborne Industrial Anti-Corrosion Coating Market, by End-Use Industry
- Waterborne Industrial Anti-Corrosion Coating Market, by Coating Technology
- Waterborne Industrial Anti-Corrosion Coating Market, by Application Method
- Waterborne Industrial Anti-Corrosion Coating Market, by Functionality
- Waterborne Industrial Anti-Corrosion Coating Market, by Formulation
- Americas Waterborne Industrial Anti-Corrosion Coating Market
- Asia-Pacific Waterborne Industrial Anti-Corrosion Coating Market
- Europe, Middle East & Africa Waterborne Industrial Anti-Corrosion Coating Market
- Competitive Landscape
- ResearchAI
- ResearchStatistics
- ResearchContacts
- ResearchArticles
- Appendix
- List of Figures [Total: 28]
- List of Tables [Total: 1073 ]
Next Steps: Connect with Ketan Rohom to Access the Full Report
To gain deep insights and actionable intelligence on the waterborne industrial anti-corrosion coating market, contact Ketan Rohom (Associate Director, Sales & Marketing at 360iResearch). Secure your copy of the comprehensive report today to inform strategic decisions and stay ahead of industry trends.
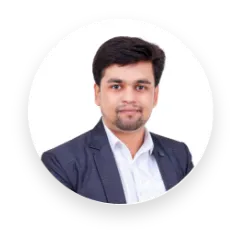
- When do I get the report?
- In what format does this report get delivered to me?
- How long has 360iResearch been around?
- What if I have a question about your reports?
- Can I share this report with my team?
- Can I use your research in my presentation?