Introduction to the Agricultural Vehicle Wire Harness Market
Wire harnesses are the circulatory system of modern agricultural vehicles, providing structured pathways for power distribution, signal transmission and system integration across critical subsystems. From powering hydraulic actuators to linking sensors on precision planting equipment, harness assemblies ensure reliability under harsh conditions, including dust, moisture and severe vibration. As farms adopt greater automation and connectivity, the complexity and performance demands placed on wiring architectures continue to rise, driving innovation in materials, manufacturing and design protocols.
In response to operator expectations for uptime and ease of maintenance, harness developers are integrating advanced insulation compounds and modular connector systems that facilitate faster service intervals and reduce the risk of environmental ingress. Meanwhile, electrification trends in tractors, sprayers and self-propelled combines are compelling engineers to balance copper and fiber-optic runs, optimizing weight and resilience without sacrificing data integrity. This introduction sets the stage for examining how evolving regulations, shifting trade policies and emerging technologies are reshaping the agricultural vehicle wire harness landscape.
Transformative Shifts Reshaping the Wire Harness Landscape
The agricultural wire harness landscape is undergoing transformative shifts driven by digitalization, connectivity and electrification. Autonomous guidance systems now demand high-bandwidth Ethernet and FlexRay trunks alongside legacy CAN Bus and LIN Bus backbones, prompting a convergence of multiple network protocols within a single harness design. Concurrently, the push toward zero-emission farming equipment accelerates adoption of copper-heavy power harnesses and fiber optics to support battery management systems and in-cab displays.
Additionally, material innovation has led to broader acceptance of lightweight aluminum conductors and high-performance polymers such as silicone and Teflon, enabling harnesses that resist abrasion, chemicals and moisture. Design styles have also diversified: braided sheaths, coiled assemblies and flat-tape formats address space constraints while preserving flexibility. Finally, the integration of semi-automatic and fully automatic assembly processes has elevated quality control and throughput, redefining cost structures and competitive benchmarks across the supply chain.
Cumulative Impact of United States Tariffs in 2025
The introduction of new U.S. tariffs in 2025 on key harness inputs such as copper rod and aluminum strip has exerted upward pressure on production costs. Suppliers have faced increased landed costs for raw conductor materials, compelling a reevaluation of sourcing strategies and supplier contracts. In parallel, tariffs on imported connector components from certain regions have driven harness manufacturers to localize production of over molded assemblies and under molded cable segments, streamlining supply chains and mitigating duty exposure.
These measures have also accelerated conversations around nearshoring, as OEMs seek closer partnerships with suppliers capable of molded cable fabrication and double-helix braid production within domestic borders. At the same time, some harness houses are passing incremental cost burdens to end users through revised pricing models, impacting total cost of ownership for tractors, sprayers and self-propelled combines. Ultimately, the cumulative effect of these trade policies is fostering strategic realignment across procurement, design and manufacturing operations.
Key Segmentation Insights Across Multiple Dimensions
A granular view of market segmentation reveals clear priorities for harness developers and purchasers alike. Across vehicle types ranging from balers and harvesters to planters, sprayers, tillers, cultivators and tractors, distinct harness architectures are required to accommodate power density, environmental sealing and integration with precision guidance modules. In body and lighting circuits, brake systems and dashboard controls, harness routing must balance electrical performance with ergonomic packaging, while engine and drivetrain harnesses emphasize thermal resistance and vibration damping.
Material choices further refine these systems: aluminum conductors support weight reduction targets, copper enables high-current pathways and fiber optics facilitate noise-immune data channels. Design styles, whether braided, coiled or flat-tape, address spatial constraints and flex life, while technology preferences-automatic, manual or semi-automatic assembly-drive assembly throughput and quality consistency. End-user considerations bifurcate between aftermarket suppliers seeking modular retrofit kits and OEMs embedding fully qualified harnesses at the factory level.
Insulation options span polyurethane, PVC, silicone and Teflon compounds selected for abrasion, chemical, moisture and weather resistance, while system connectivity protocols such as CAN Bus, Ethernet, FlexRay, LIN Bus and MOST define topology requirements. Manufacturing processes from braiding (coaxial and double-helix) to molded cable (over and under) and twisting (cross and standard) underscore the importance of precision tooling. Additional segmentation by conductor size, application environment compliance to ISO, JIS and SAE standards, and compatibility with compact specialty tractors and self-propelled combines completes a comprehensive matrix of market drivers.
