Introduction to Wire Torsion Testing and Its Strategic Importance
Wire torsion testing plays a critical role in assessing the mechanical performance of wires, cables, springs, and other components that undergo twisting stresses. By applying controlled torsional forces and precisely measuring the resulting deformation, these instruments verify material durability, predict lifecycle performance, and ensure compliance with stringent quality standards across automotive, aerospace, electronics, medical, and energy sectors.
As product specifications become more demanding and testing cycles accelerate, the emphasis on rapid testing, high-precision measurement, and user-friendly interfaces continues to intensify. In this context, market participants are investing in modular hardware designs, advanced sensor arrays, and integrated software analytics that enable real-time data visualization and automation. The convergence of digitalization, materials science advancements, and global trade considerations underscores the need for a holistic understanding of the market environment. Through this summary, stakeholders will gain actionable insights into transformative shifts, segmentation nuances, regional variations, and the competitive scene, all of which inform strategic planning and investment priorities.
Moving forward, decision-makers must navigate evolving technological innovations and shifting policy frameworks to drive efficiency, ensure compliance, and foster sustainable growth. This executive summary offers a concise yet comprehensive overview of current market dynamics, highlights pivotal trends and regulatory impacts, and lays out strategic considerations essential for maintaining a competitive edge in the wire torsion tester arena.
Transformative Shifts Shaping the Wire Torsion Tester Landscape
Recent years have witnessed transformative shifts in the wire torsion tester landscape, driven by rapid digitalization and the rise of Industry 4.0. Advanced sensor integration paired with cloud-based data management is enabling predictive maintenance models and remote diagnostics, reducing unplanned downtime and optimizing test throughput. At the same time, automation platforms equipped with robotic handlers are streamlining sample preparation and handling, thereby improving consistency and safety in high-volume manufacturing environments.
Moreover, the integration of artificial intelligence and machine learning algorithms into test software has elevated the capability to identify subtle failure patterns and correlate them with material microstructures. As sustainability emerges as a key focus, manufacturers are developing eco-friendly tester designs that minimize energy consumption and material waste. Modular architectures and open-architecture software frameworks are becoming standard, allowing seamless upgrades and customization to meet evolving testing protocols and regulatory requirements.
In parallel, the proliferation of IoT-enabled testing platforms has fostered real-time collaboration across global R&D centers. Engineers can now share live test data, apply advanced analytics, and implement iterative design improvements on the fly. This interconnected ecosystem not only accelerates product development cycles but also promotes alignment between quality assurance and production teams.
Finally, the growing importance of compliance with international standards-such as ISO, ASTM, and JIS-has prompted providers to offer turnkey validation packages, complete with calibration services and audit-friendly documentation. Collectively, these technological and regulatory developments underscore a paradigm shift toward smarter, more efficient, and fully traceable torsion testing solutions.
Cumulative Impact of United States Tariffs in 2025 on Wire Torsion Testing
United States tariffs implemented in early 2025 on critical raw materials and component imports have had a cumulative impact on the wire torsion tester market. Higher duties on steel and aluminum alloys, as well as specialized electronics and precision bearings, have increased production costs for tester manufacturers. These cost pressures have been further compounded by additional levies on imported testing accessories, such as grips, chucks, and sensor modules, prompting some suppliers to reevaluate their supply chains.
As a result, many stakeholders are pursuing supply chain diversification strategies, including sourcing raw materials from duty-free trade partners and nearshoring critical machining operations. Domestic component fabrication has gained momentum as firms seek to mitigate tariff-related cost volatility and ensure timely delivery of key parts. However, scaling localized manufacturing often requires substantial capital investment in new tooling and workforce training, which can delay product rollouts and constrain innovation.
