The Wind Turbine Composite Materials Market size was estimated at USD 15.39 billion in 2024 and expected to reach USD 17.03 billion in 2025, at a CAGR 10.47% to reach USD 27.97 billion by 2030.
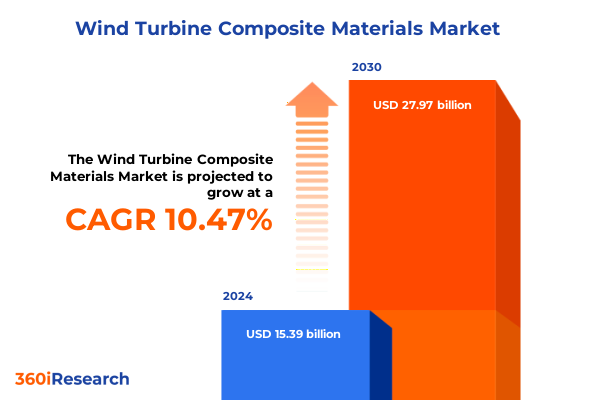
Introduction to Wind Turbine Composite Materials
In the rapidly evolving energy landscape, wind turbine composite materials have emerged as a critical element in the quest for more efficient, reliable, and sustainable energy solutions. This report delves into the sophisticated world of composite materials that are at the heart of modern wind turbine design and construction. Composite materials, a blend of various fibers and resins, enable the creation of lighter, stronger, and more durable components that withstand the harsh conditions characteristic of wind energy environments.
The importance of these materials is underscored by the dynamic interplay of material science, engineering innovation, and sustainability imperatives. Advancements in these materials not only drive improvements in turbine performance and longevity but also significantly reduce maintenance costs and installation downtime. Such improvements are essential for meeting the aggressive targets of renewable energy production while ensuring cost efficiency and operational excellence.
Marked by continuous research and development, the field of wind turbine composites is transitioning from traditional design methodologies to embrace state-of-the-art manufacturing techniques and performance-enhancing innovations. The market's evolution reflects the deep commitment of industry players and researchers, emphasizing the integration of smarter materials, longer life cycles, and adaptable components across wind turbine substructures such as blades, nacelles, and towers.
Throughout this comprehensive analysis, readers will gain insights into the emerging trends, market drivers, and technological breakthroughs that are paving the way for next-generation wind turbines. The intricate balance of durability, strength, and weight reduction, combined with technology-led innovations, is redefining industry standards and setting new benchmarks for performance, reliability, and sustainability in wind energy projects.
Transformative Shifts in the Industry Landscape
The landscape of wind turbine composite materials has undergone a dramatic transformation over recent years, driven by innovations, regulatory changes, and evolving market demands. Not long ago, traditional construction techniques and conventional materials were the norm, but the advent of advanced composite technologies has rewritten the narrative for design, manufacturing, and performance. This shift is not merely an incremental change; it represents a profound transformation that is reshaping every facet of the wind energy industry.
Key developments in material science have allowed manufacturers to move away from manually intensive processes and adopt sophisticated automated techniques. These transformative changes have seen an increased adoption of robotics, precision manufacturing, and process optimization. The incorporation of advanced composite materials and smart manufacturing processes such as filament winding, hand lay-up methods, and resin transfer molding has enabled manufacturers to enhance component performance while achieving higher production efficiency.
Significant regulatory pressures and environmental mandates have accelerated the need for sustainability and recycling in manufacturing practices. This has fostered innovation in the use of bio-composite and recyclable materials, ensuring that wind turbine components not only perform at optimal levels but also contribute to environmental preservation. Moreover, the rapid adoption of digitalization and sensor-embedded systems has led to the development of smart blade technology, allowing for real-time monitoring and predictive maintenance. Such systems provide valuable operational data that enable continuous improvement and proactive interventions.
The seismic shifts in manufacturing practices have also led to improved safety standards, reduced waste, and an overall decrease in the carbon footprint associated with wind turbine production. Manufacturers are now equipped with a better understanding of the balance between performance attributes and production efficiency, achieving a synthesis that was previously thought unattainable. The newfound alignment between economic efficiency and ecological responsibility marks a pivotal moment in the literature of renewable energy manufacturing.
