The Welding Materials Market size was estimated at USD 16.85 billion in 2024 and expected to reach USD 18.01 billion in 2025, at a CAGR 6.62% to reach USD 24.75 billion by 2030.

Igniting the Future: An Introduction to Welding Materials Market Dynamics
The welding materials market stands at a pivotal juncture, shaped by converging technological advancements, shifting regulatory environments, and evolving customer demands. As industries from automotive to energy intensify their focus on precision, efficiency, and sustainability, the need for advanced welding consumables and processes has never been greater. Leading manufacturers and end users alike are seeking not only reliable materials but also innovative solutions that can deliver cost savings, quality improvements, and reduced environmental footprints.
Against this backdrop, stakeholders across the supply chain are navigating complex challenges. Raw material price volatility and fluctuating energy costs are exerting pressure on profit margins, while stringent emission standards and safety protocols demand continuous adaptation. Meanwhile, the rapid integration of automation and digital monitoring systems is redefining operational excellence, compelling traditional suppliers to reassess their value propositions.
This executive summary distills the most critical dynamics influencing the welding materials landscape. By examining transformative industry trends, regulatory impacts, market segment performance, regional variations, and key strategic imperatives, it offers a cohesive overview designed to inform decision-makers. Whether you are a C-suite executive, procurement specialist, or technical manager, this analysis will equip you with the clarity and foresight needed to capitalize on emerging opportunities and mitigate potential risks.
Revolutionary Shifts Reshaping Welding Materials Landscape
The welding materials sector is undergoing a profound metamorphosis driven by four major forces. First, the integration of digital tools such as real-time process monitoring and predictive maintenance software is elevating quality control and reducing downtime. These solutions, once considered discretionary, have become table stakes for companies aiming to maintain a competitive advantage.
Second, automation has shifted from isolated robotic cells to fully integrated production lines. Manufacturers are increasingly deploying collaborative robots and advanced welding power sources capable of adaptive feedback. This transition is not only boosting throughput but also fostering consistency in weld quality-a critical factor in high-stakes industries like aerospace and oil & gas.
Sustainability imperatives constitute the third major force reshaping the landscape. End users are demanding low-fume consumables, recyclable packaging, and processes that minimize greenhouse gas emissions. Suppliers that proactively reformulate fluxes and wires to reduce environmental impact are gaining momentum among eco-conscious buyers.
Lastly, evolving supply chain dynamics, including the rise of nearshoring and strategic stockpiling, are altering procurement patterns. Companies are seeking diversified sourcing strategies to mitigate tariff risks and geopolitical uncertainties. In combination, these transformative shifts are catalyzing a new era of efficiency, resilience, and innovation in welding materials.
Assessing the Ripple Effects of U.S. Tariffs on Welding Materials
The introduction of new U.S. tariffs in 2025 has reverberated across the welding materials ecosystem. With import duties imposed on select consumables and precursor alloys, manufacturers face heightened cost pressures that ripple through their pricing structures. These measures have prompted some end users to accelerate efforts to localize supply, while others explore alternatives such as in-house recycling of electrode stubs and scrap reclamation.
Importers have responded by renegotiating contracts and seeking tariff-exempt substitutes, yet these adjustments often entail trade-offs in performance or availability. Meanwhile, domestic producers are scaling up capacity to capture market share, but must navigate raw material procurement challenges and the capital intensity of expansion. The tariff environment has also spurred fresh investment in R&D, as firms look to develop proprietary flux and wire formulations that qualify for preferential duty treatment under specific trade agreements.
Globally, the U.S. policy shift has triggered realignments in trade flows. Regional partners are seizing opportunities to fill gaps in supply, while long-standing exporters are diversifying their markets to offset reduced U.S. volumes. Consequently, the welding materials market is witnessing a complex dance of pricing, sourcing, and strategic repositioning-all driven by the cumulative impact of the 2025 tariff framework.
Unveiling Market Dynamics Through Four Key Segmentation Lenses
A nuanced understanding of market segmentation reveals critical differentiators in demand patterns and value creation. In terms of material type, performance requirements dictate whether flux cored wire, solid wire, welding electrodes, welding flux, or welding gases deliver the optimal balance of deposition rates, metallurgical properties, and cost efficiency. Within the gases category, active and inert gases are selected based on joint configuration and base material specifications.
