The Zinc Flake Coating Market size was estimated at USD 1.41 billion in 2024 and expected to reach USD 1.49 billion in 2025, at a CAGR 6.01% to reach USD 2.00 billion by 2030.

Innovative Zinc Flake Coating Emergence and Its Strategic Importance in Shaping a Future-Ready Corrosion Protection Industry Landscape
In recent years, zinc flake coating has ascended as a pivotal solution in combating corrosion across a myriad of industrial applications. Distinguished by its exceptional barrier protection, this technology leverages an intricate blend of zinc and aluminum flakes bound within a resin matrix to form a highly adherent and durable coating. As industries pursue enhanced performance and longer service life for critical components, the adoption of zinc flake systems has surged, driven by its ability to deliver rust prevention without the use of toxic heavy metals. This evolution marks a significant departure from traditional plating techniques, offering a more environmentally responsible alternative that aligns with tightening regulatory frameworks and the global shift toward greener technologies.
Moreover, the nuanced performance attributes of zinc flake coatings-such as combined sacrificial protection and cathodic inhibition-have positioned it as a preferred choice for applications demanding both reliability and long-term cost-efficiency. Transitioning from conventional methods, manufacturers are now leveraging advanced formulations to ensure uniform coverage, even in complex geometries. This has opened avenues in sectors ranging from automotive and aerospace to construction and heavy machinery, where component integrity is paramount. By providing a resilient shield against harsh environments, zinc flake coating not only extends asset lifespans but also enhances safety margins, thereby cementing its strategic importance in modern corrosion management landscapes.
Key Transformative Shifts Driving Zinc Flake Coating Adoption and Technological Advancements Across Diverse Industrial Sectors
The landscape of zinc flake coating is undergoing transformative shifts, propelled by evolving performance requirements and accelerating sustainability mandates. One key driver is the heightened focus on environmentally benign coatings, prompting formulators to refine resin systems and reduce volatile organic compounds. The pursuit of compliance with stringent global environmental standards, such as REACH and emerging regional regulations, has accelerated innovation in low-temperature cure technologies, enabling manufacturers to minimize energy consumption and carbon footprints.
Concurrently, the surge in electric vehicle manufacturing has introduced new challenges for battery housing and chassis components, where enhanced corrosion resistance is critical for long-term reliability. This sector-specific demand has catalyzed research into hybrid coating systems that integrate nanomaterials for improved abrasion resistance and electrical conductivity. Furthermore, advancements in process automation and quality control-driven by Industry 4.0 initiatives-are facilitating real-time monitoring of coating thickness and curing parameters. Such digital integration ensures consistent coating performance while reducing waste and operational costs. As a result, the zinc flake coating landscape is shifting from a predominantly manual operation to a data-driven ecosystem, enabling manufacturers to deliver superior protective solutions at scale.
Comprehensive Analysis of United States Tariffs in 2025 and Their Cascading Impact on Zinc Flake Coating Supply Chain Dynamics
The introduction of new tariffs by the United States government in early 2025 has generated significant recalibrations across the zinc flake coating supply chain. By imposing additional duties on imported raw materials and pretreated components, end users and suppliers alike have faced increased procurement costs and extended lead times. This shift has compelled coating formulators to reassess sourcing strategies, with many exploring alternative suppliers in friendlier trade regions or negotiating bulk contracts to alleviate cost pressures.
These tariff-induced dynamics have also accelerated the trend toward nearshoring, prompting several coating applicators to relocate or expand production facilities closer to key automotive, aerospace, and industrial clients. This geographic repositioning not only mitigates the financial impact of duties but also enhances supply chain resilience by reducing transit times and exposure to maritime disruptions. Furthermore, the increased cost base has spurred collaborative innovation between raw material producers and end users to develop cost-optimized formulations that maintain performance criteria while utilizing domestically sourced inputs. Consequently, the U.S. tariffs of 2025 have reshaped the competitive landscape, prompting stakeholders to forge strategic partnerships and invest in process efficiencies to sustain profitability and secure reliable access to critical coating technologies.
Critical Segmentation Insights Revealing Distinct Trends by Type Coating Process and Application Landscape in Zinc Flake Coating Market
Understanding the zinc flake coating ecosystem requires a granular evaluation of distinct market segments. When considering the choice of solvent-based versus water-based systems, organizations are weighing environmental compliance obligations against performance consistency. Solvent-based formulations often excel in low-temperature cure profiles, offering rapid throughput for high-volume production, while water-based alternatives attract interest for their reduced emissions and simplified disposal requirements.