These transformative shifts have not only elevated performance metrics but have also expanded the global reach of wind energy solutions. With technological advancements bridging geographical gaps, technological innovation is now available to both established markets and emerging economies alike. This democratization of technology represents a significant opportunity, unlocking new markets and fostering international collaborations that were previously unimaginable.
Key Segmentation Insights in Composite Materials
The market segmentation of wind turbine composite materials is both intricate and fundamental to understanding industry dynamics. Analyzing segmentation based on material type, resin type, application, manufacturing process, end-user industry, performance attributes, supplier type, and advancement in technology offers an in-depth view of the market’s structure and pace of innovation. Each segmentation factor provides distinct insights that cumulatively chart the pathway of competitive advantage and operational excellence.
Starting with material types, the research provides a robust analysis that spans Aramid Fiber, Carbon Fiber, Glass Fiber, and Natural Fiber. Within Aramid Fiber, further distinctions are made between paper, pulp, and woven fabrics, reflecting the versatility inherent in this high-performance material. Carbon Fiber is broken down into continuous fiber, long fiber, and short fiber, each offering unique properties that cater to varying performance requirements. When considering Glass Fiber, components evaluated include fiberglass cloth, fiberglass mats, and fiberglass rovings—each serving specialized roles in enhancing strength and durability. Meanwhile, Natural Fiber explores renewable options such as flax, hemp, and jute, underscoring the significant push toward sustainability.
When segmented by resin type, the market divides into Thermoplastic and Thermoset, each with subcategories that reveal nuanced behaviors and application potentials. Thermoplastic resins such as polycarbonate, polyethylene terephthalate, and polypropylene lead to a dynamic range of applications characterized by recyclability and process flexibility. On the thermoset side, critical materials like epoxy, polyester, and vinyl ester ensure robust bonding and high resistance to environmental stresses, fundamental for long-term performance under variable wind loads.
Diving into application-based segmentation, each structural component such as blades, nacelles, and towers benefits from focused material innovations. Blade segments include both shell elements and structural blade elements, each engineered for maximum aerodynamic efficiency and structural integrity. Within nacelles, details such as gearbox housing and rotor hub are scrutinized to optimize energy conversion and reliability. Towers have been segmented into flanges and tower bases, emphasizing the critical nature of structural support and load-bearing capacity.
Manufacturing process segmentation reveals a detailed study of methods that include compression molding, filament winding, hand lay-up techniques, and resin transfer molding. Each method is further dissected into high and low volume variations, continuous versus discontinuous winding, prepreg and wet lay-up techniques, as well as pressure versus vacuum-assisted resin transfer molding. These process-specific insights are crucial in understanding the balance between scale of production and quality of output.
The segmentation based on the end-user industry highlights the distinction between offshore and onshore wind solutions. Offshore applications, which include fixed bottom and floating platforms, call for composite materials that can endure aggressive marine environments, while onshore applications cover small wind projects and utility scale endeavors that demand rapid deployment and cost-effectiveness.
An analysis that focuses on performance attributes scrutinizes essential factors such as durability properties, strength properties, and weight attributes. Durability is further refined through studies on moisture absorption and UV resistance. Strength properties explore both flexural and tensile strengths, and weight attributes are highlighted by density considerations and measures for weight reduction. These insights are key in determining the operational and lifecycle efficiency of wind turbine components.
Furthermore, segmentation by supplier type categorizes the market into component manufacturers and raw material suppliers. Component manufacturers are evaluated based on the production of blades and towers, while raw material suppliers are classified further into primary material suppliers and secondary material suppliers. This segmentation provides clarity on the supply chain dynamics as well as the strategic partnerships that drive innovation.
Finally, the segmentation based on technological advancements includes Advanced Composite Materials and Smart Blade Technology. Advanced composites are evaluated not only in terms of performance but also for their environmental impact, as exemplified by bio-composite and recyclable composite materials. Smart blade technology, on the other hand, focuses on developments in blade monitoring systems and embedded sensors, which are pivotal for predictive maintenance and operational efficiency. Each of these segmentation factors interlocks to form a comprehensive view of the market, offering a detailed understanding of both current trends and future potential.
