Introduction to the Dynamic Welding Gear Ecosystem
The welding gear market lies at the heart of modern manufacturing and infrastructure development, serving industries as diverse as automotive, aerospace, construction, and oil and gas. With ongoing shifts toward automation, digitalization, and sustainability, welding equipment and consumables have evolved far beyond traditional arc torches and filler metals. Innovations such as robotic welding cells, inverter-based power sources, and solid-state joining techniques are rapidly redefining productivity benchmarks, safety standards, and material compatibility.
As manufacturers navigate complex supply chains, volatile raw‐material costs, and ever‐stricter regulatory frameworks, a nuanced understanding of the current landscape becomes vital. This executive summary distills the most influential drivers, emerging technologies, and competitive dynamics shaping the sector. Drawing on segmentation, regional trends, and corporate strategies, it equips decision-makers with the insights needed to align investment priorities, optimize product portfolios, and capitalize on new growth corridors. Seamlessly linking strategic analysis with practical recommendations, this overview sets the stage for informed action in a market defined by constant innovation and competitive intensity.
Transformative Technological and Operational Shifts
Over the past decade, welding gear has undergone transformative shifts propelled by converging trends in automation, advanced materials, and environmental stewardship. Industry 4.0 principles now permeate welding floors, as sensors and real-time data analytics enable predictive maintenance, process optimization, and quality assurance. Robotic welding cells equipped with vision systems deliver repeatable precision in high-volume applications, while collaborative robots bridge the gap between manual and fully automated workflows.
Simultaneously, solid-state welding methods-such as ultrasonic and friction techniques-are gaining traction for their low-heat input and minimal distortion, opening possibilities for sensitive alloys like aluminum and titanium. At the same time, strict emissions standards and energy-efficiency targets are driving adoption of inverter-based power sources and eco-friendly shielding gases. As manufacturers embrace digital welding platforms that integrate cloud connectivity and remote diagnostics, they stand to reduce downtime, improve safety, and lower total cost of ownership. Thus, the welding landscape is rapidly transitioning from traditional hardware to intelligent, sustainable solutions.
Assessing the 2025 U.S. Tariff Impact on Welding Equipment
In early 2025, new import duties across a broad array of welding equipment and consumables reshaped procurement strategies and cost structures. Tariff adjustments on key components-ranging from power sources to specialized torches-have elevated input costs by up to double‐digit percentages in certain segments. In response, many OEMs and end users have accelerated efforts to localize production, forging partnerships with domestic fabricators and contract manufacturers to insulate themselves from import surcharges.
These measures have spurred investment in regional manufacturing hubs, allowing companies to mitigate currency fluctuations and logistical bottlenecks. At the same time, incumbents are reexamining pricing models and seeking design innovations that offset cost pressures, such as modular power systems and simplified consumable architectures. Collectively, these strategic shifts underscore a broader trend: supply chain resilience now commands as much attention as process efficiency and product performance.
Comprehensive Segmentation Analysis and Strategic Implications
A detailed segmentation analysis reveals a multifaceted market structure. When viewed by product type, arc welding equipment still commands significant market share due to its versatility, while oxy-fuel units maintain relevance in maintenance operations. Resistance welding remains indispensable for battery assembly and electronics, and the solid-state category-comprising explosion, friction, and ultrasonic welding subtypes-is emerging as the fastest-growing segment, prized for low distortion and high joint integrity.
Examining technology, automatic welding systems continue to dominate large-scale production lines, but demand for manual torches and semi-automatic benches remains robust among maintenance crews and small workshops. Robotic welding technology is surging as manufacturers seek precision and repeatability, with collaborative systems lowering the entry barrier for mixed human-robot cells.
Material type segmentation highlights steel’s enduring footprint across heavy industries, while aluminum’s lightweight properties drive growth in automotive and aerospace applications. Alloy and titanium welding solutions are carving out niche roles in high-performance sectors.
From an end-user industry perspective, aerospace and defense demand ultra-precise welding processes, whereas automotive bolsters volumes, particularly in passenger vehicles, followed by commercial trucks. Construction, oil and gas, and shipbuilding uphold steady consumption, each with unique process prerequisites.
