High-Temperature Wire Wound Strain Gauges: Setting the Stage
Wire wound high-temperature strain gauges have become indispensable in applications demanding precise deformation measurements under extreme thermal conditions. By leveraging a coiled wire element bonded to a substrate, these sensors maintain accuracy and stability at temperatures that would degrade conventional foil-based devices. As industries ranging from aerospace engine testing to power generation increasingly push the boundaries of operational heat, the need for robust sensing solutions has never been greater.
The wire wound design offers enhanced durability and resistance to creep, enabling reliable strain measurement in environments exceeding 400 °C. This advantage translates into improved component longevity, reduced downtime, and more accurate performance assessments. Furthermore, recent advances in metallurgy and bonding techniques have expanded the usable temperature range, making these gauges a preferred choice for critical infrastructure monitoring and high-performance machinery testing.
In light of shifting regulatory landscapes, evolving material technologies, and emerging market demands, this executive summary delivers a concise yet comprehensive overview of core trends, segmentation insights, regional dynamics, competitive positioning, and strategic recommendations. It is crafted to equip decision-makers and technical leaders with actionable intelligence for navigating the future of high-temperature strain gauge deployment.
Emerging Forces Reshaping the Strain Gauge Sector
The landscape of high-temperature sensing is undergoing rapid transformation driven by novel materials, digital integration, and manufacturing innovations. Ceramic and semiconductor-based wire wound elements are gaining traction over traditional polymer and metal foil counterparts, as they deliver superior thermal stability and longer operational lifespans. Concurrently, additive manufacturing techniques are enabling custom substrate geometries that optimize gauge placement and adhesion on curved or irregular surfaces.
Digitalization has ushered in the development of gauges with embedded signal conditioning and self-calibrating capabilities, minimizing the need for external data acquisition hardware and manual recalibration. As the Industrial Internet of Things (IIoT) ecosystem expands, real-time wireless telemetry and predictive analytics are becoming mainstream, empowering maintenance teams to detect micro-deformations before they escalate into costly failures.
Automotive and aerospace sectors are also redefining application paradigms by integrating strain sensing into structural health monitoring systems for electric vehicles and hypersonic platforms. In parallel, civil and mechanical engineering projects now leverage surface-mounted and embedded configurations to monitor infrastructure integrity and mechanical fatigue with unprecedented granularity. These converging forces are reshaping product roadmaps, supply chains, and test protocols, setting a new bar for performance excellence in high-temperature environments.
Assessing the 2025 U.S. Tariff Effects on Strain Gauge Economics
United States tariff measures slated for 2025 are exerting compounding pressure on global supply chains and cost structures within the strain gauge ecosystem. Imported raw wire materials and specialized substrates now face elevated duties, compelling manufacturers to reassess sourcing strategies and negotiate supplier contracts under tighter margins. Many producers have responded by pursuing regional partnerships and local production schemes to mitigate duty impacts and ensure continuity of critical components.
These tariff-induced cost increases have, in turn, driven end users to explore alternative materials and gauge configurations that maintain performance while optimizing total cost of ownership. Some organizations have accelerated the qualification of domestically sourced semiconductors and ceramics, reducing exposure to cross-border duties. Others have implemented lean manufacturing principles to absorb incremental expenses through process efficiencies rather than passing them entirely onto customers.
Moreover, compliance complexities and extended customs clearance times are prompting firms to consolidate logistics networks and invest in digital trade management platforms. Such initiatives have improved visibility into landed costs and expedited decision-making. Overall, the 2025 tariff landscape has acted as a catalyst for supply chain resilience, technology diversification, and cost containment measures across the high-temperature strain gauge sector.
Deep Dive into Market Segmentation Dimensions
A granular examination of market segmentation reveals diverse trajectories across sensor types and materials. Multiple element variants are capturing share in applications demanding multi-axis measurement, while single element designs continue to satisfy cost-sensitive projects. Within the material domain, ceramic formulations are preferred in ultra-high temperature testing, whereas metal foil remains a workhorse for moderately elevated conditions. Polymer-based gauges are now phased out of critical heat scenarios, and semiconductor sensors are emerging where miniaturization and digital interfacing are priorities.
Temperature adaptability itself bifurcates into high temperature and standard ranges, with each category tailored to its respective performance envelope. In aerospace and automotive powertrain testing the high range dominates, while standard ranges retain strongholds in civil and mechanical engineering contexts. Applications span from hypersonic wind tunnel experiments to medical device reliability trials, reflecting the breadth of demand. Installation considerations also vary: surface mount configurations are favored for retrofits, bonded and welded options excel in new build environments, and embedded solutions gain momentum where structural integration is paramount.
