Uncovering the Role of Advanced Wheeled Inspection Robots in Revolutionizing Safety and Efficiency Across Intelligent Underground Coal Mining Operations
Underground coal mining operations have entered a new era defined by the pursuit of higher safety standards, increased operational efficiency, and continuous regulatory compliance. Traditional inspection methods often expose personnel to hazardous environments characterized by toxic gases, structural instability, and extreme conditions. In response to these challenges, wheeled underground inspection robots have emerged as indispensable tools for modern mining enterprises. By automating critical inspection tasks, these robotic platforms can navigate complex subterranean networks, conduct real-time data collection, and relay actionable insights to remote operators.
The convergence of advanced mobility architectures, robust sensor arrays, and artificial intelligence has enabled these wheeled robots to perform a diverse array of inspection functions-from comprehensive gas monitoring to detailed structural integrity assessments. In doing so, they not only mitigate risk to human operators but also optimize maintenance cycles and support predictive safety protocols. As coal mines transition toward intelligent operations, the adoption of such robotic solutions is accelerating, laying the groundwork for smarter, safer, and more productive subterranean workflows.
Exploring the Convergence of Digital Connectivity Autonomous Mobility and Sensor Intelligence Redefining Underground Inspection in Modern Coal Mines
The landscape of underground inspection has undergone several transformative shifts anchored in digital connectivity, autonomous mobility, and sensor intelligence. Advances in communications infrastructure-ranging from low-latency wireless mesh networks to fiber-optic backbone extensions-have made it possible for robots to operate with near-instantaneous remote oversight. This connectivity has enabled seamless integration with surface-level control centers, where data streams from multiple robotic units can be aggregated, analyzed, and visualized in real time.
Simultaneously, breakthroughs in autonomous navigation algorithms and compact drive systems have endowed wheeled inspection platforms with the capacity to traverse uneven and debris-laden mine passages without continuous human input. Coupled with sophisticated vision systems, these robots can detect roadway obstructions, map newly excavated chambers, and autonomously adjust their routes to maintain mission continuity.
Equally important is the rise of multi-modal sensor intelligence. Modern wheeled robots combine gas detection modules, laser-based structural scanners, thermal imaging cameras, and vibration sensors into unified payloads. This fusion of technologies produces comprehensive situational awareness, enabling early detection of gas leaks, thermal hotspots, structural anomalies, and equipment wear patterns. Consequently, mining operators can intervene proactively to prevent incidents and limit downtime.
Assessing the Cascading Effects of 2025 United States Tariffs on Supply Chains Technology Sourcing and Cost Structures within Underground Inspection Robotics
In 2025, the imposition of new United States tariffs on select imported robotics components has introduced significant cost and sourcing complexities for manufacturers and end users. High-precision sensors, drive motors, and specialized electronics-often produced overseas-have been subject to increased duties, leading to higher landed costs for complete robotic assemblies. This has compelled suppliers to reassess their supply chain strategies and explore opportunities for nearshoring or domestic production partnerships.
The cumulative effects of these tariff measures extend beyond mere price increases. Procurement teams are adapting by standardizing component specifications to facilitate bulk purchasing, negotiating longer-term contracts to hedge against further policy volatility, and collaborating with alternative suppliers in more tariff-favorable jurisdictions. Meanwhile, research and development cycles are shifting to emphasize modularity and component interchangeability, so that future design iterations can more readily accommodate emerging trade regulations.
From an end-user perspective, mining operators face a delicate balance between preserving their total cost of ownership targets and accessing the latest robotic capabilities. As robot unit costs adjust upward, many companies are evaluating phased deployments, leasing arrangements, and service-based contracts to spread financial impact over time. This collective response underscores the interconnected nature of trade policy, manufacturing innovation, and adoption strategies in the underground inspection robotics arena.
Deciphering Market Dynamics through Inspection Type Application Scenario Automation Level and Power Source Segmentation of Underground Inspection Robotics
A clear understanding of market segmentation reveals how inspection type, application scenario, automation level, and power source shape strategic priorities and innovation pathways. Inspection type segmentation highlights demand for gas monitoring solutions that encompass carbon monoxide detection, hydrogen sulfide detection, and methane detection to address critical safety risks. Structural inspection remains pivotal for evaluating roof stability and detecting fissures, while thermal imaging systems-ranging from longwave infrared to mediumwave infrared and shortwave infrared-enable early identification of heat anomalies in equipment and tunnel linings. Vibration analysis platforms complement these functions by tracking mechanical health and predicting component failures.
Application scenario analysis further nuances this picture by differentiating environmental monitoring, maintenance support, production monitoring, and safety inspection use cases. Environmental monitoring systems continuously log atmospheric conditions to verify compliance, whereas maintenance support deployments guide targeted interventions to minimize downtime. Production monitoring robots aggregate performance data to optimize throughput, and safety inspection units focus on gas leak prevention, roof stability assessment, and worker safety enhancements.
Automation level distinctions identify diverging adoption curves for fully automated, semi automated, and manual configurations. Fully automated platforms excel in repetitive, high-frequency inspection tasks, while semi automated solutions combine remote operator control with intelligent autonomy to handle complex scenarios. Manual robots remain essential for specialized inspections that require direct human oversight in challenging environments.