At the core of formulation development lies the distinction between inorganic and organic zinc flake coatings. Inorganic variants typically feature metallic binders that impart outstanding chemical resistance, making them suitable for heavily corrosive environments. Conversely, organic zinc flake systems leverage polymeric resins to enhance adhesion and flexibility, appealing to applications that demand impact resilience and complex shape coverage.
Process selection further differentiates market offerings, as dip applications deliver uniform layer formation for smaller fasteners, while spin techniques efficiently coat symmetrical parts with minimal overspray. Spray methods, by contrast, offer versatility for large structural elements but require rigorous control of spray parameters to achieve target thicknesses.
The spectrum of end applications-from chassis components such as brake, steering, and suspension parts to electrical busbars, connectors, and terminals-highlights the tailored protective requirements across industries. Fasteners including bolts, nuts, screws, and washers rely on zinc flake coatings to prevent seizing and galling, whereas structural parts like beams, frames, gears, shafts, and panels benefit from the combined sacrificial and barrier properties to maintain mechanical integrity.
Finally, the adoption of zinc flake coatings varies markedly by end use sector. Aerospace manufacturers prioritize extreme durability and resistance to cyclic loading, automotive OEMs emphasize mass production compatibility, construction firms focus on long-term weatherproofing, electronics producers demand nonconductive tack layers, industrial machinery builders require abrasion resistance, and oil and gas operators need robust protection in highly corrosive media. This multifaceted segmentation underscores the diverse performance and compliance parameters guiding zinc flake coating selection.
This comprehensive research report categorizes the Zinc Flake Coating market into clearly defined segments, providing a detailed analysis of emerging trends and precise revenue forecasts to support strategic decision-making.
- Type
- Coating Type
- Process Type
- Application
- End Use Industry
Regional Insights Unveiling Varied Demand Patterns and Growth Drivers Across Americas Europe Middle East Africa and Asia-Pacific
Regional dynamics exert a profound influence on zinc flake coating utilization and technology adoption. In the Americas, strong automotive production hubs and robust industrial machinery sectors have fostered steady demand for both solvent-based and water-based systems. Manufacturers in North America are increasingly investing in local capacity expansions to circumvent tariff disruptions and capitalize on growing aftermarket opportunities, while South American markets are exploring partnerships to upgrade legacy corrosion protection methods.
Across Europe, the Middle East, and Africa, regulatory rigor and industrial diversity generate a complex tapestry of requirements. European nations, led by Germany and France, drive innovation through strict emissions standards and advancements in electric mobility, whereas Middle Eastern and African markets focus on corrosion mitigation for oil and gas infrastructure under extreme environmental conditions. Regional collaboration among coating suppliers and end users is strengthening the development of specialized formulations tailored to fluctuating temperature ranges and saline exposures.
In the Asia-Pacific region, rapid industrialization and urbanization underpin a vibrant landscape for zinc flake coatings. China’s manufacturing prowess continues to expand production volumes, with an emphasis on water-based low-VOC technologies to comply with domestic environmental mandates. Meanwhile, Japan and South Korea lead in precision applications for electronics and automotive subsectors, integrating nanotechnology to enhance coating performance. Across Southeast Asia and Oceania, emerging economies are adopting proven formulations to extend asset lifecycles, thereby aligning with broader infrastructure development initiatives.
These regional insights illustrate how local regulatory, economic, and climatic conditions shape the evolution of zinc flake coating applications, driving tailored strategies that address both global trends and market-specific challenges.
This comprehensive research report examines key regions that drive the evolution of the Zinc Flake Coating market, offering deep insights into regional trends, growth factors, and industry developments that are influencing market performance.
- Americas
- Europe, Middle East & Africa
- Asia-Pacific
Key Company Profiles and Strategic Initiatives Shaping the Competitive Landscape in the Zinc Flake Coating Sector
Leading players in the zinc flake coating industry are pursuing differentiated strategies that emphasize innovation, strategic partnerships, and operational excellence. Several major coating producers have announced collaborations with raw material suppliers to co-develop advanced binders that reduce cure temperatures and improve corrosion performance under cyclic stress. Concurrently, investments in state-of-the-art coating lines equipped with automated surface preparation and post-cure testing equipment underscore a commitment to quality and throughput optimization.