Data output has evolved to encompass both analog and digital signal types, with digital architectures facilitating advanced analytics and system interoperability. Resistance value segmentation further refines choices: low resistance gauges below 120 Ω are prevalent in high-current testing rigs, medium resistance units between 120 Ω and 350 Ω strike a balance of sensitivity and noise immunity, and high resistance devices above 350 Ω offer optimal performance for precision metrology. Testing environments themselves split between indoor laboratories and outdoor field deployments, each imposing unique calibration and durability requirements. End users range from construction and energy operators to manufacturing lines, while package formats alternate between discrete gauge elements and integrated module-based assemblies. Calibration approaches include both manual procedures and self-calibrating designs, and data acquisition systems offer standalone options as well as seamless integration with onboard software. Supply voltage tiers of low, medium, and high voltage align with application constraints, and anticipated operational lifespans frame decision-making for long-term continuous monitoring versus short-term diagnostic campaigns.
This comprehensive research report categorizes the Wire Wound High-Temperature Strain Gauge market into clearly defined segments, providing a detailed analysis of emerging trends and precise revenue forecasts to support strategic decision-making.
- Sensor Type
- Strain Gauge Material
- Temperature Adaptability
- Application Domain
- Installation Type
- Output Signal Type
- Resistance Values
- Test Environment
- End User Industry
- Package Type
- Calibration Type
- Data Acquisition Systems
- Supply Voltage
- Operational Lifespan
Regional Market Dynamics and Growth Patterns
Regional dynamics exhibit marked contrasts driven by industrial policy, infrastructure investment, and technological adoption rates. In the Americas, established aerospace and automotive testing hubs maintain steady demand for high-temperature strain sensing, and reshoring trends are reinforcing domestic manufacturing footprints. Research institutions in North America are also pioneering next-generation wire wound materials, accelerating innovation cycles.
The Europe, Middle East & Africa corridor combines mature markets in Western Europe with emerging growth in the Gulf region, where petrochemical and power generation projects are ramping up high-temperature component monitoring. Regulatory emphasis on safety and environmental compliance fuels demand for robust gauges certified to stringent standards. Local suppliers often collaborate with global manufacturers to co-develop customized solutions.
Asia-Pacific continues to command significant share as industrial expansion and infrastructure development proceed at pace. Major manufacturing centers in China, South Korea, and India are integrating wire wound sensors into smart factory initiatives, while Japan and Taiwan concentrate on research-intensive applications. Cross-border partnerships and technology licensing agreements are commonplace, facilitating rapid diffusion of advanced gauge designs across the region.
This comprehensive research report examines key regions that drive the evolution of the Wire Wound High-Temperature Strain Gauge market, offering deep insights into regional trends, growth factors, and industry developments that are influencing market performance.
- Americas
- Asia-Pacific
- Europe, Middle East & Africa
Competitive Landscape and Leading Innovators
Market leadership is distributed among a cohort of specialized developers and technology conglomerates, each contributing distinct strengths. Epsilon Technology Corporation has built a reputation for rugged high-temperature alloys and custom sensor geometries. Geosense Ltd excels in geotechnical monitoring solutions, leveraging wire wound gauges for structural health assessments. HBM (Hottinger Brüel & Kjær) brings decades of metrology expertise and advanced signal conditioning modules to complex testing scenarios, while Hitec Messwandler GmbH offers precision transformers and coupling devices that enhance measurement fidelity.
Kyowa Electronic Instruments Co., Ltd. and Micro-Measurements, a Vishay brand, maintain global footprints and extensive calibration services, ensuring repeatable performance in harsh environments. OMEGA Engineering, Inc. focuses on rapid prototyping and modular system integration, and Spectris plc leverages analytics software to interpret strain data within broader performance monitoring platforms. Strainsert Co. specializes in high-resistance gauge fabrication techniques, complementing innovations by Tokyo Sokki Kenkyujo Co., Ltd. (TML) in miniature semiconductor sensing. Transducer Techniques, LLC delivers ruggedized packaging options for field deployments, and Vishay Precision Group, Inc. integrates industrial networking capabilities into gauge modules for seamless data acquisition.
This comprehensive research report delivers an in-depth overview of the principal market players in the Wire Wound High-Temperature Strain Gauge market, evaluating their market share, strategic initiatives, and competitive positioning to illuminate the factors shaping the competitive landscape.
- Epsilon Technology Corporation
- Geosense Ltd
- HBM (Hottinger Brüel & Kjær)
- Hitec Messwandler GmbH
- Kyowa Electronic Instruments Co., Ltd.
- Micro-Measurements, a Vishay brand
- OMEGA Engineering, Inc.
- Spectris plc
- Strainsert Co.
- Tokyo Sokki Kenkyujo Co., Ltd. (TML)
- Transducer Techniques, LLC
- Vishay Precision Group, Inc.