In response to these challenges, market participants are exploring collaborative partnerships and long-term agreements with domestic steel producers and electronics vendors to secure price stability. Some are also leveraging advanced materials, such as high-strength alloys and composite-infused wires, to offset increased input costs while maintaining or improving performance specifications. Overall, the tariff environment is reshaping competitive dynamics by favoring organizations with agile sourcing, strong supplier relationships, and the financial capacity to invest in localized operations.
Key Insights from Market Segmentation of Wire Torsion Testers
When analyzing the market based on product type, testers can be categorized into bench top, fixed, and portable configurations. Bench top instruments dominate laboratory and R&D settings, where automated variants are prized for their high-throughput capabilities, while manual versions remain relevant in smaller labs and maintenance workshops. Fixed systems, often integrated into production lines, provide continuous monitoring in mass-manufacturing environments, and portable devices offer field testing flexibility for on-site quality assurance and maintenance tasks.
Evaluation by application reveals distinct usage patterns across maintenance, mass production, quality assurance, and research and development. Maintenance departments leverage portable and bench top testers to conduct rapid inspections, whereas mass-production facilities rely on fixed systems to ensure each unit meets torque specifications without slowing the assembly line. Quality assurance teams favor high-precision bench top units for statistical sampling, and R&D engineers deploy both bench top and fixed platforms to perform material testing and prototype evaluation with advanced control algorithms.
From a testing method perspective, cyclic torsion testing remains the workhorse for fatigue and endurance studies, while dynamic torsion methods-encompassing impulse torsion and rotational speed variation tests-unlock insights into performance under real-world stress fluctuations. Static torsion tests, though simpler, are critical for establishing baseline torque thresholds and material yield points. Each methodology addresses specific performance questions, and many organizations maintain multi-method portfolios to cover the full spectrum of testing requirements.
Industry segmentation highlights aerospace, automotive, electronics, energy, and medical sectors as primary end-users. Aerospace manufacturers demand ultra-high precision and robust design to meet stringent safety certifications, and the automotive industry increasingly requires rapid testing capabilities to streamline high-volume production. In electronics, compact testers support miniature component evaluation, while energy companies utilize torsion testing to validate cable integrity under cyclic loading. In medical applications, cardiac and orthopedic device producers depend on reliable torsion measurements to verify implant durability and patient safety.
Operational feature segmentation distinguishes products by high precision, rapid testing, robust design, and user-friendly interfaces. Solutions optimized for high-precision outputs attract research labs, whereas rapid-testing platforms-characterized by fast setup and quick turnaround-are essential for high-volume environments. Robust design variants withstand harsh factory conditions, and intuitive user interfaces lower the barrier to adoption among non-specialist operators. Success in the marketplace often hinges on delivering the optimal combination of these operational attributes to suit specific customer workflows.
This comprehensive research report categorizes the Wire Torsion Tester market into clearly defined segments, providing a detailed analysis of emerging trends and precise revenue forecasts to support strategic decision-making.
- Product Type
- Application
- Testing Method
- Industry
- Operational Feature
Regional Dynamics and Key Opportunities Across Major Geographies
The Americas region encompasses both mature markets in North America and emerging opportunities in Latin America. In the United States and Canada, stringent regulatory frameworks and high manufacturing standards drive demand for advanced testing solutions, particularly in automotive, aerospace, and medical device segments. Investment in automation and digital traceability is robust, reflecting broader Industry 4.0 adoption. Meanwhile, Latin American manufacturers are gradually upgrading from basic manual testers to more sophisticated bench top and portable systems, spurred by quality improvement initiatives and infrastructure modernization.
In Europe, Middle East & Africa, market growth is driven by stringent certification requirements in the aerospace and energy sectors, as well as the electronics industry’s shift toward miniaturization. European nations, particularly Germany and the United Kingdom, lead in R&D spending and tend to favor high-precision, automated bench top testers integrated with advanced data analytics. In the Middle East, infrastructure projects in energy and construction are fostering demand for robust, field-deployable testers, while African markets remain nascent but show promise as government-led industrialization programs gain traction.