This comprehensive research report categorizes the Wind Turbine Composite Materials market into clearly defined segments, providing a detailed analysis of emerging trends and precise revenue forecasts to support strategic decision-making.
- Material Type
- Resin Type
- Application
- Manufacturing Process
- End-User Industry
- Performance Attributes
- Supplier Type
- Advancement In Technology
Key Regional Insights Across Global Markets
Understanding regional dynamics is paramount when assessing the potential and challenges of wind turbine composite materials on a global scale. The analysis of key regions such as the Americas, Europe, Middle East & Africa, and Asia-Pacific reveals diverse motivations and growth patterns that influence market trajectories.
In the Americas, a blend of robust industrial infrastructure and progressive energy policies has stimulated significant investments in renewable energy technologies. The region exhibits a mature market characterized by strong partnership networks, rich innovation ecosystems, and a focus on enhancing energy efficiency. Increased funding for wind energy projects and evolving regulatory frameworks in this region are fostering rapid advancements in composite material technologies that cater to both established utility-scale projects and emerging small-scale ventures.
The Europe, Middle East & Africa region represents a complex yet immensely dynamic landscape. Europe, with its long-standing commitment to renewable energy and stringent environmental mandates, is a hotbed for research and innovation in composite materials. Simultaneously, the Middle East & Africa is beginning to emerge as a significant contributor to the global renewable sector, driven by a transformational desire to diversify energy sources and reduce carbon footprints. In this region, technological collaboration and policy reforms are accelerating the adoption of smart and advanced composite solutions that ensure high-performance under extreme environmental conditions.
Asia-Pacific is witnessing explosive growth fueled by rapid industrialization, urbanization, and a strong governmental focus on renewable energy projects. In this vibrant market, domestic manufacturing capabilities and technological innovations are converging to redefine wind turbine composite manufacturing. The Asia-Pacific region exhibits a unique confluence of local expertise and global manufacturing standards, creating an environment where efficiency, cost competitiveness, and innovation thrive. These regional insights collectively demonstrate a balanced mix of mature markets and high-growth opportunities that are critically shaping the future landscape of wind turbine composite materials.
This comprehensive research report examines key regions that drive the evolution of the Wind Turbine Composite Materials market, offering deep insights into regional trends, growth factors, and industry developments that are influencing market performance.
- Americas
- Asia-Pacific
- Europe, Middle East & Africa
Key Companies Leading the Market
In a sector characterized by quick technological evolution and strong competitive forces, key companies are shaping the supply chain and spearheading innovation in wind turbine composite materials. Several leading enterprises have made significant inroads in this space, demonstrating capabilities that range from pioneering advanced material formulations to setting benchmarks in manufacturing excellence. Notable players include AREVA S.A. and Arkema S.A., whose innovative approaches have significantly impacted material durability and performance. Industry associations like Composites United e.V. foster collaboration among stakeholders, contributing to a unified approach in addressing market challenges.
Major manufacturing giants such as Enercon GmbH and Exel Composites have taken bold steps by integrating cutting-edge technology into their production processes. Gurit Services AG and Hexcel Corporation consistently push the envelope of material science by improving performance attributes such as strength and weight reduction. Huntsman International LLC along with Kemrock Industries and Exports Limited have contributed to the evolution of both thermoplastic and thermoset resin applications. The global landscape is further enriched by the contributions of Lianyungang Zhongfu Lianzhong Composites Group Co., Ltd. and LM Wind Power by General Electric Company, both providing integral support to the wind energy ecosystem. Leading chemicals and composite innovators such as Mitsubishi Chemical Corporation and Solvay S.A. are also central to this narrative, partnering with companies like Molded Fiber Glass Companies and Nordex SE to foster sustainable development in blade manufacturing.