Strategic Roadmap for Industry Leadership
Industry leaders should prioritize strategic investment in advanced material research, focusing on alloys and ceramic composites that extend operational temperature thresholds and resist creep. Diversifying supply chains through multi-regional partnerships will mitigate exposure to tariff fluctuations and geopolitical disruptions. Embracing digital transformation by adopting gauges with embedded signal processing and self-calibration functionality can reduce instrument footprints and accelerate deployment timelines.
Collaborations with OEMs in aerospace, automotive, and energy sectors will unlock co-development opportunities for application-specific gauge configurations. Establishing center-of-excellence test facilities that simulate high-temperature environments can streamline validation cycles and strengthen customer trust. Leaders must also standardize on modular packaging formats and universal data acquisition protocols to ensure interoperability within IIoT frameworks.
Proactive engagement with regulatory bodies and industry associations will shape emerging standards and certification requirements, positioning innovators as thought leaders. Investing in workforce training programs that cover advanced installation techniques and in-field calibration best practices will reinforce service excellence. Finally, integrating sustainability criteria-such as recyclable substrates and energy-efficient manufacturing processes-will align product roadmaps with broader environmental goals and enhance brand credibility.
Explore AI-driven insights for the Wire Wound High-Temperature Strain Gauge market with ResearchAI on our online platform, providing deeper, data-backed market analysis.
Ask ResearchAI anything
World's First Innovative Al for Market Research
Synthesis and Forward Outlook
In summary, the convergence of material science advances, digital integration, and evolving regulatory and tariff landscapes is redefining the high-temperature strain gauge market. Wire wound designs remain central to accurate deformation measurement under extreme heat, yet success will hinge on agility in supply chain management, commitment to R&D, and ability to deliver seamless data solutions.
Companies that embrace modular architectures, leverage regional innovation clusters, and forge cross-sector partnerships will secure competitive advantage. By aligning strategic priorities around advanced calibration methods, self-diagnosing sensors, and sustainable manufacturing practices, industry stakeholders can navigate complexity and accelerate growth. As monitoring requirements intensify across aerospace, automotive, energy, and infrastructure domains, the capacity to anticipate customer needs and tailor high-temperature strain sensing solutions will serve as the ultimate differentiator.
This section provides a structured overview of the report, outlining key chapters and topics covered for easy reference in our Wire Wound High-Temperature Strain Gauge market comprehensive research report.
- Preface
- Research Methodology
- Executive Summary
- Market Overview
- Market Dynamics
- Market Insights
- Cumulative Impact of United States Tariffs 2025
- Wire Wound High-Temperature Strain Gauge Market, by Sensor Type
- Wire Wound High-Temperature Strain Gauge Market, by Strain Gauge Material
- Wire Wound High-Temperature Strain Gauge Market, by Temperature Adaptability
- Wire Wound High-Temperature Strain Gauge Market, by Application Domain
- Wire Wound High-Temperature Strain Gauge Market, by Installation Type
- Wire Wound High-Temperature Strain Gauge Market, by Output Signal Type
- Wire Wound High-Temperature Strain Gauge Market, by Resistance Values
- Wire Wound High-Temperature Strain Gauge Market, by Test Environment
- Wire Wound High-Temperature Strain Gauge Market, by End User Industry
- Wire Wound High-Temperature Strain Gauge Market, by Package Type
- Wire Wound High-Temperature Strain Gauge Market, by Calibration Type
- Wire Wound High-Temperature Strain Gauge Market, by Data Acquisition Systems
- Wire Wound High-Temperature Strain Gauge Market, by Supply Voltage
- Wire Wound High-Temperature Strain Gauge Market, by Operational Lifespan
- Americas Wire Wound High-Temperature Strain Gauge Market
- Asia-Pacific Wire Wound High-Temperature Strain Gauge Market
- Europe, Middle East & Africa Wire Wound High-Temperature Strain Gauge Market
- Competitive Landscape
- ResearchAI
- ResearchStatistics
- ResearchContacts
- ResearchArticles
- Appendix
- List of Figures [Total: 44]
- List of Tables [Total: 766 ]
Next Steps: Engage with Ketan Rohom
To obtain the full market research report and gain deeper insights into technology trends, competitive benchmarks, and strategic imperatives, please reach out to Ketan Rohom (Associate Director, Sales & Marketing at 360iResearch). Ketan can guide you through the report’s key findings, discuss customized data requirements, and facilitate a seamless purchase process. Engage now to equip your organization with the actionable intelligence needed to excel in the evolving high-temperature strain gauge arena.
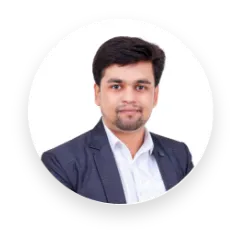
- When do I get the report?
- In what format does this report get delivered to me?
- How long has 360iResearch been around?
- What if I have a question about your reports?
- Can I share this report with my team?
- Can I use your research in my presentation?