Turning to welding technology, the selection between gas metal arc welding, gas tungsten arc welding, laser beam welding, plasma arc welding, resistance welding, shielded metal arc welding, and submerged arc welding hinges on factors such as precision requirements, automation compatibility, and heat input control. Each process commands a distinct consumables profile and supports different production scales.
End users across aerospace, automotive, construction, energy and power, general fabrication, heavy machinery, oil and gas, and shipbuilding and marine exercise unique weld design and certification standards, influencing both material selection and supplier partnerships. These industry-driven demands shape product development cycles and inform strategic alliances.
Finally, operation mode segmentation-spanning fully automatic welding, manual welding, robotic welding, and semi-automatic welding-further underscores the interplay between labor skill levels, capital investment thresholds, and throughput targets. Together, these segmentation dimensions furnish a comprehensive framework for understanding competitive positioning and growth opportunities.
This comprehensive research report categorizes the Welding Materials market into clearly defined segments, providing a detailed analysis of emerging trends and precise revenue forecasts to support strategic decision-making.
- Material Type
- Welding Technology
- End-Use Industry
- Operation Mode
Regional Drivers Shaping Welding Materials Demand
Regional analysis illuminates how geographic factors, regulatory frameworks, and economic conditions drive divergent growth trajectories. In the Americas, infrastructure investment programs and reshoring initiatives have elevated demand for both consumables and associated equipment upgrades. Incentives for domestic production, combined with robust aftermarket services, are strengthening the region’s weld consumable supply chain.
Meanwhile, Europe, Middle East and Africa are characterized by a dual focus on energy transition and heavy industry modernization. Renewable energy projects and stringent environmental mandates are leading to increased adoption of low-emission electrodes and advanced wire formulations. At the same time, legacy sectors such as shipbuilding and petrochemicals continue to rely on tried-and-tested consumables, creating a dynamic balance in product portfolios.
In Asia-Pacific, rapid industrialization across manufacturing hubs is fueling expansion in automotive, electronics, and infrastructure projects. Cost-sensitive markets are exhibiting a strong appetite for high-efficiency processes and value-engineered consumables. Government initiatives promoting smart factories and export-oriented production are further accelerating the integration of automated welding technologies and specialized gases.
This comprehensive research report examines key regions that drive the evolution of the Welding Materials market, offering deep insights into regional trends, growth factors, and industry developments that are influencing market performance.
- Americas
- Europe, Middle East & Africa
- Asia-Pacific
Spotlight on Leading Innovators in Welding Materials
Leading companies within the welding materials space are distinguishing themselves through a blend of technological innovation, integrated solutions, and strategic partnerships. Some are investing heavily in next-generation flux chemistries to enhance deposition efficiency and weld integrity under extreme conditions. Others are deploying digital platforms that enable end users to monitor wire feed rates, arc stability, and gas consumption in real time, thereby unlocking new service revenue streams.
Collaborations with equipment manufacturers have also become a hallmark of top-tier players, ensuring seamless interoperability between power sources, torches, and consumables. Joint ventures in high-growth regions are facilitating capacity expansions and localized product development, tailored to regional standards and price sensitivities. Furthermore, targeted acquisitions of specialty alloy producers and gas blending facilities are enabling select firms to broaden their portfolios and capture cross-selling synergies.
Through these strategic moves, industry frontrunners are not only reinforcing their market positions but also accelerating the transition toward fully integrated welding ecosystems that deliver performance, sustainability, and cost advantages.
This comprehensive research report delivers an in-depth overview of the principal market players in the Welding Materials market, evaluating their market share, strategic initiatives, and competitive positioning to illuminate the factors shaping the competitive landscape.
- Lincoln Electric Holdings, Inc.
- Illinois Tool Works Inc.
- voestalpine AG
- Kobe Steel, Ltd.
- Panasonic Holdings Corporation
- Sandvik AB
- Linde plc
- Air Liquide S.A.
- Air Products and Chemicals, Inc.
- OC Oerlikon Corporation AG
Strategic Imperatives for Welding Materials Executives
Industry leaders should prioritize a multifaceted strategy to thrive in the evolving welding materials market. First, fostering close collaboration between R&D and customer-facing teams will ensure that new consumables address real-world process challenges and regulatory requirements. Embracing agile development cycles and pilot trials can accelerate time to market and bolster product-market fit.