This comprehensive research report categorizes the Wire Harnesses for Agriculture Vehicles market into clearly defined segments, providing a detailed analysis of emerging trends and precise revenue forecasts to support strategic decision-making.
- Vehicle Type
- Application
- Material Type
- Design Style
- Technology Type
- End-User Industry
- Insulation Material
- System Connectivity
- Manufacturing Process
- Conductor Size
- Application Environment
- Compliance Standards
- Compatibility With Vehicle Models
Key Regional Insights Driving Market Dynamics
Regional dynamics in the Americas are characterized by a robust mix of OEM assembly and aftermarket retrofit activity, supported by established agricultural equipment hubs and evolving electrification incentives. In North America, proximity to raw material producers and tariff-driven nearshoring have strengthened domestic harness capacity, while in South America, growth in sugarcane and soybean harvesters is fueling demand for durable, moisture-resistant harnesses.
In Europe, Middle East & Africa, stringent emission regulations and advanced precision farming practices are accelerating the uptake of connectivity-rich harness solutions, particularly in Western Europe. Manufacturers in Eastern Europe are gaining competitiveness through cost-effective molded cable production, serving both regional OEMs and export markets. Meanwhile, in Africa and the Middle East, infrastructure investments and mechanization subsidies are creating nascent opportunities for tailored harness designs that emphasize chemical and harsh-weather resistance.
The Asia-Pacific region remains the fastest-growing arena, with electrification initiatives in China and advanced automation projects in Japan driving demand for sophisticated multi-protocol harnesses. India’s expanding tractor fleet and Southeast Asia’s growing mix of planters and cultivators further underscore the region’s strategic importance for harness suppliers aiming to scale capacity and innovate on material and assembly techniques.
This comprehensive research report examines key regions that drive the evolution of the Wire Harnesses for Agriculture Vehicles market, offering deep insights into regional trends, growth factors, and industry developments that are influencing market performance.
- Americas
- Asia-Pacific
- Europe, Middle East & Africa
Strategic Developments Among Leading Industry Players
Competitive intensity in the agricultural vehicle wire harness market is shaped by a blend of global conglomerates and specialized tier-one suppliers. Amphenol Corporation leverages its connector expertise to offer integrated modular harness assemblies, while Aptiv PLC focuses on high-speed data architectures and electromagnetic shielding. Delphi Technologies emphasizes advanced insulation materials and automated assembly capabilities, and Furukawa Electric Co., Ltd. brings deep experience in fiber-optic harnesses.
Kromberg & Schubert GmbH & Co. KG has built a reputation for precision braiding solutions, while Lear Corporation integrates infotainment and power distribution networks. Leoni AG excels in large-scale copper and aluminum conductor fabrication, and Molex Incorporated supports custom over molded solutions. Nexans S.A. offers a wide portfolio of conductor and insulation compounds, and PKC Group Ltd targets heavy-duty agriculture applications.
Samvardhana Motherson Group and Sumitomo Electric Wiring Systems, Inc. continue to expand their regional footprints through strategic partnerships, while Sumitomo Electric Industries, Ltd. drives innovation in Teflon and silicone insulations. TE Connectivity offers robust harsh-environment connectors, and Yazaki Corporation emphasizes lean manufacturing and just-in-time delivery models, collectively raising the bar on quality, lead times and total cost of ownership.
This comprehensive research report delivers an in-depth overview of the principal market players in the Wire Harnesses for Agriculture Vehicles market, evaluating their market share, strategic initiatives, and competitive positioning to illuminate the factors shaping the competitive landscape.
- Amphenol Corporation
- Aptiv PLC
- Delphi Technologies
- Furukawa Electric Co., Ltd.
- Kromberg & Schubert GmbH & Co. KG
- Lear Corporation
- Leoni AG
- Molex Incorporated
- Nexans S.A.
- PKC Group Ltd
- Samvardhana Motherson Group
- Sumitomo Electric Industries, Ltd.
- Sumitomo Electric Wiring Systems, Inc.
- TE Connectivity
- Yazaki Corporation
Actionable Recommendations for Industry Leaders
To navigate the evolving agricultural wire harness landscape, industry leaders should pursue a multi-pronged approach. First, prioritize investments in advanced material research, targeting next-generation insulation compounds and lightweight conductor alloys to meet emerging performance and sustainability benchmarks. Second, diversify manufacturing footprints by incorporating nearshoring strategies that optimize duty exposure and enhance supply resilience, particularly for braided and molded cable processes.