Asia-Pacific represents the fastest-evolving region, characterized by rapid industrialization, expanding automotive production, and a growing electronics manufacturing ecosystem. In China, domestic manufacturers are intensifying efforts to upgrade testing capabilities from static and cyclic torsion methods to dynamic, IoT-enabled platforms. Japan and South Korea continue to prioritize high-precision bench top systems for semiconductor and automotive component testing. Southeast Asian nations, including Thailand and Vietnam, are emerging as manufacturing hubs and are increasingly investing in portable and fixed testers to support local production lines and maintenance operations.
This comprehensive research report examines key regions that drive the evolution of the Wire Torsion Tester market, offering deep insights into regional trends, growth factors, and industry developments that are influencing market performance.
- Americas
- Asia-Pacific
- Europe, Middle East & Africa
Competitive Landscape: Leading Companies in Wire Torsion Testing
The competitive landscape in wire torsion testing is marked by established global leaders and a growing roster of specialized innovators. Key players with a long-standing market presence-such as Instron Corporation, MTS Systems Corporation, Shimadzu Corporation, ZwickRoell Group, and Tinius Olsen-are renowned for their comprehensive product portfolios, rigorous validation services, and integrated software ecosystems that meet the most demanding industry standards.
Apex Test Machinery and Archway Engineering have distinguished themselves with modular, high-throughput automation solutions, while Benchmark Testing Technologies, Brookfield Engineering, Inc., and Celerity Test Equipment focus on precision sensor integration and turnkey calibration offerings. Dynamic Testing Solutions, EuroTest Instruments, ForceTech Systems, and Kinetic Force Technologies emphasize robust design for field operations. MechTest Technologies Ltd., NextGen Testing Systems, OmniTest Solutions, and Optimum Test Labs drive innovation in user-friendly interfaces and rapid-testing platforms.
Further competition comes from Pinnacle Engineering Instruments, Precision Dynamics Inc., PrimeTest Corp, QuantTest Engineering, Radian Technology Solutions, Reliance Test Instruments, RotaryTech Solutions Inc., SolidState Testing Instruments, Sterling Engineering Solutions, TestMaster Instruments, TorqueTest Innovations LLC, Vector Mechanics Inc., and other emerging firms that are carving niche segments by offering specialized testing methods, industry-specific configurations, and value-added services such as remote diagnostics and predictive analytics. Many of these companies are expanding their service networks and investing in local support facilities to ensure fast calibration and maintenance, further intensifying competition in core markets.
This comprehensive research report delivers an in-depth overview of the principal market players in the Wire Torsion Tester market, evaluating their market share, strategic initiatives, and competitive positioning to illuminate the factors shaping the competitive landscape.
- Apex Test Machinery
- Archway Engineering
- Benchmark Testing Technologies
- Brookfield Engineering, Inc.
- Celerity Test Equipment
- Dynamic Testing Solutions
- EuroTest Instruments
- ForceTech Systems
- Instron Corporation
- Kinetic Force Technologies
- MechTest Technologies Ltd.
- MTS Systems Corporation
- NextGen Testing Systems
- OmniTest Solutions
- Optimum Test Labs
- Pinnacle Engineering Instruments
- Precision Dynamics Inc.
- PrimeTest Corp
- QuantTest Engineering
- Radian Technology Solutions
- Reliance Test Instruments
- RotaryTech Solutions Inc.
- Shimadzu Corporation
- SolidState Testing Instruments
- Sterling Engineering Solutions
- TestMaster Instruments
- Tinius Olsen
- TorqueTest Innovations LLC
- Vector Mechanics Inc.
- ZwickRoell Group
Actionable Recommendations for Industry Leaders in Wire Torsion Testing
To navigate the complex dynamics of the wire torsion tester market, industry leaders should prioritize diversified sourcing strategies, balanced by strategic nearshoring and robust supplier partnerships. Implementing dual sourcing for critical alloys and electronics components will mitigate tariff volatility and safeguard production continuity. Concurrently, investing in modular automation platforms with scalable software architectures enables rapid adaptation to evolving testing standards and customer requirements.