Power source segmentation differentiates battery powered, diesel powered, and hybrid robots, each offering unique trade-offs between operational range, emission profiles, and refueling or recharging cycles. Battery powered units are prized for emission-free operation and minimal maintenance, diesel powered robots deliver longer run times in remote sectors, and hybrid configurations strive to blend the advantages of both in dynamic mission profiles.
This comprehensive research report categorizes the Wheeled Underground Inspection Robot For Intelligent Coal Mines market into clearly defined segments, providing a detailed analysis of emerging trends and precise revenue forecasts to support strategic decision-making.
- Inspection Type
- Application Scenario
- Automation Level
- Power Source
Mapping Regional Variations in Adoption Cost Constraints and Technological Preferences for Wheeled Inspection Robots across Americas EMEA and Asia Pacific
Regional analysis underscores distinct adoption patterns and investment drivers across the Americas, Europe Middle East and Africa, and Asia Pacific. In the Americas, stringent safety regulations combined with mature underground infrastructures have fostered early and widespread deployment of advanced wheeled inspection robots. Facilities emphasize gas detection and structural monitoring to comply with federal and state standards, while leveraging automation to sustain productivity amid labor constraints.
Conversely, Europe Middle East and Africa exhibit a varied landscape shaped by divergent regulatory regimes and resource profiles. Western European coal operations have shifted toward stringent environmental oversight, prioritizing thermal imaging and vibration analysis to meet emission and safety thresholds. In parts of the Middle East and North Africa, emerging mining projects are integrating robotics from project inception to circumvent workforce challenges and establish modern safety protocols. South Africa’s established mining sector, in turn, is calibrating its fleet mix to balance legacy diesel powered platforms with new battery powered designs.
Asia Pacific represents the fastest-growing demand center, driven by high coal production volumes in China and India and by cost-sensitive market dynamics. Local manufacturers are co-developing entry-level wheeled robots optimized for production monitoring and environmental oversight at scale. As regional supply chains mature, mid-tier operators are exploring hybrid power solutions to reconcile peripheral site energy constraints with the need for autonomous, round-the-clock inspections.
This comprehensive research report examines key regions that drive the evolution of the Wheeled Underground Inspection Robot For Intelligent Coal Mines market, offering deep insights into regional trends, growth factors, and industry developments that are influencing market performance.
- Americas
- Europe, Middle East & Africa
- Asia-Pacific
Illuminating Strategic Movements Collaborations and Portfolio Expansions of Leading Manufacturers in the Wheeled Underground Inspection Robotics Sector
Several leading companies are shaping the competitive dynamics of the wheeled underground inspection robotics market through targeted investments, strategic alliances, and technology portfolio expansion. Established mining equipment manufacturers are integrating robotics expertise into their legacy product lines, leveraging deep customer relationships to bundle inspection services with traditional vehicle offerings. At the same time, specialized robotics firms are forging partnerships with sensor providers and software developers, enabling seamless data capture and analytics modules that enhance remote monitoring capabilities.
A notable trend involves the acquisition of niche technology startups by larger conglomerates seeking to accelerate time-to-market for autonomous solutions. These consolidation moves not only broaden product catalogs but also pool R&D resources to pursue next-generation sensor fusion and artificial intelligence features. Additionally, cross-industry collaborations-such as teaming with telecommunications providers to embed low-latency networks within mine tunnels-are increasingly common.
Emerging competitors are also making inroads by focusing on modular architectures that reduce total lifecycle costs and simplify field upgrades. By offering interchangeable payload bays, open software platforms, and subscription-based analytics services, these agile entrants are putting pressure on incumbents to match flexibility and address evolving end-user requirements in real time.
This comprehensive research report delivers an in-depth overview of the principal market players in the Wheeled Underground Inspection Robot For Intelligent Coal Mines market, evaluating their market share, strategic initiatives, and competitive positioning to illuminate the factors shaping the competitive landscape.
- Shanghai Tongdong Intelligent Closed Mine Robot Co., Ltd.
- CITIC Heavy Industries Co., Ltd.
- Komatsu Ltd.
- Caterpillar Inc.
- Epiroc AB
- Sandvik AB
- Atlas Copco AB
- ABB Ltd.
- Hexagon AB
- Honeywell International Inc.
Strategic Roadmap for Industry Leaders Emphasizing Collaboration Innovation and Operational Excellence in Deploying Underground Inspection Robot Technologies
Industry leaders should pursue a multi-faceted approach to capitalize on the evolving underground inspection robotics landscape. Strengthening supply chain resilience through diversified sourcing and strategic nearshoring can mitigate tariff-related disruptions, while co-investment models with component suppliers help secure preferential pricing and guaranteed production capacity. Concurrently, a focus on sensor fusion-integrating gas detection, thermal imaging, and vibration analysis into unified platforms-will differentiate offerings in a competitive marketplace.