Third, develop modular harness architectures that streamline integration across multiple vehicle platforms, reducing engineering lead time and inventory complexity. Fourth, expand capabilities in high-speed connectivity protocols such as Ethernet and FlexRay, ensuring compatibility with evolving precision agriculture electronics. Fifth, collaborate closely with OEMs and aftermarket suppliers to co-create retrofit solutions that address abrasion and chemical resistance requirements in diverse operating environments.
Finally, implement digital quality monitoring and Industry 4.0 practices on the production floor to bolster first-pass yield, traceability and rapid changeover between coaxial braid, standard twisting and under-molded harness variants. This holistic strategy will position harness suppliers to capitalize on both incumbent and emerging opportunities.
Explore AI-driven insights for the Wire Harnesses for Agriculture Vehicles market with ResearchAI on our online platform, providing deeper, data-backed market analysis.
Ask ResearchAI anything
World's First Innovative Al for Market Research
Conclusion
The agricultural vehicle wire harness market stands at the convergence of technological innovation, regulatory complexity and shifting trade policies. As connectivity and electrification initiatives accelerate, harness designers must balance the demands of high-bandwidth networks and power distribution with the realities of field-level robustness. Material and process innovations in insulation, conductor composition and automated assembly will define competitive differentiation, while strategic supply-chain realignments in response to tariff pressure will determine cost leadership.
Success hinges on a clear segmentation strategy that aligns vehicle types, application zones and environmental requirements with targeted design and manufacturing processes. Regional insights highlight the necessity of localized production agility in the Americas, compliance-driven innovation in EMEA and capacity expansion in Asia-Pacific. Meanwhile, collaboration with technology-focused OEMs and aftermarket partners will unlock new retrofit and upgrade pathways.
By integrating these themes, industry participants can navigate uncertainties, deliver next-generation harness solutions and sustain profitable growth within this dynamic, mission-critical sector.
This section provides a structured overview of the report, outlining key chapters and topics covered for easy reference in our Wire Harnesses for Agriculture Vehicles market comprehensive research report.
- Preface
- Research Methodology
- Executive Summary
- Market Overview
- Market Dynamics
- Market Insights
- Cumulative Impact of United States Tariffs 2025
- Wire Harnesses for Agriculture Vehicles Market, by Vehicle Type
- Wire Harnesses for Agriculture Vehicles Market, by Application
- Wire Harnesses for Agriculture Vehicles Market, by Material Type
- Wire Harnesses for Agriculture Vehicles Market, by Design Style
- Wire Harnesses for Agriculture Vehicles Market, by Technology Type
- Wire Harnesses for Agriculture Vehicles Market, by End-User Industry
- Wire Harnesses for Agriculture Vehicles Market, by Insulation Material
- Wire Harnesses for Agriculture Vehicles Market, by System Connectivity
- Wire Harnesses for Agriculture Vehicles Market, by Manufacturing Process
- Wire Harnesses for Agriculture Vehicles Market, by Conductor Size
- Wire Harnesses for Agriculture Vehicles Market, by Application Environment
- Wire Harnesses for Agriculture Vehicles Market, by Compliance Standards
- Wire Harnesses for Agriculture Vehicles Market, by Compatibility With Vehicle Models
- Americas Wire Harnesses for Agriculture Vehicles Market
- Asia-Pacific Wire Harnesses for Agriculture Vehicles Market
- Europe, Middle East & Africa Wire Harnesses for Agriculture Vehicles Market
- Competitive Landscape
- ResearchAI
- ResearchStatistics
- ResearchContacts
- ResearchArticles
- Appendix
- List of Figures [Total: 42]
- List of Tables [Total: 735 ]
Contact for In-Depth Research Access
For detailed insights and tailored guidance on optimizing your agricultural vehicle wire harness strategy, connect with Ketan Rohom, Associate Director, Sales & Marketing. He can guide you through the latest research findings, answer your questions and facilitate access to the comprehensive market report. Reach out today to secure the intelligence you need to stay ahead in this rapidly evolving sector.
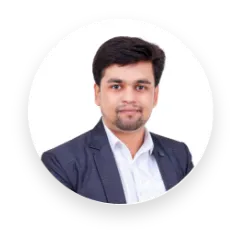
- When do I get the report?
- In what format does this report get delivered to me?
- How long has 360iResearch been around?
- What if I have a question about your reports?
- Can I share this report with my team?
- Can I use your research in my presentation?