Process segmentation shows gas metal arc welding as a workhorse for speed and penetration, gas tungsten arc welding prized for finesse on thin materials, shielded metal arc welding favored for field repair, and submerged arc welding deployed in high-throughput fabrications.
In terms of application, fabrication shops lead the consumption of advanced gear, followed by maintenance and repair units that value portability and ease of use. Transportation and warehouse operations increasingly leverage automated welding cells to support just-in-time workflows.
User type analysis underscores industrial users as the primary investors in high-end, fully automated systems, while welding professionals seek specialized solutions with integrated monitoring. At the entry level, home users and hobbyists fuel demand for compact, semi-automatic machines with intuitive interfaces.
This comprehensive research report categorizes the Welding Gear market into clearly defined segments, providing a detailed analysis of emerging trends and precise revenue forecasts to support strategic decision-making.
- Product Type
- Technology
- Material Type
- End-User Industry
- Process
- Application
- User Type
Key Regional Market Dynamics and Growth Drivers
Regional dynamics underscore the market’s geographical diversity. In the Americas, substantial manufacturing bases in North America and growing nearshore operations in Mexico drive demand for both legacy arc welders and cutting-edge robotic cells. Brazil and Argentina also contribute through infrastructure projects and energy sector expansions.
Europe, the Middle East and Africa reflect a blend of mature markets and emerging opportunities. Western European countries prioritize green welding solutions in alignment with stringent environmental regulations, while Eastern Europe’s automotive clusters spur high-volume equipment purchases. In the Middle East and Africa, oil, gas, and heavy construction projects underpin steady demand for rugged, field-ready welding systems.
Asia-Pacific stands out as a powerhouse of consumption and innovation. China’s industrial modernization continues to fuel broad uptake of inverter technology and automation, Japan and South Korea invest heavily in robotics integration, and Southeast Asian nations are rapidly adopting welding gear for expanding automotive, shipbuilding, and infrastructure sectors.
This comprehensive research report examines key regions that drive the evolution of the Welding Gear market, offering deep insights into regional trends, growth factors, and industry developments that are influencing market performance.
- Americas
- Asia-Pacific
- Europe, Middle East & Africa
Competitive Landscape and Leading Supplier Strategies
Leading suppliers are differentiating through technology leadership, global reach, and comprehensive service ecosystems. ABICOR BINZEL USA enhances torch ergonomics and consumable lifecycles by leveraging advanced materials and modular designs. Air Liquide S.A. capitalizes on its global gas-supply network to bundle shielding solutions with welding equipment, fostering customer loyalty through seamless integration.
Daihen Corporation specializes in robotic welding systems with proprietary control algorithms, targeting high-speed manufacturing lines, while ESAB’s broad portfolio spans manual torches to fully automated cells, reinforced by strategic acquisitions that deepen its product breadth. Fronius International GmbH pushes inverter power-source innovation, focusing on energy efficiency and remote diagnostics, whereas Hobart Welding Products addresses light industrial and consumer segments with accessible, user-friendly machines.
Hypertherm, Inc. extends its plasma cutting expertise into hybrid welding-cutting solutions, catering to fabrication shops seeking process consolidation. Kemppi Oy drives digital welding trends via cloud-enabled platforms that capture weld data for quality assurance and training purposes. KOBE Steel’s (KOBELCO) integration of steel production and welding equipment production creates synergies in material compatibility and cost control.
Lincoln Electric Holdings, Inc. combines training services with equipment sales to cultivate skilled operators and foster brand loyalty. Miller Electric Mfg. LLC leverages its extensive distribution network in North America to accelerate product rollouts and aftermarket support. Panasonic Welding Systems Co., Ltd. integrates robotic welding heads with factory automation platforms, targeting high-precision automotive and electronics applications.
The Harris Products Group supplies gas and torch accessories that complement major OEMs, while Thermadyne Holdings Corporation’s incorporation into ESAB enhances synergies in consumables and customer support. Together, these companies exemplify a competitive landscape driven by R&D investment, strategic partnerships, and a relentless focus on customer-centric solutions.
This comprehensive research report delivers an in-depth overview of the principal market players in the Welding Gear market, evaluating their market share, strategic initiatives, and competitive positioning to illuminate the factors shaping the competitive landscape.
- ABICOR BINZEL USA
- Air Liquide S.A.