Industry leaders such as Owens Corning, Reliance Industries Ltd., and SGL Carbon SE have also played a pivotal role in steering research and development towards more environmentally sustainable practices. Siemens Gamesa Renewable Energy, S.A and SpecialChem S.A. are at the forefront of integrating smart technologies into material design, ensuring efficiency and resilience. Suzlon Energy Limited, Tejin Limited, and Toray Industries, Inc. have shown notable expertise in manufacturing processes, while Toray TCAC Holding B.V, TPI Composites, Inc. and Vestas Wind Systems A/S broaden the horizon of wind turbine innovation through strategic research investments and global supply chain integration. The strategic direction and market influence of these companies represent the collective strengths of an industry that is continuously adapting to high-performance and sustainability benchmarks.
This comprehensive research report delivers an in-depth overview of the principal market players in the Wind Turbine Composite Materials market, evaluating their market share, strategic initiatives, and competitive positioning to illuminate the factors shaping the competitive landscape.
- AREVA S.A.
- Arkema S.A.
- Composites United e.V.
- Enercon GmbH
- Exel Composites
- Gurit Services AG
- Hexcel Corporation
- Huntsman International LLC
- Kemrock Industries and Exports Limited
- Lianyungang Zhongfu Lianzhong Composites Group Co., Ltd.
- LM Wind Power by General Electric Company
- Mitsubishi Chemical Corporation
- Molded Fiber Glass Companies
- Nordex SE
- Owens Corning
- Reliance Industries Ltd.
- SGL Carbon SE
- Siemens Gamesa Renewable Energy, S.A
- Solvay S.A.
- SpecialChem S.A.
- Suzlon Energy Limited
- Tejin Limited
- Toray Industries, Inc.
- Toray TCAC Holding B.V
- TPI Composites, Inc.
- Vestas Wind Systems A/S
Actionable Recommendations for Industry Leaders
Industry leaders must adopt a multi-faceted strategy to remain competitive and harness the full potential of wind turbine composite materials. First, focus on accelerating research and development efforts to foster the integration of cutting-edge technologies such as embedded sensor systems and smart blade monitoring. These innovations provide valuable real-time data that not only enhance operational efficiency but also extend the lifespan of turbine components.
It is crucial for companies to invest in modernizing manufacturing processes by incorporating advanced techniques like automated filament winding, high precision resin transfer molding, and hybrid hand lay-up methods. Such investments will yield significant performance enhancements, reduce production costs, and improve quality control measures. Moreover, optimizing supply chain interactions by forging deeper collaborations with both primary and secondary raw material suppliers will ensure greater production flexibility, scalability, and innovation.
Sustainability must remain at the forefront of any strategic initiative. Leaders should prioritize the development of recyclable composite materials and bio-based resin formulations that align with strict environmental regulations and global sustainability targets. Aligning sustainability with economic performance not only meets regulatory demands but also enhances brand reputation and market appeal.
Diversification of applications is another strategic pathway. Companies should actively explore opportunities across both onshore and offshore wind energy projects, ensuring that the composite materials portfolio is well-positioned to serve a dual market. Emphasizing quality control and performance testing across critical segments such as blade components, nacelle systems, and tower structures will ensure that products are well-tailored to meet the rigorous demands of varying operational environments.
Industry leaders must also place a premium on training and talent development. Equipping teams with the latest insights in material science and manufacturing technology helps in driving continuous improvement and innovation in the production process. Constant technological upskilling, coupled with customer-centric service models, will foster stronger customer relationships and improve market responsiveness.
Lastly, strategic partnerships with academic institutions, research centers, and technology incubators can act as fertile grounds for innovation. Proactive collaborative research can unlock novel material formulations and influence the next-generation design of wind turbine components. These partnerships create a synergetic effect that accelerates time-to-market for innovative solutions and builds a resilient, forward-thinking industry landscape.
Explore AI-driven insights for the Wind Turbine Composite Materials market with ResearchAI on our online platform, providing deeper, data-backed market analysis.