Strategic mergers and acquisitions are also redefining competitive dynamics. Some established chemical companies have integrated specialized coating formulators into their portfolios to broaden their protective solutions offerings and access niche end use segments such as offshore energy and high-speed rail. At the same time, regional applicators are differentiating through value-added services, including pre-treatment consultancy and on-site performance audits, to strengthen customer relationships and ensure adherence to evolving environmental guidelines.
Furthermore, several market leaders have initiated pilot programs incorporating digital twin technology to simulate coating processes, enabling predictive maintenance and real-time process adjustments. These efforts aim to reduce scrap rates, enhance consistency, and accelerate time to market. Collectively, these strategic initiatives by key companies illustrate a trend toward greater collaboration, technology integration, and customer-centric service models that are shaping the future competitiveness of the zinc flake coating sector.
This comprehensive research report delivers an in-depth overview of the principal market players in the Zinc Flake Coating market, evaluating their market share, strategic initiatives, and competitive positioning to illuminate the factors shaping the competitive landscape.
- Aalberts N.V.
- ALTANA AG
- ALU - FIN
- American Elements
- Anochrome Group
- Atotech Deutschland GmbH & Co. KG by MKS Instruments, Inc.
- Aum Dacro Coatings LLP
- AVL METAL POWDERS n.v.
- EJOT Holding GmbH & Co. KG
- Ewald Dörken AG
- Forplan AG
- Holder GmbH
- Hunan Jinhao New Material Technology Co., Ltd
- Huster Oberflächentechnik GmbH
- Kansai Helios Coatings GmbH by Kansai Paint Co.,Ltd.
- Keys & Clamps
- Klimas sp. z o. o.
- Licco Group
- Noelson Chemicals
- NOF CORPORATION
- Novamet Specialty Products Corporation
- Otto Chemie Pvt. Ltd.
- PPG Industries, Inc.
- Progressive Surface Systems
- RIE Coatings
- ROTOVER Lackiertechnik GmbH
- Shiva co.
- Shree Balaji Industries LLP
- Sika AG
- Thai Parkerizing Co., Ltd.
- The DECC Company
- The Magni Group, Inc.
- Varun Advance Coatings
- Wellcoat Tech
- Yuken Industrial Co., Ltd.
- Zincotec Co.,Ltd
Actionable Recommendations Empowering Industry Leaders to Navigate Challenges and Capitalize on Emerging Opportunities in Zinc Flake Coatings
To stay ahead in a rapidly evolving zinc flake coating environment, industry leaders must undertake targeted actions that address both operational efficiency and long-term differentiation. First, investing in research and development of low-temperature cure systems can significantly reduce energy consumption and enable compatibility with heat-sensitive substrates. By prioritizing advanced binder chemistries, organizations can achieve superior corrosion resistance while meeting stricter environmental mandates.
Second, supply chain resilience should be bolstered through diversified sourcing strategies and regional manufacturing footprints. Establishing partnerships with multiple raw material suppliers across geographies mitigates tariff exposure and transportation disruptions. Additionally, incorporating nearshoring or dual sourcing for critical inputs can provide a buffer against sudden regulatory changes and geopolitical tensions.
Third, embracing digital transformation is essential to unlock process efficiencies. Implementing real-time coating thickness monitoring and automated quality inspection reduces variability and lowers rework costs. Coupling these tools with data analytics enables predictive insights that inform maintenance schedules and resource allocation, thereby enhancing overall operational agility.
Finally, cultivating collaborative relationships with end users through joint development programs ensures that formulations evolve in lockstep with emerging application requirements. By co-innovating with key customers, coating providers can tailor solutions for specialized performance needs and foster long-term partnerships built on mutual value creation.
Robust Multi-Level Research Methodology Ensuring Reliable and Unbiased Insights into Zinc Flake Coating Market Dynamics
The insights presented in this report stem from a robust research methodology designed to ensure transparency and reliability. Initially, comprehensive secondary research involved reviewing scientific journals, industry publications, patent databases, and regulatory filings to establish foundational knowledge on zinc flake chemistry and application trends. These findings were then supplemented by primary interviews with coating formulators, applicators, raw material suppliers, and end users across multiple industries to validate key assumptions and uncover emerging use cases.