- Daihen Corporation
- ESAB
- Fronius International GmbH
- Hobart Welding Products
- Hypertherm, Inc.
- Kemppi Oy
- KOBE Steel, Ltd. (KOBELCO)
- Lincoln Electric Holdings, Inc.
- Miller Electric Mfg. LLC
- Panasonic Welding Systems Co., Ltd.
- The Harris Products Group
- Thermadyne Holdings Corporation (now part of ESAB)
Actionable Recommendations for Welding Gear Industry Leaders
To capitalize on evolving market dynamics, industry leaders should pursue a multipronged strategic agenda. First, invest boldly in automation and digital welding platforms that integrate real-time monitoring, predictive maintenance, and remote support. This capability will enhance throughput, improve quality yields, and differentiate offerings in an increasingly connected factory environment.
Second, diversify supply chains to mitigate tariff risks and geopolitical volatility. Establish regional assembly hubs, partner with local contract manufacturers, and qualify multiple suppliers for critical components to ensure continuity under shifting trade regimes.
Third, collaborate with standards bodies and material scientists to accelerate adoption of solid-state welding techniques. Participating in joint research efforts will help drive acceptance of low-heat processes across industries that demand minimal distortion and superior joint strength.
Fourth, expand aftermarket services and training programs to foster customer loyalty and generate recurring revenue streams. By offering advanced operator certification, virtual welding simulators, and on-site technical support, suppliers can create a comprehensive value proposition beyond the initial equipment sale.
Finally, embed sustainability into product design and operations through energy-efficient power sources, recyclable consumables, and emissions-reducing gas mixtures. Demonstrating a credible environmental footprint will resonate with end users and regulators alike, unlocking opportunities in infrastructure, automotive, and aerospace projects with stringent ESG requirements.
Explore AI-driven insights for the Welding Gear market with ResearchAI on our online platform, providing deeper, data-backed market analysis.
Ask ResearchAI anything
World's First Innovative Al for Market Research
Concluding Perspectives on Market Evolution
The welding gear market stands at the crossroads of technological innovation, regulatory evolution, and global trade realignments. Automation and digitalization are redefining productivity, while tariffs underscore the imperative of supply-chain resilience. Segmentation insights reveal opportunities in solid-state welding, robotic systems, and specialized alloys, and regional analysis highlights diverse growth drivers in the Americas, EMEA, and Asia-Pacific.
Leading suppliers are responding with targeted R&D, strategic partnerships, and expanded service offerings, shaping a competitive arena that prizes agility and customer intimacy. As the industry moves forward, companies that embrace integrated, sustainable solutions-backed by robust regional footprints and data-driven support services-will set the benchmark for success.
This section provides a structured overview of the report, outlining key chapters and topics covered for easy reference in our Welding Gear market comprehensive research report.
- Preface
- Research Methodology
- Executive Summary
- Market Overview
- Market Dynamics
- Market Insights
- Cumulative Impact of United States Tariffs 2025
- Welding Gear Market, by Product Type
- Welding Gear Market, by Technology
- Welding Gear Market, by Material Type
- Welding Gear Market, by End-User Industry
- Welding Gear Market, by Process
- Welding Gear Market, by Application
- Welding Gear Market, by User Type
- Americas Welding Gear Market
- Asia-Pacific Welding Gear Market
- Europe, Middle East & Africa Welding Gear Market
- Competitive Landscape
- ResearchAI
- ResearchStatistics
- ResearchContacts
- ResearchArticles
- Appendix
- List of Figures [Total: 30]
- List of Tables [Total: 422 ]
Contact Ketan Rohom to Access the Full Market Research Report
For executives seeking a deeper dive into the full scope of market dynamics, segmentation breakdowns, regional forecasts, and competitor profiles, reach out to Ketan Rohom, Associate Director of Sales & Marketing. Engage today to secure your copy of the comprehensive welding gear market research report and empower strategic decision-making.
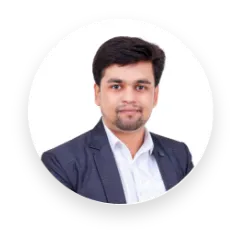
- When do I get the report?
- In what format does this report get delivered to me?
- How long has 360iResearch been around?
- What if I have a question about your reports?
- Can I share this report with my team?
- Can I use your research in my presentation?