Ask ResearchAI anything
World's First Innovative Al for Market Research
Conclusion: Shaping the Future of Wind Turbine Composites
The evolution of wind turbine composite materials stands as a testament to the relentless pursuit of innovation in response to the growing demand for sustainable energy solutions. Throughout the analysis, it becomes evident that progress in composite materials is not confined merely to technological advancements but embraces a holistic strategy involving material science refinement, manufacturing process updates, and strategic supply chain management. The ensuing developments have the potential to redefine the mechanics of wind energy generation by enhancing overall system durability, reducing operational costs, and paving the way for environmentally friendly designs.
From detailed market segmentation analysis that spans material types, resin formulations, applications, manufacturing processes, and performance attributes, it is clear that a comprehensive understanding of market dynamics is essential for sustaining competitive advantage. The fusion of technical expertise with strategic planning has equipped industry stakeholders with the knowledge necessary to drive future growth and innovation. The evolving global market, evidenced through insights drawn from regions including the Americas, Europe, Middle East & Africa, and Asia-Pacific, highlights a broad spectrum of opportunities and challenges that demand proactive and adaptive strategies.
Furthermore, the presence of influential industry players, each contributing their unique strengths, serves as a catalyst for further technological breakthroughs. These leading companies are not only expanding the boundaries of material performance but also solidifying the foundation of an industry geared towards long-term sustainability. In this context, driving research, fostering smart manufacturing, and emphasizing eco-friendly practices have become key imperatives for shaping the future of wind turbine composites.
In summary, the journey towards enhancing wind turbine composite materials is both challenging and promising. This evolving narrative is characterized by transformative shifts that signal not only improved performance metrics but also a seamless integration of sustainable practices with innovative manufacturing. The insights drawn from market segmentation, regional dynamics, and competitive analysis collectively chart a path forward for an industry poised for remarkable opportunities in the renewable energy sector.
This section provides a structured overview of the report, outlining key chapters and topics covered for easy reference in our Wind Turbine Composite Materials market comprehensive research report.
- Preface
- Research Methodology
- Executive Summary
- Market Overview
- Market Insights
- Cumulative Impact of United States Tariffs 2025
- Wind Turbine Composite Materials Market, by Material Type
- Wind Turbine Composite Materials Market, by Resin Type
- Wind Turbine Composite Materials Market, by Application
- Wind Turbine Composite Materials Market, by Manufacturing Process
- Wind Turbine Composite Materials Market, by End-User Industry
- Wind Turbine Composite Materials Market, by Performance Attributes
- Wind Turbine Composite Materials Market, by Supplier Type
- Wind Turbine Composite Materials Market, by Advancement In Technology
- Americas Wind Turbine Composite Materials Market
- Asia-Pacific Wind Turbine Composite Materials Market
- Europe, Middle East & Africa Wind Turbine Composite Materials Market
- Competitive Landscape
- ResearchAI
- ResearchStatistics
- ResearchContacts
- ResearchArticles
- Appendix
- List of Figures [Total: 32]
- List of Tables [Total: 1343 ]
Call-To-Action: Connect with Ketan Rohom for In-Depth Market Insights
For decision-makers seeking to gain a competitive edge through rigorous market analysis and actionable intelligence, further insights into wind turbine composite materials are now within reach. Connect directly with Ketan Rohom, Associate Director of Sales & Marketing, to explore the detailed findings and future projections contained within the comprehensive market research report. This is an opportunity to dive deeper into transformative industry trends, detailed segmentation insights, and strategic recommendations designed to empower industry leaders in making informed decisions. Do not hesitate to reach out and secure your copy of this essential research resource, designed specifically to help you navigate the quickly evolving landscape of wind turbine composite materials.
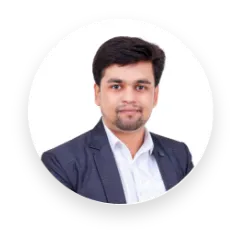
- How big is the Wind Turbine Composite Materials Market?
- What is the Wind Turbine Composite Materials Market growth?
- When do I get the report?
- In what format does this report get delivered to me?
- How long has 360iResearch been around?
- What if I have a question about your reports?
- Can I share this report with my team?
- Can I use your research in my presentation?