Second, organizations must expand their digital footprint by integrating cloud-based analytics and remote support capabilities. This shift not only enhances customer engagement through predictive maintenance alerts and performance benchmarking but also generates valuable usage data to inform future product enhancements. Strategic partnerships with software providers and automation specialists can expedite this transformation.
Third, a targeted approach to sustainability-such as adopting green flux formulations and optimizing packaging waste-will resonate with end users under increasing environmental scrutiny. Aligning product roadmaps with global emission reduction targets can open doors to new market segments and government incentives.
Lastly, companies should adopt a flexible supply chain strategy, leveraging a mix of regional manufacturing hubs and strategic inventory buffers to mitigate tariff risks and raw material volatility. By balancing cost efficiency with resilience, organizations can secure reliable supply while preserving profitability in an unpredictable trade environment.
Robust Framework Underpinning the Market Analysis
Our analysis is based on a rigorous, multi-tiered research methodology combining both primary and secondary sources. In-depth interviews with industry executives, procurement managers, and technical specialists provided firsthand insights into current challenges and future expectations. These qualitative findings were triangulated with data from regulatory filings, trade associations, and proprietary industry databases to ensure comprehensive coverage and accuracy.
Market segmentation frameworks were developed through iterative consultation with subject matter experts, enabling precise categorization of material types, welding technologies, end-use industries, and operation modes. Regional dynamics were assessed by analyzing macroeconomic indicators, infrastructure spending plans, and environmental regulations across the Americas, Europe, Middle East and Africa, and Asia-Pacific.
A robust validation process, including cross-referencing against shipment data and financial disclosures, underpinned our conclusions. All data points were subjected to stringent quality checks, ensuring both reliability and relevance for strategic decision-making.
Explore AI-driven insights for the Welding Materials market with ResearchAI on our online platform, providing deeper, data-backed market analysis.
Ask ResearchAI anything
World's First Innovative Al for Market Research
Concluding Perspectives on Welding Materials Market Trajectory
The welding materials market is poised for continued evolution, driven by a convergence of technological innovation, sustainability mandates, and shifting global trade policies. As stakeholders navigate the complexities of automation, tariff impacts, and regional nuances, those equipped with an integrated understanding of segmentation and strategic imperatives will be best positioned to capture growth.
By aligning product development with end-user needs, expanding digital capabilities, and maintaining agile supply chain strategies, organizations can not only mitigate risks but also unlock new value pools. The interplay between advanced consumables, process optimization, and environmental stewardship will define competitive advantage in the years ahead.
Ultimately, the companies that proactively adapt to these dynamics-leveraging data-driven insights and fostering collaborative ecosystems-will shape the next frontier of welding materials performance and profitability.
This section provides a structured overview of the report, outlining key chapters and topics covered for easy reference in our Welding Materials market comprehensive research report.
- Preface
- Research Methodology
- Executive Summary
- Market Overview
- Market Dynamics
- Market Insights
- Cumulative Impact of United States Tariffs 2025
- Welding Materials Market, by Material Type
- Welding Materials Market, by Welding Technology
- Welding Materials Market, by End-Use Industry
- Welding Materials Market, by Operation Mode
- Americas Welding Materials Market
- Europe, Middle East & Africa Welding Materials Market
- Asia-Pacific Welding Materials Market
- Competitive Landscape
- ResearchAI
- ResearchStatistics
- ResearchContacts
- ResearchArticles
- Appendix
- List of Figures [Total: 24]
- List of Tables [Total: 247 ]
Unlock Exclusive Market Intelligence with Our Expert Liaison
For more detailed insights and to secure your comprehensive market research report, reach out directly to Ketan Rohom, Associate Director of Sales & Marketing at 360iResearch. Engage with an expert who can guide you through tailored data solutions and empower your strategic initiatives with the most authoritative welding materials market intelligence available.
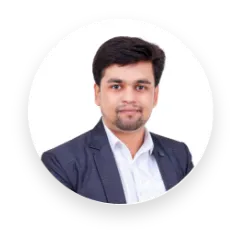
- How big is the Welding Materials Market?
- What is the Welding Materials Market growth?
- When do I get the report?
- In what format does this report get delivered to me?
- How long has 360iResearch been around?
- What if I have a question about your reports?
- Can I share this report with my team?
- Can I use your research in my presentation?