To drive adoption, providers must enhance user experiences by embedding intuitive remote-control interfaces and delivering turnkey deployment services. This includes on-site training modules, virtual simulation labs for operator certification, and comprehensive maintenance support programs that lower barriers to entry for prospective buyers. Building robust partnerships with mine operators to conduct pilot programs and share operational data will further accelerate technology validation and foster deep customer engagement.
Finally, aligning product roadmaps with industry digitalization trends-such as edge computing, cloud-based analytics, and real-time performance dashboards-can unlock new subscription-based revenue streams. By leveraging actionable insights from continuous inspection cycles, mining companies can optimize safety, reduce unplanned downtime, and achieve measurable improvements in operational efficiency.
Comprehensive Framework Detailing Data Collection Sources Analytical Techniques and Validation Processes Underpinning the Underground Inspection Robotics Study
This study is underpinned by a rigorous research framework combining primary data collection, secondary analysis, and robust validation processes. Primary research involved in-depth interviews with senior decision-makers at coal mining operators, robotics manufacturers, sensor technology providers, and system integrators. These qualitative discussions yielded rich insights into real-world deployment challenges, purchasing criteria, and future innovation priorities.
Secondary research encompassed a thorough review of technical papers, industry standards, regulatory documents, and published case studies relevant to underground inspection robotics. This desk-based analysis provided context on historical adoption trends, performance benchmarks, and safety requirements. To ensure data accuracy, information from public sources was cross-referenced with proprietary databases and anonymized survey responses from experienced field technicians.
Analytical techniques included segmentation mapping, comparative scenario analysis, and triangulation of quantitative and qualitative inputs. Expert validation workshops brought together a panel of mining engineers, robotics specialists, and safety consultants to verify findings and refine strategic recommendations. Throughout the process, methodological rigor was maintained through iterative quality checks, consistency reviews, and alignment with recognized market research best practices.
Explore AI-driven insights for the Wheeled Underground Inspection Robot For Intelligent Coal Mines market with ResearchAI on our online platform, providing deeper, data-backed market analysis.
Ask ResearchAI anything
World's First Innovative Al for Market Research
Synthesizing Insights to Highlight the Strategic Imperatives Unlocking Growth Potential and Safety Advancements in Underground Inspection Robotics
The integration of wheeled underground inspection robots represents a pivotal advancement for coal mining operations seeking to enhance safety, efficiency, and regulatory compliance. As sensor capabilities expand and autonomous functions mature, these robots will play an increasingly central role in detecting hazards, streamlining maintenance, and supporting data-driven decision-making on the mine floor.
Despite headwinds from trade policy changes and regional cost pressures, the market is poised for continued transformation through supply chain optimization, modular design innovation, and targeted partnerships. Regional variations in adoption patterns highlight the need for customizable solutions that align with local regulations, infrastructure maturity, and energy availability.
By synthesizing segmentation insights, regional dynamics, and competitive developments, this report provides stakeholders with a clear roadmap to navigate evolving challenges and capitalize on emerging opportunities. The strategic imperatives outlined herein will enable industry leaders to deliver safer working environments, unlock operational efficiencies, and secure a technological edge in tomorrow’s intelligent coal mines.
This section provides a structured overview of the report, outlining key chapters and topics covered for easy reference in our Wheeled Underground Inspection Robot For Intelligent Coal Mines market comprehensive research report.
- Preface
- Research Methodology
- Executive Summary
- Market Overview
- Market Dynamics
- Market Insights
- Cumulative Impact of United States Tariffs 2025
- Wheeled Underground Inspection Robot For Intelligent Coal Mines Market, by Inspection Type
- Wheeled Underground Inspection Robot For Intelligent Coal Mines Market, by Application Scenario
- Wheeled Underground Inspection Robot For Intelligent Coal Mines Market, by Automation Level
- Wheeled Underground Inspection Robot For Intelligent Coal Mines Market, by Power Source
- Americas Wheeled Underground Inspection Robot For Intelligent Coal Mines Market
- Europe, Middle East & Africa Wheeled Underground Inspection Robot For Intelligent Coal Mines Market
- Asia-Pacific Wheeled Underground Inspection Robot For Intelligent Coal Mines Market
- Competitive Landscape
- ResearchAI
- ResearchStatistics
- ResearchContacts
- ResearchArticles
- Appendix
- List of Figures [Total: 26]
- List of Tables [Total: 652 ]
Engage with Ketan Rohom to Secure Your In-depth Report on Wheeled Underground Inspection Robots and Drive Strategic Advantage
To unlock the full strategic value of this analysis and gain a competitive edge in the rapidly evolving underground inspection robotics market, reach out today. Engage directly with Ketan Rohom, Associate Director of Sales & Marketing, to secure comprehensive insights and detailed findings that will empower informed decision-making. Discover how this report can guide your roadmap to enhanced safety, operational efficiency, and technological leadership in intelligent coal mining environments.
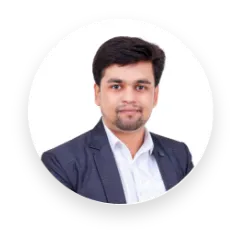
- When do I get the report?
- In what format does this report get delivered to me?
- How long has 360iResearch been around?
- What if I have a question about your reports?
- Can I share this report with my team?
- Can I use your research in my presentation?