Data triangulation techniques were employed to cross-verify information from disparate sources, ensuring that qualitative observations aligned with market practices and regulatory developments. Additionally, an expert advisory panel comprising corrosion engineers, surface treatment specialists, and procurement executives provided iterative feedback on preliminary findings, enriching the analysis with real-world perspectives.
To further enhance the rigor of the study, process mapping of typical coating workflows was conducted to identify critical control points and performance metrics. This approach facilitated the evaluation of technological advancements and operational best practices. Throughout the research, adherence to ethical guidelines and stringent confidentiality protocols guaranteed unbiased and actionable insights for stakeholders considering zinc flake coating solutions.
Explore AI-driven insights for the Zinc Flake Coating market with ResearchAI on our online platform, providing deeper, data-backed market analysis.
Ask ResearchAI anything
World's First Innovative Al for Market Research
Strategic Conclusion Emphasizing Key Learnings and Implications for Stakeholders in the Zinc Flake Coating Ecosystem
This executive summary has highlighted the evolution of zinc flake coating from a niche protective treatment to a cornerstone technology in modern corrosion management. Key trends such as the shift toward eco-friendly formulations, the impact of 2025 U.S. tariffs on supply chains, and regional demand nuances underscore the complexity and dynamism of this market. Strategic segmentation insights revealed how variations in solvent and water-based systems, inorganic and organic formulations, application methods, and end use industries converge to create a highly differentiated landscape.
Regional analysis demonstrated how Americas, Europe Middle East Africa, and Asia-Pacific exhibit unique drivers-from automotive innovation to regulatory rigor and manufacturing scalability-that influence coating adoption. Meanwhile, the strategic maneuvers of industry leaders in research, partnerships, digital integration, and operational excellence are setting new benchmarks for competitive advantage.
Looking forward, stakeholders must integrate the actionable recommendations provided to optimize coating performance, enhance supply chain resilience, and foster collaborative innovation. By doing so, organizations can position themselves to navigate regulatory shifts, capitalize on emerging sectors such as electric mobility and renewable energy, and secure long-term profitability in the evolving zinc flake coating ecosystem.
This section provides a structured overview of the report, outlining key chapters and topics covered for easy reference in our Zinc Flake Coating market comprehensive research report.
- Preface
- Research Methodology
- Executive Summary
- Market Overview
- Market Dynamics
- Market Insights
- Cumulative Impact of United States Tariffs 2025
- Zinc Flake Coating Market, by Type
- Zinc Flake Coating Market, by Coating Type
- Zinc Flake Coating Market, by Process Type
- Zinc Flake Coating Market, by Application
- Zinc Flake Coating Market, by End Use Industry
- Americas Zinc Flake Coating Market
- Europe, Middle East & Africa Zinc Flake Coating Market
- Asia-Pacific Zinc Flake Coating Market
- Competitive Landscape
- ResearchAI
- ResearchStatistics
- ResearchContacts
- ResearchArticles
- Appendix
- List of Figures [Total: 28]
- List of Tables [Total: 834 ]
Take Immediate Action Today to Secure Comprehensive Strategic Insights in a Zinc Flake Coating Report with Our Associate Director
To secure an in-depth market research report that delivers strategic clarity and actionable insights on zinc flake coatings, reach out directly to Ketan Rohom, Associate Director of Sales & Marketing. Ketan brings extensive domain knowledge and a consultative approach to understand your unique business challenges, ensuring you receive tailored solutions that drive competitive advantage. By partnering now, you gain immediate access to comprehensive analysis, proven best practices, and future-focused recommendations that empower informed decision making and accelerate growth. Don’t miss the opportunity to leverage this essential resource to optimize your coating strategies, navigate evolving regulatory landscapes, and capitalize on emerging industry trends. Contact Ketan today to discuss your requirements, explore bespoke research options, and secure your copy of the definitive zinc flake coating report.
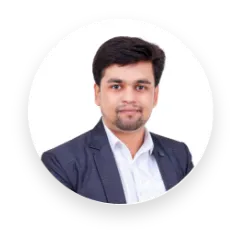
- How big is the Zinc Flake Coating Market?
- What is the Zinc Flake Coating Market growth?
- When do I get the report?
- In what format does this report get delivered to me?
- How long has 360iResearch been around?
- What if I have a question about your reports?
- Can I share this report with my team?
- Can I use your research in my presentation?