Enhancing digital capabilities is equally crucial. Firms should integrate IoT-enabled sensors with cloud-based analytics to drive real-time performance monitoring and predictive maintenance workflows. Developing or licensing advanced AI models tailored to torsion data can unlock deeper material insights and foster more efficient R&D cycles. Additionally, embedding compliance-ready documentation and audit trails within testing software will streamline regulatory approvals and quality audits across global markets.
Leaders must also cultivate cross-functional collaboration between R&D, quality, production, and sales teams to align product development with customer expectations. Establishing technical training programs and certification courses will empower end users and strengthen brand loyalty. Finally, exploring strategic collaborations or joint ventures with regional distributors and system integrators can accelerate market penetration in high-growth geographies while sharing the burden of capital investment and operational risk. Regularly benchmarking product performance against competitors and soliciting customer feedback will ensure that feature roadmaps remain aligned with market demand and that innovations deliver tangible ROI.
Explore AI-driven insights for the Wire Torsion Tester market with ResearchAI on our online platform, providing deeper, data-backed market analysis.
Ask ResearchAI anything
World's First Innovative Al for Market Research
Conclusion: Navigating Challenges and Leveraging Growth Drivers
Navigating the wire torsion tester market requires a nuanced understanding of technological advancements, regulatory landscapes, and global trade dynamics. The convergence of digitalization, automation, and sustainable design principles is redefining product expectations, while tariff-induced cost pressures underscore the importance of supply chain resilience. By dissecting market segmentation, regional drivers, and competitive strategies, stakeholders can identify high-value niches and allocate resources effectively.
In essence, success in this landscape depends on balancing innovation with operational agility, leveraging data-driven insights, and forging strategic partnerships that enhance both product offerings and market reach. As the market continues to evolve, the organizations that anticipate change, adapt swiftly, and maintain a customer-centric focus will emerge as the leaders in wire torsion testing.
This section provides a structured overview of the report, outlining key chapters and topics covered for easy reference in our Wire Torsion Tester market comprehensive research report.
- Preface
- Research Methodology
- Executive Summary
- Market Overview
- Market Dynamics
- Market Insights
- Cumulative Impact of United States Tariffs 2025
- Wire Torsion Tester Market, by Product Type
- Wire Torsion Tester Market, by Application
- Wire Torsion Tester Market, by Testing Method
- Wire Torsion Tester Market, by Industry
- Wire Torsion Tester Market, by Operational Feature
- Americas Wire Torsion Tester Market
- Asia-Pacific Wire Torsion Tester Market
- Europe, Middle East & Africa Wire Torsion Tester Market
- Competitive Landscape
- ResearchAI
- ResearchStatistics
- ResearchContacts
- ResearchArticles
- Appendix
- List of Figures [Total: 26]
- List of Tables [Total: 460 ]
Call-to-Action: Partner with Ketan Rohom to Acquire the Full Market Report
To access the full suite of proprietary data, in-depth analysis, and strategic frameworks presented in this report, please reach out to Ketan Rohom, Associate Director, Sales & Marketing. Engage directly to receive customized briefing options, sample insights, and details on how this comprehensive study can inform your strategic planning and investment decisions. Contact Ketan to secure your copy of the market research report and position your organization to capitalize on emerging opportunities with confidence.
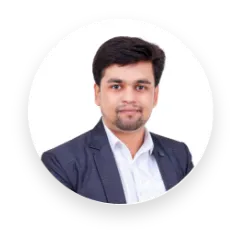
- When do I get the report?
- In what format does this report get delivered to me?
- How long has 360iResearch been around?
- What if I have a question about your reports?
- Can I share this report with my team?
- Can I use your research in my presentation?